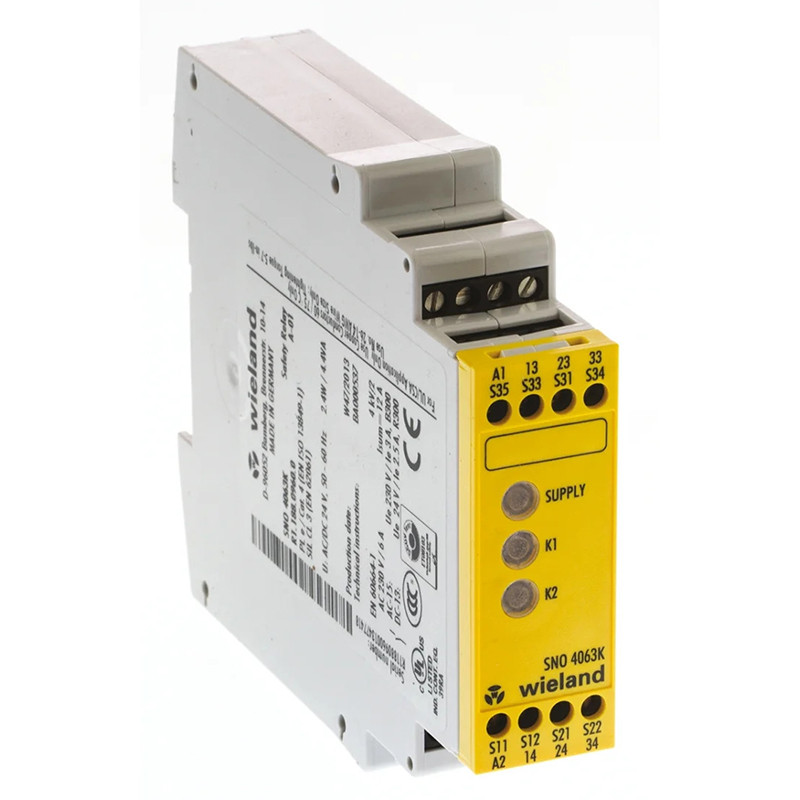
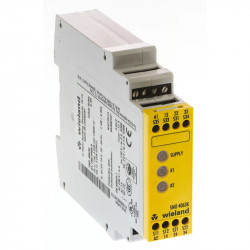
Category
Photos are for informational purposes only. View product specification
please use latin characters
Base devices for single-channel or two-channel emergency stop,safety gate, safety mat/strip and light curtain monitoring
• Stop category 0 according to EN 60204-1
• Applications up to safety category 4 according to EN 954-1
• Safety category of the devices: 4 according to EN 954-1
• Manual or automatic start
• Cross monitoring
• Single-channel and two-channel control
• 3 enabling current paths (NO contact, positively driven);
feedback loop for monitoring external contactors
• Supply voltage reset with SNO 4063KR (without start inhibit)
• Emergency stop, safety gate, safety mat and light curtain applications
• For processing signals from the output signal switching devices (OSSD) of a light
curtain according to DIN EN 61496-1
• For connecting to a safety mat according to DIN EN 1760-1
SNO 4063K
The device is a two-channel switching device for emergency stop applications with self-monitoring on each ON-OFF cycle. It complies with EN 60204-1 and is equipped with positively driven relays.
Basic function
After supply voltage has been applied to terminals A1 / A2 and the safety inputs closed, operating of the reset button closes the enabling current paths (manual start). When the safety inputs are opened/de-energized the enabling current paths will open.
Operating modes / system functions
•Single or two-channel control
With single-channel control both safety channels CH1 and CH2 are connected in parallel; with two-channel control they are switched separately.
•Without cross monitoring
Both safety channels are switched to the positive potential (S12 and S31 to S11).
•With cross monitoring
Safety channel CH1 is switched to the positive potential (S11 to S12), and safety channel CH2 to the negative potential (S21 to S22).
• Manual start
When the safety inputs are closed, a button is used to open reset input S34 (triggering with falling edge) or to close reset input S35 (triggering with rising edge).
•Automatic start
Reset input S35 is connected to S33. The device starts with the rising edge of the signal on safety input S12.
• Start inhibit
After supply voltage has been applied and the safety inputs closed, the enabling paths will not close. Starting is only possible after the reset button has been operated. For start inhibit the reset inputs have to be controlled with the
button, as with manual start mode.
