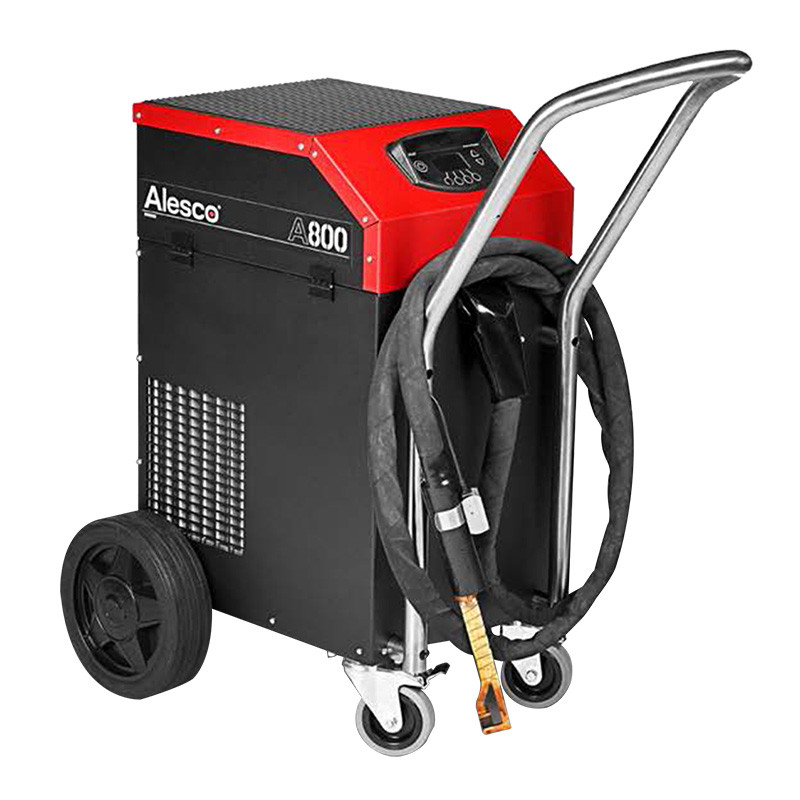
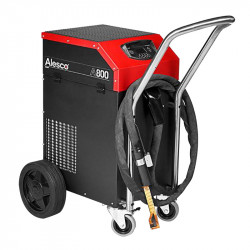
Debes estar logueado
Category
Las fotos son solo para fines informativos. Ver especificaciones de producto
please use latin characters
DACPOL company offers a range of induction heaters are designed to support the work of the workshop.
Induction heating is a contact-free method that can be used to heat metals. The induction heater creates an alternating magnetic field that generates eddy currents inside the material. It is these eddy currents that generate the heat. In our machines, the alternating current is “pumped” backwards and forwards in the inductor at between 15-20 kHz.
Three factors that influence heating
With induction, there is much talk about the induction heater’s power. But the power is only one of three important parameters. The other two are the surface across which the power is produced and the frequency. The power per unit area is a very important ratio where the inductor itself is completely crucial for achieving a high power density. In this area, Alesco are world leaders.
The last factor, the frequency, is always a compromise. In principle, the lower the frequency, the deeper the magnetic penetration into the material. In other words, at low frequencies the heat is generated deeper inside the material. So induction heaters with higher frequencies heat up the surface more. This can be seen with the naked eye, but since it is only surface heat one sees, it can be difficult to judge the depth of heat penetration. Alesco’s 3-phase models work in the frequency range 15-18 kHz.
The art of undoing a screwed joint
In a vehicle workshop, induction heaters are used for straightening frames and axles and even for releasing screwed joints, which is actually the greatest area of use. A modern screwed joint in today’s vehicles can be difficult to undo. It is a precision part where the tolerances in the threads are minimal and often comprise several different qualities of metal. In addition, it often consists of a mix of different materials such as rubber, different types of adhesives, etc. Many screws fitted to vehicles are pre-torqued by the manufacturer. In other words, there are both pre-torqued and non pre-torqued joints in a vehicle. The designer of the joint has determined which of them are placed where. In addition to this, over time different types of corrosion occur between the parts of the joint. All these things together influence the demand for torque and even the ability to separate the joint at all. An induction heater simplifies this situation considerably.
Induction heating is fast and gentle
Releasing a joint with induction differs somewhat from using an open flame. With an open flame, one heats the outer surface of the joint causing it to expand. With induction, an immediate difference in temperature is created between the various parts of the joint, causing movement and "breaking" the joint. This means that one can just heat up the screw to achieve a "movement" which in turn reduces the torque necessary to release the joint.
There are many other different areas of use for an induction heater. One can for example release glued parts such as windows, decals, rubber strips, etc. Gluing is something that occurs more and more often in modern vehicles, which creates even more future areas of use for induction heaters.
