-
BackX
-
Components
-
-
Category
-
Semiconductors
- Diodes
- Thyristors
-
Electro-insulated Modules
- Electro-insulated Modules | VISHAY (IR)
- Electro-insulated Modules | INFINEON (EUPEC)
- Electro-insulated Modules | Semikron
- Electro-insulated Modules | POWEREX
- Electro-insulated Modules | IXYS
- Electro-insulated Modules | POSEICO
- Electro-insulated Modules | ABB
- Electro-insulated Modules | TECHSEM
- Go to the subcategory
- Bridge Rectifiers
-
Transistors
- Transistors | GeneSiC
- SiC MOSFET Modules | Mitsubishi
- SiC MOSFET Modules | STARPOWER
- Module SiC MOSFET ABB’s
- IGBT Modules | MITSUBISHI
- Transistor Modules | MITSUBISHI
- MOSFET Modules | MITSUBISHI
- Transistor Modules | ABB
- IGBT Modules | POWEREX
- IGBT Modules | INFINEON (EUPEC)
- Silicon Carbide (SiC) semiconductor elements
- Go to the subcategory
- Gate Drivers
- Power Blocks
- Go to the subcategory
- Electrical Transducers
-
Passive components (capacitors, resistors, fuses, filters)
- Resistors
-
Fuses
- Miniature Fuses for electronic circuits - ABC & AGC Series
- Tubular Fast-acting Fuses
- Time-delay Fuse Links with GL/GG & AM characteristics
- Ultrafast Fuse Links
- Fast-acting Fuses (British & American standard)
- Fast-acting Fuses (European standard)
- Traction Fuses
- High-voltage Fuse Links
- Go to the subcategory
- Capacitors
- EMI Filters
- Supercapacitors
- Power surge protection
- TEMPEST emission revealing filters
- Go to the subcategory
-
Relays and Contactors
- Relays and Contactors - Theory
- 3-Phase AC Semiconductor Relays
- DC Semiconductor Relays
- Controllers, Control Systems and Accessories
- Soft Starters and Reversible Relays
- Electromechanical Relays
- Contactors
- Rotary Switches
-
Single-Phase AC Semiconductor Relays
- AC ONE PHASE RELAYS 1 series| D2425 | D2450
- One phase semiconductor AC relays CWA and CWD series
- One phase semiconductor AC relays CMRA and CMRD series
- One phase semiconductor AC relays - PS series
- Double and quadruple semiconductor AC relays - D24 D, TD24 Q, H12D48 D series
- One phase semiconductor relays - gn series
- Ckr series single phase solid state relays
- One phase AC semiconductor relays for DIN bus - ERDA I ERAA series
- 150A AC single phase relays
- Rail Mountable Solid State Relays With Integrated Heat Sink - ENDA, ERDA1 / ERAA1 series
- Go to the subcategory
- Single-Phase AC Semiconductor Relays for PCBs
- Interface Relays
- Go to the subcategory
- Cores and Other Inductive Components
- Heatsinks, Varistors, Thermal Protection
- Fans
- Air Conditioning, Accessories for Electrical Cabinets, Coolers
-
Batteries, Chargers, Buffer Power Supplies and Inverters
- Batteries, Chargers - Theoretical Description
- Modular Li-ion Battery Building Blocks, Custom Batteries, BMS
- Batteries
- Battery Chargers and Accessories
- Uninterruptible Power Supply and Buffer Power Supplies
- Inverters and Photovoltaic Equipments
- Energy storage
- Fuel cells
- Lithium-ion batteries
- Go to the subcategory
-
Automatics
- Futaba Drone Parts
- Limit Switches, Microswitches
- Sensors, Transducers
-
Infrared Thermometers (Pyrometers)
- IR-TE Series - Water-proof Palm-sized Radiation Thermometer
- IR-TA Series - Handheld Type Radiation Thermometer
- IR-H Series - Handheld Type Radiation Thermometer
- IR-BA Series - High-speed Compact Radiation Thermometer
- IR-FA Series - Fiber Optic Radiation Thermometer
- IR-BZ Series - Compact Infrared Thermometers
- Go to the subcategory
- Counters, Time Relays, Panel Meters
- Industrial Protection Devices
- Light and Sound Signalling
- Thermographic Camera
- LED Displays
- Control Equipments
- Go to the subcategory
-
Cables, Litz wires, Conduits, Flexible connections
- Wires
- Cable feedthroughs and couplers
- Litz wires
- Cables for extreme applications
- Sleevings
-
Braids
- Flat Braids
- Round Braids
- Very Flexible Flat Braids
- Very Flexible Round Braids
- Cylindrical Cooper Braids
- Cylindrical Cooper Braids and Sleevings
- Flexible Earthing Connections
- Galvanized and Stainless Steel Cylindrical Braids
- PCV Insulated Copper Braids (temp. up to 85C)
- Flat Aluminium Braids
- Junction Set - Braids and Tubes
- Go to the subcategory
- Traction Equipment
- Cable Terminals
- Flexible Insulated Busbars
- Flexible Multilayer Busbars
- Cable Duct Systems
- Go to the subcategory
- View all categories
-
Semiconductors
-
-
- Suppliers
-
Applications
- CNC Machine Tools
- DC and AC Drives (Inverters)
- Energetics
- Energy bank
- Equipment and Components for Hazardous Areas [Ex]
- Equipment for Distribution, Control and Telecommunications Cabinets
- HVAC Automation
- Induction Heating
- Industrial Automation
- Industrial Protective Devices
- Machines for Drying and Wood Processing
