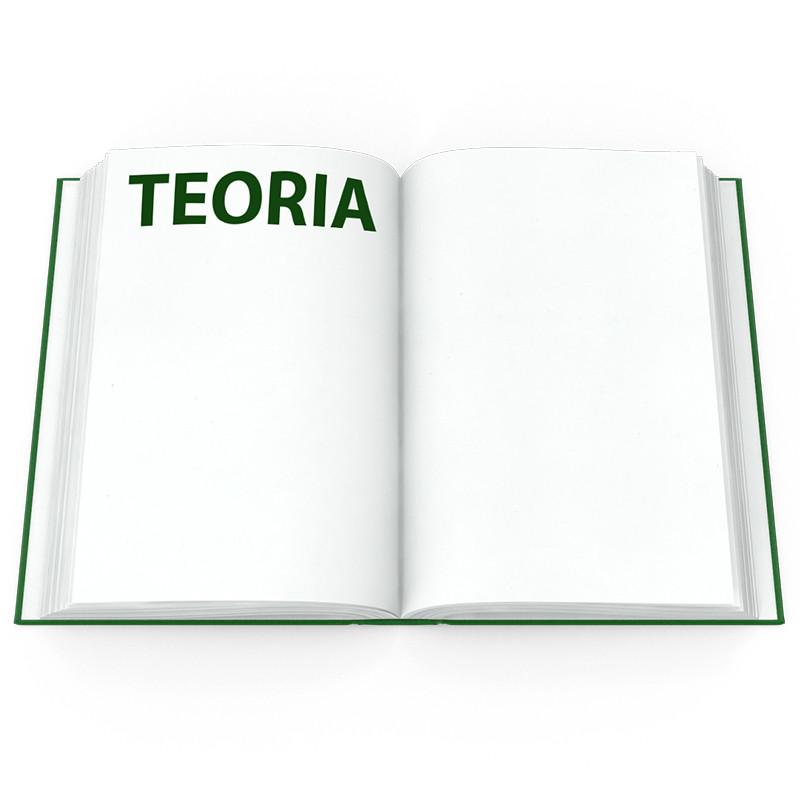
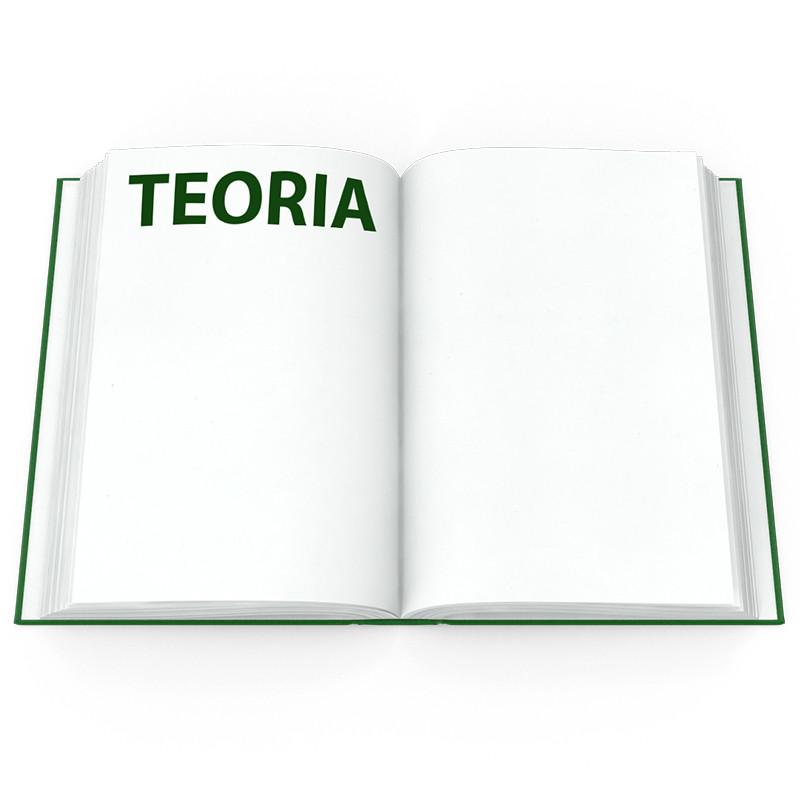
Category
Photos are for informational purposes only. View product specification
please use latin characters
Solid State Relays (SSR) are components used to control current load using a semiconductor controlled by a separated electronic circuit. Galvanic isolation is achieved using an optoelectronic element such as an infrared emitting diode, photodiode, phototransistor, photothyristor or phototriac. In the relay's idle state, when no current flows through the LED in the input circuit, the optoelectronic element remains off and its equivalent resistance is very high. Upon activation of the diode, the photoelement is irradiated and begins to conduct, closing the load circuit. This solution allows for a significant increase in switching frequency, eliminates the phenomenon of electric arc and enables achieving durability of the order of 109 .
