Pressure sensors in HVAC applications
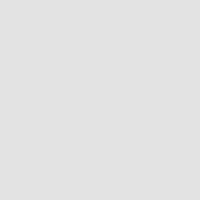
Pressure sensors in HVAC applications
Pressure sensors are an essential element of automation of ventilation systems. These sensors are designed to measure air or gas pressure and provide accurate readings to the control system. Automation of ventilation systems is becoming more and more important in modern buildings because it allows better control of air quality and energy efficiency. Pressure sensors are used to monitor pressure in channels, pipes and other elements of the ventilation system. They can detect pressure changes caused by changes in air flow, temperature or humidity and provide feedback in real time to the control system. This information is used to adjust the speed of fans, shock absorbers and other components to maintain the desired pressure and air flow. In this article, we will examine various types of pressure sensors used in ventilation systems, their applications and the benefits of their use in automation.
Pressure sensors play a key role in ventilation automation, ensuring that the air flow in the building is optimized for maximum efficiency and comfort. These sensors measure the air pressure in the ventilation system, enabling the system to adjust the air flow to maintain a coherent pressure level. This is important because if the pressure in the system is too high or too low, it can cause problems such as poor air quality, increased energy consumption, and even damage to ventilation equipment. Using pressure sensors, ventilation systems can be automated to adapt the air flow if necessary, ensuring that the pressure remains optimal for the residents of the building. This not only improves the overall comfort and health of residents, but also reduces energy costs and extends the life of ventilation equipment. In short, understanding the importance of pressure sensors in ventilation automation is necessary to ensure that the buildings are safe, comfortable and efficient.
Pressure sensors are an essential element of ventilation automation systems. They are used to measure air and gas pressure in channels, pipes and other ventilation systems. There are three main types of pressure sensors used in ventilation automation: differential pressure sensors, absolute pressure sensors and meter pressure sensors. Differential pressure sensors are the most commonly used type of pressure sensor in ventilation automation. They measure the pressure difference between two points in the ventilation system. This type of sensor is used to monitor the pressure drop in filters, damping and other components in the ventilation system. Differential pressure sensors are also used to control the air and gas flow in the system by regulating the speed of fans and blowers. Absolute pressure sensors are used to measure air and gas pressure in the ventilation system in relation to the vacuum. This type of sensor is used to monitor pressure in sealed systems, such as clean rooms and laboratories. Absolute pressure sensors are also used to measure gas pressure in combustion processes. Meter pressure sensors are used to measure air and gas pressure in the ventilation system compared to atmospheric pressure. This sensor type is used to monitor pressure in open systems, such as HVAC systems and industrial ventilation systems. Meter pressure sensors are also used to measure gas pressure in pneumatic systems. To sum up, pressure sensors are an important element of ventilation automation systems. Differential pressure sensors, absolute pressure sensors and meter pressure sensors are three main types of pressure sensors used in ventilation automation. Each type of sensor has its own unique applications and benefits, and choosing the right type of sensor for a specific ventilation system is crucial for optimal efficiency and energy efficiency.
The benefits of using pressure sensors
Pressure sensors are becoming more and more popular in the field of ventilation automation. These sensors are designed to measure air pressure and other gases in the system and offer a number of benefits that make them the perfect choice for ventilation automation. In this article, we will examine four key advantages of using pressure sensors in ventilation automation.
1. Improved energy efficiency One of the main advantages of using pressure sensors in ventilation automation is to improve energy efficiency. By monitoring the pressure of the air and other gases in the system, these sensors can help optimize the performance of ventilation systems, ensuring that they work at peak performance. This can help reduce energy consumption and lower operating costs, thanks to which pressure sensors are an excellent investment for companies and organizations that want to improve their financial results.
2. Increased safety Another key advantage of using pressure sensors in ventilation automation is increased safety. These sensors can help detect and prevent dangerous pressure imbalances in ventilation systems, which can lead to a number of safety threats, including fires, explosions and other accidents. By monitoring pressure levels and notifications of potential problems, pressure sensors can help ensure that ventilation systems work safely and effectively.
