-
BackX
-
Components
-
-
Category
-
Semiconductors
- Diodes
- Thyristors
-
Electro-insulated Modules
- Electro-insulated Modules | VISHAY (IR)
- Electro-insulated Modules | INFINEON (EUPEC)
- Electro-insulated Modules | Semikron
- Electro-insulated Modules | POWEREX
- Electro-insulated Modules | IXYS
- Electro-insulated Modules | POSEICO
- Electro-insulated Modules | ABB
- Electro-insulated Modules | TECHSEM
- Go to the subcategory
- Bridge Rectifiers
-
Transistors
- Transistors | GeneSiC
- SiC MOSFET Modules | Mitsubishi
- SiC MOSFET Modules | STARPOWER
- Module SiC MOSFET ABB’s
- IGBT Modules | MITSUBISHI
- Transistor Modules | MITSUBISHI
- MOSFET Modules | MITSUBISHI
- Transistor Modules | ABB
- IGBT Modules | POWEREX
- IGBT Modules | INFINEON (EUPEC)
- Silicon Carbide (SiC) semiconductor elements
- Go to the subcategory
- Gate Drivers
- Power Blocks
- Go to the subcategory
- Electrical Transducers
-
Passive components (capacitors, resistors, fuses, filters)
- Resistors
-
Fuses
- Miniature Fuses for electronic circuits - ABC & AGC Series
- Tubular Fast-acting Fuses
- Time-delay Fuse Links with GL/GG & AM characteristics
- Ultrafast Fuse Links
- Fast-acting Fuses (British & American standard)
- Fast-acting Fuses (European standard)
- Traction Fuses
- High-voltage Fuse Links
- Go to the subcategory
- Capacitors
- EMI Filters
- Supercapacitors
- Power surge protection
- Go to the subcategory
-
Relays and Contactors
- Relays and Contactors - Theory
- 3-Phase AC Semiconductor Relays
- DC Semiconductor Relays
- Controllers, Control Systems and Accessories
- Soft Starters and Reversible Relays
- Electromechanical Relays
- Contactors
- Rotary Switches
-
Single-Phase AC Semiconductor Relays
- AC ONE PHASE RELAYS 1 series| D2425 | D2450
- One phase semiconductor AC relays CWA and CWD series
- One phase semiconductor AC relays CMRA and CMRD series
- One phase semiconductor AC relays - PS series
- Double and quadruple semiconductor AC relays - D24 D, TD24 Q, H12D48 D series
- One phase semiconductor relays - gn series
- Ckr series single phase solid state relays
- One phase AC semiconductor relays for DIN bus - ERDA I ERAA series
- 150A AC single phase relays
- Rail Mountable Solid State Relays With Integrated Heat Sink - ENDA, ERDA1 / ERAA1 series
- Go to the subcategory
- Single-Phase AC Semiconductor Relays for PCBs
- Interface Relays
- Go to the subcategory
- Cores and Other Inductive Components
- Heatsinks, Varistors, Thermal Protection
- Fans
- Air Conditioning, Accessories for Electrical Cabinets, Coolers
-
Batteries, Chargers, Buffer Power Supplies and Inverters
- Batteries, Chargers - Theoretical Description
- Modular Li-ion Battery Building Blocks, Custom Batteries, BMS
- Batteries
- Battery Chargers and Accessories
- Uninterruptible Power Supply and Buffer Power Supplies
- Inverters and Photovoltaic Equipments
- Energy storage
- Fuel cells
- Lithium-ion batteries
- Go to the subcategory
-
Automatics
- Futaba Drone Parts
- Limit Switches, Microswitches
- Sensors, Transducers
-
Infrared Thermometers (Pyrometers)
- IR-TE Series - Water-proof Palm-sized Radiation Thermometer
- IR-TA Series - Handheld Type Radiation Thermometer
- IR-H Series - Handheld Type Radiation Thermometer
- IR-BA Series - High-speed Compact Radiation Thermometer
- IR-FA Series - Fiber Optic Radiation Thermometer
- IR-BZ Series - Compact Infrared Thermometers
