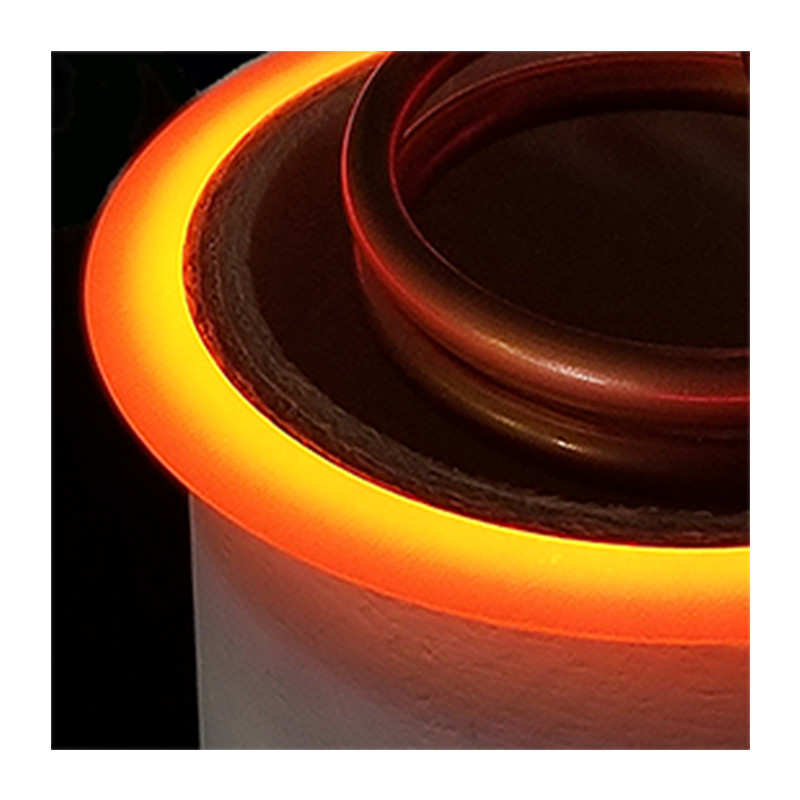
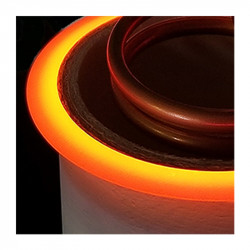
Category
Photos are for informational purposes only. View product specification
please use latin characters
Annealing is a heat treatment in which a material such as copper is exposed to an elevated temperature for an extended time and then slowly cooled. Annealing heat treatments are largely characterized by induced microstructural changes which are ultimately responsible for altering the material's mechanical properties. The ultimate goal of this process is to reduce the hardness of the metal and improve its ductility.
Annealing specifically refers to the process of bringing the material to its softest possible point. A tempering process softens the metal but not to the full extent possible.
Modern induction heating provides many advantages over other heating methods and is commonly used for annealing applications such as copper pipe bending. Heating through induction provides reliable, repeatable, non-contact and energy-efficient heat in a minimal amount of time without the use of flame or torch. Solid state systems are capable of heating very small areas within precise production tolerances, without disturbing individual metallurgical characteristics.
Induction can be used for either surface or through heating; case annealing is possible depending on time, temperature and the material's characteristics.
The degree of temper depends on the material, the maximum temperature reached and the length of the cool down time. Process or Stress Relief Annealing is used to negate the effects of cold work; that is, to soften and increase the ductility of a previously strain-hardened metal. Internal stresses may develop as a result of plastic deformation processes such as machining or grinding, non-uniform cooling in a welding or casting process, or a phase transformation. Distortion and warping may occur if the internal stresses are not removed. Annealing will eliminate these stresses when the part is heated to the recommended temperature, held there long enough, and slowly cooled to room temperature.
Closed loop control, through the use of an optical pyrometer or other temperature sensing device, can provide constant heat with a tolerance as low as 3°C at 700°C. Induction heating also ideal for in-line production processes because of its ability to produce repeatable, rapid and accurate heating cycles.
Induction systems typically used for induction annealing range from 1 to 20kW, depending on the parts and application requirements.
Are you interested in this product? Do you need additional information or individual pricing?
Annealing is a heat treatment in which a material such as copper is exposed to an elevated temperature for an extended time and then slowly cooled. Annealing heat treatments are largely characterized by induced microstructural changes which are ultimately responsible for altering the material's mechanical properties. The ultimate goal of this process is to reduce the hardness of the metal and improve its ductility.
Annealing specifically refers to the process of bringing the material to its softest possible point. A tempering process softens the metal but not to the full extent possible.
Modern induction heating provides many advantages over other heating methods and is commonly used for annealing applications such as copper pipe bending. Heating through induction provides reliable, repeatable, non-contact and energy-efficient heat in a minimal amount of time without the use of flame or torch. Solid state systems are capable of heating very small areas within precise production tolerances, without disturbing individual metallurgical characteristics.
Induction can be used for either surface or through heating; case annealing is possible depending on time, temperature and the material's characteristics.
The degree of temper depends on the material, the maximum temperature reached and the length of the cool down time. Process or Stress Relief Annealing is used to negate the effects of cold work; that is, to soften and increase the ductility of a previously strain-hardened metal. Internal stresses may develop as a result of plastic deformation processes such as machining or grinding, non-uniform cooling in a welding or casting process, or a phase transformation. Distortion and warping may occur if the internal stresses are not removed. Annealing will eliminate these stresses when the part is heated to the recommended temperature, held there long enough, and slowly cooled to room temperature.
Closed loop control, through the use of an optical pyrometer or other temperature sensing device, can provide constant heat with a tolerance as low as 3°C at 700°C. Induction heating also ideal for in-line production processes because of its ability to produce repeatable, rapid and accurate heating cycles.
Induction systems typically used for induction annealing range from 1 to 20kW, depending on the parts and application requirements.
Your review appreciation cannot be sent
Report comment
Report sent
Your report cannot be sent
Write your review
Review sent
Your review cannot be sent