Sie müssen eingeloggt sein
-
zurückX
-
Komponenten
-
-
Category
-
Halbleiter
- Dioden
- Thyristoren
-
Elektroisolierte Module
- Elektroisolierte Module | VISHAY (IR)
- Elektroisolierte Module | INFINEON (EUPEC)
- Elektroisolierte Module | Semikron
- Elektroisolierte Module | POWEREX
- Elektroisolierte Module IXYS
- Elektroisolierte Module | POSEICO
- Elektroisolierte Module ABB
- Elektroisolierte Module | TECHSEM
- Gehen Sie zur Unterkategorie
- Brückengleichrichter
-
Transistoren
- Transistoren | GeneSiC
- SiC-MOSFET-Module | Mitsubishi
- SiC-MOSFET-Module | STARPOWER
- ABB SiC-MOSFET-Module
- IGBT-Module | MITSUBISHI
- Transistormodule | MITSUBISHI
- MOSFET-Module von MITSUBISHI
- Transistormodule | ABB
- IGBT-Module | POWEREX
- IGBT-Module | INFINEON (EUPEC)
- Halbleiterkomponente aus Siziliumkarbid
- Gehen Sie zur Unterkategorie
- Treiber
- Leistungsblöcke
- Gehen Sie zur Unterkategorie
- Strom- und Spannungswandler von LEM
-
Passive Elemente (Kondensatoren, Widerstände, Sicherungen, Filter)
- Widerstände
-
Sicherungen
- Miniatursicherungen für elektronische Schaltungen der Serien ABC und AGC
- Schnelle Röhrensicherungen
- Zeitverzögerungssicherungen mit GL / GG- und AM-Eigenschaften
- Ultraschnelle Sicherungseinsätze
- Britische und amerikanische schnelle Sicherungen
- Schnelle europäische Sicherungen
- Traktionssicherungen
- Hochspannungs-Sicherungseinsätze
- Gehen Sie zur Unterkategorie
-
Kondensatoren
- Kondensatoren für Motoren
- Elektrolytkondensator
- Island Filmkondensatoren
- Leistungskondensatoren
- Kondensatoren für Gleichstromkreise
- Kondensatoren zur Leistungskompensation
- Hochspannungskondensatoren
- Induktionsheizkondensatoren
- Impulskondensatoren
- DC LINK-Kondensatoren
- Kondensatoren für AC / DC-Schaltungen
- Gehen Sie zur Unterkategorie
- Entstörungsfilter
- Superkondensatoren
-
Überspannungsschutz
- Überspannungsableiter für HF-Anwendungen
- Überspannungsableiter für Bildverarbeitungssysteme
- Überspannungsableiter für Stromleitungen
- Überspannungsableiter für LED
- Überspannungsableiter für die Photovoltaik
- Überspannungsableiter für Wägesysteme
- Überspannungsableiter für den Feldbus
- Gehen Sie zur Unterkategorie
- Gehen Sie zur Unterkategorie
-
Relais und Schütze
- Theorie der Relais und Schütze
- Dreiphasen-Halbleiterrelais AC
- Halbleiterrelais DC
- Regler, Steuerungen und Zubehör
- Sanftstarter und Schaltschütze
- Elektromechanische Relais
- Schütze
- Drehschalter
-
Einphasen-Halbleiterrelais AC
- Einphasen-Wechselstrom-Halbleiterrelais, Serie 1 | D2425 | D2450
- Einphasige AC-Halbleiterrelais der Serien CWA und CWD
- Einphasen-Wechselstrom-Halbleiterrelais der Serien CMRA und CMRD
- Einphasen-Wechselstrom-Halbleiterrelais, PS-Serie
- Doppel- und Vierfach-Wechselstrom-Halbleiterrelais, Serie D24 D, TD24 Q, H12D48 D.