- Go to the subcategory
- Counters, Time Relays, Panel Meters
- Industrial Protection Devices
- Light and Sound Signalling
- Thermographic Camera
- LED Displays
- Control Equipments
-
Recorders
- Hybrid Recorders - AL3000 Series | CHINO
- Graphic Recorder - KR2000 Series | CHINO
- Ubiquitous Recorders - KR5000 Series | CHINO
- Palm-sized Temperature/Humidity Meters - HN-CH Series | CHINO
- Consumables for Recorders
- 71VR1 - Compact Paperless Recorder | M-SYSTEM
- Graphic Recorder - KR3000 Series | CHINO
- PC Recorders - R1M Series | M-SYSTEM
- PC Recorders - R2M Series | M-SYSTEM
- PC Recorders - RZMS Series | M-SYSTEM
- PC Recorders - RZUS Series | M-SYSTEM
- Go to the subcategory
- Go to the subcategory
-
Cables, Litz wires, Conduits, Flexible connections
- Wires
- Litz wires
- Cables for extreme applications
- Sleevings
-
Braids
- Flat Braids
- Round Braids
- Very Flexible Flat Braids
- Very Flexible Round Braids
- Cylindrical Cooper Braids
- Cylindrical Cooper Braids and Sleevings
- Flexible Earthing Connections
- Galvanized and Stainless Steel Cylindrical Braids
- PCV Insulated Copper Braids (temp. up to 85C)
- Flat Aluminium Braids
- Junction Set - Braids and Tubes
- Go to the subcategory
- Traction Equipment
- Cable Terminals
- Flexible Insulated Busbars
- Flexible Multilayer Busbars
- Cable Duct Systems
- Hoses
- Go to the subcategory
- View all categories
-
Semiconductors
-
-
- Suppliers
-
Applications
- CNC Machine Tools
- DC and AC Drives (Inverters)
- Energetics
- Energy bank
- Equipment and Components for Hazardous Areas [Ex]
- Equipment for Distribution, Control and Telecommunications Cabinets
- HVAC Automation
- Induction Heating
- Industrial Automation
- Industrial Protective Devices
- Machines for Drying and Wood Processing
- Machines for Thermoforming Plastics
- Mining, Metallurgy and Foundry
- Motors and Transformers
- Power Supplies (UPS) and Rectifier Systems
- Printing
- Temperature Measurement and Regulation
- Test and Laboratory Measurements
- Tram and Railway Traction
- Welding Machines
-
Assembly
-
-
Inductors
-
-
Induction devices
-
-
https://www.dacpol.eu/pl/naprawy-i-modernizacje
-
-
Service
-
- Contact
- Zobacz wszystkie kategorie
Humidity sensors - principle of operation, installation
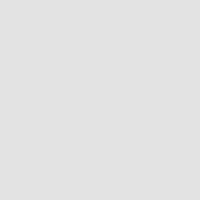
Humidity is the presence of water in the air. The amount of water vapour in the air can affect human comfort as well as many industrial production processes. The presence of water vapour also affects various physical, chemical and biological processes.
Humidity sensors work by detecting changes that alter electrical currents or temperature in the air. There are three basic types of humidity sensors: capacitive, resistive, and thermal (thermally conductive). All three types monitor small changes in the atmosphere to calculate the humidity of the air.
A capacitive humidity sensor measures relative humidity by placing a thin strip of metal oxide between two electrodes. The electrical capacitance of the metal oxide changes with the relative humidity of the atmosphere. The main application areas are meteorological stations, electrical engineering industries, HVAC automation.
Resistive humidity sensors use ions in salts to measure the electrical impedance of atoms. As the humidity changes, the resistance of the electrodes on either side of the salt medium changes.
