-
BackX
-
Components
-
-
Category
-
Semiconductors
- Diodes
- Thyristors
-
Electro-insulated Modules
- Electro-insulated Modules | VISHAY (IR)
- Electro-insulated Modules | INFINEON (EUPEC)
- Electro-insulated Modules | Semikron
- Electro-insulated Modules | POWEREX
- Electro-insulated Modules | IXYS
- Electro-insulated Modules | POSEICO
- Electro-insulated Modules | ABB
- Electro-insulated Modules | TECHSEM
- Go to the subcategory
- Bridge Rectifiers
-
Transistors
- Transistors | GeneSiC
- SiC MOSFET Modules | Mitsubishi
- SiC MOSFET Modules | STARPOWER
- Module SiC MOSFET ABB’s
- IGBT Modules | MITSUBISHI
- Transistor Modules | MITSUBISHI
- MOSFET Modules | MITSUBISHI
- Transistor Modules | ABB
- IGBT Modules | POWEREX
- IGBT Modules | INFINEON (EUPEC)
- Silicon Carbide (SiC) semiconductor elements
- Go to the subcategory
- Gate Drivers
- Power Blocks
- Go to the subcategory
- Electrical Transducers
-
Passive components (capacitors, resistors, fuses, filters)
- Resistors
-
Fuses
- Miniature Fuses for electronic circuits - ABC & AGC Series
- Tubular Fast-acting Fuses
- Time-delay Fuse Links with GL/GG & AM characteristics
- Ultrafast Fuse Links
- Fast-acting Fuses (British & American standard)
- Fast-acting Fuses (European standard)
- Traction Fuses
- High-voltage Fuse Links
- Go to the subcategory
- Capacitors
- EMI Filters
- Supercapacitors
- Power surge protection
- TEMPEST emission revealing filters
- Go to the subcategory
-
Relays and Contactors
- Relays and Contactors - Theory
- 3-Phase AC Semiconductor Relays
- DC Semiconductor Relays
- Controllers, Control Systems and Accessories
- Soft Starters and Reversible Relays
- Electromechanical Relays
- Contactors
- Rotary Switches
-
Single-Phase AC Semiconductor Relays
- AC ONE PHASE RELAYS 1 series| D2425 | D2450
- One phase semiconductor AC relays CWA and CWD series
- One phase semiconductor AC relays CMRA and CMRD series
- One phase semiconductor AC relays - PS series
- Double and quadruple semiconductor AC relays - D24 D, TD24 Q, H12D48 D series
- One phase semiconductor relays - gn series
- Ckr series single phase solid state relays
- One phase AC semiconductor relays for DIN bus - ERDA I ERAA series
- 150A AC single phase relays
- Rail Mountable Solid State Relays With Integrated Heat Sink - ENDA, ERDA1 / ERAA1 series
- Go to the subcategory
- Single-Phase AC Semiconductor Relays for PCBs
- Interface Relays
- Go to the subcategory
- Cores and Other Inductive Components
- Heatsinks, Varistors, Thermal Protection
- Fans
- Air Conditioning, Accessories for Electrical Cabinets, Coolers
-
Batteries, Chargers, Buffer Power Supplies and Inverters
- Batteries, Chargers - Theoretical Description
- Modular Li-ion Battery Building Blocks, Custom Batteries, BMS
- Batteries
- Battery Chargers and Accessories
- Uninterruptible Power Supply and Buffer Power Supplies
- Inverters and Photovoltaic Equipments
- Energy storage
- Fuel cells
- Lithium-ion batteries
- Go to the subcategory
-
Automatics
- Futaba Drone Parts
- Limit Switches, Microswitches
- Sensors, Transducers
-
Infrared Thermometers (Pyrometers)
- IR-TE Series - Water-proof Palm-sized Radiation Thermometer
- IR-TA Series - Handheld Type Radiation Thermometer
- IR-H Series - Handheld Type Radiation Thermometer
