Musíte být přihlášen
-
moreX
-
Komponenty
-
-
Category
-
Polovodiče
- LED diody
- Tyristory
- Elektroizolační moduly
- Přemosťovací usměrňovače
-
Tranzistory
- Tranzistory | GeneSiC
- SiC MOSFET moduly | Mitsubishi
- SiC MOSFET moduly | STARPOWER
- Moduly ABB SiC MOSFET
- Moduly IGBT | MITSUBISHI
- Tranzistorové moduly | MITSUBISHI
- Moduly MOSFET | MITSUBISHI
- Tranzistorové moduly | ABB
- Moduly IGBT | POWEREX
- Moduly IGBT | INFINEON (EUPEC)
- Polovodičové prvky z karbidu křemíku (SiC)
- Go to the subcategory
- Ovladače brány
- Bloky napájení
- Go to the subcategory
- Měniče proudu a napětí LEM
-
Pasivní součásti (kondenzátory, rezistory, pojistky, filtry)
- Rezistory
-
Pojistky
- Miniaturní pojistky pro elektronické obvody řady ABC a AGC
- Trubkové rychle působící pojistky
- Pojistkové vložky s časovým zpožděním s charakteristikami GL / GG a AM
- Ultrarychlé pojistkové články
- Rychle působící pojistky (britský a americký standard)
- Rychle působící pojistky (evropský standard)
- Pojistky pojezdu
- Pojistkové vložky vysokého napětí
- Go to the subcategory
-
Kondenzátory
- Motorové kondenzátory
- Elektrolytické kondenzátory
- Filmové kondenzátory
- Výkonové kondenzátory
- Kondenzátory pro stejnosměrné obvody
- Kondenzátory korekce účiníku
- Vysokonapěťové kondenzátory
- Indukční topné kondenzátory
- Kondenzátory pulsu a energie
- DC LINK kondenzátory
- Kondenzátory pro AC / DC obvody
- Go to the subcategory
- EMI filtry
- Superkondenzátory
- Přepěťová ochrana
- Go to the subcategory
-
Relé a stykače
- Teorie relé a stykačů
- 3fázová střídavá polovodičová relé
- 3fázová střídavá polovodičová relé
- Regulátory, ovládací prvky a příslušenství
- Měkké spouštění a reverzační stykače
- Elektromechanická relé
- Stykače
- Otočné spínače
-
Jednofázová střídavá polovodičová relé
- Jednofázová střídavá polovodičová relé, 1 řada | D2425 | D2450
- Jednofázová střídavá polovodičová relé řady CWA a CWD
- Jednofázová střídavá polovodičová relé řady CMRA a CMRD
- Jednofázová střídavá polovodičová relé řady PS
- Dvojitá a čtyřnásobná střídavá polovodičová relé řady D24 D, TD24 Q, H12D48 D.
- Jednofázová polovodičová relé řady GN
- Jednofázová střídavá polovodičová relé řady CKR
- Jednofázová AC relé na lištu DIN řady ERDA A ERAA
- Jednofázová AC relé pro proud 150 A.
