-
BackX
-
Components
-
-
Category
-
Semiconductors
- Diodes
- Thyristors
-
Electro-insulated Modules
- Electro-insulated Modules | VISHAY (IR)
- Electro-insulated Modules | INFINEON (EUPEC)
- Electro-insulated Modules | Semikron
- Electro-insulated Modules | POWEREX
- Electro-insulated Modules | IXYS
- Electro-insulated Modules | POSEICO
- Electro-insulated Modules | ABB
- Electro-insulated Modules | TECHSEM
- Go to the subcategory
- Bridge Rectifiers
-
Transistors
- Transistors | GeneSiC
- SiC MOSFET Modules | Mitsubishi
- SiC MOSFET Modules | STARPOWER
- Module SiC MOSFET ABB’s
- IGBT Modules | MITSUBISHI
- Transistor Modules | MITSUBISHI
- MOSFET Modules | MITSUBISHI
- Transistor Modules | ABB
- IGBT Modules | POWEREX
- IGBT Modules | INFINEON (EUPEC)
- Silicon Carbide (SiC) semiconductor elements
- Go to the subcategory
- Gate Drivers
- Power Blocks
- Go to the subcategory
- Electrical Transducers
-
Passive components (capacitors, resistors, fuses, filters)
- Resistors
-
Fuses
- Miniature Fuses for electronic circuits - ABC & AGC Series
- Tubular Fast-acting Fuses
- Time-delay Fuse Links with GL/GG & AM characteristics
- Ultrafast Fuse Links
- Fast-acting Fuses (British & American standard)
- Fast-acting Fuses (European standard)
- Traction Fuses
- High-voltage Fuse Links
- Go to the subcategory
- Capacitors
- EMI Filters
- Supercapacitors
- Power surge protection
- Go to the subcategory
-
Relays and Contactors
- Relays and Contactors - Theory
- 3-Phase AC Semiconductor Relays
- DC Semiconductor Relays
- Controllers, Control Systems and Accessories
- Soft Starters and Reversible Relays
- Electromechanical Relays
- Contactors
- Rotary Switches
-
Single-Phase AC Semiconductor Relays
- AC ONE PHASE RELAYS 1 series| D2425 | D2450
- One phase semiconductor AC relays CWA and CWD series
- One phase semiconductor AC relays CMRA and CMRD series
- One phase semiconductor AC relays - PS series
- Double and quadruple semiconductor AC relays - D24 D, TD24 Q, H12D48 D series
- One phase semiconductor relays - gn series
- Ckr series single phase solid state relays
- One phase AC semiconductor relays for DIN bus - ERDA I ERAA series
- 150A AC single phase relays
- Rail Mountable Solid State Relays With Integrated Heat Sink - ENDA, ERDA1 / ERAA1 series
- Go to the subcategory
- Single-Phase AC Semiconductor Relays for PCBs
- Interface Relays
- Go to the subcategory
- Cores and Other Inductive Components
- Heatsinks, Varistors, Thermal Protection
- Fans
- Air Conditioning, Accessories for Electrical Cabinets, Coolers
-
Batteries, Chargers, Buffer Power Supplies and Inverters
- Batteries, Chargers - Theoretical Description
- Modular Li-ion Battery Building Blocks, Custom Batteries, BMS
- Batteries
- Battery Chargers and Accessories
- Uninterruptible Power Supply and Buffer Power Supplies
- Inverters and Photovoltaic Equipments
- Energy storage
- Fuel cells
- Lithium-ion batteries
- Go to the subcategory
-
Automatics
- Futaba Drone Parts
- Limit Switches, Microswitches
- Sensors, Transducers
-
Infrared Thermometers (Pyrometers)
- IR-TE Series - Water-proof Palm-sized Radiation Thermometer
- IR-TA Series - Handheld Type Radiation Thermometer
- IR-H Series - Handheld Type Radiation Thermometer
- IR-BA Series - High-speed Compact Radiation Thermometer
- IR-FA Series - Fiber Optic Radiation Thermometer
- IR-BZ Series - Compact Infrared Thermometers
- Go to the subcategory
- Counters, Time Relays, Panel Meters
- Industrial Protection Devices
- Light and Sound Signalling
- Thermographic Camera
- LED Displays
- Control Equipments
-
Recorders
- Hybrid Recorders - AL3000 Series | CHINO
- Graphic Recorder - KR2000 Series | CHINO
- Ubiquitous Recorders - KR5000 Series | CHINO
- Palm-sized Temperature/Humidity Meters - HN-CH Series | CHINO
- Consumables for Recorders
- 71VR1 - Compact Paperless Recorder | M-SYSTEM
- Graphic Recorder - KR3000 Series | CHINO
- PC Recorders - R1M Series | M-SYSTEM
- PC Recorders - R2M Series | M-SYSTEM
- PC Recorders - RZMS Series | M-SYSTEM
- PC Recorders - RZUS Series | M-SYSTEM
- Go to the subcategory
- Go to the subcategory
-
Cables, Litz wires, Conduits, Flexible connections
- Wires
- Litz wires
- Cables for extreme applications
- Sleevings
-
Braids
- Flat Braids
- Round Braids
- Very Flexible Flat Braids