Thermal sensors conduct an electrical current depending on the humidity of the surrounding air. They are most commonly made of two sensors in one housing - one sensor is encased in dry nitrogen while the other measures the humidity of the air. The difference between the two indicates the humidity.
Application of humidity sensors
Capacitive relative humidity sensors are used in many applications to measure humidity in printers, HVAC systems, fax machines, automobiles, weather stations, refrigerators, food processing, etc.
Because of their small size and low cost, resistive sensors are used in domestic, residential and industrial applications.
Thermally conductive sensors are typically used in dryers, food dehydration, pharmaceutical facilities, etc.
Below are examples and application of humidity sensors:
Domestic: Controlling and sensing humidity in offices and homes is important because higher humidity can affect mood e.g. change in blood flow, feeling uncomfortable. Other application areas include indoor plant farms, cooking, etc.
Industrial: Industries such as chemical, refining, metallurgy where furnaces are used need humidity sensors because high humidity reduces the amount of oxygen present in the air, which can significantly affect the productivity of these industries. Other industries such as paper, textile, food, etc. also require humidity control.
Agriculture: Drip irrigation is a crop growing technique that requires precise humidity. Soil moisture also plays an important role in plant growth. When growing plants indoors or in greenhouses, moisture level testing is essential for their proper growth.
Electronics and Semiconductors: A number of electronic devices are parameterized with respect to the range of humidity in which they will operate properly. Generally, the value is between 10 and 50% humidity. Semiconductor manufacturing facilities must also maintain very precise humidity and temperature values, as even a minute difference can have a huge impact on production.
Medical: Medical equipment such as sterilizers, incubators, ventilators, etc. require humidity control. Humidity sensors are also used in pharmaceutical facilities.
Issues that humidity can cause in industry
In many factories, steam and humidity are daily byproducts of various industrial processes; if not properly maintained, excessive humidity levels can cause a host of problems, resulting in delays, safety hazards and additional expenses.
Even reliable air conditioning may not be enough to achieve the required relative humidity, as the percentage of relative humidity increases as the room temperature decreases.
Different manufacturing facilities have different humidity problems, depending on the specific equipment and products used. Particularly in machine shops, excess moisture can cause condensation, fog or mold buildup that can damage products, equipment and even the facility structure itself.
A safety hazard
Condensation can form on store floors creating a dangerous, slippery environment. Electrical and electronic equipment can also quickly become saturated, posing serious safety and quality risks. Electrical products exposed to high levels of moisture often corrode and reduce insulation resistance, which can eventually cause short circuits.
The problem with labelling
The surface to which the label is applied must not be wet. Condensation may occur on it due to the temperature difference between the packaging and the air in the room. The air must have a relative humidity of about 40-45% for the surface of the packaging to remain dry and for the label to stick. We put labels on fruit, bottles, anything that needs some labelling.
Disrupting drying cycles
Products that require specific drying cycles are also susceptible to moisture problems; if humidity levels are too high, drying times can be severely delayed, resulting in production shutdowns, increased energy consumption, and lost productivity.
Dry food packaging plants are an example. When exposed to excessive humidity, the quality of food products is compromised, which can threaten the health and well-being of consumers. In addition, many insects and insects seek humid conditions, thriving in areas with humidity levels between 70-80%.
Humidity sensors do their job
In order for your manufacturing facility to run at peak efficiency, it is essential to maintain proper humidity levels. Taking care of air quality and humidity levels should be one of the key aspects that every industrial business strives for. Using the highest quality humidity sensors will allow you to precisely control humidity levels in your premises, which will result in increased productivity, as well as ensuring the safety of machinery and equipment, and the comfort of employees or users of a given room.
Related products
Related posts
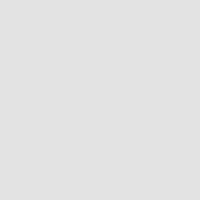
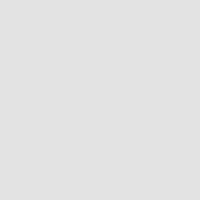
Leave a comment