The activation of the relay, depending on the type, can occur by supplying the input circuit with direct voltage (from 3V to 32V) or alternating voltage (from 90V to 280V at 50Hz). There is also the possibility of triggering the relay by current. Depending on the purpose, they are built for switching direct and alternating currents. Three-phase relays are also manufactured, used for example for switching three-phase electric motors.
We distinguish the following relays:
Zero-crossing relays – conduction occurs when the supply voltage crosses zero. Thanks to this solution, it increases gradually without causing radio interference. Used for controlling inductive and resistive loads (resistive heaters, light bulbs). | ![]() |
Instant-on relays – the activation occurs immediately after the control voltage is applied. This type of control is intended for solutions where a short response time is required. | ![]() |
Peak voltage relays - the relay operates when the supply voltage reaches its peak value. Used for highly inductive loads (transformers). | ![]() |
Analog switching relays – controlled by an analog signal (0-10V DC or 4-20mA DC). Used for smooth control of light intensity, heating, etc. | ![]() |
Input circuit
Output circuit
Operational parameters
Relay cooling
The lifespan of semiconductor relays is virtually unlimited provided they are properly cooled. Therefore, special attention should be paid to the selection of the heat sink, use thermal paste and ensure proper air circulation. A good solution is to mount the relay with the heat sink on a DIN rail, leaving free space around it.
Relay protection
Another important thing is protection against the effects of short circuits or overloads. Delayed fuses are not able to protect semiconductor relays, so for proper protection, ultra-fast fuses should be used, whose Joule integral value is less than the semiconductor's integral value. For full relay protection, a varistor should be connected at the output for surge protection.
The operating principle of electromagnetic relaysis similar to the principle of operation of an electromagnetic contactor. Relay contacts have a relatively low current-carrying capacity, on the order of a few amperes. Therefore, the relay is equipped with a much smaller electromagnet than the contactor, and the contacts do not have additional arc extinguishing devices.
The dimensions of the relay are smaller than those of the contactor, while the durability of the relay is very high and reaches several tens of millions of connections. Depending on their purpose, relays have one or more pairs of contacts. They can operate under the influence of changes in current intensity, voltage, direction of current flow, frequency, phase shift, etc. The principle of operation of the relay is explained by the diagram:
The flow of current through the coil winding causes the armature to be attracted. Upon attraction of the armature, the normally closed contacts close: (1), (2), (3) and the normally open contacts open (4). When the voltage is disconnected and the armature drops, the contacts open: (1),(2),(3) and the normally open contacts close (4). In the most commonly encountered relay designs, the coil voltage is 230VAC or 24VDC, the operating current of the contacts - from 1 to 10A, the number of contacts - from one to four pairs of changeover contacts.
A contactor is a switch, whose working contacts are closed by means of an electromagnet and maintained in this state, as long as the coil voltage is sufficiently high. When the coil circuit is interrupted, the armature drops (under the action of a spring) and the working contacts open.
Operation and construction of a contactorIt is similar to the construction and operation of electromagnetic relays. The difference is that contactors are used for connecting main circuits (e.g., motors), while electromagnetic relays are intended for connecting auxiliary circuits (e.g., control, signaling). In addition to main contacts, contactors can have several auxiliary contacts used for signaling or blocking. The principle of operation of a contactor is explained by the diagram:
Under the influence of current flowing through the contactor coil S, an attractive force is generated on the armature K, which causes the closing of the main contacts Z1, Z2, Z3, and auxiliary contacts z1, z2. Contactors are mainly intended for remote connection of three-phase AC circuits under conditions specified by the usage category AC3 and AC4 (connecting squirrel-cage motors). They can also be used for connecting slip-ring motors (category AC2) or heating devices (category AC1).
In addition to AC contactors, DC contactors are also available. They have electromagnetic or pneumatic drives, with both electromagnets and solenoid valves being controlled by DC. The main applications of these contactors are railway, tram, and battery traction (carts).
Contactors offered by DACPOL are available for AC coils in the power range from 1,5 to 238kW and DC coils in the power range from 2,2 to 11kW. The equipment includes a wide range of auxiliary contacts and delay relays, interface modules, and RC elements. Optionally, thermal relays can also be installed to protect electric motors.
Are you interested in this product? Do you need additional information or individual pricing?
