Vous devez être connecté
-
revenirX
-
Composants
-
-
Category
-
Semi-conducteurs
- La diode
- Les thyristors
- Modules de puissance isolés
- Ponts redresseurs
-
Transistors
- Transistors | GeneSiC
- Modules MOSFET SiC | Mitsubishi
- Modules MOSFET SiC | STARPOWER
- Modules MOSFET SiC ABB
- Modules IGBT | MITSUBISHI
- Modules de transistors | MITSUBISHI
- Modules MOSFET | MITSUBISHI
- Modules de transistors | ABB
- Modules IGBT | POWEREX
- Modules IGBT | INFINEON (EUPEC)
- Composants semiconducteurs en carbure de silicium
- Aller à la sous-catégorie
- Circuits de commande
- Blocs de puissance
- Aller à la sous-catégorie
- Transducteurs électriques
-
Composants passifs (condensateurs, résistances, fusibles, filtres)
- Résistances
-
Fusibles
- Fusibles miniatures pour c.imp. série ABC et AGC
- Fusible rapides tubulaires
- Cartouches de courbe GL/GG et AM
- Cartouches ultrarapides
- Fusibles à action rapide (norme britannique et américaine)
- Fusibles à action rapide (norme européenne)
- Fusibles de traction
- Cartouche de haute tension
- Aller à la sous-catégorie
-
Condensateurs
- Condensateurs pour moteurs
- Condensateurs électrolitiques
- Condensateurs de type snubbers
- Condensateurs de puissance
- Condensateurs pour circuits continus
- Condensateurs de compensation de puissance
- Condensateurs de haute tension
- Condensateurs pour chauffage par induction
- Condensateurs pour impulsions
- Condensateurs DC LINK
- Condensateurs pour circuits AC/DC
- Aller à la sous-catégorie
- Filtres anti-interférences
- Supercondensateurs
-
Protection contre les surtensions
- Protection contre les surtensions pour les applications coaxiales
- Protection contre les surtensions pour les systèmes de vidéosurveillance
- Parafoudres de ligne électrique
- Protection contre surtensions pour LED
- Parafoudres pour le photovoltaïque
- Protection du système de pesage
- Protection contre les surtensions pour bus de terrain
- Aller à la sous-catégorie
- Filtres de détection des émissions TEMPEST
- Aller à la sous-catégorie
-
Relais et contacteurs
- Théorie relais et contacteurs
- Relais statiques triphasés
- Relais statiques CC
- Régulateurs, circuits de commande et accessoires
- Démarrages progressifs et contacteurs inverseurs
- Relais electromécaniques
- Contacteurs
- Commutateurs rotatifs
-
Relais statiques monophasés
- Relais semi-conducteurs AC monophasés, série 1 | D2425 | D2450
- Relais à semi-conducteurs CA monophasés, séries CWA et CWD
- Relais à semi-conducteurs CA monophasés des séries CMRA et CMRD
- Relais à semi-conducteurs CA monophasés, série PS
- Relais semi-conducteurs AC double et quadruple, série D24 D, TD24 Q, H12D48 D
- Relais statiques monophasés, série GN
- Relais à semi-conducteurs CA monophasés, série CKR
- Relais AC monophasés SÉRIES ERDA ET ERAA pour rail DIN
- Relais CA monophasés pour courant 150A
- Relais à semi-conducteurs doubles intégrés à un dissipateur thermique pour un rail DIN
- Aller à la sous-catégorie
- Relais statiques monophasé pour c.imp.
- Relais d'interface
- Aller à la sous-catégorie
- Composants inductifs
- Radiateurs, varistances, protections thermiques
- Ventilateurs
- Climatiseurs et accessoires d'armoires électriques
-
Batteries, chargeurs, blocs d'alimentation tampon et onduleurs
- Batteries et Chargeurs - théorie
- Batteries Li-ion et non-standards. Systèmes de gestion des batteries (BMS)
- Batteries
- Chargeurs de batteries et accessoires
- Alimentation de secours UPS et alimentation tampon
- Convertisseurs de tension et accessoires pour photovoltaïque
- Stockage d'Energie
- Réservoirs de carburant
- Batteries lithium-ion
- Aller à la sous-catégorie
-
Automatique industrielle
- Futaba Drone Parts
- Interrupteurs de fin de course, micro-rupteurs
- Capteurs et convertisseurs
- Pyromètres
- Compteurs, Relais temporisés, Indicateurs de tableau
- Appareils industriels de protection
- Signalisation lumineuse et sonore
- Caméra thermique
- Afficheurs à LED
- Boutons et commutateurs
- Aller à la sous-catégorie
-
Câbles et chemins de câbles
- Fils
- Fils de Litz
- Câbles pour les applications spéciales
- Gaines
-
Tresses
- Tresses plates
- Tresses rondes
- Tresses très souples - plates
- Tresses très souples - rondes
- Tresses cuivre cylindriques
- Tresses cuivre cylindriques et protection
- Bandes de mise à la terre souples
- Tresses en acier zingué et inox
- Tresses isolantes en PVC - temp. 85°C
- Tresses plates en aluminium
- Kit de liaison - tresses et gaines
- Aller à la sous-catégorie
- Equipement pour la traction
- Cosses
- Barres flexible isolées
- Barre flexibles multicouches
- Systèmes de traçage des câbles
- Aller à la sous-catégorie
- Voir toutes les catégories
-
Semi-conducteurs
-
-
- Fournisseurs
-
Applications
- Alimentations (UPS) et systèmes de redressement
- Automatisation HVAC
- Automatisation industrielle
- Chauffage par induction
- Composants pour atmosphères potentiellement explosives (EX)
- Dispositifs de protection industriels
- Énergétique
- Energy bank
- Équipements pour armoires de distribution, de contrôle et de télécommunications
- Impression
- Machines à souder et machines à souder
- Machines de séchage et de traitement du bois
- Machines pour le thermoformage des plastiques
- Machines-outils CNC
- Mesure et régulation de la température
- Mesure et régulation de la température
- Mines, métallurgie et fondation
- Moteurs et transformateurs
- Traction de tram et de chemin de fer
- Variateurs CA et CC (onduleurs)
-
Installation
-
-
Inducteurs
-
-
Appareils à induction
-
-
https://www.dacpol.eu/pl/naprawy-i-modernizacje
-
-
Service
-
- Contact
- Zobacz wszystkie kategorie
Maintenance and safety
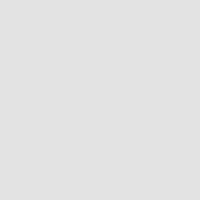
Regular conduction of maintenance and providing safety in the company or production workshop is a key requirement in maintaining proper work of the machines and enterprise.