- IR-BA Series - High-speed Compact Radiation Thermometer
- IR-FA Series - Fiber Optic Radiation Thermometer
- IR-BZ Series - Compact Infrared Thermometers
- Go to the subcategory
- Counters, Time Relays, Panel Meters
- Industrial Protection Devices
- Light and Sound Signalling
- Thermographic Camera
- LED Displays
- Control Equipments
- Go to the subcategory
-
Cables, Litz wires, Conduits, Flexible connections
- Wires
- Cable feedthroughs and couplers
- Litz wires
- Cables for extreme applications
- Sleevings
-
Braids
- Flat Braids
- Round Braids
- Very Flexible Flat Braids
- Very Flexible Round Braids
- Cylindrical Cooper Braids
- Cylindrical Cooper Braids and Sleevings
- Flexible Earthing Connections
- Galvanized and Stainless Steel Cylindrical Braids
- PCV Insulated Copper Braids (temp. up to 85C)
- Flat Aluminium Braids
- Junction Set - Braids and Tubes
- Go to the subcategory
- Traction Equipment
- Cable Terminals
- Flexible Insulated Busbars
- Flexible Multilayer Busbars
- Cable Duct Systems
- Go to the subcategory
- View all categories
-
Semiconductors
-
-
- Suppliers
-
Applications
- CNC Machine Tools
- DC and AC Drives (Inverters)
- Energetics
- Energy bank
- Equipment and Components for Hazardous Areas [Ex]
- Equipment for Distribution, Control and Telecommunications Cabinets
- HVAC Automation
- Induction Heating
- Industrial Automation
- Industrial Protective Devices
- Machines for Drying and Wood Processing
- Machines for Thermoforming Plastics
- Mining, Metallurgy and Foundry
- Motors and Transformers
- Power Supplies (UPS) and Rectifier Systems
- Printing
- Temperature Measurement and Regulation
- Test and Laboratory Measurements
- Tram and Railway Traction
- Welding Machines
-
Assembly
-
-
Inductors
-
-
Induction devices
-
-
https://www.dacpol.eu/pl/naprawy-i-modernizacje
-
-
Service
-
- Contact
- Zobacz wszystkie kategorie
7th Generation NX type (NX7) Converter Inverter Brake (CIB) Modules
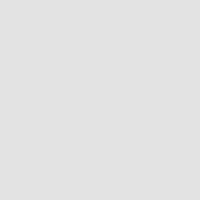
7th Generation NX type (NX7) Converter Inverter Brake (CIB) Modules
Developed to address the requirements of high performance drives by utilizing an innovative packaging concept and an advanced chip technology.
Applications such as elevator drives or servomotors have several special requirements. One on hand, high efficiency is important, while on the other hand, the inverter unit be resilient to the different types of load cycling. Furthermore, the inverter must be designed as compact as possible. NX7 CIB modules aim to address these challenges.
By Toshinari Hirai and Narender Lakshmanan, Mitsubishi Electric Europe B.V
Advanced Chip Technology Combined with a New Packaging Concept:
Each CIB module consists of an integrated 3 phase inverter part, a converter (3 ph diode rectifier) part and a brake chopper part. The line-up of the latest NX7 CIB modules is shown in Figure 1. The NX7 CIB modules utilize the latest 7th generation CSTBT™ IGBT along with the RFC (Relaxed Field of Cathode) diodes. The electrical characteristics of the new thin wafer 7th generation chips have been tuned for the reduction of overall power losses.
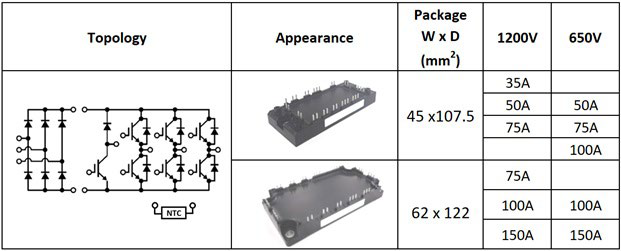
Figure 1: Line-up of the NX7 CIB Modules. NOTE: Pressfit and PCTIM options available.
