Musíte být přihlášen
Telescopické kryty – co to jsou a proč jsou důležité?
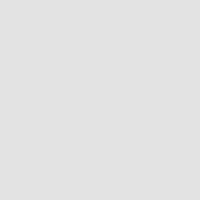
Teleskopické kryty jsou ochranné prvky používané v průmyslových strojích, navržené k ochraně pohyblivých částí před nečistotami, mechanickým poškozením a předčasným opotřebením. Díky své konstrukci efektivně chrání vodicí lišty, šrouby a další součásti odpovědné za přesný chod zařízení.
Teleskopické kryty – Co jsou a proč jsou důležité?
Použití teleskopických krytů je nezbytné v kovoprůmyslu, CNC výrobě a mnoha dalších sektorech, kde stroje musí pracovat v náročných podmínkách. Teleskopické kryty nejen prodlužují životnost strojů, ale také snižují riziko poruch, což vede k nižším nákladům na údržbu a vyšší efektivitě výroby.
Teleskopické kryty v průmyslových strojích
Teleskopické kryty hrají důležitou roli v ochraně strojních mechanismů před vnějšími faktory. Jejich úkoly jsou:
Ochrana před prachem, třískami a kapalinami – při obráběcích procesech vznikají jemné třísky a chladicí kapaliny, které mohou negativně ovlivnit chod strojů. Teleskopické kryty efektivně blokují přístup těchto nečistot.
Prevence mechanického poškození vodicích lišt – průmyslové stroje pracují s vysokou přesností a i drobné poškození vodicí lišty může ovlivnit kvalitu obrábění. Teleskopické kryty toto riziko minimalizují.
Snižování provozních nákladů – ochrana strojních součástí znamená méně častou údržbu a výměnu, což snižuje náklady na údržbu a dobu nefunkčnosti výroby.
Zvýšení bezpečnosti operátora – dobře navržené teleskopické kryty zabraňují náhodnému kontaktu pracovníků s pohyblivými částmi strojů, což zvyšuje bezpečnost na pracovišti.
Materiály používané při výrobě teleskopických krytů
Teleskopické kryty mohou být vyrobeny z různých materiálů, ale nejběžněji používané jsou:
Nerezová ocel – obzvláště doporučována v prostředích, kde je přítomna velká množství mazacích a chladicích kapalin. Nerezová ocel je odolná proti korozi a zajišťuje dlouhou životnost i v náročných podmínkách.
Litina – méně běžně používaná, ale stále aplikovaná v některých aplikacích. Je těžší než ocel, ale nabízí vysokou odolnost proti opotřebení a mechanickou stabilitu.
Hliníkové slitiny a další kovy – v některých případech se používají lehké kovy, zejména tam, kde je hmotnost krytu důležitá pro dynamiku pohybu stroje.
Volba materiálu závisí na pracovních podmínkách stroje a prostředí, ve kterém bude kryt použit.
Příslušenství zajišťující správnou funkci
Pro teleskopické kryty, aby efektivně plnily svou funkci, jsou často vybaveny dalšími komponenty, které zlepšují jejich odolnost a provozní účinnost. Mezi nejdůležitější příslušenství patří:
- Kluzné podložky – snižují tření a zajišťují plynulý pohyb krytu.
- Válečky a vodicí lišty – umožňují přesný a lehký pohyb krytů, což je zvláště důležité pro rychlé stroje.
- Stojky – snižují nárazovou sílu mezi segmenty krytu, čímž prodlužují jeho životnost.
- Škrabky a stěrky na olej – odstraňují přebytečnou chladicí kapalinu, olej a nečistoty z vodicích lišt, čímž brání jejich vniknutí do vnitřku krytu.
Díky správnému výběru materiálů a příslušenství mohou teleskopické kryty spolehlivě fungovat po dlouhou dobu a efektivně chránit strojní součásti a zajistit jejich spolehlivost.
Výroba teleskopických krytů
Výroba teleskopických krytů je proces, který vyžaduje precizní přístup a plnou přizpůsobivost specifickým potřebám zákazníků. Každý stroj, jeho pracovní podmínky a požadavky jsou jiné, takže design a výroba krytů musí být flexibilní, aby splnily tyto individuální očekávání. Společnosti, které se zabývají výrobou teleskopických krytů, jako je Metal Gennari, reagují na tyto potřeby vytvářením "na míru" řešení a zajišťováním nejvyšší kvality zpracování.
