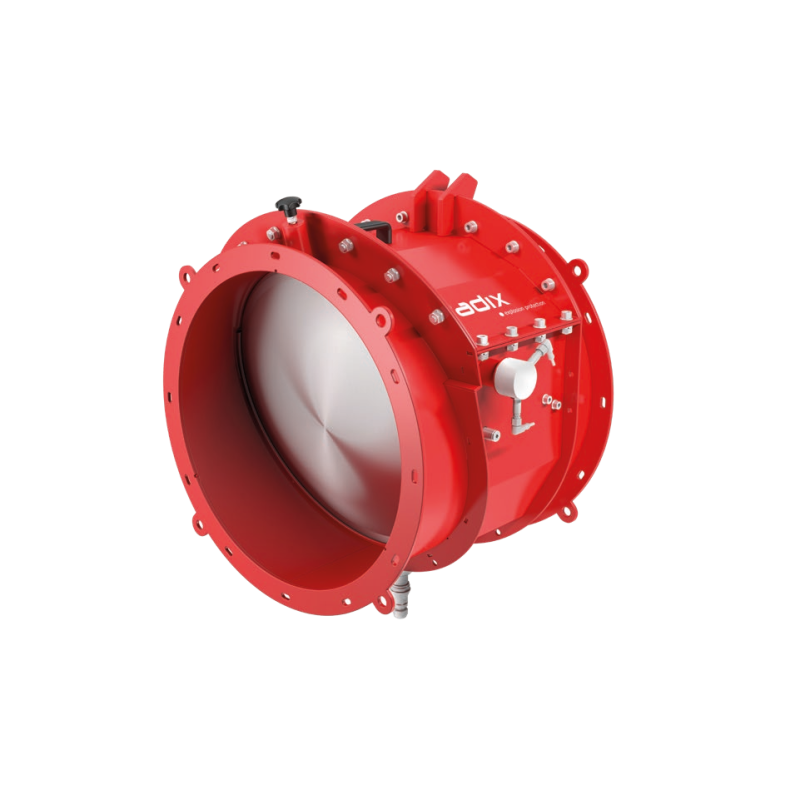
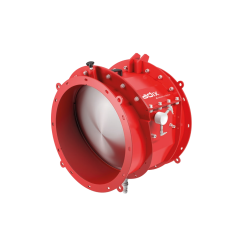
Category
Photos are for informational purposes only. View product specification
please use latin characters
Explosion Isolation Method
The explosion isolation method involves preventing flames from escaping outside the installation where an explosion occurred. In the absence of this type of protection, there is a risk that sparks or flames escaping could become effective sources of ignition for the surrounding explosive atmosphere.
Application
The NOVEx II series is a protection system consisting of a passive flame arrester for cutting off explosive dust and holds a certificate of compliance with harmonized standards EN16447:2014 and EN15089:2009. NOVEx II valves are used to prevent the spread of an explosion from dust filters to the inlet of polluted air and/or the outlet of clean air. In this case, the filter must be additionally protected with explosion panels or explosion suppression.
Key Information
Dimensions and Versions
ATEX-certified NOVEx II return valves are available in popular sizes from DN100 to DN1250 (DIN 24154/R2, T2).
Options: ANSI flanges, open and/or closed valve position detection, product sediment detection, automatic cleaning system, valve wear detection, pressure drop monitoring support ring, for vertical installation.
Characteristics
Pressure Drop
Order Code
Unprotected System Challenges
In an unprotected system, it is not the first explosion that causes the most damage, but subsequent secondary explosions. Explosion suppression and explosion-resistant design solve a significant part of the problem, but in both cases, isolation still plays a crucial role. Several methods are available in the market to implement this idea.
Isolation Through Existing Process Elements
Various types of explosion isolation can be achieved by utilizing existing process elements such as rotary valves, roots blowers, screw conveyors, double valves (lock-type), or check valves.
Isolation Through Passive Elements
A wide range of passive elements is also offered, including flame arresters, quick-closing VENTEX valves, and explosion relief chimneys. These operate without external detection or control.
Isolation Through Active Elements
Several active systems also help prevent explosions, such as quick-closing gates, chemical barriers, fire dampers, and switching valves. All are operated by a detector above the control system.
Are you interested in this product? Do you need additional information or individual pricing?
Explosion Isolation Method
The explosion isolation method involves preventing flames from escaping outside the installation where an explosion occurred. In the absence of this type of protection, there is a risk that sparks or flames escaping could become effective sources of ignition for the surrounding explosive atmosphere.
Application
The NOVEx II series is a protection system consisting of a passive flame arrester for cutting off explosive dust and holds a certificate of compliance with harmonized standards EN16447:2014 and EN15089:2009. NOVEx II valves are used to prevent the spread of an explosion from dust filters to the inlet of polluted air and/or the outlet of clean air. In this case, the filter must be additionally protected with explosion panels or explosion suppression.
Key Information
Dimensions and Versions
ATEX-certified NOVEx II return valves are available in popular sizes from DN100 to DN1250 (DIN 24154/R2, T2).
Options: ANSI flanges, open and/or closed valve position detection, product sediment detection, automatic cleaning system, valve wear detection, pressure drop monitoring support ring, for vertical installation.
Characteristics
Pressure Drop
Order Code
Unprotected System Challenges
In an unprotected system, it is not the first explosion that causes the most damage, but subsequent secondary explosions. Explosion suppression and explosion-resistant design solve a significant part of the problem, but in both cases, isolation still plays a crucial role. Several methods are available in the market to implement this idea.
Isolation Through Existing Process Elements
Various types of explosion isolation can be achieved by utilizing existing process elements such as rotary valves, roots blowers, screw conveyors, double valves (lock-type), or check valves.
Isolation Through Passive Elements
A wide range of passive elements is also offered, including flame arresters, quick-closing VENTEX valves, and explosion relief chimneys. These operate without external detection or control.
Isolation Through Active Elements
Several active systems also help prevent explosions, such as quick-closing gates, chemical barriers, fire dampers, and switching valves. All are operated by a detector above the control system.
Your review appreciation cannot be sent
Report comment
Report sent
Your report cannot be sent
Write your review
Review sent
Your review cannot be sent