- Very Flexible Round Braids
- Cylindrical Cooper Braids
- Cylindrical Cooper Braids and Sleevings
- Flexible Earthing Connections
- Galvanized and Stainless Steel Cylindrical Braids
- PCV Insulated Copper Braids (temp. up to 85C)
- Flat Aluminium Braids
- Junction Set - Braids and Tubes
- Go to the subcategory
- Traction Equipment
- Cable Terminals
- Flexible Insulated Busbars
- Flexible Multilayer Busbars
- Cable Duct Systems
- Hoses
- Go to the subcategory
- View all categories
-
Semiconductors
-
-
- Suppliers
-
Applications
- CNC Machine Tools
- DC and AC Drives (Inverters)
- Energetics
- Energy bank
- Equipment and Components for Hazardous Areas [Ex]
- Equipment for Distribution, Control and Telecommunications Cabinets
- HVAC Automation
- Induction Heating
- Industrial Automation
- Industrial Protective Devices
- Machines for Drying and Wood Processing
- Machines for Thermoforming Plastics
- Mining, Metallurgy and Foundry
- Motors and Transformers
- Power Supplies (UPS) and Rectifier Systems
- Printing
- Temperature Measurement and Regulation
- Test and Laboratory Measurements
- Tram and Railway Traction
- Welding Machines
-
Assembly
-
-
Inductors
-
-
Induction devices
-
-
https://www.dacpol.eu/pl/naprawy-i-modernizacje
-
-
Service
-
- Contact
- Zobacz wszystkie kategorie
Technical ceramics for metal injection molding processes
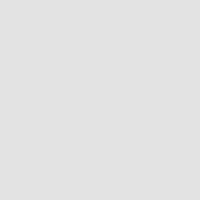
1. Introduction
Metal Injection Molding (MIM) is an advanced metal forming technique that combines the advantages of plastic injection molding and powder metallurgy. This process allows the production of complex metal parts with high precision and excellent mechanical properties.
It is also an extremely sensitive process, carrying several risks and challenges that can affect the final product quality and production efficiency. Issues such as excessive adhesion, uneven thermal distribution, and binder removal or non-uniform shrinkage of the component can arise. Many of these problems can be eliminated by using technical ceramics.
2. Introduction to Metal Injection Molding (MIM)
Metal Injection Molding (MIM) is a manufacturing technique that involves injecting "feedstock" into molds to create complex-shaped components with high repeatability. The feedstock is a mixture of powdered metal and a polymer binder that holds the material together. Before the components can be used, the binder must be removed and the internal structure of the parts strengthened; this is achieved by subjecting the components to debinding and sintering heat treatment processes in a furnace.
3. MIM Stages
Debinding
This is the process of removing the binder from the green part. It can be achieved either catalytically, where the binder is removed using a combination of catalytic additives, solvents, and water, or thermally, which requires heat treatment in a modified atmosphere in a furnace. The required method depends on the type of feedstock used. Components that have undergone this process are then referred to as "brown" parts. Depending on the type of feedstock used, both chemical and thermal debinding may be necessary. The chemical process removes most of the binder, while the thermal process removes the remaining binder, also known as "skeleton binder." This process is often referred to as "rest debinding."
Sintering
This is the heat treatment process of metal injection molded (MIM) components that have first undergone the debinding process (brown parts). The goal of sintering is to alter the internal microstructure of the components to improve their overall density and ultimately their strength. This is achieved by heating the metal parts in a furnace under an inert atmosphere to a temperature about 20% below the metal's melting point, allowing the atoms to diffuse through the microstructure and join into denser formations. During sintering, the metal parts will experience some shrinkage, with a 15-22% size reduction depending on the metal used and the final density of the parts. Temperature profiles, atmosphere, and temperature uniformity in the furnace during both debinding and sintering must be very precisely controlled to avoid distortion and the formation of cracks and blisters. An inert or reducing atmosphere is also important to prevent oxidation of the parts.