Každý teleskopický kryt je navržen s ohledem na specifikace stroje, kde bude použit. Proces návrhu začíná důkladnou analýzou požadavků zákazníka, pracovních podmínek stroje a případných speciálních potřeb, jako je rychlost pohybu nebo přítomnost mazacích a chladicích látek. Na základě toho jsou vytvářeny řešení, která nebudou jen efektivní, ale i odolná.
Návrháři přizpůsobují tvar, rozměry a materiály krytů specifickým požadavkům aplikace. Díky tomuto individualizovanému přístupu se teleskopické kryty stávají optimálním řešením pro ochranu strojů při minimalizaci provozních nákladů a maximalizaci bezpečnosti a výrobní efektivity.
Význam přesnosti a kvality materiálů
Kvalita materiálů použitých při výrobě teleskopických krytů je rozhodující pro jejich výkon a dlouhověkost. Kvalitní materiály nejen poskytují lepší ochranu proti mechanickému poškození a nečistotám, ale také zvyšují odolnost proti korozi, opotřebení a dalším náročným pracovním podmínkám.
V případě velkých průmyslových strojů, kde kryty musí pracovat v obtížných podmínkách (např. při vysokých skluzových rychlostech nebo při intenzivním použití mazacích kapalin), je zvláště důležité používat materiály odolné proti korozi a vysokým teplotám. Z tohoto důvodu je nerezová ocel jedním z nejčastěji vybraných materiálů pro výrobu teleskopických krytů. Dále přesná výroba a správné zpracování materiálů zaručují spolehlivost krytu během dlouhé doby používání.
Příklady teleskopických krytů vyrobených z nerezové oceli
Nerezová ocel je ideálním materiálem pro teleskopické kryty, které musí pracovat v prostředí s vysokým výskytem mazacích a chladicích kapalin. Díky své odolnosti proti korozi zajišťuje nerezová ocel dlouhověkost krytů i v náročných průmyslových podmínkách. Metal Gennari jako výrobce teleskopických krytů nabízí řešení vyrobená z tohoto materiálu, přizpůsobená požadavkům zákazníků na tvar, velikost a pracovní podmínky stroje.
Příkladem může být teleskopický kryt z nerezové oceli pro obráběcí stroj, který pracuje v prostředí s vysokou vlhkostí a intenzivním používáním chladicí kapaliny. Použitím nerezové oceli kryt zajišťuje ochranu proti korozi a jeho konstrukce je vhodná pro vysoké zátěže a častý pohyb. Teleskopické kryty z nerezové oceli jsou také snadno čistitelné a udržovatelné, což přispívá k jejich dlouhověkosti a spolehlivosti.
Oprava teleskopických krytů
Oprava teleskopických krytů je důležitý proces, který prodlužuje jejich životnost a udržuje stroje v plně funkčním stavu, čímž minimalizuje riziko poruch a s nimi spojené náklady. Profesionální diagnostika a odborné opravy jsou klíčem k udržení vysoké efektivity krytů, zejména v průmyslovém prostředí, kde teleskopické kryty hrají klíčovou roli v ochraně strojů.
Diagnostika a rozsah možných oprav
Proces opravy teleskopických krytů začíná důkladnou diagnostikou, která pomáhá identifikovat poškození a posoudit technický stav krytu. Odborníci ve firmách specializujících se na tyto opravy, jako je Metal Gennari, provádějí podrobnou inspekci, aby pochopili, které komponenty krytu potřebují opravu nebo výměnu.
V závislosti na stupni opotřebení a typu poškození mohou opravy zahrnovat různé úkoly. Mechanické poškození nebo opotřebení materiálu, například od tření, může vyžadovat výměnu těsnění, válečků nebo tlumičů. Na druhé straně problémy způsobené třením nebo opotřebením v důsledku maziv mohou vyžadovat výměnu ochranných prvků, jako jsou olejové stírky nebo vodiče. Prováděním komplexní opravy se kryt vrací do plné funkčnosti.
Jaké komponenty mohou být v teleskopických krytech vyměněny?
Během opravy teleskopických krytů lze vyměnit mnoho klíčových komponent, které jsou náchylné k poškození během provozu. Některé z nich jsou:
• Olejové stírky: Teleskopické kryty vybavené stírači (jak mosaznými, tak PVC) pomáhají odstraňovat přebytečný olej, čímž zabraňují jeho hromadění a usazování. Výměna opotřebovaných stíračů je jedním z nejběžnějších úkolů při opravách.
