Debes estar logueado
-
moreX
-
Componentes
-
-
Category
-
Semiconductores
- Diodos
- Tiristores
-
Módulos con aislamiento eléctrico
- Módulos con aislamiento eléctrico | VISHAY (IR)
- Módulos con aislamiento eléctrico | INFINEON (EUPEC)
- Módulos con aislamiento eléctrico | Semikron
- Módulos con aislamiento eléctrico | POWEREX
- Módulos con aislamiento eléctrico | IXYS
- Módulos con aislamiento eléctrico | POSEICO
- Módulos con aislamiento eléctrico | ABB
- Módulos con aislamiento eléctrico | TECHSEM
- Go to the subcategory
- Rectificadores de puente
-
Transistores
- Transistores | GeneSiC
- Módulos SiC MOSFET | Mitsubishi
- Módulos SiC MOSFET | STARPOWER
- Módulos ABB SiC MOSFET
- Módulos IGBT | MITSUBISHI
- Módulos de transistores | MITSUBISHI
- Módulos MOSFET | MITSUBISHI
- Módulos de transistores | ABB
- Módulos IGBT | POWEREX
- Módulos IGBT | INFINEON (EUPEC)
- Elementos semiconductores de carburo de silicio (SiC)
- Go to the subcategory
- Controladores de puerta
- Bloques de energía
- Go to the subcategory
- Convertidores de corriente y tensión LEM
-
Componentes pasivos (condensadores, resistencias, fusibles, filtros)
- Resistencias
-
Fusibles
- Fusibles miniatura para circuitos electrónicos, serie ABC y AGC
- Fusibles tubulares de acción rápida
- Eslabones fusibles de retardo de tiempo con características GL / GG y AM
- Eslabones fusibles ultrarrápidos
- Fusibles de acción rápida (estándar británico y estadounidense)
- Fusibles de acción rápida (estándar europeo)
- Fusibles de tracción
- Eslabones fusibles de alto voltaje
- Go to the subcategory
-
Condensadores
- Condensadores de motor
- Condensadores electrolíticos
- Condensadores de película
- Condensadores de potencia
- Condensadores para circuitos de CC
- Condensadores de corrección del factor de potencia
- Condensadores de alto voltaje
- Condensadores de calentamiento por inducción
- Condensadores de almacenamiento de energía y pulsos
- Condensadores de ENLACE CC
- Condensadores para circuitos AC/DC
- Go to the subcategory
- Filtros EMI
- Supercondensadores
-
Protección contra sobretensiones
- Protección contra sobretensiones para aplicaciones coaxiales
- Protección contra sobretensiones para sistemas de videovigilancia
- Protección contra sobretensiones para cableado de potencia
- Pararrayos para LED
- Descargadores de sobretensiones para energía fotovoltaica
- Protección del sistema de pesaje
- Protección contra sobretensiones para Fieldbus
- Go to the subcategory
- Filtros para detección de emisiones TEMPEST
- Go to the subcategory
-
Relés y contactores
- Teoría de relés y contactores
- Relés semiconductores de CA trifásicos
- Relés semiconductores de CA trifásicos
- Reguladores, controles y accesorios
- Arranques suaves y contactores de inversión
- Relés electromecánicos
- Contactores
- Interruptores giratorios
-
Relés semiconductores de CA monofásicos
- Relés semiconductores CA monofásicos, serie 1 | D2425 | D2450
- Relés semiconductores CA monofásicos, series CWA y CWD
- Relés semiconductores CA monofásicos de las series CMRA y CMRD
- Relés semiconductores de CA monofásicos, serie PS
- Relés semiconductores de CA dobles y cuádruples, serie D24 D, TD24 Q, H12D48 D
- Relés de estado sólido monofásicos, serie gn
- Relés semiconductores de ca monofásicos, serie ckr
- Relés AC monofásicos SERIE ERDA Y ERAA para carril DIN
- Relés AC monofásicos para corriente 150A