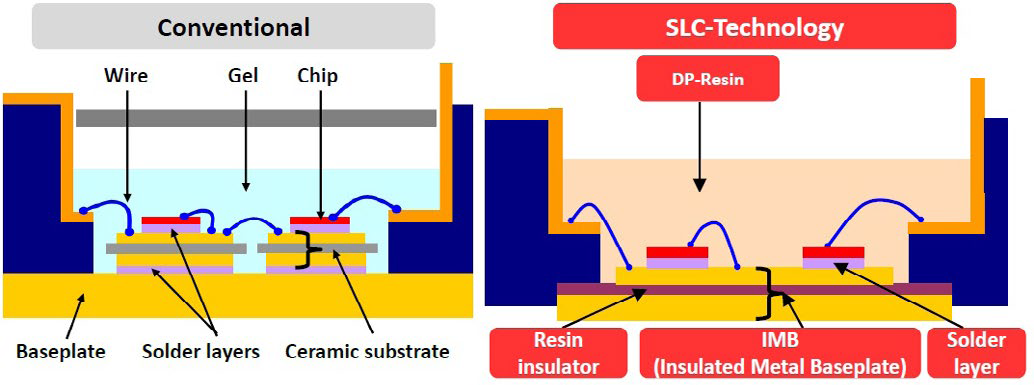
Figure 2: Cross section of the NX7 package versus a conventional module package.
The NX7 CIB employs a new packaging concept – the SLC (SoLid Cover) Technology which includes an insulated metal baseplate structure (refer to Figure 2). The conventional baseplate has been replaced by an insulated metal baseplate structure where the metal baseplate contains an organic insulation layer directly bonded to it. Therefore the conventional substrate solder between metal baseplate and isolation ceramic has been eliminated. The soft silicone gel of the conventional structure is replaced by the hard DP-resin (direct potting resin) [1].
Minimizing Losses and Maximizing Performance:
Operating the inverter at elevated switching frequencies helps in reducing the audible noise, hence low loss operation even at high switching frequencies is an important capability for applications such as elevators. In addition, limiting the IGBT chip temperature rise during low rotation speed (low output frequency) operation is a key requirement.
Figure 3 indicates the overall power loss comparison of an NX7 CIB module (CM50MXUA-24T) with a previous 6th gen. IGBT module (CM50MXA-24S) considering different switching frequencies and a low output current frequency of fout=5Hz. The benefit in terms of pow-
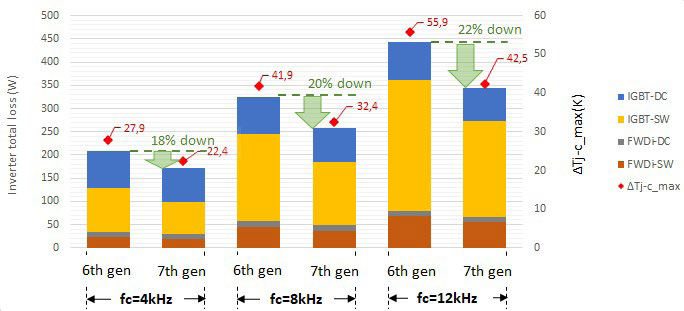
Figure 3: Power loss and junction temperature performance of the NX7 CIB vs conventional module. Conditions: VCC = 600V, Io = 24 Arms, PF = 0.9, M = 1, fout = 5 Hz, Data @ Tj = 125°C.W
er loss between a conventional module and an NX7 CIB module increases with increase in switching frequency. This can be attributed to the optimization in the trade-off between the switching losses and the ON state losses in the new 7th generation chip technology. A combination of loss reduction and the low thermal resistance (chip to case) offered by the 7th generation chip technology ensures that the maximum junction temperature can be reduced by utilizing the NX7 CIB module. The analysis indicated in Figure 3 has been carried out considering a target switching dv⁄dt (max)= 10 kV/μs.
Designed for High Reliability:
Intermittent operation is a characteristic feature of applications such as elevators. The impact of load cycling can be categorized into two types of cycling phenomena: power cycling and thermal cycling. Power cycling refers to a cycling of the junction temperature which affects the reliability of the chip-tobond wire contact whereas thermal cycling refers to the cycling of baseplate temperature which conventionally affect the solder layer connecting the isolation substrate and the baseplate. But due to the elimination of the ceramic substrate and the solder layer, the limitation pertaining to thermal cycling is not present in NX7 CIB modules.
Case 1: Extended Loading Conditions (temperature swing at the heatsink and case):
It is common for applications such as elevators to experience operation cycles where the heatsink temperature rises to an allowable point and then falls back to the ambient temperature. Session involving continuous operation which would generate a temperature swing at the heatsink, would also involve temperature swings at the case of the power module and at the chip surface (junction). An example of such operation is represented in Figure 4. For this analysis, the Mitsubishi Electric 6th generation modules represent the conventional modules.