• Válečky a tlumiče: Tyto komponenty jsou zodpovědné za hladký pohyb krytu. Časem se mohou opotřebovat, a jejich výměna obnoví optimální funkčnost teleskopického krytu.
• Vodiče a další příslušenství: Poškozené vodiče nebo jiné strukturální komponenty lze také opravit výměnou. Správné vedení teleskopických komponentů je klíčové pro efektivitu krytu.
Oprava teleskopických krytů umožňuje precizní nastavení komponent v závislosti na stupni opotřebení, což zajišťuje jejich dlouhotrvající a spolehlivý provoz.
Testování a rychlé doručení po opravě
Po dokončení opravy procházejí všechny teleskopické kryty důkladným testováním, aby se zkontrolovala jejich funkčnost a odolnost. Firmy jako Metal Gennari používají simulátory a testovací stanice, které umožňují provádět zátěžové zkoušky za podmínek blízkých reálnému provozu. To zajišťuje, že jakékoli potenciální nesrovnalosti budou odhaleny a opravené kryty budou fungovat bez problémů.
Po dokončení testování je opravený teleskopický kryt připraven k rychlému doručení zákazníkovi. Čas dokončení opravy je v mnoha případech jen několik dní, což pomáhá minimalizovat prostoje a udržet kontinuitu průmyslových strojů. Rychlé doručení je důležitou součástí komplexní služby, která je vysoce ceněna v situacích, kdy je čas klíčový.
Speciální aplikace teleskopických krytů
Teleskopické kryty jsou nepostradatelné v mnoha průmyslových sektorech a jejich úloha není jen v ochraně strojů před nečistotami, ale také v zajištění jejich dlouhodobého bezporuchového provozu. Jak se obráběcí stroje a průmyslová zařízení stále vyvíjejí, vznikají nové požadavky na návrh teleskopických krytů. Přizpůsobení těchto krytů novým technologiím je zásadní pro zachování jejich efektivity v dynamicky se měnících pracovních podmínkách.
Jak přizpůsobit kryty moderním obráběcím strojům?
Moderní obráběcí stroje často vyžadují teleskopické kryty, které splňují vyšší nároky týkající se pracovní rychlosti a specifických provozních podmínek. Proto musí být teleskopické kryty přizpůsobeny parametrům, jako je měnící se rychlost pohybu, velké množství chladicích kapalin a složité operace, které se v obráběcích strojích vyskytují.
Návrh teleskopických krytů pro moderní stroje začíná důkladným pochopením specifických potřeb zákazníka. Je nutné zvážit, jak rychle se pohybují strojní prvky, jaký je kontakt s mazivovými kapalinami a které materiály poskytnou optimální ochranu. Proto jsou často používány materiály, jako je nerezová ocel, známá svou vysokou odolností vůči olejům a chemikáliím. Návrháři také často do designu zahrnují inovativní řešení, jako jsou dodatečné příslušenství, které snižují tření a zlepšují plynulost pohybu.
Řešení pro velké množství kapalin a vysokou rychlost
V mnoha moderních obráběcích strojích může přítomnost velkého množství mazacích nebo chladicích kapalin představovat další výzvy. I když jsou tyto kapaliny nezbytné při obrábění, mohou způsobit předčasné opotřebení teleskopických krytů, pokud nejsou správně řízeny. Aby se tomu zabránilo, návrh teleskopických krytů zohledňuje speciální materiály a příslušenství.
Teleskopické kryty navržené pro takové podmínky jsou obvykle vyrobeny z nerezové oceli, která zajišťuje dlouhověkost a odolnost vůči korozi. V prostředí, kde je přítomno velké množství kapaliny, je také důležité používat olejové stírky (v mosazné nebo PVC verzi), aby se zabránilo nadměrnému hromadění oleje. Díky těmto řešením teleskopické kryty nejen chrání stroj před poškozením, ale také zajišťují dlouhodobý a efektivní provoz v náročných podmínkách.
V podmínkách vysokorychlostního klouzání musí být teleskopické kryty navrženy tak, aby minimalizovaly riziko poškození. V takových situacích se používají speciální tlumící příslušenství, která zabraňují nárazům mezi komponenty a zajišťují jejich trvanlivost.
Příklady speciálních teleskopických vodičů
Pro vysokorychlostní obrábění je nutné používat specializovaná designová řešení, jako jsou dvojité pantografy nebo pokročilejší teleskopické vodiče. Příkladem takového řešení je teleskopický vodič pro paralelní soustruh, vybavený dvojitým pantografem a pěti řadami mosazných vodičů, které se vzájemně zamykají. Tento typ řešení se používá v situacích, kdy je vysoká klouzavá rychlost, protože pantografy a vodiče zajišťují rovnoměrné otevírání prvků, čímž se snižuje riziko poškození nebo zablokování. Díky těmto systémům je možné dosáhnout větší konzistence komponent teleskopického krytu a zvýšit jejich odolnost proti poškození, což vede k delší životnosti krytu.