3. Improved air quality pressure sensors may also help improve air quality in ventilation systems. By monitoring pressure levels, these sensors can help ensure that the air flows correctly through the system, preventing the accumulation of harmful pollution and impurities. This can help improve air quality in rooms, which is necessary for health and well -being of building residents.
4. Finally, increased system reliability, pressure sensors may help increase the reliability of ventilation systems. By monitoring pressure levels and warning operators to potential problems, these sensors can help prevent system failure and downtime, ensuring that ventilation systems work smoothly and efficiently at all times. This can help reduce the costs of maintenance and improve the general efficiency of the system, which makes pressure sensors an important element of any ventilation automation system.
To sum up, pressure sensors offer a number of benefits for ventilation automation, including better energy efficiency, increased safety, better air quality and increased system reliability. By investing in pressure sensors, companies and organizations can improve the efficiency of ventilation systems, reduce operating costs and ensure the health and safety of building residents.
Pressure sensors are an essential element of ventilation systems because they help monitor and regulate air pressure levels. Proper installation and maintenance of these sensors is crucial for ensuring efficient and effective operation of the ventilation system. Here are five key considerations regarding the installation and maintenance of pressure sensors in ventilation systems:
1. Location: The location of the pressure sensor is of key importance for its accuracy and reliability. It should be installed in a position where it can thoroughly measure the air pressure flowing through the ventilation system. The sensor should be placed in a place that is easily available for maintenance and calibration.
2. Calibration: pressure sensors must be regularly calibrated to ensure their accuracy. Calibration consists in comparing the sensor readings with a known standard and adjusting it if necessary. Regular calibration ensures that the sensor provides accurate readings, which is necessary to maintain adequate air pressure levels in the ventilation system.
3. Cleaning: With time, pressure sensors may become dirty, which can affect their accuracy. It is necessary to regularly clean to remove dirt or impurities that could accumulate on the sensor. Cleansing should be done carefully to avoid damage to the sensor.
4. Replacement: Pressure sensors have a limited service life and will eventually have to be replaced. The sensor's life depends on several factors, including the environment in which it is installed and how often it is used. Regular maintenance can help prolong the sensor life, but ultimately it needs to be replaced.
5. Monitoring: Regular monitoring of pressure sensor readings is necessary to ensure that the ventilation system works properly. Any significant changes in readings may indicate a problem with the system that should be solved. Monitoring can be done manually or via an automatic system that warns maintenance staff if there are any problems. To sum up, proper installation and maintenance of pressure sensors are necessary for the efficient and effective operation of ventilation systems. Regular calibration, cleaning and monitoring are necessary to ensure that the sensors provide accurate readings and that the system works correctly. By following these guidelines, building owners and maintenance staff can ensure that their ventilation systems work properly and provide a safe and healthy environment for residents.
Pressure sensors are an essential element of ventilation automation systems, providing key information about air pressure and flow in the building. However, these sensors have a few challenges and restrictions that can affect their accuracy and reliability. One of the main challenges is the need for regular calibration and maintenance to ensure that the sensors provide accurate readings. In addition, environmental factors, such as temperature and humidity, can be influenced by pressure sensors, which can cause fluctuations in their readings. Another limitation is the cost of high quality pressure sensors, which can be excessive for some owners and building operators. Finally, pressure sensors may not be suitable for all types of ventilation systems, especially those that are based on natural ventilation or other non-mechanical methods. Despite these challenges and restrictions, pressure sensors remain a key tool ensuring optimal air quality and energy efficiency in modern buildings. Understanding these restrictions and working on alleviating them, building owners and operators can maximize the benefits of ventilation automation when minimizing risk.
Innovation forecasts in pressure sensors for the HVAC application
Pressure sensors have become an important element in ventilation automation systems, providing accurate and reliable measurements of air pressure and flow speed. As the technology progresses, the future of pressure sensors in ventilation automation looks promising. Here are seven potential changes that can shape the future of pressure sensors in ventilation automation:
1. Miniaturization: pressure sensors are becoming smaller and more compact, which allows easier integration with ventilation systems.