- 1-phasige Festkörperrelais, gn-Serie
- Einphasige Wechselstrom-Halbleiterrelais, Serie ckr
- Einphasen-Wechselstromrelais der ERDA- UND ERAA-SERIE für die DIN-Schiene
- Einphasige Wechselstromrelais für 150A Strom
- Doppelte Halbleiterrelais mit integriertem Kühlkörper für eine DIN-Schiene
- Gehen Sie zur Unterkategorie
- Einphasen-Halbleiterrelais AC für Leiterplatten
- Interface-Relais
- Gehen Sie zur Unterkategorie
- Induktive Komponente
- Radiatoren, Varistoren, Thermoschütze
- Ventilatoren
- Klimaanlagen, Ausrüstung für Schaltschränke, Industriekühler
-
Batterien, Ladegeräte, Pufferstromversorgungen und Wechselrichter
- Batterien, Ladegeräte - theoretische Beschreibung
- Lithium-Ionen-Batterien. Kundenspezifische Batterien. Batteriemanagementsystem (BMS)
- Batterien
- Ladegeräte und Zubehör
- USV-Notstromversorgung und Pufferstromversorgung
- Konverter und Zubehör für die Photovoltaik
- Energiespeicher
- Brennstoffzellen
- Lithium-Ionen-Batterien
- Gehen Sie zur Unterkategorie
-
Automation
- Futaba Drone Parts
- Grenzschalter, Microschalter
- Sensoren, Wandler
-
Pyrometer
- Infrarot-Temperatursensor, kabellos, wasserdicht, IR-TE-Serie
- Infrarot-Temperatursensor, kabellos, IR-TA-Serie
- Infrarot-Temperatursensor, kabellos, IR-H-Serie
- Ein schnelles stationäres Pyrometer in einem sehr kleinen IR-BA-Gehäuse
- Lichtleiter-Temperatursensoren, IR-FA-Serie
- Das stationäre Pyrometer der IR-BZ-Serie
- Gehen Sie zur Unterkategorie
- Zähler, Zeitrelais, Einbaumessgeräte
- Industrielle Schutzausrüstung
- Licht- und Signalentechnik
- Infrarot-Kamera
- LED-Anzeigen
- Taster, Schalter und Zubehör
-
Datenerfassung und Datenlogger
- Temperaturschreiber mit Display und Textdruck AL3000
- Digitale Temperaturschreiber mit LCD Display KR 2000-Serie
- Sicherheitstemperaturwächter KR 5000
- Temperatur / Feuchtigkeit Hand-Meter mit Datenlogger HN-CH-Serie
- Messdatenerfassung und Datenlogger Zubehör
- Kompakter Bildschirmschreiber 71VR1
- Sicherheitstemperaturwächter KR 3000-Serie
- PC-Datenerfassung R1M-Serie
- PC-Datenerfassung R2M-Serie
- PC-Datenerfassung, 12 universelle isolierte Eingänge, Typ RZMS-U9
- PC-Datenerfassung, 12 universelle isolierte Eingänge, USB, RZUS-Serie
- Gehen Sie zur Unterkategorie
- Gehen Sie zur Unterkategorie
-
Adern, Litzen, Schutzhüllen, Flexible Verbingungen
- Drähte
- Litzen
-
Kabel für spezielle Anwendungen
- Verlängerungskabel und Kompensations
- Kabel für Thermoelemente
- Die Verbindungsdrähte zu czyjnków PT
- Mehradrige Kabel Temp. -60 ° C bis + 1400 ° C
- SILICOUL Mittelspannungskabeln
- Zündkabel
- Heizleitungen
- Einadriges Temp. -60 ° C bis + 450 ° C
- Zugbegleiter
- Heizleitungen im Ex
- Gehen Sie zur Unterkategorie
- Schläuche
-
Geflochtene Kabel
- Zöpfe flach
- Zöpfen Runde
- Sehr flexible Geflecht - flach
- Sehr flexible Geflecht - Rund
- Kupfergeflecht zylindrischen
- Kupfergeflechtschirm und zylindrischer
- Flexible Massebänder
- Geflechte zylindrischen verzinkt und Edelstahl
- PVC-isolierte Kupferlitzen - Temperatur 85 ° C
- Flach geflochtene Aluminium
- Connection Kit - Zöpfe und Röhren
- Gehen Sie zur Unterkategorie
- Leitungen und Sonstiges für Traktion
- Crimpverbinder
- Flexible isolierte Kupferschienen
- Mehrschichte flexible Kupferschienen
- Kabelrohre, Kabelkanäle und Kabelführung
- Kabelschutzschlauchsysteme
- Gehen Sie zur Unterkategorie
- Alle Kategorien
-
Halbleiter
-
-
- Lieferanten
-
Applications
- AC- und DC-Antriebe (Wechselrichter)
- Ausrüstung für Verteilungs-, Steuerungs- und Telekommunikationsschränke
- Bergbau, Metallurgie und Gründung
- CNC-Werkzeugmaschinen
- Energy bank
- HLK-Automatisierung
- Induktionsheizung
- Industrielle Automatisierung
- Industrielle Automatisierung
- Industrielle Schutzvorrichtungen
- Komponenten für explosionsgefährdete Bereiche (EX)
- Maschinen zum Tiefziehen von Kunststoffen
- Maschinen zum Trocknen und Verarbeiten von Holz
- Motoren und Transformatoren
- Schweißmaschinen und Schweißmaschinen
- Straßenbahn- und Bahntraktion
- Temperaturmessung und -regelung
- Temperaturmessung und -regelung
- USV- und Gleichrichtersysteme