- Machines for Thermoforming Plastics
- Mining, Metallurgy and Foundry
- Motors and Transformers
- Power Supplies (UPS) and Rectifier Systems
- Printing
- Temperature Measurement and Regulation
- Test and Laboratory Measurements
- Tram and Railway Traction
- Welding Machines
-
Assembly
-
-
Inductors
-
-
Induction devices
-
-
https://www.dacpol.eu/pl/naprawy-i-modernizacje
-
-
Service
-
- Contact
- Zobacz wszystkie kategorie
EX s – higher level of pressurized protection
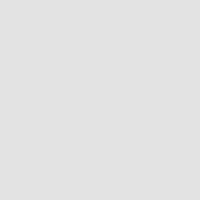
Requirements for Equipment in Explosive Atmosphere Zones
According to the primary document regarding explosion protection applicable in the European Union, namely the ATEX directive (both 114 and 153), equipment intended for use in so-called explosive atmosphere zones must meet specific requirements. The hazard is related to the presence of an explosive atmosphere, which is a mixture of air—under atmospheric conditions—flammable substances in the form of gases, vapors, mist, or dust, where combustion spreads to the entire unburned mixture once ignition occurs. Additionally, in the section "Explosion Prevention and Explosion Protection" at the beginning of Article 3 of the ATEX User Directive, the employer is required to take technical and/or organizational measures corresponding to the nature of the specified hazard, as reflected in the Integrated Safety concept, which is briefly illustrated in the diagram below.
Electrical Equipment Protection
The protection of electrical equipment is included in the second layer. There is no single best method for minimizing—or ideally eliminating—the risk of an effective ignition source. Generally, equipment intended for use in explosive atmosphere spaces is designed, manufactured, tested, and marked according to the requirements of:
- ATEX Directive 2014/34/EU of February 26, 2014,
- Regulation of the Minister of Economy of December 22, 2005, on essential requirements for equipment and protective systems intended for use in explosive atmosphere spaces,
- The multi-part EN 60079 standard concerning the construction of explosion-proof equipment.
Pressure Protection EX s
This article focuses on one specific method of protection, namely the ventilated type of protection called pressure protection EX s, which is currently offered by DACPOL. According to the standard PN-EN 60079-2:2015-02 – Explosive Atmospheres – Part 2: Protection of Equipment by Gas Pressure 'p' – it involves placing components that could spark or overheat during operation inside a closed enclosure filled with air or another inert (non-flammable) gas maintained at a constant pressure.
Differences Between EX p and EX s Systems
The difference between the EX p and EX s systems is primarily the need for ventilation. While ventilation is a necessity in the EX p system, it is optionally activated in the EX s system after analyzing the presence of flammable gas inside the enclosure. In both cases, a gas sensor adapted to the currently present flammable/explosive substance and its calibration once a year are required. Technically, the EX s system features a set of valves used by a permanently connected compressor and, if the current exceeds 5A, a special contactor. The principle of operation is based on the phenomenon of overpressure, that is, utilizing the pressure difference between the outside of the enclosure (where there is an explosive atmosphere) and the inside (safe zone). The inability of the explosive atmosphere to penetrate ensures that the devices and components inside are safe, allowing the placement of non-ATEX certified equipment. This is a very convenient feature of this protection method, making EX s a versatile solution with many applications. Gas pressure protection is most commonly used for protecting high-power electric motors, especially high-voltage ones, as well as distribution and control panels.
Modularity and Versatility of the EX s System
What distinguishes the pressure systems supplied by DACPOL from others available on the market is the possibility of shifting a significant part of the assembly to the customer. In the past, with older solutions, after determining the BOM (Bill of Materials), everything was assembled and delivered by the manufacturer. Now, thanks to special certification (EX s), there is the possibility to purchase just the control unit, with the enclosure and assembly being the responsibility of the user. Of course, along with the Quinguard module responsible for system control, a manual is provided regarding the requirements for the enclosure and other elements, as well as the method for testing the tightness, which is absolutely required if the system is to operate in an explosive atmosphere zone.
