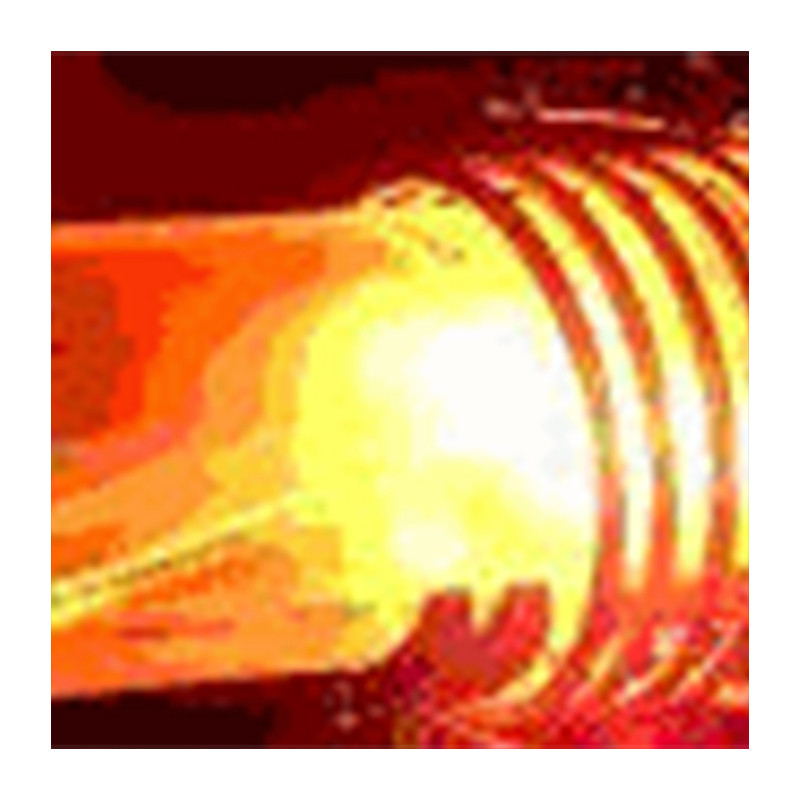
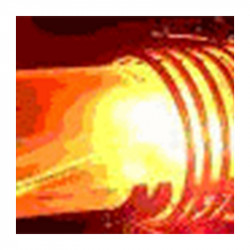
Category
Photos are for informational purposes only. View product specification
please use latin characters
Although induction heating is normally used with metals or other conductive materials, plastics and other non-conductive materials can often be heated very effectively by using a conductive metal susceptora material which is heated as a result of its presence in the induction field, then passes its heat to the workpiece. The susceptor is used to transfer heat to the target part through conduction or radiation.
Graphite is frequently used as a susceptor because it offers machinability, high resistivity (ideal for induction), and a temperature range up to 3000°C (5430°F). Susceptors can also be made from Molybdenum, Silicon Carbide, Stainless Steel, Niobium, Aluminum, and other conductive materials. The susceptor can be made in the form of a crucible, disk, tube, a layer in the material, or whatever form best suites the application. Some example applications include:
Modern induction heating provides reliable, repeatable, non-contact and energy-efficient heat in a minimal amount of time. Solid state systems are capable of heating very small areas within precise production tolerances, without disturbing individual metallurgical characteristics.
When heating a susceptor, solid state RF induction power supplies provide accuracy and speed. During heating, temperature ramping can be controlled by using optical pyrometers or thermocouples to form a closed loop system. Uniform surface temperatures can be achieved with careful coil design.
Typical RF power supplies for susceptor heating range from 1 to 20kW, depending on the parts and application requirements.
Are you interested in this product? Do you need additional information or individual pricing?
Although induction heating is normally used with metals or other conductive materials, plastics and other non-conductive materials can often be heated very effectively by using a conductive metal susceptora material which is heated as a result of its presence in the induction field, then passes its heat to the workpiece. The susceptor is used to transfer heat to the target part through conduction or radiation.
Graphite is frequently used as a susceptor because it offers machinability, high resistivity (ideal for induction), and a temperature range up to 3000°C (5430°F). Susceptors can also be made from Molybdenum, Silicon Carbide, Stainless Steel, Niobium, Aluminum, and other conductive materials. The susceptor can be made in the form of a crucible, disk, tube, a layer in the material, or whatever form best suites the application. Some example applications include:
Modern induction heating provides reliable, repeatable, non-contact and energy-efficient heat in a minimal amount of time. Solid state systems are capable of heating very small areas within precise production tolerances, without disturbing individual metallurgical characteristics.
When heating a susceptor, solid state RF induction power supplies provide accuracy and speed. During heating, temperature ramping can be controlled by using optical pyrometers or thermocouples to form a closed loop system. Uniform surface temperatures can be achieved with careful coil design.
Typical RF power supplies for susceptor heating range from 1 to 20kW, depending on the parts and application requirements.
Your review appreciation cannot be sent
Report comment
Report sent
Your report cannot be sent
Write your review
Review sent
Your review cannot be sent