The following points are the key conclusions from Figure 4:
- Bottleneck identification: For conventional modules which utilize a baseplate solder layer, thermal cycling performance is the lifetime limitation factor for long operation cycles due to the degradation of the solder layer under such conditions.
- Solution: The bottleneck (solder layer) has been eliminated in the new NX7 module due to the adoption of the IMB structure.
Case 2: Short term loading conditions (temperature swing predominantly at the chip):
Operating cycles (in the range of a few seconds) which generate temperature swings only at IGBT chip (ΔTj) affect the reliability of the chip to bond wire contact. The amplitude of the ΔTj is the deciding factor with regards to the power cycling lifetime. This point has been addressed by employing the low loss 7th generation chip technology
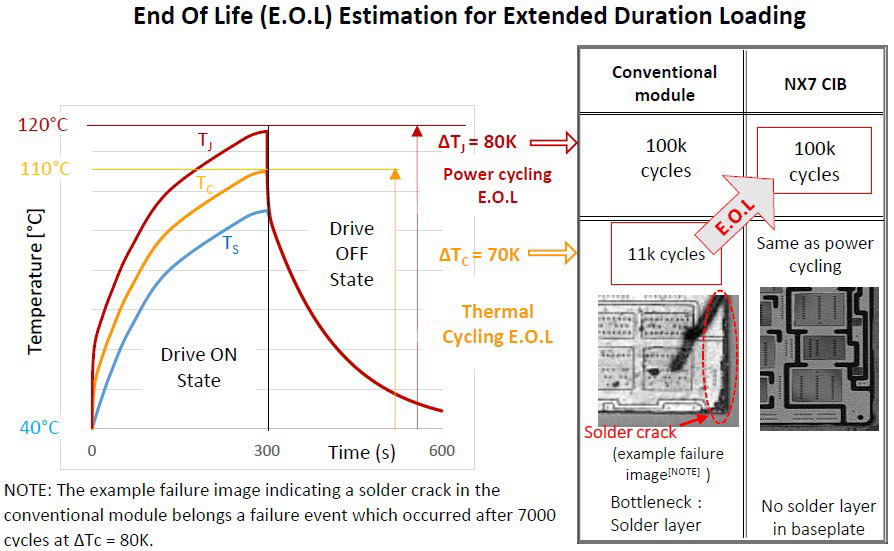
Figure 4: Lifetime estimation for extended duration loading (Conventional module vs NX7 CIB).
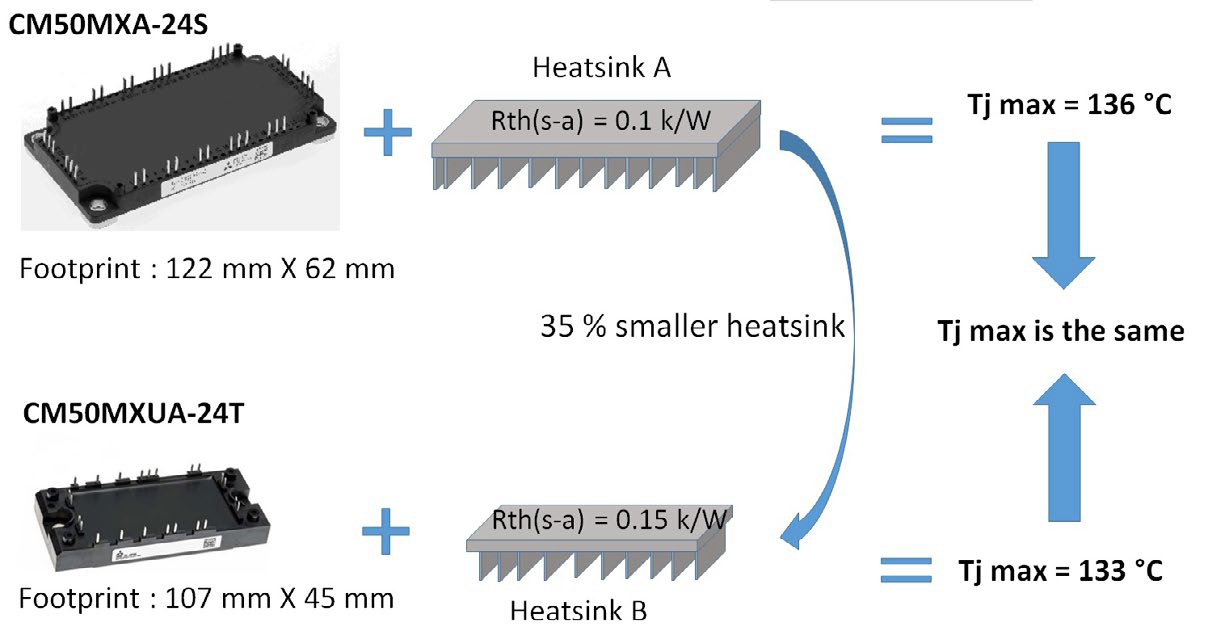
Figure 5: Compactness by heatsink reduction. Conditions: Vcc = 600V, fc = 12 kHz, fout = 5 Hz, M = 1, PF = 0.9, Ic = 24 Arms, Ta = 30 °C, data @ Tj = 125 °C

Figure 6: Optimization of terminal temperature in the NX7 CIB module.
