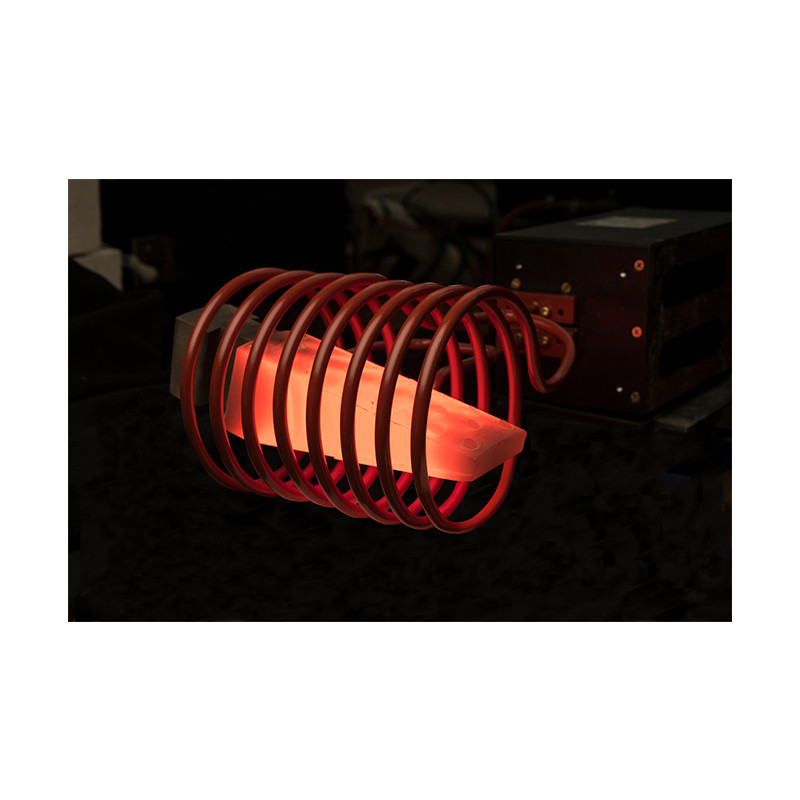
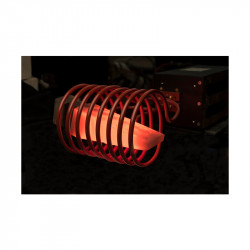
Sie müssen eingeloggt sein
Category
Fotos dienen nur zu Informationszwecken.
please use latin characters
The ultimate test of our equipment is performance on the job. But, even before your system is delivered, your solution will be developed through a comprehensive process review by our engineering team. A feasibility test will be performed in our applications lab and a written and video-recorded solution will be provided to ensure proven results.
With a reputation for quality, built on over 30 years of experience, Ambrell provides innovative heating solutions. Our equipment is installed in over 50 countries and supported by a network of dedicated induction heating experts. If you want to improve your heating application – anywhere in your process – consult with our team for high-efficiency and cost-effective solutions. Ambrell’s technical experts design and manufacture a range of systems to bring you the highest quality induction heating solutions available. Ambrell’s engineers and scientists are responsible for over 30 patents and some of the latest induction heating advances on the market today. By reinvesting over 10% of revenue, we are dedicated to inventing, developing and introducing cutting-edge technology to improve our customers’ manufacturing processes.
Components of Induction Heating Systems
Maximizing production after induction heating
The application of innovative advanced induction heating technology affects many production and financial factors of enterprises, including:
Each application is customized to meet the individual needs of the client.
The versatility of induction heating
Markets served
Stages of project implementation
In order for our team to develop and test the optimal solution for your application, all you need to do are three easy steps:
We also invite you to visit our laboratory, where you can see our state-of-the-art test equipment and hundreds of tested inductors. In addition, you can contact our engineers and hear first-hand how prototype inductors are designed and how successful solutions are run to maximize process efficiency.
Interessieren Sie sich für dieses Produkt? Benötigen Sie zusätzliche Informationen oder individuelle Preise?
Sie müssen eingeloggt sein
The ultimate test of our equipment is performance on the job. But, even before your system is delivered, your solution will be developed through a comprehensive process review by our engineering team. A feasibility test will be performed in our applications lab and a written and video-recorded solution will be provided to ensure proven results.
With a reputation for quality, built on over 30 years of experience, Ambrell provides innovative heating solutions. Our equipment is installed in over 50 countries and supported by a network of dedicated induction heating experts. If you want to improve your heating application – anywhere in your process – consult with our team for high-efficiency and cost-effective solutions. Ambrell’s technical experts design and manufacture a range of systems to bring you the highest quality induction heating solutions available. Ambrell’s engineers and scientists are responsible for over 30 patents and some of the latest induction heating advances on the market today. By reinvesting over 10% of revenue, we are dedicated to inventing, developing and introducing cutting-edge technology to improve our customers’ manufacturing processes.
Components of Induction Heating Systems
Maximizing production after induction heating
The application of innovative advanced induction heating technology affects many production and financial factors of enterprises, including:
Each application is customized to meet the individual needs of the client.
The versatility of induction heating
Markets served
Stages of project implementation
In order for our team to develop and test the optimal solution for your application, all you need to do are three easy steps:
We also invite you to visit our laboratory, where you can see our state-of-the-art test equipment and hundreds of tested inductors. In addition, you can contact our engineers and hear first-hand how prototype inductors are designed and how successful solutions are run to maximize process efficiency.
Your review appreciation cannot be sent
Report comment
Report sent
Your report cannot be sent
Eigenen Kommentar verfassen
Review sent
Your review cannot be sent