2. Wireless connectivity: With the increase in the Internet of Things (IoT), pressure sensors probably become more connected, enabling remote monitoring and control.
3. Improved accuracy: As pressure sensors become more advanced, they will probably become even more accurate, providing more precise measurements of air pressure and flow speed.
4. Increased durability: pressure sensors will probably become more durable, with better resistance to environmental factors, such as temperature, humidity and vibrations.
5. Energy performance: Pressure sensors will probably become more energy -saving, reducing the amount of power required to operate them.
6. Artificial intelligence: With the integration of artificial intelligence (AI), pressure sensors can become even more intelligent, providing real -time analysis and predictive maintenance.
7. Integration with other sensors: pressure sensors probably become more integrated with other sensors, such as temperature and humidity sensors, providing a more comprehensive image of the ventilation system performance. In general, the future of pressure sensors in ventilation automation looks bright, with progress in miniaturization, wireless communication, accuracy, durability, energy efficiency, AI and integration with other sensors. These development will probably lead to more efficient and effective ventilation systems, improve air quality and reducing energy consumption.
The use of pressure sensors in HVAC systems
Pressure sensors have become an indispensable element in ventilation automation systems. They are used to monitor and control air pressure in HVAC systems, ensuring that the air flows and efficiently. In this article, we will discuss eight cases of cases that show the successful implementation of pressure sensors in ventilation automation.
The first case study includes a large commercial building, which had problems with the HVAC system. The building management team has installed pressure sensors to monitor air pressure in the cable. The sensors allowed them to identify and improve system problems, which causes better air quality and energy efficiency.
In another case study, the hospital installed pressure sensors in its HVAC system to monitor air pressure in patient rooms. The sensors allowed the hospital staff to maintain a comfortable and safe environment for patients, reducing the risk of infection and improving patients' results.
The third case study includes a production plant, which installed pressure sensors in its ventilation system to monitor air pressure in the production area. The sensors allowed the object to maintain a clean and safe environment for employees, reducing the risk of breathing problems and improving performance.
In the fourth case study, the school district installed pressure sensors in its HVAC system to monitor air pressure in the classroom. The sensors allowed the district to maintain a comfortable and healthy learning environment for students, reducing absence and improving academic results.
The fifth case study includes a data center that has been installed by pressure sensors in its HVAC system to monitor air pressure in servers. The sensors allowed the data center to maintain a stable and safe environment for its servers, reducing the risk of downtime and data loss.
In the sixth case study, the hotel installed pressure sensors in its HVAC system to monitor air pressure in guest rooms. The sensors allowed the hotel to maintain a comfortable and encouraging environment for guests, improve customer satisfaction and loyalty.
The seventh case study includes a sports arena, which installed pressure sensors in its HVAC system to monitor air pressure in the safety area. The sensors allowed the arena to maintain a comfortable and pleasant environment for viewers, improving attendance and revenues.
Finally, in the eighth case study, the government building installed pressure sensors in its HVAC system to monitor air pressure in conference rooms. The sensors allowed the building to maintain a comfortable and productive environment for meetings, improvement of communication and making decisions.
To sum up, pressure sensors have proved to be a valuable tool in ventilation automation systems. These cases of cases show a wide range of pressure sensors applications, from commercial buildings to hospitals, production facilities, schools, data centers, hotels, sports arenas and government buildings. By monitoring and controlling air pressure, pressure sensors can improve air quality, energy efficiency, safety, efficiency, customer satisfaction and many others.
Pressure sensors for the HVAC application - Summary
To sum up, pressure sensors play a key role in automation of ventilation systems. They provide accurate and reliable air pressure measurements that are necessary to maintain optimal air flow and pressure levels in HVAC systems. As the demand for energy -saving and sustainable buildings, pressure sensors have become an indispensable tool for automation and control of building systems. They allow HVAC systems more efficient, reducing energy consumption and improving air quality in rooms. In addition, pressure sensors can help detect and diagnose problems in ventilation systems, enabling timely maintenance and repair. As the technology progresses, pressure sensors will continue to play an important role in the automation of ventilation systems, ensuring that the buildings are convenient, safe and energy -saving.
Leave a comment