-
BackX
-
Components
-
-
Category
-
Semiconductors
- Diodes
- Thyristors
-
Electro-insulated Modules
- Electro-insulated Modules | VISHAY (IR)
- Electro-insulated Modules | INFINEON (EUPEC)
- Electro-insulated Modules | Semikron
- Electro-insulated Modules | POWEREX
- Electro-insulated Modules | IXYS
- Electro-insulated Modules | POSEICO
- Electro-insulated Modules | ABB
- Electro-insulated Modules | TECHSEM
- Go to the subcategory
- Bridge Rectifiers
-
Transistors
- Transistors | GeneSiC
- SiC MOSFET Modules | Mitsubishi
- SiC MOSFET Modules | STARPOWER
- Module SiC MOSFET ABB’s
- IGBT Modules | MITSUBISHI
- Transistor Modules | MITSUBISHI
- MOSFET Modules | MITSUBISHI
- Transistor Modules | ABB
- IGBT Modules | POWEREX
- IGBT Modules | INFINEON (EUPEC)
- Silicon Carbide (SiC) semiconductor elements
- Go to the subcategory
- Gate Drivers
- Power Blocks
- Go to the subcategory
- Electrical Transducers
-
Passive components (capacitors, resistors, fuses, filters)
- Resistors
-
Fuses
- Miniature Fuses for electronic circuits - ABC & AGC Series
- Tubular Fast-acting Fuses
- Time-delay Fuse Links with GL/GG & AM characteristics
- Ultrafast Fuse Links
- Fast-acting Fuses (British & American standard)
- Fast-acting Fuses (European standard)
- Traction Fuses
- High-voltage Fuse Links
- Go to the subcategory
- Capacitors
- EMI Filters
- Supercapacitors
- Power surge protection
- TEMPEST emission revealing filters
- Go to the subcategory
-
Relays and Contactors
- Relays and Contactors - Theory
- 3-Phase AC Semiconductor Relays
- DC Semiconductor Relays
- Controllers, Control Systems and Accessories
- Soft Starters and Reversible Relays
- Electromechanical Relays
- Contactors
- Rotary Switches
-
Single-Phase AC Semiconductor Relays
- AC ONE PHASE RELAYS 1 series| D2425 | D2450
- One phase semiconductor AC relays CWA and CWD series
- One phase semiconductor AC relays CMRA and CMRD series
- One phase semiconductor AC relays - PS series
- Double and quadruple semiconductor AC relays - D24 D, TD24 Q, H12D48 D series
- One phase semiconductor relays - gn series
- Ckr series single phase solid state relays
- One phase AC semiconductor relays for DIN bus - ERDA I ERAA series
- 150A AC single phase relays
- Rail Mountable Solid State Relays With Integrated Heat Sink - ENDA, ERDA1 / ERAA1 series
- Go to the subcategory
- Single-Phase AC Semiconductor Relays for PCBs
- Interface Relays
- Go to the subcategory
- Cores and Other Inductive Components
- Heatsinks, Varistors, Thermal Protection
- Fans
- Air Conditioning, Accessories for Electrical Cabinets, Coolers
-
Batteries, Chargers, Buffer Power Supplies and Inverters
- Batteries, Chargers - Theoretical Description
- Modular Li-ion Battery Building Blocks, Custom Batteries, BMS
- Batteries
- Battery Chargers and Accessories
- Uninterruptible Power Supply and Buffer Power Supplies
- Inverters and Photovoltaic Equipments
- Energy storage
- Fuel cells
- Lithium-ion batteries
- Go to the subcategory
-
Automatics
- Futaba Drone Parts
- Limit Switches, Microswitches
- Sensors, Transducers
-
Infrared Thermometers (Pyrometers)
- IR-TE Series - Water-proof Palm-sized Radiation Thermometer
- IR-TA Series - Handheld Type Radiation Thermometer
- IR-H Series - Handheld Type Radiation Thermometer
- IR-BA Series - High-speed Compact Radiation Thermometer
- IR-FA Series - Fiber Optic Radiation Thermometer
- IR-BZ Series - Compact Infrared Thermometers
- Go to the subcategory
- Counters, Time Relays, Panel Meters
- Industrial Protection Devices
- Light and Sound Signalling
- Thermographic Camera
- LED Displays
- Control Equipments
- Go to the subcategory
-
Cables, Litz wires, Conduits, Flexible connections
- Wires
- Cable feedthroughs and couplers
- Litz wires
- Cables for extreme applications
- Sleevings
-
Braids
- Flat Braids
- Round Braids
- Very Flexible Flat Braids
- Very Flexible Round Braids
- Cylindrical Cooper Braids
- Cylindrical Cooper Braids and Sleevings
- Flexible Earthing Connections