- Dvojitá polovodičová relé integrovaná s chladičem pro lištu DIN
- Go to the subcategory
- Jednofázová AC polovodičová relé pro PCB
- Relé rozhraní
- Go to the subcategory
- Jádra a další indukční součásti
- Radiátory, varistory, tepelné ochrany
- Fanoušci
- Klimatizace, příslušenství pro elektrické skříně, chladiče
-
Baterie, nabíječky, vyrovnávací zdroje a střídače
- Baterie, nabíječky - teoretický popis
- Lithium-iontové baterie. Vlastní baterie. Systém správy baterií (BMS)
- Baterie
- Nabíječky baterií a příslušenství
- Záložní zdroj UPS a vyrovnávací napájecí zdroje
- Převaděče a příslušenství pro fotovoltaiku
- Úschovna energie
- Palivové články
- Lithium-iontové baterie
- Go to the subcategory
-
Automatika
- Futaba Drone Parts
- Koncové spínače, mikrospínače
- Senzory, převodníky
- Pyrometrie
- Počítadla, časovače, panelové měřiče
- Průmyslová ochranná zařízení
- Světelná a zvuková signalizace
- Termovizní kamera
- LED displeje
- Tlačítka a spínače
-
Zapisovače
- Zapisovač AL3000
- Rekordér KR2000
- Rekordér KR5000
- Měřič HN-CH s funkcí registrace vlhkosti a teploty
- Spotřební materiál pro zapisovače
- Rekordér 71VR1
- Zapisovač KR 3000
- Počítačové rekordéry řady R1M
- Počítačové rekordéry řady R2M
- PC rekordér, 12 izolovaných vstupů - RZMS-U9
- PC rekordér, USB, 12 izolovaných vstupů - RZUS
- Go to the subcategory
- Go to the subcategory
-
Kabely, dráty, vodiče, flexibilní připojení
- dráty
- lanka
- Kabely pro speciální aplikace
- košile
-
prýmky
- prýmky byt
- prýmky kolo
- Velmi flexibilní opletení - plochý
- Velmi flexibilní opletení - Round
- Měď opletené válcové
- Mědí štít a válcové
- Flexibilní zemnící pásky
- Opletení válcovité pozinkované a nerezové oceli
- PVC izolované měděné pletivo - teplota 85 ° C
- Ploché pletené hliníkové
- Connection Kit - prýmky a trubky
- Go to the subcategory
- Příslušenství pro trakční
- kabelové botky
- Ohebné izolované přípojnice
- Vícevrstvá ohebná lišta
- Systémy vedení kabelů
- Potrubí, trubky
- Go to the subcategory
- View all categories
-
Polovodiče
-
-
- Suppliers
-
Applications
- AC a DC pohony (střídače)
- Automatizace HVAC
- CNC obráběcí stroje
- Energy bank
- Indukční ohřev
- Komponenty pro prostředí s nebezpečím výbuchu (EX)
- Měření a regulace teploty
- Měření a regulace teploty
- Motory a transformátory
- Napájecí zdroje (UPS) a usměrňovací systémy
- Průmyslová automatizace
- Průmyslová automatizace
- Průmyslová ochranná zařízení
- Stroje na sušení a zpracování dřeva
- Stroje na tvarování plastů za tepla
- Svařovací stroje a svářecí stroje
- Těžba, hutnictví a slévárenství
- Tisk
- Tramvajová a železniční trakce
- Zařízení pro distribuční, řídicí a telekomunikační skříně
-
Instalace
-
-
Induktory
-
-
Indukční zařízení
-
-
https://www.dacpol.eu/pl/naprawy-i-modernizacje
-
-
Servis
-
- Kontakt
- Zobacz wszystkie kategorie
Tepelné hospodářství – výzvy pro elektromobily
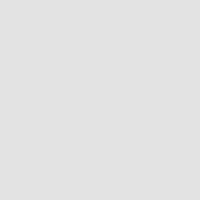
Thermal Management- Challenges for electric vehicles
The change to electric powertrains and the increasing importance of autonomous driving imply a variety of new challenges. Thermal management or rather thermal connectivity and cooling of electrical components have an important role to play. While there is a large number of Thermal Interface Materials, the most common solution for the automotive sector are the Gap Filler Liquids (GFL) and the Softtherm Pads, both of them can be individual customized.