Induction heaters type A 80
Mains supply | 208-240 V/50/60 Hz 4-16 A |
Enclosure | IP 21 |
Working frequency | 17-40 kHz |
Output Power | 3,7 kW |
Power control | 5 stopni |
Weight | 8kg z pełnym zbiornikiem |
Size | (LxBxH) 450 x 220 x 250 mm |
Induction heaters type A 800
Mains supply | 3x400 + PE V/50/60 Hz 16 A |
Enclosure | IP 21 |
Working frequency | 16-18 kHz |
Output Power | 10,0 kW |
Microprocessor power control | 5-100 % |
Weight | 78 kg |
Size | (LxBxH) 450x500x800 mm |
Induction heaters type A 1200
Mains supply | 3x400 + PE V/50/60 Hz 16 A |
Enclosure | IP 21 |
Working frequency | 16-18 kHz |
Output Power | 12,0 kW |
Microprocessor power control | 5-100 % |
Weight | 153 kg |
Size | (LxBxH) 650x600x900 mm |
Induction heaters type 4000
Mains supply | 3x400 + PE V/50/60 Hz 32 A |
Enclosure | IP 21 |
Working frequency | 16-18 kHz |
Output Power | 18,0 kW |
Microprocessor power control | 5-100 % |
Weight | 230 kg |
Size | (LxBxH) 870x700x1000 mm |
Typical applications
![]() |
![]() |
![]() |
¿Estás interesado en este producto? ¿Necesita información adicional o precios individuales?
Usted debe estar conectado
DACPOL company offers a range of induction heaters are designed to support the work of the workshop.
Induction heating is a contact-free method that can be used to heat metals. The induction heater creates an alternating magnetic field that generates eddy currents inside the material. It is these eddy currents that generate the heat. In our machines, the alternating current is “pumped” backwards and forwards in the inductor at between 15-20 kHz.
Three factors that influence heating
With induction, there is much talk about the induction heater’s power. But the power is only one of three important parameters. The other two are the surface across which the power is produced and the frequency. The power per unit area is a very important ratio where the inductor itself is completely crucial for achieving a high power density. In this area, Alesco are world leaders.
The last factor, the frequency, is always a compromise. In principle, the lower the frequency, the deeper the magnetic penetration into the material. In other words, at low frequencies the heat is generated deeper inside the material. So induction heaters with higher frequencies heat up the surface more. This can be seen with the naked eye, but since it is only surface heat one sees, it can be difficult to judge the depth of heat penetration. Alesco’s 3-phase models work in the frequency range 15-18 kHz.
The art of undoing a screwed joint
In a vehicle workshop, induction heaters are used for straightening frames and axles and even for releasing screwed joints, which is actually the greatest area of use. A modern screwed joint in today’s vehicles can be difficult to undo. It is a precision part where the tolerances in the threads are minimal and often comprise several different qualities of metal. In addition, it often consists of a mix of different materials such as rubber, different types of adhesives, etc. Many screws fitted to vehicles are pre-torqued by the manufacturer. In other words, there are both pre-torqued and non pre-torqued joints in a vehicle. The designer of the joint has determined which of them are placed where. In addition to this, over time different types of corrosion occur between the parts of the joint. All these things together influence the demand for torque and even the ability to separate the joint at all. An induction heater simplifies this situation considerably.
Induction heating is fast and gentle
Releasing a joint with induction differs somewhat from using an open flame. With an open flame, one heats the outer surface of the joint causing it to expand. With induction, an immediate difference in temperature is created between the various parts of the joint, causing movement and "breaking" the joint. This means that one can just heat up the screw to achieve a "movement" which in turn reduces the torque necessary to release the joint.
There are many other different areas of use for an induction heater. One can for example release glued parts such as windows, decals, rubber strips, etc. Gluing is something that occurs more and more often in modern vehicles, which creates even more future areas of use for induction heaters.
Induction heaters type A 80
Mains supply | 208-240 V/50/60 Hz 4-16 A |
Enclosure | IP 21 |
Working frequency | 17-40 kHz |
Output Power | 3,7 kW |
Power control | 5 stopni |
Weight | 8kg z pełnym zbiornikiem |
Size | (LxBxH) 450 x 220 x 250 mm |
Induction heaters type A 800
Mains supply | 3x400 + PE V/50/60 Hz 16 A |
Enclosure | IP 21 |
Working frequency | 16-18 kHz |
Output Power | 10,0 kW |
Microprocessor power control | 5-100 % |
Weight | 78 kg |
Size | (LxBxH) 450x500x800 mm |
Induction heaters type A 1200
Mains supply | 3x400 + PE V/50/60 Hz 16 A |
Enclosure | IP 21 |
Working frequency | 16-18 kHz |
Output Power | 12,0 kW |
Microprocessor power control | 5-100 % |
Weight | 153 kg |
Size | (LxBxH) 650x600x900 mm |
Induction heaters type 4000
Mains supply | 3x400 + PE V/50/60 Hz 32 A |
Enclosure | IP 21 |
Working frequency | 16-18 kHz |
Output Power | 18,0 kW |
Microprocessor power control | 5-100 % |
Weight | 230 kg |
Size | (LxBxH) 870x700x1000 mm |
Typical applications
![]() |
![]() |
![]() |
Su agradecimiento a la reseña no pudo ser enviado
Reportar comentario
Reporte enviado
Su reporte no pudo ser enviado
Escriba su propia reseña
Reseña enviada
Su reseña no pudo ser enviada