Requirements for EX s Systems
From the perspective of process safety, the EX s system adheres to the principle of Integrated Safety, which states that the entire problem of preventing explosion risks can be broken down into three layers:
- Preventing the formation of explosive atmospheres,
- Preventing the occurrence of an effective ignition source,
- Limiting the harmful effects of an explosion.
Methods of protecting electrical equipment that could generate a spark during normal operation (i.e., at rated voltage and current) qualify as preventing the appearance of an ignition source. In the case of EX s protection, the situation is somewhat less straightforward because, although an ignition source may appear, due to the overpressure, ignition or explosion propagation to the surroundings does not occur. Therefore, from the perspective of protection layers, it is a method based on explosion isolation. The inert gas pumped into the sealed enclosure also acts as a cooling medium, which further reduces the risk of excessive heating of the components inside. Safety is ensured by a system that monitors pressure differences, supplements the inert gas deficiency (or blocks its supply), and disconnects the circuit in case of leakage.
Benefits of Using the EX s System
The greatest advantage of the EX s pressure system is its modularity and versatility. The former is reflected in the ability to deliver it in various ways. For the customer, these options include:
- Purchasing the entire solution as a "black box" – the customer provides the enclosure components, and assembly and wiring are handled by the manufacturer, followed by the return shipping of the ready-to-use system.
- Purchasing the enclosure and control (Quinguard, valve modules, power supply) with assembly handled by the customer.
- Purchasing the control only, with the enclosure and assembly handled by the customer.
Regarding the detector, there is flexibility: it can be provided by either the customer or the manufacturer.
Versatility, on the other hand, means broad application possibilities in various conditions. The EX s system can operate in gas zones 1 and 2 as well as dust zones 21 and 22, and it also allows for the protection of devices or component sets with unusual geometries. The nature of the protection means that with EX s, almost any device can be adapted for use in an explosive atmosphere because it does not need to have ATEX certification, yet it can still operate in an EX zone. For large installations like electrical distribution panels, this is a significant advantage that avoids the need to move equipment out of the hazardous area or use large, costly fireproof enclosures.
This solution is simple and convenient to operate but requires close cooperation between the supplier and the customer from the very early stages of the project, so early contact is recommended.
EX s System Guide
To ensure optimal use of the EX s system, it is crucial for the user to adhere to a few key principles. Firstly, when purchasing the enclosure and control with assembly on the customer’s side, it is recommended to thoroughly review the technical documentation provided by the manufacturer. This documentation includes detailed information on enclosure requirements, installation, system calibration, and leakage testing procedures. In case of any doubts, it is advisable to consult with a DACPOL representative who can assist in performing the proper tests and ensure that the system is correctly configured for operation in an explosive atmosphere zone.
Installation and Calibration Process
During the installation of the EX s system, it is crucial to ensure that all components are correctly installed and configured. For the EX s pressure system, it is essential that the enclosure is airtight and maintains constant internal pressure. Any leaks could reduce protection efficiency and increase the risk of an explosion. Calibration of gas sensors and pressure control should be performed according to the manufacturer's instructions, and the results of these tests should be documented and archived.
Examples of EX s System Applications
The EX s system finds broad application in various industrial sectors. Here are some examples where this technology can be particularly useful:
- High-performance electric motors – especially those operating under high voltage conditions, where the gas pressure protection ensures safe operation.
- Distribution and control panels – the EX s system effectively protects sensitive components from explosive atmospheres, ensuring their long-term and safe operation.
- Industrial installations – in large installations, such as electrical distribution panels, the EX s system provides protection without the need for costly fireproof enclosures.
Benefits of Using the EX s System
Using the EX s system offers several benefits, including:
- Modularity – the ability to purchase various components and customize the system to meet the user’s specific needs.
- Versatility – applicability in various conditions, including gas and dust zones, making it a versatile solution.
- Cost savings – reducing the costs associated with large and expensive fireproof enclosures in large industrial installations.
- Flexibility – the ability to adapt almost any device for use in an explosive atmosphere, even without ATEX certification.
Summary
The EX s pressure system is a modern solution offering advanced protection in explosive atmosphere zones. Its modularity, versatility, and adaptability make it an attractive option for various industrial sectors. By allowing customization to specific needs and requirements, the EX s system represents an effective protection method that enhances safety in challenging conditions. For proper functioning, strict adherence to manufacturer recommendations and regular testing and calibration of the system are essential.
Related product
Related posts
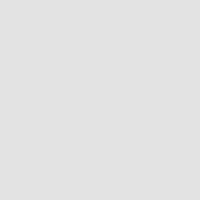
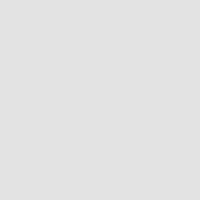
Leave a comment