Трябва да сте влезли в
-
moreX
-
Компоненти
-
-
Category
-
Полупроводници
- Диоди
- Тиристори
- Електроизолирани модули
- Изправителни мостове
-
Транзистори
- Транзистори | GeneSiC
- Модули SiC MOSFET | Mitsubishi
- Модули SiC MOSFET | STARPOWER
- ABB SiC MOSFET модули
- IGBT модули | MITSUBISHI
- Транзисторни модули | MITSUBISHI
- MOSFET модули | MITSUBISHI
- Транзисторни модули | ABB
- IGBT модули | POWEREX
- IGBT модули | INFINEON (EUPEC)
- Полупроводникови елементи от силициев карбид
- Go to the subcategory
- Драйвeри
- Силови блокове
- Go to the subcategory
- Електрически преoбразователи
-
Пасивни компоненти (кондензатори, резистори, предпазители, филтри)
- Резистори
-
Предпазители
- Миниатюрни предпазители за електронни системи серия ABC и AGC
- Бързи тръбни предпазители
- Закъснителни вложки с характеристика GL/GG и AM
- Ултрабързи стопяеми вложки
- Бързи предпазители британски и американски стандарт
- Бързи предпазители европейски стандарт
- Тягови предпазители
- Високоволтни предпазителни вложки
- Go to the subcategory
-
Кондензатори
- Кондензатори за двигатели
- Електролитни кондензатори
- Кондензатори тип snubbers
- Кондензатори за мощност
- Кондензатори за DC (постояннотокови вериги)
- Кондензатори за компенсиране на мощност
- Високоволтови кондензатори
- Кондензатори за индукционно нагряване
- Кондензатори за съхранение на импулси и енергия
- DC LINK кондензатори
- Кондензатори за AC/DC вериги
- Go to the subcategory
- Филтри EMI (против смущения)
- Суперкондензатори
-
Защита от пренапрежение
- Защита от пренапрежение за коаксиални приложения
- Защита от пренапрежение за системи за видеонаблюдение
- Защита от пренапрежение за захранващи кабели
- Ограничители за пренапрежение за LED
- Ограничители за пренапрежение за фотоволтаици
- Защита на системата за претегляне
- Защита от пренапрежение за Fieldbus
- Go to the subcategory
- Go to the subcategory
-
Релета и контактори
- Теория- релета и контактори
- Полупроводникови релета АС 3-фазни
- Релета полупроводникови DC
- Регулатори, управляващи системи и аксесоари
- Системи за мек старт и реверсивни контактори
- Електромеханични релета
- Контактори
- Ротационни превключватели
-
Полупроводникови релета АС 1-фазни
- Полупроводникови релета AC еднофазни серия 1 | D2425 | D2450
- Полупроводникови релета AC еднофазни серия CWA I CWD
- Полупроводникови релета AC еднофазни серия CMRA I CMRD
- Полупроводникови релета АС ендофазни серия PS
- Полупроводникови релета AC двойни и четворни серия D24 D, TD24 Q, H12D48 D
- 1-фазни полупроводникови релета серия gn
- Полупроводникови релета АС серия ckr
- Релета AC еднофазни на шина DIN серия ERDA и ERAA
- Еднофазни AC релета за ток 150А
- Двойни полупроводникови релета, интегрирани с радиатор за DIN шина
- Go to the subcategory
- Полупроводникови релета АС 1-фазни, за печатни платки
- Интрфейс релета
- Go to the subcategory
- Индукционни елементи
- Радиатори, Bаристори, Tермични защити
- Вентилатори
- Климатизация, Оборудване за електрически шкафове, Охладители
-
Батерии, зарядни устройства, буферни захранвания и инвертори
- Батерии, зарядни устройства - теоретично описание
- Литиево-йонни батерии. Персонализирани батерии. Система за управление на батерията (BMS)
- Батерии
- Зарядни устройства и аксесоари за батерии
- UPS резервно захранване и буферни захранвания
- Преобразуватели и аксесоари за фотоволтаици
- Енергиен запас
- Горивни клетки