• Restart inhibit
No restart after the safety inputs have been opened and closed. Restarting is only possible after the reset button has been operated. For restart inhibit the reset inputs have to be activated with the button, as in manual start
mode.
• Semiconductor compatible
OSSD (output signal switching devices) signals from a light curtain or other safety sensors with semiconductor outputs can be processed. Test pulses < t TP do not influence the device functions. Test pulses > t TP can lock the device.
• Synchrocheck
With two-channel control both safety channels are monitored against one another with the synchronous time tS . Safety channel CH1 must close before CH2 and bridge S33 / S35 must be connected. If CH2 closes before CH1, the
synchronous time is t S =∞
SNO 4063KM
The function of this device corresponds to that of the SNO 4063K without synchrocheck. The device is suitable for connecting to light curtains for Si category 4 and to short-circuit forming 4-wire safety mats, switching strips or switching edges (without monitoring resistance).
•Safety mats
The device must be operated with two channels and cross monitoring. If there is resistance < 50 Ω
/ channel and a short circuit between the channels (S11 / S12 and S21 / S22) the enabling paths open and the SUPPLY LED flashes.
•Light curtain for Si category 4
The device will be operated with two channels and without cross monitoring, if the light curtain connected to the OSSD detects a shunt fault on its own.
•Input debouncing
Input debouncing prevents fast consecutive switching of the enabling current paths when the safety inputs are opened for less than t ASP
Safety inputs opened for longer than t ASP lead to opening of the enabling current paths after t R . Restarting is blocked for time t SP
For applications with tactile operating modes (rapid ON-OFF cycles, for example at
manual supply) we recommend the use of SNO 4063KM
SNO 4063K/KR/KM/K-A/KR-A/KM-A | AC/DC 24 V |
![]() |
|
SNO 4063K/KR/K-A/KR-A | AC 115 – 120 V/AC 230 V |
![]() |
![]() |
A1/A2 S12 S31/S22 S34 K1,K2 13/14,23/24,33/34 tM= minimum ON time tA1 = response time tTP = test pulse time, tR = release time tW = recovery time |
![]() |
A1/A2 S12 S31/S22 S34 K1,K2 13/14,23/24,33/34 tM= minimum ON time tA3/A1 = response time tTP = test pulse time, tR = release time tW = recovery time |
![]() |
A1/A2 S12 S31/S22 S34 K1,K2 13/14,23/24,33/34 tSP= disable time, tA2 = response time tTP = test pulse time, tASP = response time of the disable tR = release time tW = recovery time |
SNO 4062K/SNO 4062KM |
![]() |
SNO 4062K-A/SNO 4062KM-A |
![]() |
Overview of devices / Part numbers | |||
---|---|---|---|
type | Rated voltage | Terminals | numer Std. Pack |
SNO 4063K |
DC 12 V
|
Terminal block, rising cage termination | R1.188.1110.0 1 |
AC/DC 24 V 50 - 60 Hz
|
Terminal block, rising cage termination | R1.188.0960.0 1 | |
AC 115 - 120 V 50 - 60 Hz
|
Terminal block, rising cage termination | R1.188.0970.0 1 | |
AC 230 V 50 - 60 Hz
|
Terminal block, rising cage termination | R1.188.0980.0 1 | |
SNO 4063K-A |
DC 12 V
|
Pluggable connector, rising cage terminatio | R1.188.1120.0 1 |
AC/DC 24 V 50 - 60 Hz
|
Pluggable connector, rising cage terminatio | R1.188.0990.0 1 | |
AC 115 - 120 V 50 - 60 Hz
|
Pluggable connector, rising cage terminatio | R1.188.1000.0 1 | |
AC 230 V 50 - 60 Hz
|
Pluggable connector, rising cage terminatio | R1.188.1010.0 1 | |
SNO 4063KM |
AC/DC 24 V 50 - 60 Hz
|
Terminal block, rising cage termination | R1.188.1270.0 1 |
SNO 4063KM-A |
AC/DC 24 V 50 - 60 Hz
|
Pluggable connector, rising cage terminatio | R1.188.1280.0 1 |
SNO 4063KR |
DC 12 V
|
Terminal block, rising cage termination | R1.188.1160.0 1 |
AC/DC 24 V 50 - 60 Hz
|
Terminal block, rising cage termination | R1.188.1130.0 1 | |