- Relés dobles de estado sólido integrados con disipador de calor para carril DIN
- Go to the subcategory
- Relés semiconductores CA monofásicos para PCB
- Relés de interfaz
- Go to the subcategory
- Núcleos y otros componentes inductivos
- Radiadores, varistores, protecciones térmicas
- Aficionados
- Aire Acondicionado, Accesorios para Armarios Eléctricos, Neveras
-
Baterías, cargadores, fuentes de alimentación de búfer e inversores
- Baterías, cargadores - descripción teórica
- Baterías de iones de litio. Baterías personalizadas. Sistema de gestión de batería (BMS)
- Pilas
- Cargadores de baterías y accesorios
- Fuente de alimentación de respaldo de UPS y fuentes de alimentación de búfer
- Convertidores y accesorios para fotovoltaica
- Almacen de energia
- Celdas de combustible
- Baterías de iones de litio
- Go to the subcategory
- Automaticas
-
Cables, alambres Litz, conductos, conexiones flexibles
- alambres
- cables Litz
-
Cables para aplicaciones especiales
- Los cables de extensión y compensación
- Cables para termopares
- Los cables de conexión a PT czyjnków
- Multicore cables temp. -60 ° C a + 1400 ° C
- cables de media tensión SILICOUL
- ignición alambres
- Los cables calefactores
- temp núcleo único. -60 ° C a + 450 ° C
- conductores de trenes
- El calentamiento de los cables en el Ex
- Go to the subcategory
- camisas
-
trenzas
- trenzas planas
- trenzas ronda
- trenza muy flexible - plana
- trenza muy flexible - Ronda
- Copper cilíndrico trenzado
- Copper protector de la trenza y cilíndrica
- cintas de conexión flexibles
- Trenzas cilíndrico galvanizado y acero inoxidable
- Aislamiento de PVC trenzas de cobre - Temperatura 85 ° C
- aluminio trenzado plano
- Kit de conexión - trenzas y tubos
- Go to the subcategory
- Accesorios para la tracción
- Terminales de cable
- barras flexibles aisladas
- carril flexible multicapa
- sistemas de gestión de cables
- Go to the subcategory
- View all categories
-
Semiconductores
-
-
- Suppliers
-
Applications
- Accionamientos de CA y CC (inversores)
- Automatización HVAC
- Automatización industrial
- Automatización industrial
- Calentamiento por inducción
- Componentes para atmósferas potencialmente explosivas (EX)
- Dispositivos de protección industrial
- Energy bank
- Equipos para Armarios de Distribución, Control y Telecomunicaciones
- Fuentes de alimentación (UPS) y sistemas rectificadores
- Impresión
- Máquinas de soldar y máquinas de soldar
- Máquinas herramientas CNC
- Máquinas para secar y procesar madera
- Máquinas para termoformado de plásticos
- Medición y regulación de temperatura
- Medición y regulación de temperatura
- Minería, metalurgia y fundación
- Motores y transformadores
- Tracción de tranvía y ferrocarril
-
Instalación
-
-
Inductores
-
-
Dispositivos de inducción
-
-
https://www.dacpol.eu/pl/naprawy-i-modernizacje
-
-
Servicio
-
- Contact
- Zobacz wszystkie kategorie
Flow transducers
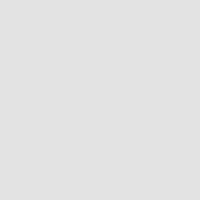
Recent advances in flow detection have resulted in more accurate, durable and cost-effective meters. It is becoming increasingly important to be able to connect flow meters to a computer for instant flow readings, remote flow control or to enable unattended process operation.
To meet these demands, new types of flow transducers are being introduced and older designs are being improved and upgraded.