in combination with the optimized chip to case thermal resistance in the NX7 module. This combination ensures that for the same operating condition, the corresponding ΔTj is lower (compared the performance of the conventional module). This tendency can be understood from the following results indicating power cycling capability based on the conditions mentioned in Figure 3 (for fc = 12 kHz):
- Conventional CIB (CM50MXA-24S): ΔTj = 54.52 K: 600 thousand cycles (approx.)
- NX7 CIB (CM50MXUA-24T): ΔTj = 36.64 K:WWWW 6 million cycles (approx.)
Summary – Overall lifetime enhancement
Overall improvement in lifetime has been ensured by the following two-step strategy:
- Elimination of the thermal cycling bottleneck
- Reduction of ΔTj to achieve better power cycling capability
Compact Design:
To achieve a compact design, several important considerations have to be made. The following points illustrate the advantage offered by adopting an NX7 CIB module.
1. Since the NX7 CIB module exhibits an improved loss performance and superior thermal performance (refer Figure 4), the designer can shrink the size of the heatsink in order to achieve an overall compact design. The example presented in Figure 5 illustrates a 35% reduction of the heatsink without causing an increase in the maximum junction temperature.
2. To achieve compactness, the classical copper busbar structure can be replaced by a PCB which would be connected to the terminals of the power module via pressfit or soldering. The challenge with this approach is that, due to high current density at the terminal pins, the temperature developed at the terminal could impose a limitation on the maximum operating current. This possibility has been taken into consideration while developing the NX7 CIB and accordingly the pin structure has been designed to reduce the temperature developed at the terminal during operation. As indicated in Figure 6, the temperature rise developed at the terminals of the Mitsubishi module (NX7 CIB) is lower in comparison with a competitor’s design. The improved thermal conductivity of the potting material (DP-resin) versus gel is an added advantage.
Scalable solutions:
The NX7 CIB line-up allows the designer to develop platform solutions – one mechanical design for multiple power ratings. For example, (refer Figure 1), in the 1200V category, the 45mm x 107.5mm module is available in 3 different current ratings (35A, 50A and 75A and the 62mm x 122mm module is available in 3 different current ratings (75A, 100A, 150A). This allows the designer to develop one mechanical design for 3 different power levels.
Conclusion:
The requirements of applications such as elevator drives have been taken into consideration while developing the NX7 CIB module. The unique combination of the SLC technology packing and the 7th generation chip technology allows the designer to develop an efficient, reliable and a compact inverter that can be used as a platform solution for multiple power levels.
References:
[1] Thomas Radke, et al: Enhanced IGBT Module Power Density Utilizing the Improved Thermal Conductivity of SLCTechnology, Bodo’s Power systems, June 2016
[2] Thomas Radke, et al : New Horizons in Thermal Cycling Capability Realized with the 7th gen. IGBT module Based on SLC-Technology, Bodo’s Power systems, May 2017
[3] MELCOSIM: IGBT thermal and loss simulation software, available at www. mitsubishielectric.com/semiconductors/ simulator/
Related posts
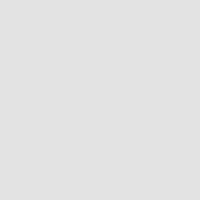
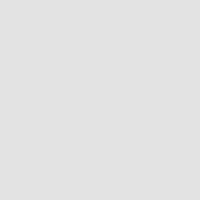
Leave a comment