Solid State Relays (SSR) are components used to control current load using a semiconductor controlled by a separated electronic circuit. Galvanic isolation is achieved using an optoelectronic element such as an infrared emitting diode, photodiode, phototransistor, photothyristor or phototriac. In the relay's idle state, when no current flows through the LED in the input circuit, the optoelectronic element remains off and its equivalent resistance is very high. Upon activation of the diode, the photoelement is irradiated and begins to conduct, closing the load circuit. This solution allows for a significant increase in switching frequency, eliminates the phenomenon of electric arc and enables achieving durability of the order of 109 .
The activation of the relay, depending on the type, can occur by supplying the input circuit with direct voltage (from 3V to 32V) or alternating voltage (from 90V to 280V at 50Hz). There is also the possibility of triggering the relay by current. Depending on the purpose, they are built for switching direct and alternating currents. Three-phase relays are also manufactured, used for example for switching three-phase electric motors.
We distinguish the following relays:
Zero-crossing relays – conduction occurs when the supply voltage crosses zero. Thanks to this solution, it increases gradually without causing radio interference. Used for controlling inductive and resistive loads (resistive heaters, light bulbs). | ![]() |
Instant-on relays – the activation occurs immediately after the control voltage is applied. This type of control is intended for solutions where a short response time is required. | ![]() |
Peak voltage relays - the relay operates when the supply voltage reaches its peak value. Used for highly inductive loads (transformers). | ![]() |
Analog switching relays – controlled by an analog signal (0-10V DC or 4-20mA DC). Used for smooth control of light intensity, heating, etc. | ![]() |
Input circuit
Output circuit
Operational parameters
Relay cooling
The lifespan of semiconductor relays is virtually unlimited provided they are properly cooled. Therefore, special attention should be paid to the selection of the heat sink, use thermal paste and ensure proper air circulation. A good solution is to mount the relay with the heat sink on a DIN rail, leaving free space around it.
Relay protection
Another important thing is protection against the effects of short circuits or overloads. Delayed fuses are not able to protect semiconductor relays, so for proper protection, ultra-fast fuses should be used, whose Joule integral value is less than the semiconductor's integral value. For full relay protection, a varistor should be connected at the output for surge protection.
The operating principle of electromagnetic relaysis similar to the principle of operation of an electromagnetic contactor. Relay contacts have a relatively low current-carrying capacity, on the order of a few amperes. Therefore, the relay is equipped with a much smaller electromagnet than the contactor, and the contacts do not have additional arc extinguishing devices.
The dimensions of the relay are smaller than those of the contactor, while the durability of the relay is very high and reaches several tens of millions of connections. Depending on their purpose, relays have one or more pairs of contacts. They can operate under the influence of changes in current intensity, voltage, direction of current flow, frequency, phase shift, etc. The principle of operation of the relay is explained by the diagram:
The flow of current through the coil winding causes the armature to be attracted. Upon attraction of the armature, the normally closed contacts close: (1), (2), (3) and the normally open contacts open (4). When the voltage is disconnected and the armature drops, the contacts open: (1),(2),(3) and the normally open contacts close (4). In the most commonly encountered relay designs, the coil voltage is 230VAC or 24VDC, the operating current of the contacts - from 1 to 10A, the number of contacts - from one to four pairs of changeover contacts.
A contactor is a switch, whose working contacts are closed by means of an electromagnet and maintained in this state, as long as the coil voltage is sufficiently high. When the coil circuit is interrupted, the armature drops (under the action of a spring) and the working contacts open.
Operation and construction of a contactorIt is similar to the construction and operation of electromagnetic relays. The difference is that contactors are used for connecting main circuits (e.g., motors), while electromagnetic relays are intended for connecting auxiliary circuits (e.g., control, signaling). In addition to main contacts, contactors can have several auxiliary contacts used for signaling or blocking. The principle of operation of a contactor is explained by the diagram:
Under the influence of current flowing through the contactor coil S, an attractive force is generated on the armature K, which causes the closing of the main contacts Z1, Z2, Z3, and auxiliary contacts z1, z2. Contactors are mainly intended for remote connection of three-phase AC circuits under conditions specified by the usage category AC3 and AC4 (connecting squirrel-cage motors). They can also be used for connecting slip-ring motors (category AC2) or heating devices (category AC1).
In addition to AC contactors, DC contactors are also available. They have electromagnetic or pneumatic drives, with both electromagnets and solenoid valves being controlled by DC. The main applications of these contactors are railway, tram, and battery traction (carts).
Contactors offered by DACPOL are available for AC coils in the power range from 1,5 to 238kW and DC coils in the power range from 2,2 to 11kW. The equipment includes a wide range of auxiliary contacts and delay relays, interface modules, and RC elements. Optionally, thermal relays can also be installed to protect electric motors.
Your review appreciation cannot be sent
Report comment
Report sent
Your report cannot be sent
Write your review
Review sent
Your review cannot be sent