The primary factors to consider when selecting a flow transducer are:
- type of medium e.g. water, air;
- medium flow velocity range;
- medium temperature and pressure;
- accuracy;
- measuring range;
- output value type e.g. voltage, current;
- ease of installation and maintenance requirements.
Let's take a closer look at the principle of such transducers and what types we can find in the industrial sector.
Working principle of flow transducers
Flowmeters are used to measure the velocity of air or liquid flow. Flow meter sensors work in different ways, but have the same end goal: to provide the most accurate and repeatable flow measurement for a specific application, whether for process control, general scientific research or semiconductor processing.
The most common solutions can calculate the flow level or its quantity based on the cross-sectional area of the pipe. Then, the analytical components of the transducers convert this value into an appropriate output signal.
You can find transducers based on Faraday's law of induction. A medium flows through a pipe in a certain magnetic field, producing a voltage proportional to the amount of that medium or its velocity.
Another type are transducers, which through the flowing medium, count the resulting turbulence depending on the speed of the medium. If we know the cross-section of the pipe, we can determine the flow rate.
Other solutions use ultrasound reflections and measure the transit time of the signals between the ultrasound transducers. By calculating the time difference between the reflections received by the transducers, the flow rate can be determined and converted to an output value accordingly.
There are also sensors with spring-loaded pistons. Through the flowing medium, a piston located in a valve of the transducer housing exerts pressure on a spring. The position of the spring is monitored by special sensors, usually magnetic, which send the corresponding analogue signals to the evaluation units.
Applications for flow transducers in industry
Flow transducers are used in almost all areas of process and engineering where liquids or gases are used, e.g. to provide equipment and machinery with coolant and lubricants, in hall and building ventilation systems, in processing etc. If the flow is not correct, significant damage and downtime in the industry can result. Inaccurate flow measurements or failure to measure can cause serious and irreversible consequences. In modern installations, electronic monitoring systems are used to prevent such situations. Below are some of the many applications of flow sensors:
- controlling irrigation and water consumption in the agricultural industry;
- maintaining energy efficiency and usability of HVAC systems;
- wastewater treatment facilities;
- monitoring product flow in the food, pharmaceutical and other industries;
- monitoring pump operation, balancing system flow;
- diesel and other oil flow monitoring, cooling water flow in power industry;
- monitoring of water, fuel and lubricant consumption and related products in the form of sludge and slurry in the mining industry.
Choosing the right solution for your industrial process
Choosing the best flow transducer for industrial systems is not as complicated as it sounds. The most important variables in this choice are pipe size and the type of fluid used in the cooling system. There are many flow monitoring technologies, such as the models described in this article and each type of device can be purchased for different pipe sizes.
For a basic water-cooling system, a simple impeller flowmeter is usually sufficient. These are economical and easy to install in almost any system, and they are compatible with many types of pipe. The unit is simply installed so that the impeller is in line with the direction of water flow. Many impeller-type meters are available with temperature probes that plug directly into the meter to calculate overall efficiency.
Ultrasonic meters are useful in applications where liquids other than water are present, as some chemicals can damage impellers. Ultrasonic meters can also measure flow in both directions.
Electromagnetic flowmeters measure flow in conductive fluids. Electromagnetic flow meters are useful for slurries and other liquids containing solids that could contaminate the impeller or interfere with the ultrasonic transducer.
In summary, improving the efficiency of industrial systems has a direct impact on a facility's bottom line. Flow monitoring is a critical variable in efficiency calculations. To best manage a facility's energy consumption, more information is always better so invest in durable, high-quality flow measurement equipment.
Producto relacionado
Publicaciones relacionadas
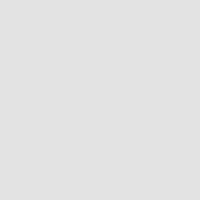
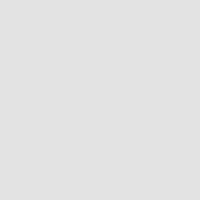
Deja un comentario