-
Installation
-
-
Inductors
-
-
Induktionsgeräte
-
-
https://www.dacpol.eu/pl/naprawy-i-modernizacje
-
-
Service
-
- Kontakt
- Zobacz wszystkie kategorie
The use of induction heating in the manufacture of industrial equipment
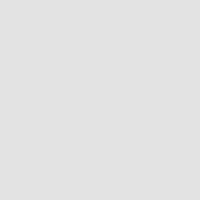
Induction heating is a method of heating conductive materials that is gaining more and more popularity in industrial applications. Compared to conventional heating methods, induction heating provides the highest safety for workers through contact-free operation.
The technology is developing rapidly and there are more and more solutions and devices using it on the market. The vast majority of companies decide to switch to such a solution, due to the savings of time and money associated with heating processes.
What is induction heating?
Induction heating is a method of heating conductive materials used in the production and machining of mechanical parts or industrial machine components. The process involves placing the workpiece near an induction coil through which an alternating current is passed. As the current flows through the coil, an alternating magnetic field is generated in its field, which initiates eddy currents within the workpiece material. Unlike common heating methods, in induction the heat is not supplied from outside, but is generated in the workpiece itself. This gives many advantages for production processes, energy consumption and working conditions.
The benefits of induction heating:
- Saves energy and reduces CO₂ emissions, thanks to short heating times;
- All induction processes are easily repeatable;
- Precision heating significantly reduces scrap and rework;
- Ability to automate and integrate with other manufacturing processes;
- Even the largest induction systems take up relatively little space;
- Induction processes are easy to use;
- Each solution can be easily selected and adapted to each application.
Induction heating systems
Each induction heating system consists of an induction generator, a workstation and an induction coil. Additionally, depending on the application, peripheral devices supporting the system operation can be added, such as chillers for the coil cooling water, pyrometers for measuring the heating temperature, industrial regulators for controlling the generator operation.
Induction generators are responsible for converting input current into alternating current at a specific frequency. By selecting the appropriate power and frequency range of the generator, we can adjust the heating time and heat penetration depth of the heat-treated material, depending on the size and weight of the work insert.
Workstations are components of a heating system in which induction coils are placed. Depending on the solution, the workstation may be built into the generator or may exist as an independent part of the unit to facilitate equipment operation. In most cases, cooling water also flows through the workstation and is then directed to the heating coil.
The coil itself is the element through which heat is generated in the workpiece. By selecting the size, shape and design of the coil, we can achieve different types of heating - from spot heating to area heating. The coils are usually made of copper, because copper conducts electricity very well, and by using a cooling system, we can reduce excessive heating of the coil.
Induction heating applications
- Induction heating is used in many heating processes. The most important of these are:
- Soldering and brazing;
- Heating, bonding;
- Shrink fitting;
- Annealing, hardening, tempering and curing;
- Melting and hot forming;
- Forging;
- Stacking;
- Sealing;
- Glaze removal;
- Material testing.
Except for the aforementioned applications, induction heating is used in high-tech applications where specific standards and high hygiene are required, e.g. medical applications (nanoparticle technology), chemical industry, etc.
Ähnliche Produkte
Ähnliche Beiträge
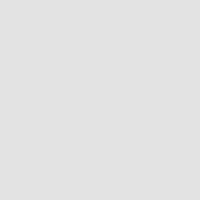
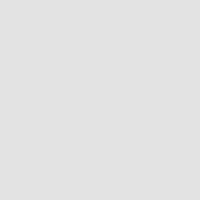
Hinterlassen Sie einen Kommentar