According to the latest calculations by the Federal Ministry of Environment, Germany will significantly miss the self-imposed climate target of reducing CO2 emissions by more than 40% until 2020. In contrast to the trend of other sectors, greenhouse gas emissions from the transport sector even recorded a slight increase compared to the reference year 1990 and are responsible for one fifth of Germany's total emissions. Improved vehicle efficiency could not compensate conflictual factors such as increasing traffic and engine performance. The Federal Government's new climate protection plan envisages a 40-42% reduction in greenhouse gas for the transport sector by 2030, just a small component to meet the 2 ° C target of the Paris climate agreement. Alternative drive systems are essential in order to meet the target of 95 g CO2/km on average for cars. If these values are exceeded, car manufacturers face massive fines. This pricing mechanism has a positive impact on low-emission cars. A global rethink has to take place in the automotive industry.
Thermal Interface Materials
According to forecasts by leading German automobile manufacturers, all top sellers will also be available as an electric car by 2030 at the latest, an extremely ambitious goal. Aspects like an continuous increasing power density or higher heat flow per area (W/m2) and "high power charging" lead to an increased component temperature and consequently to a reduced lifetime in the application.Efficient thermal cooling of electrical components by connecting of the heat source to heat sink, while at the same time having an electrically insulating effect, is therefore a prerequisite for the high quality standards from the automotive sector. This connection and the levelling of appropriate component tolerances, gaps or air inclusions can be realized individually by the wide range of Thermal Interface Materials of KERAFOL, depending on the requirements for thermal conductivity (W/mK) and desired temperature difference ∆T.
Check out our offer of thermal materials
Thermal Management for e-mobility
The change to electric drive systems as well as the increasing importance of autonomous driving imply completely new applications and challenges in the field of "Thermal Management." The functional relationship between the operating temperature of a battery stack and its maximum achievable number of cycles has been sufficiently proven, which can be quantified extremely precisely by the following rule of thumb:
"A reduction in operating temperature by 10°C doubles the lifetime of the battery cells"
The net reach of an electric car is also noticeably dependent on the operating temperature of the battery and thus also indirectly on the present thermal cooling. In addition to the concept for thermal connectivity of the energy source, the "car of tomorrow" also requires solutions for electrical components in the areas of LED, sensor technology, on-board network and inverter, one of the core elements of the electric powertrain.
Thermal Management for electric cars
Gap Filler Liquids
For high volumes in particular, two-component GFL are an efficient and cost-oriented solution. For this purpose, the two components of the ceramic filled silicone elastomers are blended by a mixing tube and can be directly applied to the component (e.g. metal housing) by a dispensing system. In the next step, the electronic components (e.g. IGBTs, capacitors, etc.) are attached under slight pressure to the still uncured mass, thus creating an even distribution of the mass and consequently a defined thickness as well as reproducible electrical and thermal parameters. The cross-linking or curing of the mass takes place under room temperature and lasts about an hour, but can be customized at the customer's request. Primarily the GFL with lower thermal conductivity has a high self-adhesion, which can be very useful for the assembly. Nevertheless, in case of a disassembly the GFL of KERAFOL can be removed again, a property that is not always customary in the market.
Compared to systems based on polyurethane or epoxy, silicon-containing GFL can absorb and compensate vibrations much better, an effect that is favoured by the high softness of the GFL. In addition, the low viscosity of the GFL allows for a simple workability and has a gentle effect on the dispensing system, a thesis that has been confirmed by leading plant manufacturers such as ViscoTec, bdtronic or Scheugenpflug.