- Литиево-йонни батерии
- Go to the subcategory
-
Автоматика
- Futaba Drone Parts
- Крайни изключватели, Микроизключватели
- Датчици, Преобразователи
- Пирометри
- Броячи, Времеви релета, Панелни измервателни прибори
- Промишленни защитни устройства
- Светлинна и звукова сигнализация
- Термокамера
- Екрани LED
- Управляваща апаратура
-
Регистратори
- Регистратор на температура със запис на лента и цифров показател - AL3000
- Микропроцесорни регистратори с екран LCD серия KR2000
- Регистратор KR5000
- Измервател със функция за регистриране на влажност и температура HN-CH
- Експлоатационни материали за регистратори
- Компактен графичен регистратор 71VR1
- Регистратор KR 3000
- Регистратор РС серия R1M
- Регистратори РС серия R2M
- Регистратор РС - 12 изолирани входа– RZMS
- Регистратор PC, USB, 12 изолирани входа – RZUS
- Go to the subcategory
- Go to the subcategory
-
Проводници, Кабел литцендрат, Кабелни канали, Меки връзки
- Проводници
- Кабел литцендрат
-
Кабели за специални приложения
- Компенсиращи и удължаващи проводници
- Проводници за термодвойки
- Съединителни проводници за РТ датчици
- Многожилни проводници темп. -60C до +1400C
- SILICOUL проводници средно напрежение
- Запалителни проводници
- Нагревателни проводници
- Едножилни проводници темп. -60C до +450C
- Проводници за ЖП приложения
- Нагревателни проводници в Ех изпълнение
- Go to the subcategory
- Кабелни канали
-
Плетени кабели
- Плоски плетени кабели
- Кръгли плетени кабели
- Много гъвкави плетени кабели - плоски
- Много гъвкави плетени кабели - кръгли
- Медни цилиндрични плетени кабели
- Медни цилиндрични плетени кабели и канали/кожуси
- Гъвкави заземяващи ленти
- Плетени проводници от оцинкована и неръждясваща стомана
- Медни изолирани плетени проводници PCV -температура до 85 градуsа по C
- Плоски плетени алуминиеви проводници
- Комплект за подсъединение - плетени проводници и тръбички
- Go to the subcategory
- Оборудване за тяга
- Кабелни накрайници
- Изолирани еластични шини
- Многослойни еластични шини
- Системи за провеждане на кабели (шлауфи)
- Кабелни канали / маркучи
- Go to the subcategory
- View all categories
-
Полупроводници
-
-
- Suppliers
-
Applications
- AC и DC задвижвания (инвертори)
- CNC машинни инструменти
- Energy bank
- HVAC автоматизация
- Двигатели и трансформатори
- Заваръчни машини и заваръчни машини
- Захранващи (UPS) и токоизправителни системи
- Измерване и регулиране на температурата
- Измерване и регулиране на температурата
- Индукционно отопление
- Индустриална автоматизация
- Индустриална автоматизация
- Индустриални защитни устройства
- Компоненти за потенциално експлозивна атмосфера (EX)
- Машини за сушене и обработка на дървесина
- Машини за термоформоване на пластмаси
- Минно дело, металургия и основаване
- Оборудване за разпределителни, контролни и телекомуникационни шкафове
- Печат
- Трамвайна и железопътна тяга
-
Инсталация
-
-
Индуктори
-
-
Индукционни устройства
-
-
https://www.dacpol.eu/pl/naprawy-i-modernizacje
-
-
Обслужване
-
- Contact
- Zobacz wszystkie kategorie
High Power Density, High Performance X-Series 4500V IGBT Power Modules
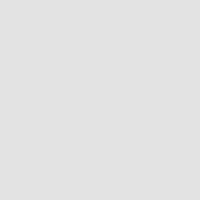
High Power Density, High Performance X-Series 4500V IGBT Power Modules
Mitsubishi Electric has developed high performance 4500V IGBT power modules providing reliable solutions for medium voltage drive, railway and power transmission applications.
