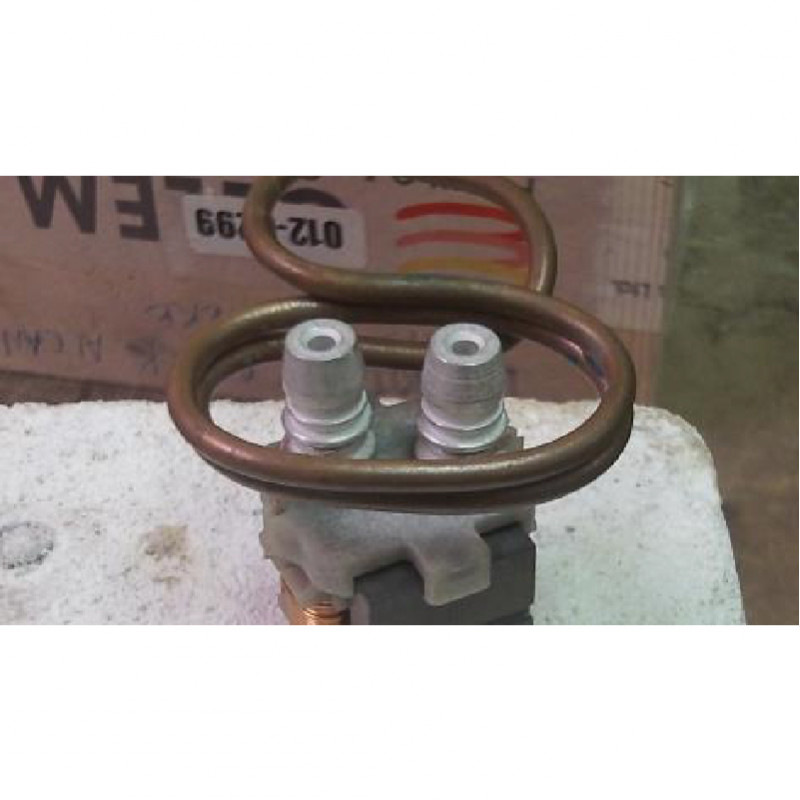
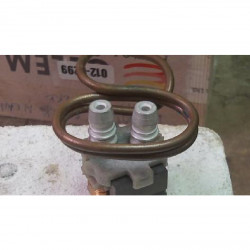
Category
Photos are for informational purposes only. View product specification
please use latin characters
Objective: To solder a pair of magnetic steel pins/posts to create an automotive component.
Frequency: 214 kHz
Material: Coil and steel pin assembly (5/16”/7.9 mm pin/post O.D.)
Temperature: 470 °F (243 °C)
Any remaining insulation on the wire was removed with sandpaper. A foot peddle was part of the induction heating system setup to facilitate manual feeding of the solder. The part was placed in the coil and the power was turned on. After seven seconds the solder began to flow and the solder was fed to the joint. Power was pulsed for one additional second to allow the solder to continue to be fed. The overall process took less than ten seconds.
Are you interested in this product? Do you need additional information or individual pricing?
Objective: To solder a pair of magnetic steel pins/posts to create an automotive component.
Frequency: 214 kHz
Material: Coil and steel pin assembly (5/16”/7.9 mm pin/post O.D.)
Temperature: 470 °F (243 °C)
Any remaining insulation on the wire was removed with sandpaper. A foot peddle was part of the induction heating system setup to facilitate manual feeding of the solder. The part was placed in the coil and the power was turned on. After seven seconds the solder began to flow and the solder was fed to the joint. Power was pulsed for one additional second to allow the solder to continue to be fed. The overall process took less than ten seconds.
Your review appreciation cannot be sent
Report comment
Report sent
Your report cannot be sent
Write your review
Review sent
Your review cannot be sent