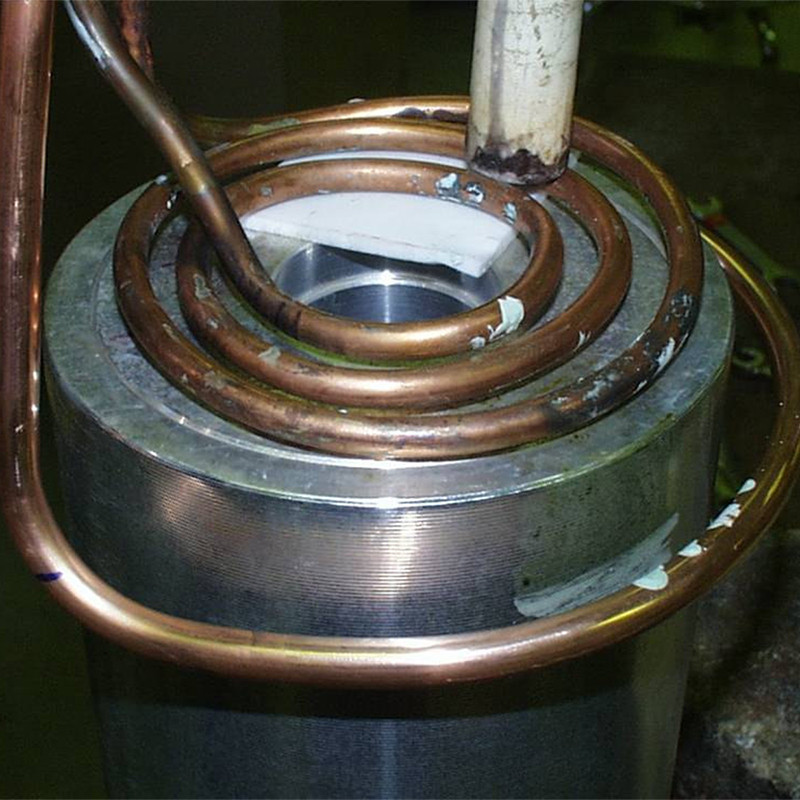
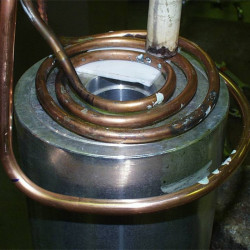
Category
Photos are for informational purposes only. View product specification
please use latin characters
Objective: Heat the end of an aluminum copier roller to 400 ºF (200 ºC) to cure epoxy
Material: Aluminum roller 4.75” (120mm) diameter, 2’ (0.6m) long with 1.5” (38.1mm) thick plug at end
Temperature: 400 ºF (200 ºC)
Frequency: 112 kHz
Process: A four turn helical pancake coil is used to heat the end of the copier roller assembly. The assembly is heated 90 seconds to cure the adhesive.
Benefits: Induction heating provides:
Are you interested in this product? Do you need additional information or individual pricing?
Objective: Heat the end of an aluminum copier roller to 400 ºF (200 ºC) to cure epoxy
Material: Aluminum roller 4.75” (120mm) diameter, 2’ (0.6m) long with 1.5” (38.1mm) thick plug at end
Temperature: 400 ºF (200 ºC)
Frequency: 112 kHz
Process: A four turn helical pancake coil is used to heat the end of the copier roller assembly. The assembly is heated 90 seconds to cure the adhesive.
Benefits: Induction heating provides:
Your review appreciation cannot be sent
Report comment
Report sent
Your report cannot be sent
Write your review
Review sent
Your review cannot be sent