AC 115 - 120 V 50 - 60 Hz
|
Terminal block, rising cage termination | R1.188.1140.0 1 | |
AC 230 V 50 - 60 Hz
|
Terminal block, rising cage termination | R1.188.1150.0 1 | |
SNO 4063KR-A |
DC 12 V
|
Pluggable connector, rising cage termination | R1.188.1200.0 1 |
AC/DC 24 V 50 - 60 Hz
|
Pluggable connector, rising cage termination | R1.188.1170.0 1 | |
AC 115 - 120 V 50 - 60 Hz
|
Pluggable connector, rising cage termination | R1.188.1180.0 1 | |
AC 230 V 50 - 60 Hz
|
Pluggable connector, rising cage termination | R1.188.1190.0 1 |
Technical data | SNO 4063K/SNO 4063KR | SNO 4063KM | |
---|---|---|---|
Function according to EN 60204-1
|
Emergency stop relay
|
||
Function display
|
3 LEDs green
|
||
Function diagram
|
FD 221-5-1 W, FD 221-5-2 W, FD 221-5-3 W
|
||
Power supply circuit
|
|||
Rated voltage U
|
DC 12 V,AC/DC 24V,
AC 115 -120 V,AC 230 V |
AC/DC 24 V
|
|
Rated consumption DC
|
2,0 W
|
2,1 W
|
|
Rated consumption AC
|
2,4 W/4,4 VA
|
2,5 W/4,6 VA
|
|
Residual ripple
|
2,4 VSS
|
||
Rated frequency
|
50-60 Hz
|
||
Operating voltage range
|
0,85-1,1xUN
|
||
Fuse for control circuit supply
|
short-circuit resistant
|
||
Control circuit
|
|||
Outputs (S11, S21)
|
|||
Rated output voltage (S11 to S21)
|
DC22V
|
||
Open circuit voltage (only AC devices)
|
<40V
|
||
Output current
|
100 mA
|
||
Short circuit protection / current limitation
|
tak/-
|
tak/250 mA
|
|
Inputs (S12 / S33, S31 / S22, S34, S35)
|
|||
Input voltage range (only for DC devices)
|
DC 17,4 V bis DC 26,4 V
|
||
Rated current / peak current (safety inputs S12 / S33, S31 / S22)
|
40mA/100mA
|
||
Rated current / peak current (reset inputs S34, S35)
|
5 mA/50 mA
|
||
Times
|
|||
Permissible test pulse time tTP / test frequency
|
≤ 1000 us≤10s-1
|
||
Response time tA1 (reset input S34)
|
20 ms - 40 ms
|
||
Response time tA2 (reset input S34)
|
200 ms - 600 ms
|
20 ms - 80 ms
|
|
Response time tA3 (only SNO 4063KR)
|
100ms-400ms
|
||
Minimum ON time tM (reset inputs S34, S35)
|
>80ms
|
||
Locking time tSP
|
-
|
70ms-130ms
|
|
Response time of the lock tASP
|
-
|
>7ms
|
|
Recovery time tW
|
≥100 ms
|
||
Release time tR (K1, K2) with emergency stop
|
<25ms
|
||
Synchronous time tS
|
ca. 200 ms
|
||
Output circuit
|
|||
Enabling paths
|
|||
Contact assignment
|
3 NO contacts, positively driven
|
||
Rated switching voltage U
|
AC 230V/DC 300V
|
||
Max. continuous current I per current path
|
6A
|
||
Max. total current of all current paths DC 12 V, AC/ DC 24 VAC
|
12A 8A
|
||
115 -120 V, AC 230 V
|
|||
Application category according to EN 60947-5 -1 360 h-1
|
AC-15: Ue 230 V AC, Ie 4A / DC-13: Ue24 V DC, Ie 4 A
|
||
3600 h-1
|
AC-15: Ue 230 V AC, Ie 3 A / DC-13: Ue 24 V DC, Ie 2,5 A
|
||
Short-circuit protection, max. fuse insert
|
6 A class gG or circuit breaker with trigger characteristic B or C
|
||
Mechanical life
|
10x106 switching cycles
|
||
General data
|
|||
Creepage distances and clearances between the circuits
|
according EN 60664-1
|
||
Rated impulse voltage
|
4kV
|
||
Overvoltage category
|
III
|
||
Degree of pollution of the device: inside / outside
|
2/3
|
||
Rated voltage
|
AC 300 V
|
||
Test voltage Uaff 50 Hz
|
2kV
|
||
Protection degree according to DIN EN 60529
(housing / terminals)
|
IP40/IP20
|
||
Ambient temperature / storage temperature
|
-25-+55°C/-25-+75°C
|
||
Dimension diagram |
K 4-1 (screw terminals / K 4-2 (pluggable terminals
|
||
Wire ranges fine-stranded / solid or fine-stranded with ferrules
|
2 x 0,14 - 0,75 mm2/1 x 0,14-2,5 mm2
1 x 0,25 - 2,5 mm2/2 x 0,25 - 0,5 mm2 |
||
Permissible tightening torque
|
0,5 - 0,6 Nm
AWG 18-16 tylko przewody Cu |
||
Weight
|
0.21 kg (DC device) / 0.25 kg (AC device)
|
Are you interested in this product? Do you need additional information or individual pricing?
