-
BackX
-
Components
-
-
Category
-
Semiconductors
- Diodes
- Thyristors
-
Electro-insulated Modules
- Electro-insulated Modules | VISHAY (IR)
- Electro-insulated Modules | INFINEON (EUPEC)
- Electro-insulated Modules | Semikron
- Electro-insulated Modules | POWEREX
- Electro-insulated Modules | IXYS
- Electro-insulated Modules | POSEICO
- Electro-insulated Modules | ABB
- Electro-insulated Modules | TECHSEM
- Go to the subcategory
- Bridge Rectifiers
-
Transistors
- Transistors | GeneSiC
- SiC MOSFET Modules | Mitsubishi
- SiC MOSFET Modules | STARPOWER
- Module SiC MOSFET ABB’s
- IGBT Modules | MITSUBISHI
- Transistor Modules | MITSUBISHI
- MOSFET Modules | MITSUBISHI
- Transistor Modules | ABB
- IGBT Modules | POWEREX
- IGBT Modules | INFINEON (EUPEC)
- Silicon Carbide (SiC) semiconductor elements
- Go to the subcategory
- Gate Drivers
- Power Blocks
- Go to the subcategory
- Electrical Transducers
-
Passive components (capacitors, resistors, fuses, filters)
- Resistors
-
Fuses
- Miniature Fuses for electronic circuits - ABC & AGC Series
- Tubular Fast-acting Fuses
- Time-delay Fuse Links with GL/GG & AM characteristics
- Ultrafast Fuse Links
- Fast-acting Fuses (British & American standard)
- Fast-acting Fuses (European standard)
- Traction Fuses
- High-voltage Fuse Links
- Go to the subcategory
- Capacitors
- EMI Filters
- Supercapacitors
- Power surge protection
- Go to the subcategory
-
Relays and Contactors
- Relays and Contactors - Theory
- 3-Phase AC Semiconductor Relays
- DC Semiconductor Relays
- Controllers, Control Systems and Accessories
- Soft Starters and Reversible Relays
- Electromechanical Relays
- Contactors
- Rotary Switches
-
Single-Phase AC Semiconductor Relays
- AC ONE PHASE RELAYS 1 series| D2425 | D2450
- One phase semiconductor AC relays CWA and CWD series
- One phase semiconductor AC relays CMRA and CMRD series
- One phase semiconductor AC relays - PS series
- Double and quadruple semiconductor AC relays - D24 D, TD24 Q, H12D48 D series
- One phase semiconductor relays - gn series
- Ckr series single phase solid state relays
- One phase AC semiconductor relays for DIN bus - ERDA I ERAA series
- 150A AC single phase relays
- Rail Mountable Solid State Relays With Integrated Heat Sink - ENDA, ERDA1 / ERAA1 series
- Go to the subcategory
- Single-Phase AC Semiconductor Relays for PCBs
- Interface Relays
- Go to the subcategory
- Cores and Other Inductive Components
- Heatsinks, Varistors, Thermal Protection
- Fans
- Air Conditioning, Accessories for Electrical Cabinets, Coolers
-
Batteries, Chargers, Buffer Power Supplies and Inverters
- Batteries, Chargers - Theoretical Description
- Modular Li-ion Battery Building Blocks, Custom Batteries, BMS
- Batteries
- Battery Chargers and Accessories
- Uninterruptible Power Supply and Buffer Power Supplies
- Inverters and Photovoltaic Equipments
- Energy storage
- Fuel cells
- Lithium-ion batteries
- Go to the subcategory
-
Automatics
- Futaba Drone Parts
- Limit Switches, Microswitches
- Sensors, Transducers
-
Infrared Thermometers (Pyrometers)
- IR-TE Series - Water-proof Palm-sized Radiation Thermometer
- IR-TA Series - Handheld Type Radiation Thermometer
- IR-H Series - Handheld Type Radiation Thermometer
- IR-BA Series - High-speed Compact Radiation Thermometer
- IR-FA Series - Fiber Optic Radiation Thermometer
- IR-BZ Series - Compact Infrared Thermometers
- Go to the subcategory
- Counters, Time Relays, Panel Meters
- Industrial Protection Devices
- Light and Sound Signalling
- Thermographic Camera
- LED Displays
- Control Equipments
-
Recorders
- Hybrid Recorders - AL3000 Series | CHINO
- Graphic Recorder - KR2000 Series | CHINO
- Ubiquitous Recorders - KR5000 Series | CHINO
- Palm-sized Temperature/Humidity Meters - HN-CH Series | CHINO
- Consumables for Recorders
- 71VR1 - Compact Paperless Recorder | M-SYSTEM
- Graphic Recorder - KR3000 Series | CHINO
- PC Recorders - R1M Series | M-SYSTEM
- PC Recorders - R2M Series | M-SYSTEM
- PC Recorders - RZMS Series | M-SYSTEM
- PC Recorders - RZUS Series | M-SYSTEM
- Go to the subcategory
- Go to the subcategory
-
Cables, Litz wires, Conduits, Flexible connections
- Wires
- Litz wires
- Cables for extreme applications
- Sleevings
-
Braids
- Flat Braids
- Round Braids
- Very Flexible Flat Braids
- Very Flexible Round Braids
- Cylindrical Cooper Braids
- Cylindrical Cooper Braids and Sleevings
- Flexible Earthing Connections
- Galvanized and Stainless Steel Cylindrical Braids
- PCV Insulated Copper Braids (temp. up to 85C)
- Flat Aluminium Braids
- Junction Set - Braids and Tubes
- Go to the subcategory
- Traction Equipment
- Cable Terminals
- Flexible Insulated Busbars
- Flexible Multilayer Busbars
- Cable Duct Systems
- Hoses
- Go to the subcategory
- View all categories
-
Semiconductors
-
-
- Suppliers
-
Applications
- CNC Machine Tools
- DC and AC Drives (Inverters)
- Energetics
- Energy bank
- Equipment and Components for Hazardous Areas [Ex]
- Equipment for Distribution, Control and Telecommunications Cabinets
