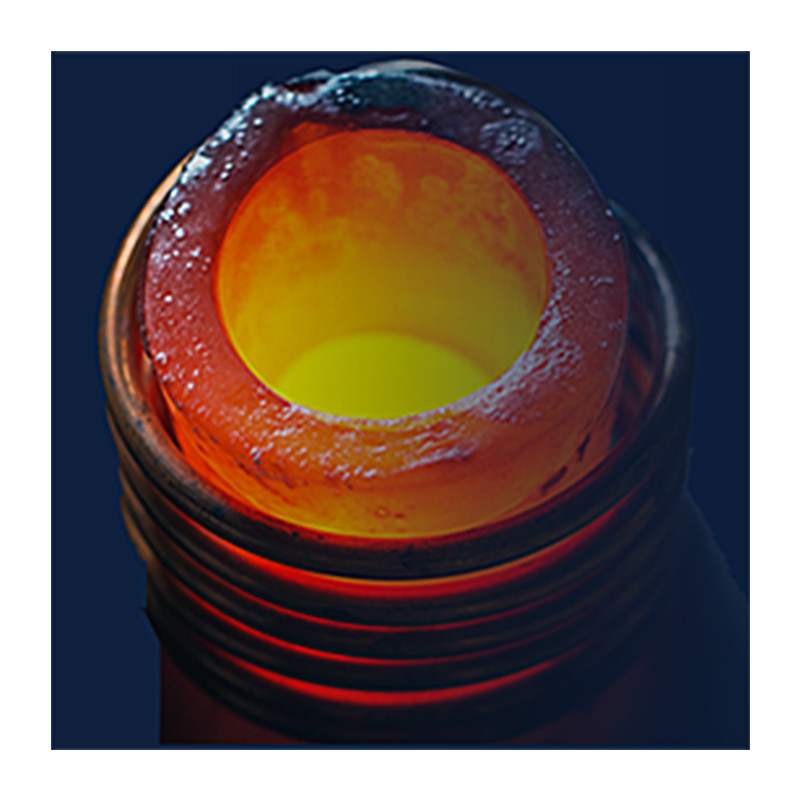
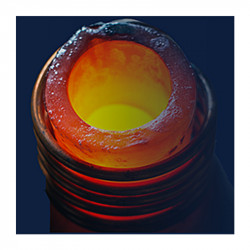
Debes estar logueado
Category
Las fotos son solo para fines informativos. Ver especificaciones de producto
please use latin characters
Melting metals with solid state RF induction heating is usually accomplished by heating the metal in a crucible made from a non-conductive refractory material. The charge of metal within the crucible is melted down to liquid form.
This process is commonly used to produce high quality steels and nonferrous alloys for casting operations. The liquified metal is poured into a cavity having the desired shape. The metal solidifies with a minimum of shrinkage, after which the mold is removed to reveal a finished, machinable product
Modern induction heating provides reliable, repeatable, non-contact and energy-efficient heat in a minimal amount of time. Induction produces circular eddy currents within the molten mass, creating a stirring action which results in a very uniform product. Induction heating provides fast, controllable temperature ramp, allowing for consistent quality results. Both ferrous and non-ferrous alloys can be melted in induction furnaces. The flexibility and cleanliness of induction melting cannot be duplicated by conventional steel mill and foundry methods.
Typical induction furnaces for melting range from 1 to 20kW, depending on the metal and application requirements
¿Estás interesado en este producto? ¿Necesita información adicional o precios individuales?
Usted debe estar conectado
Melting metals with solid state RF induction heating is usually accomplished by heating the metal in a crucible made from a non-conductive refractory material. The charge of metal within the crucible is melted down to liquid form.
This process is commonly used to produce high quality steels and nonferrous alloys for casting operations. The liquified metal is poured into a cavity having the desired shape. The metal solidifies with a minimum of shrinkage, after which the mold is removed to reveal a finished, machinable product
Modern induction heating provides reliable, repeatable, non-contact and energy-efficient heat in a minimal amount of time. Induction produces circular eddy currents within the molten mass, creating a stirring action which results in a very uniform product. Induction heating provides fast, controllable temperature ramp, allowing for consistent quality results. Both ferrous and non-ferrous alloys can be melted in induction furnaces. The flexibility and cleanliness of induction melting cannot be duplicated by conventional steel mill and foundry methods.
Typical induction furnaces for melting range from 1 to 20kW, depending on the metal and application requirements
Su agradecimiento a la reseña no pudo ser enviado
Reportar comentario
Reporte enviado
Su reporte no pudo ser enviado
Escriba su propia reseña
Reseña enviada
Su reseña no pudo ser enviada