Base devices for single-channel or two-channel emergency stop,safety gate, safety mat/strip and light curtain monitoring
• Stop category 0 according to EN 60204-1
• Applications up to safety category 4 according to EN 954-1
• Safety category of the devices: 4 according to EN 954-1
• Manual or automatic start
• Cross monitoring
• Single-channel and two-channel control
• 3 enabling current paths (NO contact, positively driven);
feedback loop for monitoring external contactors
• Supply voltage reset with SNO 4063KR (without start inhibit)
• Emergency stop, safety gate, safety mat and light curtain applications
• For processing signals from the output signal switching devices (OSSD) of a light
curtain according to DIN EN 61496-1
• For connecting to a safety mat according to DIN EN 1760-1
SNO 4063K
The device is a two-channel switching device for emergency stop applications with self-monitoring on each ON-OFF cycle. It complies with EN 60204-1 and is equipped with positively driven relays.
Basic function
After supply voltage has been applied to terminals A1 / A2 and the safety inputs closed, operating of the reset button closes the enabling current paths (manual start). When the safety inputs are opened/de-energized the enabling current paths will open.
Operating modes / system functions
•Single or two-channel control
With single-channel control both safety channels CH1 and CH2 are connected in parallel; with two-channel control they are switched separately.
•Without cross monitoring
Both safety channels are switched to the positive potential (S12 and S31 to S11).
•With cross monitoring
Safety channel CH1 is switched to the positive potential (S11 to S12), and safety channel CH2 to the negative potential (S21 to S22).
• Manual start
When the safety inputs are closed, a button is used to open reset input S34 (triggering with falling edge) or to close reset input S35 (triggering with rising edge).
•Automatic start
Reset input S35 is connected to S33. The device starts with the rising edge of the signal on safety input S12.
• Start inhibit
After supply voltage has been applied and the safety inputs closed, the enabling paths will not close. Starting is only possible after the reset button has been operated. For start inhibit the reset inputs have to be controlled with the
button, as with manual start mode.
• Restart inhibit
No restart after the safety inputs have been opened and closed. Restarting is only possible after the reset button has been operated. For restart inhibit the reset inputs have to be activated with the button, as in manual start
mode.
• Semiconductor compatible
OSSD (output signal switching devices) signals from a light curtain or other safety sensors with semiconductor outputs can be processed. Test pulses < t TP do not influence the device functions. Test pulses > t TP can lock the device.
• Synchrocheck
With two-channel control both safety channels are monitored against one another with the synchronous time tS . Safety channel CH1 must close before CH2 and bridge S33 / S35 must be connected. If CH2 closes before CH1, the
synchronous time is t S =∞
SNO 4063KM
The function of this device corresponds to that of the SNO 4063K without synchrocheck. The device is suitable for connecting to light curtains for Si category 4 and to short-circuit forming 4-wire safety mats, switching strips or switching edges (without monitoring resistance).
•Safety mats
The device must be operated with two channels and cross monitoring. If there is resistance < 50 Ω
/ channel and a short circuit between the channels (S11 / S12 and S21 / S22) the enabling paths open and the SUPPLY LED flashes.