- HVAC Automation
- Induction Heating
- Industrial Automation
- Industrial Protective Devices
- Machines for Drying and Wood Processing
- Machines for Thermoforming Plastics
- Mining, Metallurgy and Foundry
- Motors and Transformers
- Power Supplies (UPS) and Rectifier Systems
- Printing
- Temperature Measurement and Regulation
- Test and Laboratory Measurements
- Tram and Railway Traction
- Welding Machines
-
Assembly
-
-
Inductors
-
-
Induction devices
-
-
https://www.dacpol.eu/pl/naprawy-i-modernizacje
-
-
Service
-
- Contact
- Zobacz wszystkie kategorie
Industrial pressure sensors - principle of operation, types and application
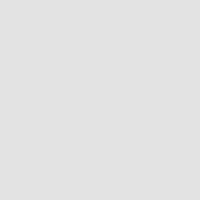
Pressure is one of the basic measurements performed in the vast majority of industrial and manufacturing facilities. The primary functions of such sensors are to measure pressure and transmit the collected information to external devices.
Due to the ability of most sensors to convert an input signal into an analog or digital electrical signal, they are also often called transducers.
Principle of operation of industrial pressure sensors
Pressure sensors work like a strain gauge by using the deformation of a membrane made of silicone, metal or ceramic. Pressure is a non-electrical signal, so it is necessary to convert these values into signals that electrical devices can easily use. The precise construction of membrane pressure sensors allows them to work efficiently with electronic circuits, so that when a flexible element is deformed, the measured value is immediately converted into an electrical signal proportional to the amount of pressure applied.
The most popular solutions are sensors with silicon and stainless steel membranes. The first solution increases the pressure resistance of the membrane, so the lifetime of such sensors increases significantly. Additionally, silicon can be combined with other materials, e.g. ceramics, to obtain new properties that increase the transmitters' performance. The second solution can be found in sensors that operate in harsh environments and heavy industry.
Types of industrial pressure sensors
There are many types of pressure transmitters on the market. The choice of a particular solution depends on the end application, but above all on the measuring system. A very popular solution are differential sensors, which measure the pressure from two sources on a membrane. The deflection resulting from this difference gives information about the relationship between the pressure of the measured gas and the external pressure.
Relative pressure sensors, which measure pressure relative to vacuum or atmospheric pressure, are another option. Absolute pressure sensors that compare the measurement with vacuum exclude the influence of atmospheric pressure on the measurement. Such solutions are often found in applications for checking the tightness of sealed tanks.
Technical information about industrial pressure sensors
Before purchasing a sensor for the solution, it is worth to get acquainted with several parameters that can be helpful in selecting the right element:
Measuring range
Several standards are used in industry to measure analog signals. The standards used in pressure transmitters are 4 - 20 mA, 0 - 10 V and 0.5 - 4.5 V.
Because of the need to choose the right measurement accuracy, most facilities use sensors that have the ability to switch between different ranges.
Minimum pressure
Each transmitter has a lower measurement limit for which it will show the correct pressure values. With a measurement range of 4 - 20 mA, this will be 0 bar for 4 mA.
Maximum pressure
This is the upper measurement limit of the sensor. When we have the minimum and maximum pressure, we are able to select a suitable sensor with this measurement range.
Power supply
Determining the type and value of the power supply is critical for any sensor. The industry standard is 24 VDC.
Use of industrial pressure sensors
Pressure sensors can be found in many advanced applications and industries. Pressure transmitters are commonly used in:
- Manufacturing industry;
- Heavy industry – military and aeronautics;
- Hydraulic industry;
- Automotive industry;
- Medical and chemical industry;
- HVAC systems – heating, ventilation, air conditioning.
Despite their small size, pressure sensors are key elements of every automation system. They are able to monitor the course of processes and work of devices and installations, allowing for quick elimination of any failures and damages in production processes. With many years of experience in distribution of products and devices for automation, Dacpol offers the best solutions to meet customer requirements. Our offer includes a wide range of pressure sensors for industrial applications. Our specialists will help you choose the right solution and answer all your questions.
Related products
Related posts
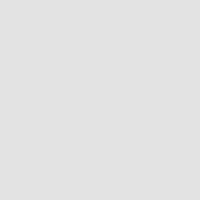
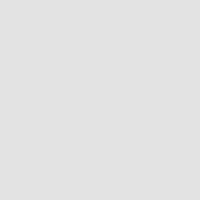
Leave a comment