- Galvanized and Stainless Steel Cylindrical Braids
- PCV Insulated Copper Braids (temp. up to 85C)
- Flat Aluminium Braids
- Junction Set - Braids and Tubes
- Go to the subcategory
- Traction Equipment
- Cable Terminals
- Flexible Insulated Busbars
- Flexible Multilayer Busbars
- Cable Duct Systems
- Go to the subcategory
- View all categories
-
Semiconductors
-
-
- Suppliers
-
Applications
- CNC Machine Tools
- DC and AC Drives (Inverters)
- Energetics
- Energy bank
- Equipment and Components for Hazardous Areas [Ex]
- Equipment for Distribution, Control and Telecommunications Cabinets
- HVAC Automation
- Induction Heating
- Industrial Automation
- Industrial Protective Devices
- Machines for Drying and Wood Processing
- Machines for Thermoforming Plastics
- Mining, Metallurgy and Foundry
- Motors and Transformers
- Power Supplies (UPS) and Rectifier Systems
- Printing
- Temperature Measurement and Regulation
- Test and Laboratory Measurements
- Tram and Railway Traction
- Welding Machines
-
Assembly
-
-
Inductors
-
-
Induction devices
-
-
https://www.dacpol.eu/pl/naprawy-i-modernizacje
-
-
Service
-
- Contact
- Zobacz wszystkie kategorie
Nowe osiągnięcia w technologii klejów akrylowych następnej generacji.
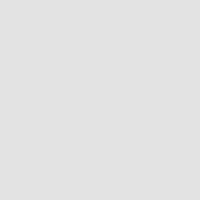
INTRODUCTION
Structural acrylic adhesives are two-component systems (adhesive plus accelerator) that provide bonding strength equal to or exceeding the strength of the substrate. Significant commercial use of acrylic adhesives began in the 1960s. "First-generation systems" were brittle and typically used for bonding plastics. They usually contained poly(methyl methacrylate) dissolved in methyl methacrylate ("syrup") and a "lacquer" accelerator used in a high mixing ratio.
"Second-generation structural adhesives" provided effective bonding performance in various commercial applications for the past 30 or more years. These systems were more durable and offered improved performance at low temperatures and better bonding with metals. They contained butadiene rubber reinforcements, metal adhesion promoters, and mixing ratios of 1:1 and 4:1 with accelerators.
"Next-generation acrylic adhesives" have evolved in recent years to provide increased performance in more demanding applications. Key features of "next-generation adhesives" include advanced core-shell rubber reinforcements, polymerizable monomer blends, and a 10:1 mixing ratio. Enhanced performance features include:
- High tensile shear strength - targeting structural applications
- Improved peel strength - better performance in mixed stress applications
- Excellent damage mode on a wide range of substrates - more resilient performance increasing usability for many applications
- High impact resistance - suitable for use in tough conditions where impacts may occur
- Improved fatigue resistance - performs better under cyclic stresses or vibrations
- Excellent performance at low temperatures - important for use in challenging climatic conditions
- Electrophoretic and paint bake resistance - bonded parts will not shift/separate during baking
- REACH compliant formula (Europe) - elimination of toxic components enables global use
ENHANCED PERFORMANCE
It's worth comparing "structural acrylic adhesives" such as LORD 852/25GB with some of the most commercially successful examples of "second-generation acrylic adhesives." One significant difference in physical properties is a significant increase in elongation (100 percent compared to 35 percent) for "next-generation acrylic adhesive," while maintaining the same high tensile strength (about 18 MPa for both). This increase in elongation without loss of tensile strength is key to many elements of improved performance of "next-generation acrylic adhesives." Another element of improved performance of "next-generation acrylic adhesives," which is most visible to manufacturers, is excellent damage mode and performance on various, difficult-to-bond metal substrates.