•Light curtain for Si category 4
The device will be operated with two channels and without cross monitoring, if the light curtain connected to the OSSD detects a shunt fault on its own.
•Input debouncing
Input debouncing prevents fast consecutive switching of the enabling current paths when the safety inputs are opened for less than t ASP
Safety inputs opened for longer than t ASP lead to opening of the enabling current paths after t R . Restarting is blocked for time t SP
For applications with tactile operating modes (rapid ON-OFF cycles, for example at
manual supply) we recommend the use of SNO 4063KM
SNO 4063K/KR/KM/K-A/KR-A/KM-A | AC/DC 24 V |
![]() |
|
SNO 4063K/KR/K-A/KR-A | AC 115 – 120 V/AC 230 V |
![]() |
![]() |
A1/A2 S12 S31/S22 S34 K1,K2 13/14,23/24,33/34 tM= minimum ON time tA1 = response time tTP = test pulse time, tR = release time tW = recovery time |
![]() |
A1/A2 S12 S31/S22 S34 K1,K2 13/14,23/24,33/34 tM= minimum ON time tA3/A1 = response time tTP = test pulse time, tR = release time tW = recovery time |
![]() |
A1/A2 S12 S31/S22 S34 K1,K2 13/14,23/24,33/34 tSP= disable time, tA2 = response time tTP = test pulse time, tASP = response time of the disable tR = release time tW = recovery time |
SNO 4062K/SNO 4062KM |
![]() |
SNO 4062K-A/SNO 4062KM-A |
![]() |
Overview of devices / Part numbers | |||
---|---|---|---|
type | Rated voltage | Terminals | numer Std. Pack |
SNO 4063K |
DC 12 V
|
Terminal block, rising cage termination | R1.188.1110.0 1 |
AC/DC 24 V 50 - 60 Hz
|
Terminal block, rising cage termination | R1.188.0960.0 1 | |
AC 115 - 120 V 50 - 60 Hz
|
Terminal block, rising cage termination | R1.188.0970.0 1 | |
AC 230 V 50 - 60 Hz
|
Terminal block, rising cage termination | R1.188.0980.0 1 | |
SNO 4063K-A |
DC 12 V
|
Pluggable connector, rising cage terminatio | R1.188.1120.0 1 |
AC/DC 24 V 50 - 60 Hz
|
Pluggable connector, rising cage terminatio | R1.188.0990.0 1 | |
AC 115 - 120 V 50 - 60 Hz
|
Pluggable connector, rising cage terminatio | R1.188.1000.0 1 | |
AC 230 V 50 - 60 Hz
|
Pluggable connector, rising cage terminatio | R1.188.1010.0 1 | |
SNO 4063KM |
AC/DC 24 V 50 - 60 Hz
|
Terminal block, rising cage termination | R1.188.1270.0 1 |
SNO 4063KM-A |
AC/DC 24 V 50 - 60 Hz
|
Pluggable connector, rising cage terminatio | R1.188.1280.0 1 |
SNO 4063KR |
DC 12 V
|
Terminal block, rising cage termination | R1.188.1160.0 1 |
AC/DC 24 V 50 - 60 Hz
|
Terminal block, rising cage termination | R1.188.1130.0 1 | |
AC 115 - 120 V 50 - 60 Hz
|
Terminal block, rising cage termination | R1.188.1140.0 1 | |
AC 230 V 50 - 60 Hz
|
Terminal block, rising cage termination | R1.188.1150.0 1 | |
SNO 4063KR-A |
DC 12 V
|
Pluggable connector, rising cage termination | R1.188.1200.0 1 |
AC/DC 24 V 50 - 60 Hz
|
Pluggable connector, rising cage termination | R1.188.1170.0 1 | |
AC 115 - 120 V 50 - 60 Hz
|
Pluggable connector, rising cage termination | R1.188.1180.0 1 | |
AC 230 V 50 - 60 Hz
|
Pluggable connector, rising cage termination | R1.188.1190.0 1 |
Technical data | SNO 4063K/SNO 4063KR | SNO 4063KM | |
---|---|---|---|
Function according to EN 60204-1
|
Emergency stop relay
