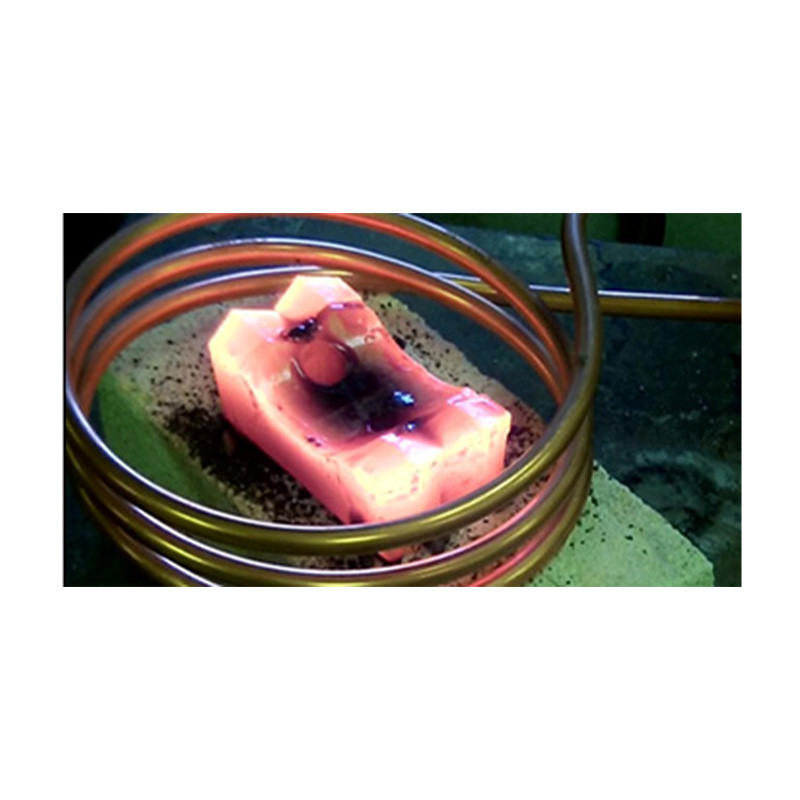
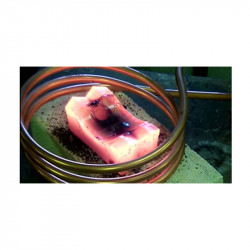
Трябва да сте влезли в
Category
Снимките са само с информационна цел. Вижте спецификацията на продукта
please use latin characters
Objective |
To heat a magnetic steel cutting tool for a brazing application; the end product is a cutter for the logging industry |
---|---|
Material |
|
Temperature | 871°C |
Frequency | 55kHz |
Equipment |
|
Process |
The multiple-position coil was used to test the brazing application on a large rectangular cutting head. With an EKOHEAT 45 kW power supply, the part can be heated to temperature within 150 seconds. Despite testing occurring on a 45kW /100 kHz power supply, Ambrell actually recommends an EKOHEAT 50 kW/30 kHz |
Results |
|
Интересувате ли се от този продукт? Имате ли нужда от допълнителна информация или индивидуални цени?
Трябва да сте влезли
Objective |
To heat a magnetic steel cutting tool for a brazing application; the end product is a cutter for the logging industry |
---|---|
Material |
|
Temperature | 871°C |
Frequency | 55kHz |
Equipment |
|
Process |
The multiple-position coil was used to test the brazing application on a large rectangular cutting head. With an EKOHEAT 45 kW power supply, the part can be heated to temperature within 150 seconds. Despite testing occurring on a 45kW /100 kHz power supply, Ambrell actually recommends an EKOHEAT 50 kW/30 kHz |
Results |
|
Your review appreciation cannot be sent
Report comment
Report sent
Your report cannot be sent
Напишете свой отзив
Review sent
Your review cannot be sent