By Eugen Wiesner, Dr. Nils Soltau, Eugen Stumpf, Mitsubishi Electric Europe B. V. and Kenji Hatori, Hitoshi Uemura, Mitsubishi Electric Corporation
Introduction
Originally, Mitsubishi Electric started the development of the 4500V IGBTs in the middle of 90s. The first commercialization of standard IGBT modules in this voltage class was started in beginning of 2000s. It was a more efficient and compact solution compared to existing 4500V GTO press pack devices. Mainly this development was driven by railway and medium-voltage (MV) drive applications. Meanwhile, a wide variation of the 4500V IGBT modules is available, such as: dual diode modules, modules with copper and AlSiC base plate, modules with standard (VISO=6 kV) and high isolation packages (VISO=10.2 kV).
Targets of 4500V X-Series IGBT Modules
The newly developed 4500V X-Series is already the third series after H-Series and R-Series of MITSUBISHI ELECTRIC IGBT power modules. The line-up of the new X-Series is expanding the existing line-up towards higher power densities (refer Figure 1). The current rating of the large package (footprint: 190mm x 140mm) increases from 900A to 1350A. On the other hand, the 900A rated current also will be made available in smaller package size of 140mm x 130mm.
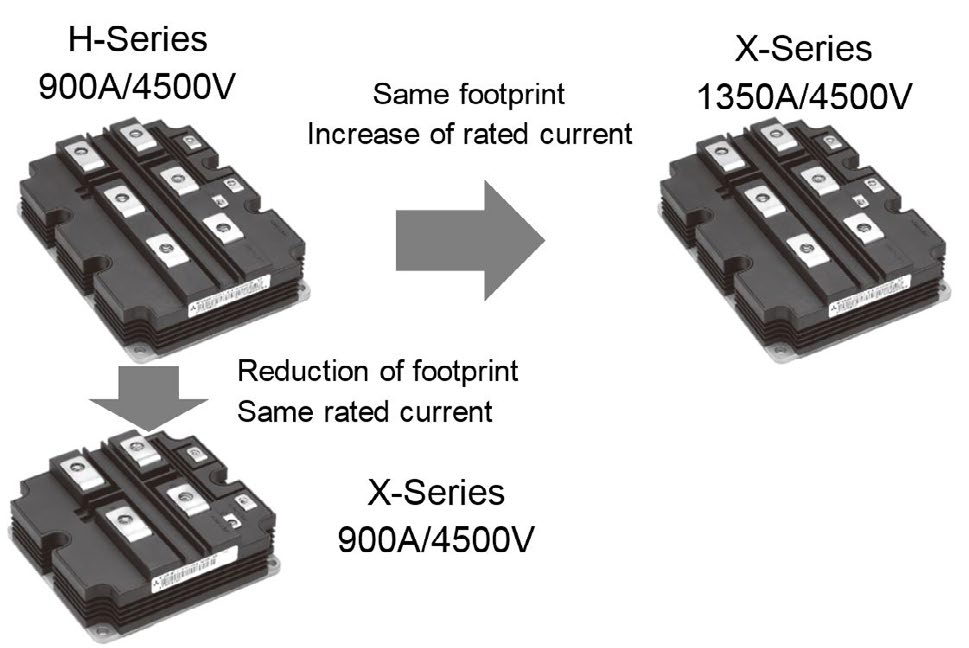
Figure 1: 4500V X-Series line-up expansion
The standard package type is still very important for different applications due to availability of second source from many IGBT device manufacturers and its proven reliability record in the field for many years. Furthermore, the upgrade or increase of the inverter output power is easily achievable by using the widely commercially available components in the market like heatsinks, gate drivers and bus bars.
The targets for 4500V X-Series device development have been defined based on feedback from customers. These were the following:
- Increasing current rating and module power density
- Reduction of module power losses
- Suitable for various applications having different switching frequency ranges
Six modules have been developed [1] to fulfill the above mentioned market requirements. The overview of the developed 4500V X-Series modules is shown in table 1.
Isolation voltage | Foot print | Type name |
---|---|---|
VISO 10.2 kV | 190mm x 140mm | CM1350HG-90X (VCCmax=3400V) CM1500HG-90X (VCCmax=3200V) |
130mm x 140mm | CM900HG-90X (VCCmax=3400V) CM1000HG-90X (VCCmax=3200V) |
|
VISO 6 kV | 190mm x 140mm | CM1350HC-90X (VCCmax=3400V) CM1500HC-90XA (VCCmax=3000V) |
Table 1: 4500V X-Series Line-up
Improving the Module Power Density
The most challenging requirement was increasing the module power density. The development target was achieved mainly by using the new 7th Gen. Chipset. The 7th Gen. IGBT chip, shown in Figure 2, contributes several significant cutting-edge features. The Carrier Stored Trench-gate Bipolar Transistor structure (CSTBT™) allows reduction of the IGBT forward voltage. The new LNFLR (Linearly- Narrowed Field Limiting Ring) chip termination structure allows for an increase in the active chip area and thereby a reduction of the thermal resistance. Finally, the partial P-Collector technology allows a special capability to manage a wide RBSOA.
