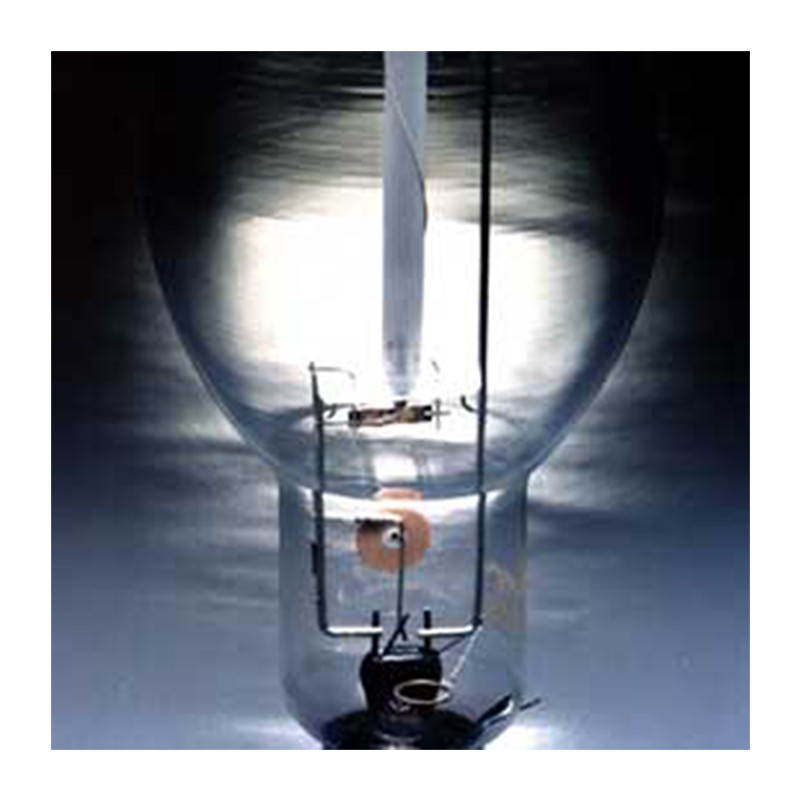
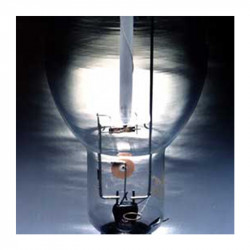
Category
Photos are for informational purposes only. View product specification
please use latin characters
The process of getter firing or getter flashing overcomes a specific hurdle which arises during the production of sealed glass tubes. How can an oxygen-free vacuum be produced to extend the life of the filament? The answer is to remove residual gases by heating a metallic disk, known as a getter, inside the bulb.
The getter is coated with Barium, which has an extremely high affinity for oxygen and nitrogen. After the bulb has been pumped down and sealed, the getter is heated to vaporize or "flash" the barium for maximum dispersion, and "get" any residual gas within the tube.
Getter firing is used in manufacturing to extend the life of laser tubes, neon tubes, fluorescent lamps, other high intensity lamps and television picture tubes.
Since the round steel disk is an ideal load for a round induction coil, modern induction heating systems quickly and easily heat getters through the glass bulb. Temperatures as high as 1100°C can be reached within 1 second to "flash" or vaporize the metal. Heating with induction is reliable, repeatable, non-contact and energy-efficient. Solid state systems, when used in conjunction with temperature sensing and control equipment, are capable of heating very small areas within precise production tolerances.
Typical RF power supplies for getter firing range from 3 to 10kW, depending on the parts and application requirements.
Are you interested in this product? Do you need additional information or individual pricing?
The process of getter firing or getter flashing overcomes a specific hurdle which arises during the production of sealed glass tubes. How can an oxygen-free vacuum be produced to extend the life of the filament? The answer is to remove residual gases by heating a metallic disk, known as a getter, inside the bulb.
The getter is coated with Barium, which has an extremely high affinity for oxygen and nitrogen. After the bulb has been pumped down and sealed, the getter is heated to vaporize or "flash" the barium for maximum dispersion, and "get" any residual gas within the tube.
Getter firing is used in manufacturing to extend the life of laser tubes, neon tubes, fluorescent lamps, other high intensity lamps and television picture tubes.
Since the round steel disk is an ideal load for a round induction coil, modern induction heating systems quickly and easily heat getters through the glass bulb. Temperatures as high as 1100°C can be reached within 1 second to "flash" or vaporize the metal. Heating with induction is reliable, repeatable, non-contact and energy-efficient. Solid state systems, when used in conjunction with temperature sensing and control equipment, are capable of heating very small areas within precise production tolerances.
Typical RF power supplies for getter firing range from 3 to 10kW, depending on the parts and application requirements.
Your review appreciation cannot be sent
Report comment
Report sent
Your report cannot be sent
Write your review
Review sent
Your review cannot be sent