|
||
Function display
|
3 LEDs green
|
||
Function diagram
|
FD 221-5-1 W, FD 221-5-2 W, FD 221-5-3 W
|
||
Power supply circuit
|
|||
Rated voltage U
|
DC 12 V,AC/DC 24V,
AC 115 -120 V,AC 230 V |
AC/DC 24 V
|
|
Rated consumption DC
|
2,0 W
|
2,1 W
|
|
Rated consumption AC
|
2,4 W/4,4 VA
|
2,5 W/4,6 VA
|
|
Residual ripple
|
2,4 VSS
|
||
Rated frequency
|
50-60 Hz
|
||
Operating voltage range
|
0,85-1,1xUN
|
||
Fuse for control circuit supply
|
short-circuit resistant
|
||
Control circuit
|
|||
Outputs (S11, S21)
|
|||
Rated output voltage (S11 to S21)
|
DC22V
|
||
Open circuit voltage (only AC devices)
|
<40V
|
||
Output current
|
100 mA
|
||
Short circuit protection / current limitation
|
tak/-
|
tak/250 mA
|
|
Inputs (S12 / S33, S31 / S22, S34, S35)
|
|||
Input voltage range (only for DC devices)
|
DC 17,4 V bis DC 26,4 V
|
||
Rated current / peak current (safety inputs S12 / S33, S31 / S22)
|
40mA/100mA
|
||
Rated current / peak current (reset inputs S34, S35)
|
5 mA/50 mA
|
||
Times
|
|||
Permissible test pulse time tTP / test frequency
|
≤ 1000 us≤10s-1
|
||
Response time tA1 (reset input S34)
|
20 ms - 40 ms
|
||
Response time tA2 (reset input S34)
|
200 ms - 600 ms
|
20 ms - 80 ms
|
|
Response time tA3 (only SNO 4063KR)
|
100ms-400ms
|
||
Minimum ON time tM (reset inputs S34, S35)
|
>80ms
|
||
Locking time tSP
|
-
|
70ms-130ms
|
|
Response time of the lock tASP
|
-
|
>7ms
|
|
Recovery time tW
|
≥100 ms
|
||
Release time tR (K1, K2) with emergency stop
|
<25ms
|
||
Synchronous time tS
|
ca. 200 ms
|
||
Output circuit
|
|||
Enabling paths
|
|||
Contact assignment
|
3 NO contacts, positively driven
|
||
Rated switching voltage U
|
AC 230V/DC 300V
|
||
Max. continuous current I per current path
|
6A
|
||
Max. total current of all current paths DC 12 V, AC/ DC 24 VAC
|
12A 8A
|
||
115 -120 V, AC 230 V
|
|||
Application category according to EN 60947-5 -1 360 h-1
|
AC-15: Ue 230 V AC, Ie 4A / DC-13: Ue24 V DC, Ie 4 A
|
||
3600 h-1
|
AC-15: Ue 230 V AC, Ie 3 A / DC-13: Ue 24 V DC, Ie 2,5 A
|
||
Short-circuit protection, max. fuse insert
|
6 A class gG or circuit breaker with trigger characteristic B or C
|
||
Mechanical life
|
10x106 switching cycles
|
||
General data
|
|||
Creepage distances and clearances between the circuits
|
according EN 60664-1
|
||
Rated impulse voltage
|
4kV
|
||
Overvoltage category
|
III
|
||
Degree of pollution of the device: inside / outside
|
2/3
|
||
Rated voltage
|
AC 300 V
|
||
Test voltage Uaff 50 Hz
|
2kV
|
||
Protection degree according to DIN EN 60529
(housing / terminals)
|
IP40/IP20
|
||
Ambient temperature / storage temperature
|
-25-+55°C/-25-+75°C
|
||
Dimension diagram |
K 4-1 (screw terminals / K 4-2 (pluggable terminals
|
||
Wire ranges fine-stranded / solid or fine-stranded with ferrules
|
2 x 0,14 - 0,75 mm2/1 x 0,14-2,5 mm2
1 x 0,25 - 2,5 mm2/2 x 0,25 - 0,5 mm2 |
||
Permissible tightening torque
|
0,5 - 0,6 Nm
AWG 18-16 tylko przewody Cu |
||
Weight
|
0.21 kg (DC device) / 0.25 kg (AC device)
|
Your review appreciation cannot be sent
Report comment
Report sent
Your report cannot be sent
Write your review
Review sent
Your review cannot be sent