Podobná inovativní řešení jsou navrhována v technických kancelářích, které vyvíjejí zakázkové teleskopické kryty přizpůsobené výjimečným podmínkám výroby. Díky těmto řešením mohou teleskopické kryty splnit požadavky moderních obráběcích strojů, a to i v náročných podmínkách zahrnujících velké množství kapalin nebo vysokorychlostní pohyb.
Vysokorychlostní teleskopické kryty
Teleskopické kryty pracující ve vysokorychlostních strojích jsou klíčovým prvkem pro zajištění dlouhodobého a bezproblémového provozu strojů. V závislosti na rychlosti pohybu strojních prvků musí být návrh krytu přizpůsoben specifickým požadavkům, aby se minimalizovalo riziko poškození, zvýšila odolnost a zajistil plynulý pohyb.
Jak rychlost klouzání ovlivňuje návrh krytu?
Rychlost klouzání prvků v obráběcím stroji ovlivňuje návrh teleskopických krytů. V případech, kdy rychlost klouzání nepřesahuje 15 m/min, teleskopické kryty nevyžadují speciální tlumicí opatření, což činí jejich návrh jednodušší a standardnější. Avšak pro vyšší rychlosti, zejména když dosahují hodnot mezi 15 a 30 m/min, je nutné použít speciální tlumicí prvky, které zabraňují nárazům mezi jednotlivými sekcemi krytu.
Použitím řešení, jako jsou tlumiče, těsnění a vhodné příslušenství, mohou teleskopické kryty fungovat v náročnějších podmínkách, poskytující delší životnost a stabilní výkon. Pro vyšší rychlosti (nad 30 m/min) musí návrh krytu zahrnovat také prvky, které umožní rovnoměrné otevírání komponent a zabrání jejich zastavení.
Řešení pro kryty pracující při rychlostech 15–60 m/min
Teleskopické kryty pracující při rychlostech od 15 do 60 m/min musí být navrženy se specifickými potřebami těchto strojů na paměti. Pro rychlosti mezi 15 a 30 m/min, jak již bylo zmíněno, je klíčové použití tlumicích systémů, které snižují nárazovou sílu mezi sekcemi krytu. V těchto návrzích je důležité, aby byly teleskopické prvky správně vyváženy a materiály použitých krytů byly dostatečně odolné k tomu, aby zvládly intenzivní pohyb a kontakt s mazacími kapalinami, které mohou v takových strojích nastat.
Pro rychlosti mezi 30 a 60 m/min musí návrháři použít pokročilejší mechanismy, jako jsou pantografy, které zabraňují zastavení krytu a zajišťují rovnoměrné otevírání komponent. Kromě toho použití speciálních vodičů a vzájemně zamykajících se mechanických prvků pomáhá udržovat stabilitu krytu a snižuje riziko jeho zaseknutí nebo zablokování.
Důležitost pantografů a vzájemně zamykajících se vodičů
V kontextu teleskopických krytů pracujících při vysokých rychlostech hrají pantografy a vzájemně zamykající se vodiče klíčovou roli při zajištění plynulého a stabilního pohybu. Pantograf, umístěný na vrcholu krytu, pracuje na principu pohybu „koncertiny“, čímž zabraňuje jakémukoli zastavení a zajišťuje rovnoměrné otevírání komponent krytu. Tento mechanismus je nesmírně důležitý u strojů pracujících při vyšších rychlostech, kde je stabilita pohybu klíčová.
Mezitím vzájemně zamykající se mosazné vodiče, jaké se používají ve speciálních teleskopických vodičích pro paralelní soustruhy, dále posilují celou konstrukci, čímž zabraňují zablokování a zajišťují lepší konzistenci mezi sekcemi krytu. Použitím tohoto řešení mohou teleskopické kryty pracující při vysokých rychlostech vydržet dlouhodobý, intenzivní pohyb bez rizika mechanického poškození.
Kombinované použití pantografů a vzájemně zamykajících se vodičů činí teleskopické kryty odolnějšími vůči nárazům a snižuje riziko poškození, čímž výrazně zlepšuje výkon a životnost celého systému.
Zanechat komentář