
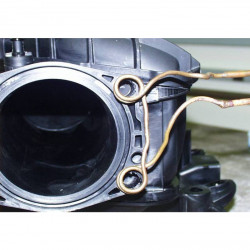
Category
Photos are for informational purposes only. View product specification
please use latin characters
Objective: Heat a 0.50” (12.7)mm brass insert for debonding application.
Frequency: 215 kHz
Material: Intake manifold and 0.50” (12.7)mm diameter brass insert.
Temperature: 500 °F (260 °C)
A four-turn two-position helical coil is used to debond the inserts from the plastic. The coil is placed against the manifold and power is applied to the two inserts for 15 seconds to soften the plastic. Power is turned off and a threaded steel screw is inserted into the parts and the inserts are easily removed from the manifold.
This debonding process is for recycling 10,000 defective parts that QES has received the contract for debond the brass from the plastic and recycle the plastic. Induction makes it possible to simultaneously heat both inserts for removal saving time in the recycle process.
Are you interested in this product? Do you need additional information or individual pricing?
Objective: Heat a 0.50” (12.7)mm brass insert for debonding application.
Frequency: 215 kHz
Material: Intake manifold and 0.50” (12.7)mm diameter brass insert.
Temperature: 500 °F (260 °C)
A four-turn two-position helical coil is used to debond the inserts from the plastic. The coil is placed against the manifold and power is applied to the two inserts for 15 seconds to soften the plastic. Power is turned off and a threaded steel screw is inserted into the parts and the inserts are easily removed from the manifold.
This debonding process is for recycling 10,000 defective parts that QES has received the contract for debond the brass from the plastic and recycle the plastic. Induction makes it possible to simultaneously heat both inserts for removal saving time in the recycle process.
Your review appreciation cannot be sent
Report comment
Report sent
Your report cannot be sent
Write your review
Review sent
Your review cannot be sent