Check out our GFL series products
„The GFL of KERAFOL is worldwide used for cooling of inverters, batteries and many other electric components”
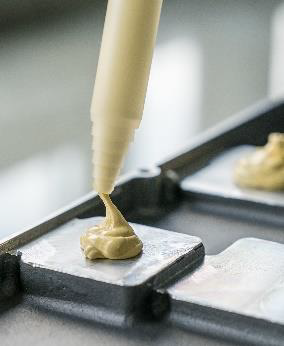
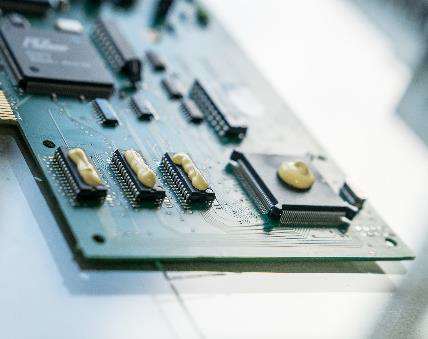
Gap Filler Liquid | |||||
---|---|---|---|---|---|
Basic Material | Thermal Conductivity (W/mK) |
Breakdown Voltage (kV/mm) |
Viscosity (Pas) |
Application Temperature (°C) |
Hardness (Shore 00) |
Silicone | 1,8 - 4,5 | 12 -20 | 45 - 90 | -40 up to +200 | 45 - 70 |
Compared to systems based on polyurethane or epoxy, silicon-containing GFL can absorb and compensate vibrations much better, an effect that is favoured by the high softness of the GFL. In addition, the low viscosity of the GFL allows for a simple workability and has a gentle effect on the dispensing system, a thesis that has been confirmed by leading plant manufacturers such as ViscoTec, bdtronic or Scheugenpflug.
Softtherm Pads
For many thermal connections in the field of e-mobility, classic thermal conducting tapes and pads are still "state of the art." Especially cross-linked silicone-based elastomers, better known as Softtherm Gap Pads, can play a crucial role in thermal cooling (power range up to 6 W/mK) of electronic components due to their variety of specifically adjustable properties.
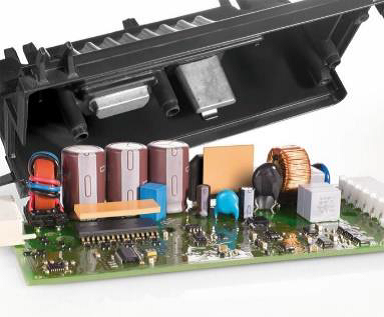
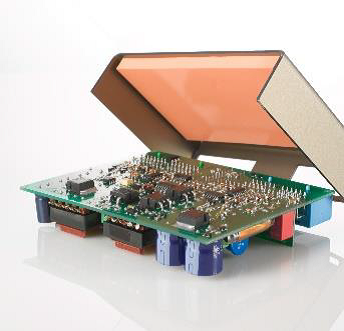
Softtherm Pads | |||||
---|---|---|---|---|---|
Basic Material | Thermal Conductivity (W/mK) |
Breakdown Voltage (kV/mm) |
Compression (%) |
Application Temperature (°C) |
Hardness (Shore 00) |
Silicone | 1,0 - 6,0 | 2 - 16 | up to 40 | -60 up to +250 | 10 - 75 |
Check out our offer of filling materials - Softtherm
Due to the high flexibility and enormous mechanical resistance of the Softtherm Pads, large gap dimensions as well as high component tolerances can be compensated. In addition to individual solutions, such as one-sided adhesive coating for component fixation or fibreglass reinforcement to increase mechanical stability, two-layer films (required by specific regulations) can also be of great added value to the customer. KERAFOL is meeting these customer-specific requirements for many years and finds the right solution for every application. Regardless of which of the "Thermal Interface Materials" is the best solution from a technical and monetary point of view,
KERAFOL together with DACPOL has been meeting these specific customer requirements for many years and finds the right solution for each application. Regardless of which of the "thermally conductive materials" is the best solution from a technical and financial point of view.
Související produkty
Související příspěvky
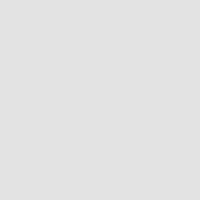
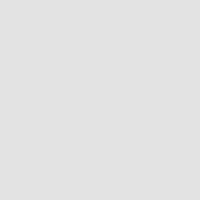
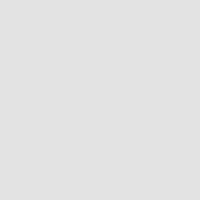
Zanechat komentář