Figure 1 and Figure 2 show comparisons of tensile shear strength and T-peel strength for "second-generation acrylic adhesive" and LORD 852/25GB. Tensile shear strength primarily reflects the adhesive's tensile strength, while good peel strength performance requires higher strength and elongation. The bonding results show equivalent tensile shear strength, while the more flexible "next-generation acrylic adhesive" demonstrates a significant improvement in T-peel strength. It is also worth noting a significant improvement in damage mode using "next-generation acrylic adhesive."
Shear Resistance Test (Metal Bonding)
Figure 1
LSS (RT Cure) | 2nd Gen | Next Gen |
AI (psi) | 2849 | 2617 |
Failure Mode | 25COH/75TLC | COH |
EGS (psi) | 2190 | 2136 |
Failure Mode | 80COH/20TLC |
APPLICATION: MOUNTING WIND TURBINE TOWERS In this application, the acrylic adhesive LORD 852/25GB "next generation" was qualified for use in the construction of wind turbine towers. Due to its excellent damage mode on difficult-to-bond substrates, the adhesive proved ideal even for hybrid bonding - aluminum to hot-dip galvanized steel sheet - necessary for the production of wind turbine tower enclosures. Figure 10 illustrates the application of mounting wind turbine towers. Figure 10: The wind tower assembly design required the use of an adhesive that would provide good damage and material fatigue resistance. Application: Wind Tower Assembly Bonding hot-dip galvanized steel and aluminum Large parts with varying line thicknesses of adhesive Key Performance Requirements: Good damage and material fatigue resistance 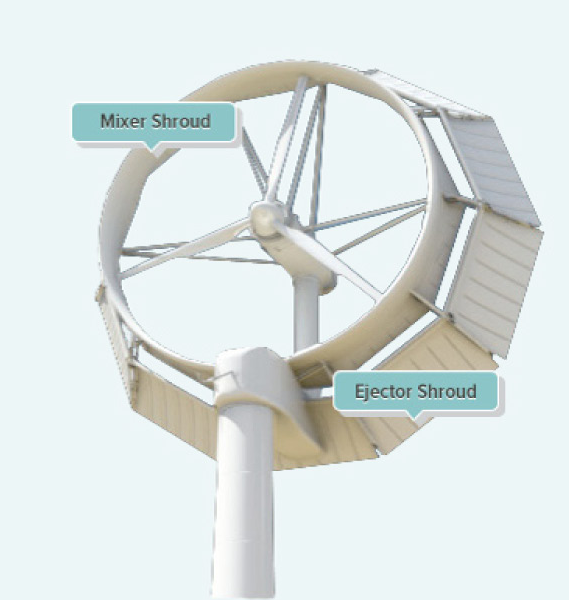 CONCLUSION The evolution of acrylic adhesives to next-generation formulations has significantly expanded their capabilities, making them suitable for a wide range of demanding applications in various industries. The LORD 852/25GB adhesive exemplifies this advancement, offering superior performance in terms of bonding strength, impact resistance, environmental durability, and ease of application. Whether in the automotive, construction, or renewable energy sectors, the versatility and reliability of next-generation acrylic adhesives make them a preferred choice for manufacturers seeking efficient, cost-effective, and durable bonding solutions.
Related posts
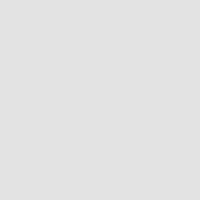
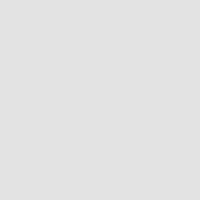
Leave a comment