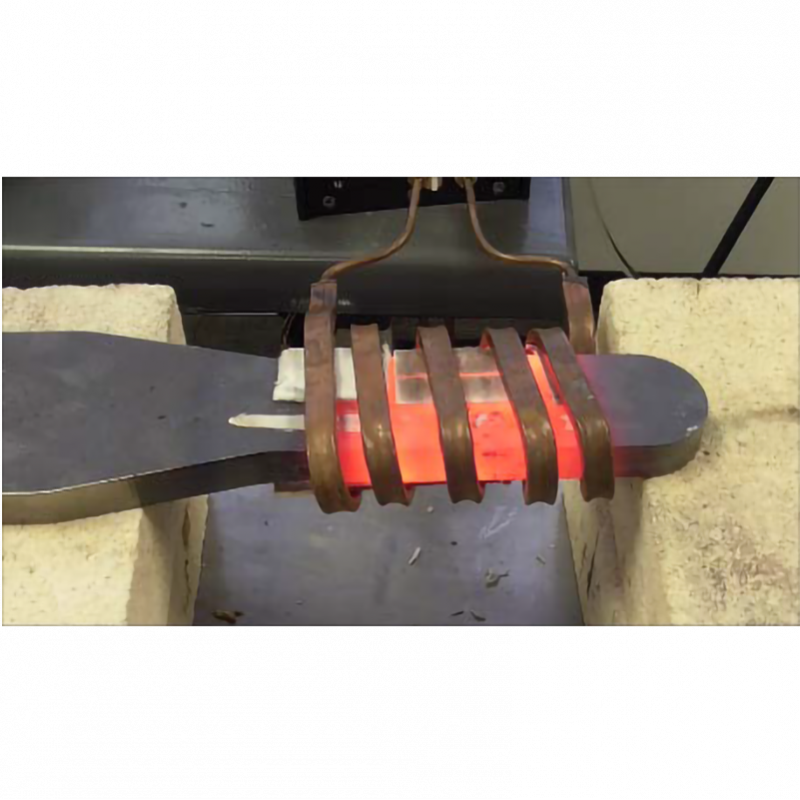
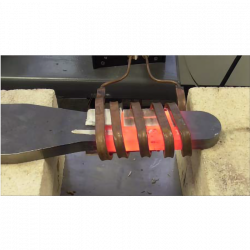
Category
Photos are for informational purposes only. View product specification
please use latin characters
Objective: To heat a magnetic steel part for a forming application; the client had been using a torch for the application.
Frequency: 125 kHz
Material: Magnetic steel part
Temperature: 1700 °F (927 °C)
Temperature indicating paint was applied to the part to easily identify when it achieved temperature, and then the induction power was turned on. It took about three minutes for the part to reach 1700 °F (927 °C) at 10 kW and two minutes and twenty seconds with 15 kW for this through-Curie heating application.
Are you interested in this product? Do you need additional information or individual pricing?
Objective: To heat a magnetic steel part for a forming application; the client had been using a torch for the application.
Frequency: 125 kHz
Material: Magnetic steel part
Temperature: 1700 °F (927 °C)
Temperature indicating paint was applied to the part to easily identify when it achieved temperature, and then the induction power was turned on. It took about three minutes for the part to reach 1700 °F (927 °C) at 10 kW and two minutes and twenty seconds with 15 kW for this through-Curie heating application.
Your review appreciation cannot be sent
Report comment
Report sent
Your report cannot be sent
Write your review
Review sent
Your review cannot be sent