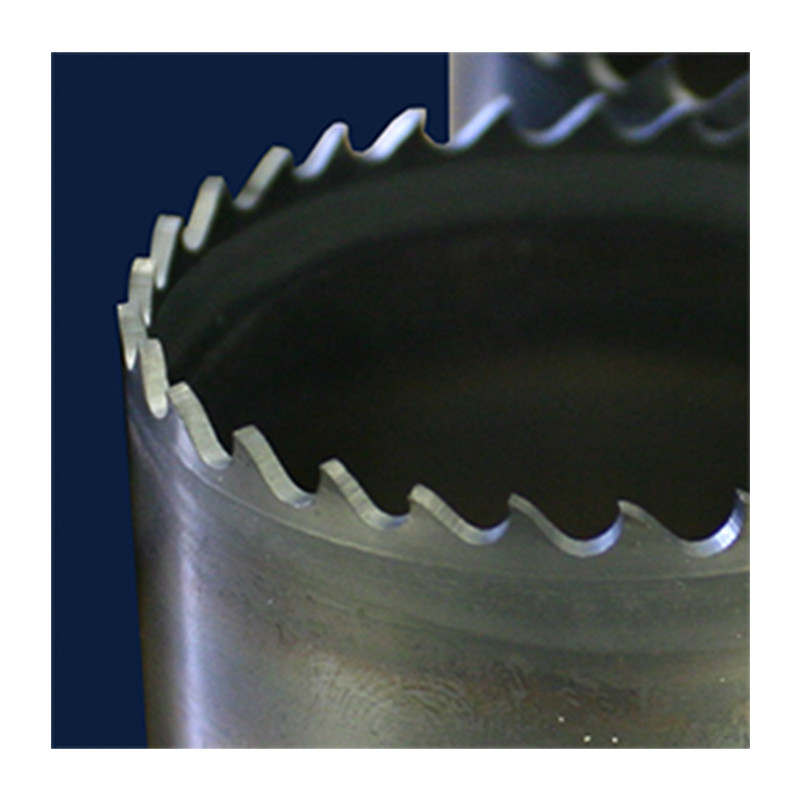
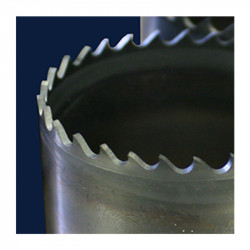
Category
Photos are for informational purposes only. View product specification
please use latin characters
Hardening is a type of heat treatment aimed at achieving increased hardness, strength, and wear resistance with reduced plasticity and increased brittleness. Depending on the depth of hardening, there are volume hardening and surface hardening processes. Volume hardening involves heating the material throughout its cross-section to the desired transformation temperature, holding it at this temperature, and cooling it at the appropriate rate. This process is used for hardening medium-carbon and high-carbon steels to achieve moderate strength and hardness. Surface hardening involves rapidly heating the thin outer layer of the material to the required transformation temperature and cooling it quickly. This results in increased hardness and strength only to the intended depth, with an unhardened structure in the rest of the material. Common cooling media include oil, air, water, water with soluble polymers, etc.
Modern induction heating provides reliable, contactless heating in minimal time without a flame. An important feature is the repeatability and accuracy of the process – the ability to set the time, temperature, control the depth of hardening, cooling, and the segment of the part to be treated. Semiconductor systems can even heat very small areas within precise process tolerance ranges.
Induction hardening is performed in two ways. The first is static hardening, which involves heating the element without changing the position of the part or the inductor relative to each other. This method is characterized by speed, the lack of need for complex automation, and allows for very precise determination of the heating area, even for parts with complicated shapes. The second method is progressive hardening, which involves heating the element while changing the position of the part and the inductor relative to each other. This allows hardening of parts with large surfaces and sizes, as well as heating several specific areas within a single part, without the need for manual repositioning.
Heat treatment using induction systems is ideal for applications in industries requiring automated, precise, and fast processes. Induction heating is particularly useful for larger manufacturers with multiple production lines operating continuously, due to the increased efficiency. For smaller manufacturers, an additional advantage is the almost immediate start-up of the machine. In case of production breaks, the machine does not need to remain constantly on, unlike conventional furnaces.
Tempering is a type of heat treatment aimed at reducing brittleness, fragility, and hardness to the required level, as well as removing hardening stresses in steel previously hardened. This process is performed at relatively low temperatures, lower than the hardening temperature. The element is heated, held at an elevated temperature for a certain period, and then slowly cooled.
Tempering performed using induction systems offers many benefits described with hardening, such as shorter process times (even in the range of seconds!), energy savings, the ability to control precisely, and repeatability. Integrating such systems into production lines simplifies process management, speeds up production, and increases profits.
Are you interested in this product? Do you need additional information or individual pricing?
Hardening is a type of heat treatment aimed at achieving increased hardness, strength, and wear resistance with reduced plasticity and increased brittleness. Depending on the depth of hardening, there are volume hardening and surface hardening processes. Volume hardening involves heating the material throughout its cross-section to the desired transformation temperature, holding it at this temperature, and cooling it at the appropriate rate. This process is used for hardening medium-carbon and high-carbon steels to achieve moderate strength and hardness. Surface hardening involves rapidly heating the thin outer layer of the material to the required transformation temperature and cooling it quickly. This results in increased hardness and strength only to the intended depth, with an unhardened structure in the rest of the material. Common cooling media include oil, air, water, water with soluble polymers, etc.
Modern induction heating provides reliable, contactless heating in minimal time without a flame. An important feature is the repeatability and accuracy of the process – the ability to set the time, temperature, control the depth of hardening, cooling, and the segment of the part to be treated. Semiconductor systems can even heat very small areas within precise process tolerance ranges.
Induction hardening is performed in two ways. The first is static hardening, which involves heating the element without changing the position of the part or the inductor relative to each other. This method is characterized by speed, the lack of need for complex automation, and allows for very precise determination of the heating area, even for parts with complicated shapes. The second method is progressive hardening, which involves heating the element while changing the position of the part and the inductor relative to each other. This allows hardening of parts with large surfaces and sizes, as well as heating several specific areas within a single part, without the need for manual repositioning.
Heat treatment using induction systems is ideal for applications in industries requiring automated, precise, and fast processes. Induction heating is particularly useful for larger manufacturers with multiple production lines operating continuously, due to the increased efficiency. For smaller manufacturers, an additional advantage is the almost immediate start-up of the machine. In case of production breaks, the machine does not need to remain constantly on, unlike conventional furnaces.
Tempering is a type of heat treatment aimed at reducing brittleness, fragility, and hardness to the required level, as well as removing hardening stresses in steel previously hardened. This process is performed at relatively low temperatures, lower than the hardening temperature. The element is heated, held at an elevated temperature for a certain period, and then slowly cooled.
Tempering performed using induction systems offers many benefits described with hardening, such as shorter process times (even in the range of seconds!), energy savings, the ability to control precisely, and repeatability. Integrating such systems into production lines simplifies process management, speeds up production, and increases profits.
Your review appreciation cannot be sent
Report comment
Report sent
Your report cannot be sent
Write your review
Review sent
Your review cannot be sent