4. Use of Ceramic Plates in the Metal Injection Molding (MIM) Process
Ceramic plates are used to transport components produced in the metal injection molding process through all stages. Their application helps eliminate many problems occurring in the process.
- Porous yet smooth surface - no adhesion or melting of binders, uniform shrinkage of the part
- Plates made of porous, high-purity 99.5% alumina oxide ceramic - uniform shrinkage, no discoloration, less or no need for further processing
- Porosity makes the material lighter - less heat is required
Due to their high resistance to temperature cycles and high temperature (1500°C), one plate can be used for transport, debinding, and sintering. This results in cost savings – no additional tools are needed for each process.
The plates can be cut to any size, allowing for the creation of holes tailored to the product being processed. They are laser-cut, meaning no additional tooling is required – another cost-saving.
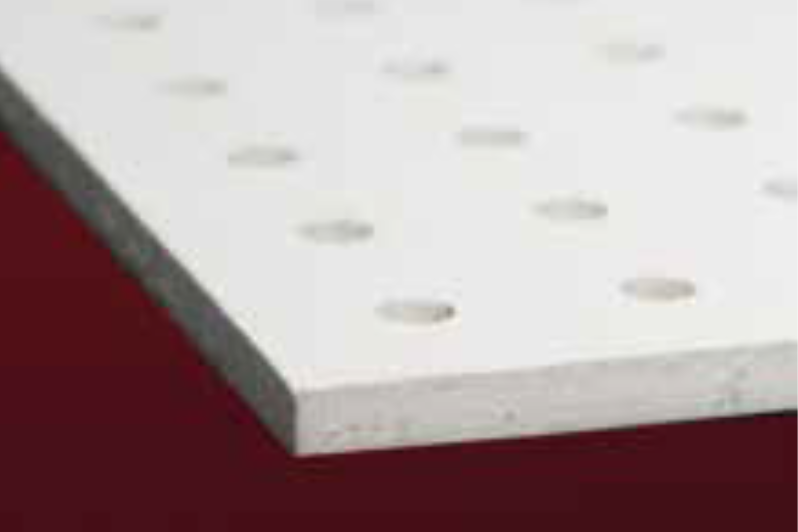
Fig. 2 Ceramic plates
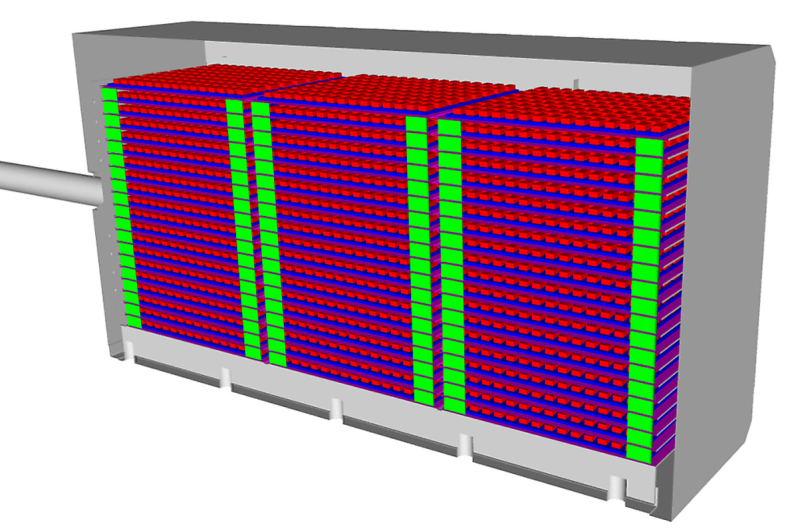
Fig. 3 Plates with elements placed in the furnace
5. Summary
The use of ceramic plates in the metal injection molding process brings tangible benefits. It significantly increases production efficiency by reducing the number of defective products.
If you are interested in custom-sized ceramic plates – feel free to contact us.
Have any questions?
+22 70 35 212
Related posts
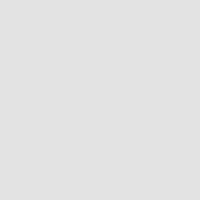
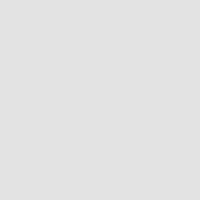
Leave a comment