When and why should you conduct maintenance work?
Lack of maintenance and conforming to safety norms leads to serious and sometimes fatal accidents at work or causes irreversible health issues.
Maintenance is not a single task to complete, but a whole process of safe exploitation of devices, which can be divided into a few stages:
- Planning - conducting risk evaluation and deciding on extent of work and needed resources e.g. qualifications and number of employees, required tools.
- Securing and cleaning the maintenance workplace - e.g. turning off the power and blocking moving parts, providing ventilation, access and evacuation roads.
- Maintenance - revitalization process, mending, servicing and securing process.
- Work evaluation - checking the results, machine safety evaluation and possibility for turning them on. Insulation elements, tools and waste created during maintenance should also be removed.
- Documentation - collecting and achieving documents concerning realized tasks and machine’s state.
Types of maintenance
In recent years technological development happens faster than ever in the world’s history, causing rapid changes in all areas of our lives. Development of IT constantly changes and influences functioning of maintenance processes - innovations in sensors and wide spreading systems based on VR/AR or cloud simplify data collection and planning maintenance processes. We distinguish types of maintenance such as:
Corrective maintenance - intended for indicating and servicing the defects, so the damaged device can be brought back to operational state within indicated norms for its normal functioning.
Preventive maintenance - routine and planned service and check up actions, providing continuous work of machines, preventing unplanned outages and failure costs.
Predictive maintenance - monitors the state and productivity of the devices during their normal functioning process and allows for setting up servicing schedule. Thanks to the development of IoT (Internet of things) eliminating pointless service interventions and outages becomes easier and more common.
Maintenance during outage - automatic exchange with a set frequency, within a period of time shorter than an average time of the machine’s proper work.
Periodical maintenance - conducted based on a calendar schedule, It is a key process to provide long-time functioning of the device and limiting possibility of breakdowns. Periodical maintenance actions include cleaning, servicing and general inspection of the machine.
Safety in production company
Providing safety in a workplace is one of the most important requirements every employer has to fulfill. Proper protection and safety of devices, company and employees can be provided by i.e. safety switches, warning signs or special protective clothing.
Accidents can occur during:
- maintenance e.g. accidentally turning on the machine,
- work in environment with dangerous substances,
- work in particular body positions,
- lack f maintenance - not fixed damages of the devices or environment in the workshop,
- improper maintenance e.g. using wrong parts.
What is the EHSR directive, and how is it beneficial to conform to it?
Essential Health and Safety Requirement (EHSR) is a directive intended for providing a standard of a minimal level of protection and safety of machines and testing devices (e.g. multimeters, thermovision cameras). ATEX 137 (1999/92/WE) is a legal foundation of this directive, addressing minimal requirements of safety and health protection of employees working in hazardous areas and positions in risk of explosive environments (Ex).
The directive includes conditions such as:
Providing training for the employees by the employer concerning possible risks in explosive areas.
- Owning proper permissions for working in a hazardous area.
- Evaluating and documentation of explosion protection (EPD) made by the employer.
- Coordinating procedures in case of the need to conduct actions in an explosive area.
- Safety measures required for work in hazardous areas
Maintenance work requires numerous defined safety procedures, including using proper personal safety measures and protection equipment. Among the most often used safety tools and solutions we distinguish:
- Personal safety measures - e.g. face shields, limiting the risk of getting infected with airborne diseases;
- Safety switches;
- Safety relays;
- Hoses and safety materials - often used for water cooling of induction furnaces or current connections for arched furnaces e.g. supplied by renowned Lippmann company non-conductive hoses for water cooling, for media transferring, insulation materials for high temperatures.
- High-temperature protection materials - protective shirts (for stable temperature 300°C and temporary up to 500°C), protective materials from laser radiation (e.g. Laservision products: safety glasses for work with lasers, glass windows with mineral screen, enclosures and cabins, covers on plastic and glass filters).
Articles similaires
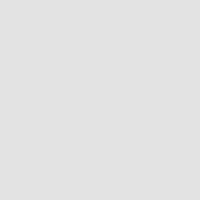
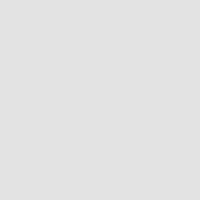
Laissez un commentaire