Furthermore, the overall packaging technology of 4500V X-Series is improved for managing the increased power density. The optimized internal chip layout reduces the module thermal resistance and increases the power cycling capability. As a result, the junction-tocase thermal resistance was reduced by more than 20% compared to previous R-Series (CM1350HG-90X and CM1200HG-90R). The module performance has been proven and specified for a wide operation temperature range from -50°C to 150°C. The previous 4500V module generations were specified up to 125°C.
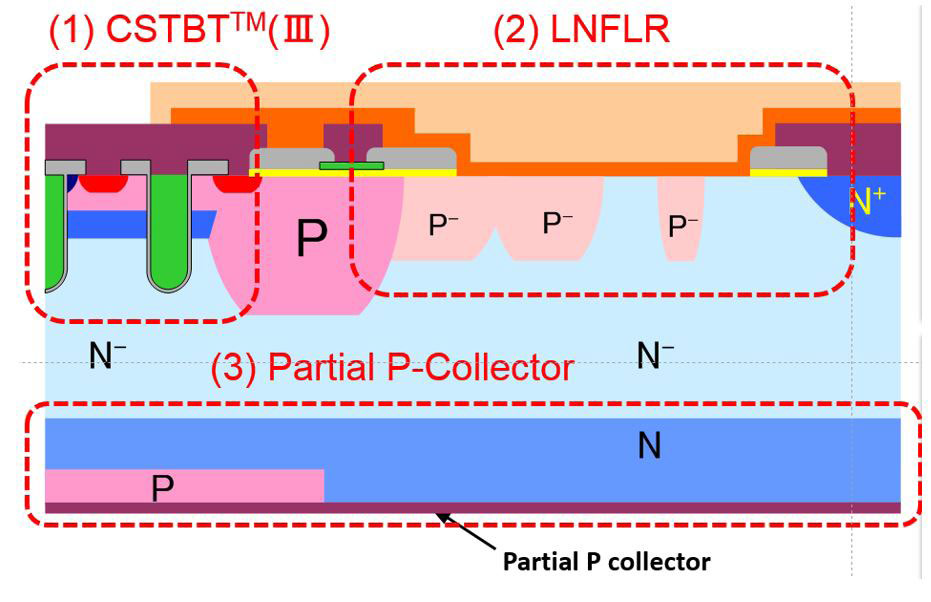
Figure 2: 4500V 7th Gen. Chip structure
Two different 7th Gen chip set are available, optimized for high and low switching frequency applications respectively. The X-Type chip set is designed for high switching frequency application (> 350Hz). The XA-type chip set achieves the lowest possible forward voltage for the IGBT and the diode. The intended switching frequency ranges from 100Hz to 350Hz. The trade-off between the forward voltage and reverse recovery switching energy for X- and XA- diode is shown in Figure 3.
