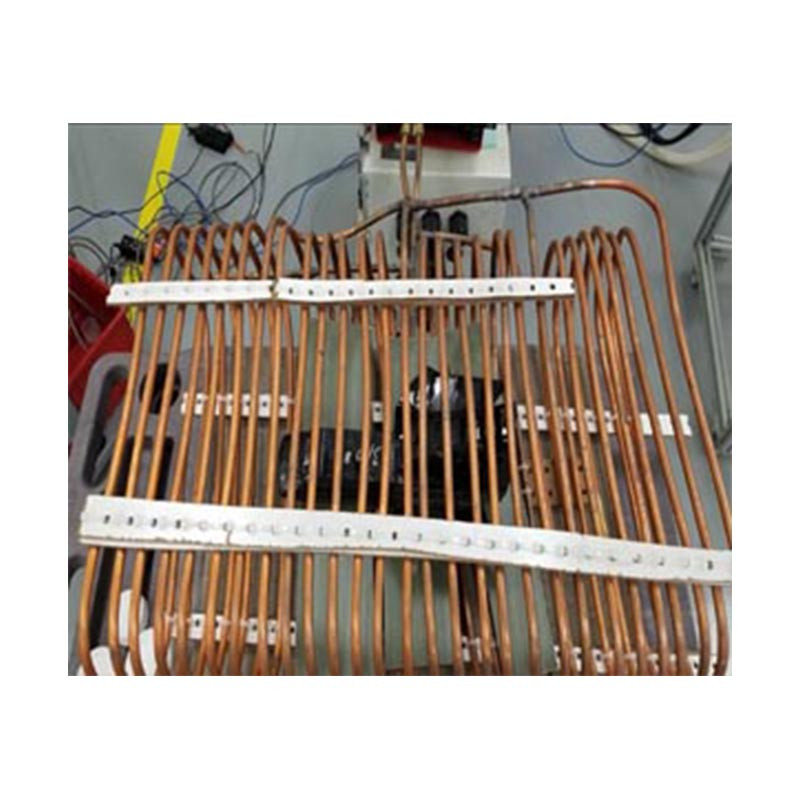
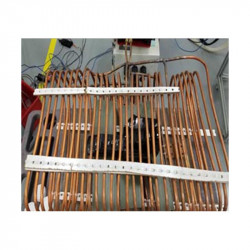
Category
Photos are for informational purposes only. View product specification
please use latin characters
Objective: To preheat castings and rods before welding; they were looking for faster, more repeatable heating than torches offered.
Equipment: Ambrell EKOHEATⓇ 20 kW, 15-40 kHz induction heating power supply with a workhead and coil specifically designed for this application.
Material: Magnetic steel castings and rods
Temperature: 450 °F (232 °C)
Testing:
Testing proved the viability of the application. The client targeted a heating time of 3 minutes. Using a torch, heating took 20 minutes.
Benefits:
Are you interested in this product? Do you need additional information or individual pricing?
Objective: To preheat castings and rods before welding; they were looking for faster, more repeatable heating than torches offered.
Equipment: Ambrell EKOHEATⓇ 20 kW, 15-40 kHz induction heating power supply with a workhead and coil specifically designed for this application.
Material: Magnetic steel castings and rods
Temperature: 450 °F (232 °C)
Testing:
Testing proved the viability of the application. The client targeted a heating time of 3 minutes. Using a torch, heating took 20 minutes.
Benefits:
Your review appreciation cannot be sent
Report comment
Report sent
Your report cannot be sent
Write your review
Review sent
Your review cannot be sent