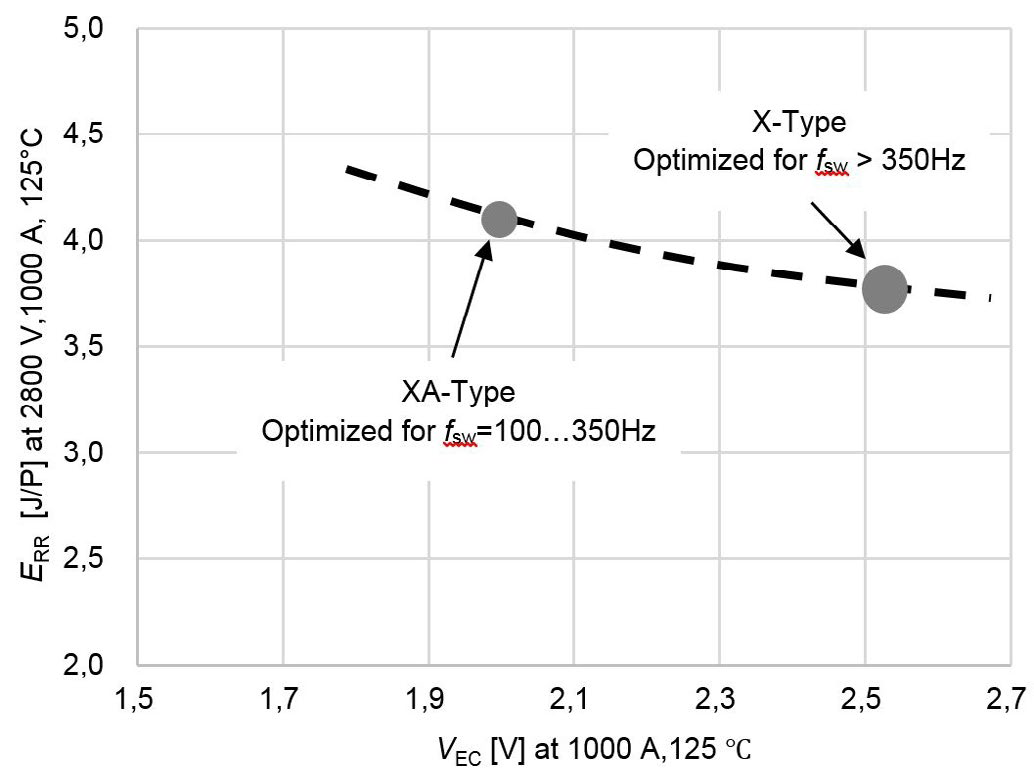
Figure 3: Diode trade-off between X- and XA device type
Safe Operating Area (SOA) for Each Application
The DC-link voltage is one of the most important stress factors influencing the SOA of IGBT module. Some applications do not require high DC-link voltage. For such cases, the SOA and with it the permitted maximum current rating increase.
The 4500V X-Series device is designed to operate at a maximum DC-link voltage of 3400V. In this case, the module’s rated current is 1350A (CM1350HG-90X). If the required maximum DC-link voltage is reduced to 3200V, the rated current increase up to 1500A (CM1500HG-90X). Both modules have the same electrical characteristics but have different SOA specifications. Each device undergoes shipping tests according to the defined maximum DC-link voltage respectively.
Example of a 3-level NPC Inverter Application
One of the targeted applications for the 4500V modules is the medium voltage (MV) drive application. For these drives, the output voltage range is between 2.3kV and 13.2kV [2]. The most common voltage levels are: 3.3 kV, 4.16kV, 6kV and 6.6kV. For these output voltages, 3-level topology is widely used. For example, these voltages can be covered by devices such as the CM1500(1350)HG-90X (as shown in Table 2). For output voltage levels higher or equal than 4160V - series connection of 4500V modules becomes necessary.
Inverter output voltage VOUT [Vrms] | Total required inverter DCLink voltage VDC_link [V] | IGBT blocking voltage VCES IGBT [V] | IGBT Series connection | IGBT DC-Link voltage VCC_IGBT [V] |
---|---|---|---|---|
3300 | 4800 | 4500 (CM1500HG-90X) | No | 2400 |
4160 | 6200 | 4500 (CM1500HG-90X) | Yes | 1600 |
6000 | 8800 | 4500 (CM1500HG-90X) | Yes | 2200 |
6600 | 9600 | 4500 (CM1500HG-90X) | Yes | 2400 |
Table 2: Example for 4500V IGBT module based 3-level NPC configurations
Scalability towards lower power ranges can be realized with the CM900HG-90X device or the H- and R-Series modules. The following example shows the potential of the new X-Series compared to the first H-Series in terms of power loss reduction. For the VOUT=3300V output voltage, the necessary DC-Link voltage is about 4800V. In 3-level NPC-configurations, the IGBT module would experience the half the total DC-Link (2400V). In case the heatsink potential would be connected to the middle of the DC-Link the IGBT Module isolation voltage of 10.2 kV(rms) would be sufficient to cover in Table 2 mentioned inverter output voltages.
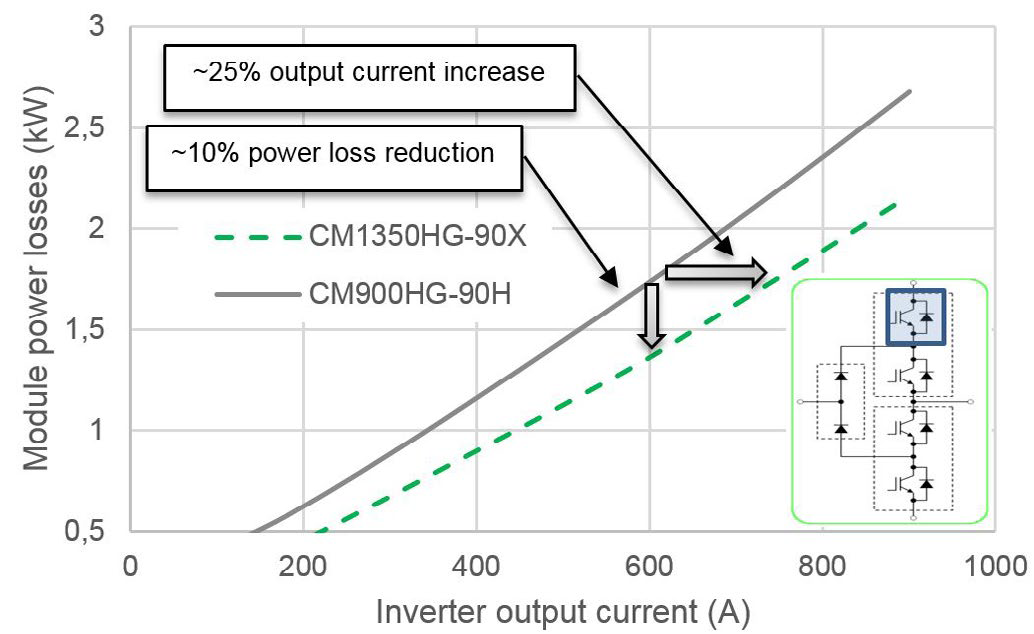
Figure 4: Comparison of the power loss simulation result using the H- and X-Series 190mm x 140mm modules.
Figure 4 shows the power loss simulation versus output current for CM900HG-90H H-Series device and CM1350HG-90X X-Series device. The simulation conditions are:
- Switching frequency fsw=0.5kHz
- Power factor p.f.=0.85
- Modulation index m=1
- Junction temperature TJ=125°C
There are two possibilities for utilizing the performance of new X-Series power modules. One possibility is a reduction of the IGBT module power losses. The power losses decrease by about 10% compared to the H-Series. The other possibility is increasing the inverter output current. The output current can be increased by about 25% compared to the H-Series. In addition, 150°C operation of X-series enables to increase even more output current than 125°C operation.
Conclusion
The newly developed 4500V X-Series enables significant increase in the inverter output power. Key enabling factors are an increased maximum junction temperature of 150°C, an improved thermal management and reduced power losses in the module. A large line-up and backward compatibility to H-Series and R-Series ensures a flexible converter design and an easy design-in. Furthermore, two different chip sets (X-type and XA-type) facilitates the optimal operation at required switching frequencies.
References
[1] Mitsubishi Electric Corporation, “Mitsubishi Electric to Expand Lineup of X-Series HVIGBT Modules,” Press Release No. 3094, May 2017
[2] Prof. Dr. M. Hiller, “Leistungselektronik mit Si-Bauelementen für die Mittelspannung”, Tagungsband des 1. Industriearbeitskreis Mittelspannungs-Leistungelektronik [Proceedings of the 1. Industry Working Group Medium-Voltage Power Electronics], Fraunhofer ISE, Berlin, Germany, 2016.
Related posts
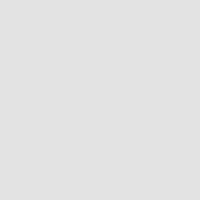
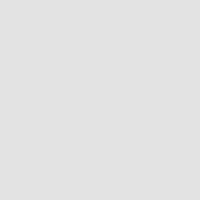
Leave a comment