Vous devez être connecté
-
revenirX
-
Composants
-
-
Category
-
Semi-conducteurs
- La diode
- Les thyristors
- Modules de puissance isolés
- Ponts redresseurs
-
Transistors
- Transistors | GeneSiC
- Modules MOSFET SiC | Mitsubishi
- Modules MOSFET SiC | STARPOWER
- Modules MOSFET SiC ABB
- Modules IGBT | MITSUBISHI
- Modules de transistors | MITSUBISHI
- Modules MOSFET | MITSUBISHI
- Modules de transistors | ABB
- Modules IGBT | POWEREX
- Modules IGBT | INFINEON (EUPEC)
- Composants semiconducteurs en carbure de silicium
- Aller à la sous-catégorie
- Circuits de commande
- Blocs de puissance
- Aller à la sous-catégorie
- Transducteurs électriques
-
Composants passifs (condensateurs, résistances, fusibles, filtres)
- Résistances
-
Fusibles
- Fusibles miniatures pour c.imp. série ABC et AGC
- Fusible rapides tubulaires
- Cartouches de courbe GL/GG et AM
- Cartouches ultrarapides
- Fusibles à action rapide (norme britannique et américaine)
- Fusibles à action rapide (norme européenne)
- Fusibles de traction
- Cartouche de haute tension
- Aller à la sous-catégorie
-
Condensateurs
- Condensateurs pour moteurs
- Condensateurs électrolitiques
- Condensateurs de type snubbers
- Condensateurs de puissance
- Condensateurs pour circuits continus
- Condensateurs de compensation de puissance
- Condensateurs de haute tension
- Condensateurs pour chauffage par induction
- Condensateurs pour impulsions
- Condensateurs DC LINK
- Condensateurs pour circuits AC/DC
- Aller à la sous-catégorie
- Filtres anti-interférences
- Supercondensateurs
-
Protection contre les surtensions
- Protection contre les surtensions pour les applications coaxiales
- Protection contre les surtensions pour les systèmes de vidéosurveillance
- Parafoudres de ligne électrique
- Protection contre surtensions pour LED
- Parafoudres pour le photovoltaïque
- Protection du système de pesage
- Protection contre les surtensions pour bus de terrain
- Aller à la sous-catégorie
- Filtres de détection des émissions TEMPEST
- Aller à la sous-catégorie
-
Relais et contacteurs
- Théorie relais et contacteurs
- Relais statiques triphasés
- Relais statiques CC
- Régulateurs, circuits de commande et accessoires
- Démarrages progressifs et contacteurs inverseurs
- Relais electromécaniques
- Contacteurs
- Commutateurs rotatifs
-
Relais statiques monophasés
- Relais semi-conducteurs AC monophasés, série 1 | D2425 | D2450
- Relais à semi-conducteurs CA monophasés, séries CWA et CWD
- Relais à semi-conducteurs CA monophasés des séries CMRA et CMRD
- Relais à semi-conducteurs CA monophasés, série PS
- Relais semi-conducteurs AC double et quadruple, série D24 D, TD24 Q, H12D48 D
- Relais statiques monophasés, série GN
- Relais à semi-conducteurs CA monophasés, série CKR
- Relais AC monophasés SÉRIES ERDA ET ERAA pour rail DIN
- Relais CA monophasés pour courant 150A
- Relais à semi-conducteurs doubles intégrés à un dissipateur thermique pour un rail DIN
- Aller à la sous-catégorie
- Relais statiques monophasé pour c.imp.
- Relais d'interface
- Aller à la sous-catégorie
- Composants inductifs
- Radiateurs, varistances, protections thermiques
- Ventilateurs
- Climatiseurs et accessoires d'armoires électriques
-
Batteries, chargeurs, blocs d'alimentation tampon et onduleurs
- Batteries et Chargeurs - théorie
- Batteries Li-ion et non-standards. Systèmes de gestion des batteries (BMS)
- Batteries
- Chargeurs de batteries et accessoires
- Alimentation de secours UPS et alimentation tampon
- Convertisseurs de tension et accessoires pour photovoltaïque
- Stockage d'Energie
- Réservoirs de carburant
- Batteries lithium-ion
- Aller à la sous-catégorie
-
Automatique industrielle
- Futaba Drone Parts
- Interrupteurs de fin de course, micro-rupteurs
- Capteurs et convertisseurs
- Pyromètres
- Compteurs, Relais temporisés, Indicateurs de tableau
- Appareils industriels de protection
- Signalisation lumineuse et sonore
- Caméra thermique
- Afficheurs à LED
- Boutons et commutateurs
- Aller à la sous-catégorie
-
Câbles et chemins de câbles
- Fils
- Fils de Litz
- Câbles pour les applications spéciales
- Gaines
-
Tresses
- Tresses plates
- Tresses rondes
- Tresses très souples - plates
- Tresses très souples - rondes
- Tresses cuivre cylindriques
- Tresses cuivre cylindriques et protection
- Bandes de mise à la terre souples
- Tresses en acier zingué et inox
- Tresses isolantes en PVC - temp. 85°C
- Tresses plates en aluminium
- Kit de liaison - tresses et gaines
- Aller à la sous-catégorie
- Equipement pour la traction
- Cosses
- Barres flexible isolées
- Barre flexibles multicouches
- Systèmes de traçage des câbles
- Aller à la sous-catégorie
- Voir toutes les catégories
-
Semi-conducteurs
-
-
- Fournisseurs
-
Applications
- Alimentations (UPS) et systèmes de redressement
- Automatisation HVAC
- Automatisation industrielle
- Chauffage par induction
- Composants pour atmosphères potentiellement explosives (EX)
- Dispositifs de protection industriels
- Énergétique
- Energy bank
- Équipements pour armoires de distribution, de contrôle et de télécommunications
- Impression
- Machines à souder et machines à souder
- Machines de séchage et de traitement du bois
- Machines pour le thermoformage des plastiques
- Machines-outils CNC
- Mesure et régulation de la température
- Mesure et régulation de la température
- Mines, métallurgie et fondation
- Moteurs et transformateurs
- Traction de tram et de chemin de fer
- Variateurs CA et CC (onduleurs)
-
Installation
-
-
Inducteurs
-
-
Appareils à induction
-
-
https://www.dacpol.eu/pl/naprawy-i-modernizacje
-
-
Service
-
- Contact
- Zobacz wszystkie kategorie
Monitoring the technical condition of industrial machinery
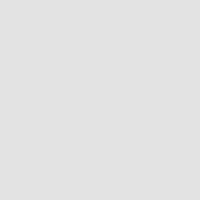
Plants with production lines face many challenges. The fourth industrial revolution will be the automation of production processes. Condition monitoring is the foundation for making better decisions that directly impact the production process, its organization and the entire production line. Machine monitoring is a fundamental element of data-driven manufacturing, which is ideally in line with Industrial Revolution 4.0.
First of all, machines are monitored in order to avoid their breakdown. Comprehensive and continuous observation reduces the possibility of production downtime, which undoubtedly has a negative impact on the production process. Each downtime is linked to financial losses, production stops and dissatisfied customers. To avoid downtime, machines are monitored and wide-scale diagnostics are performed on production lines.
Definition of diagnostics
Diagnostics is the determination of the technical condition of equipment and finding out the sources of failure. The simplest and best known method of diagnosing machines are periodic measurements of vibration levels. Such measurement can be performed by diagnostic equipment such as: simple and portable measuring devices, portable signal analyzers or stationary monitoring equipment, but it can also be on-line systems.
The common element in every technology and every solution is the use of data. Data helps us determine the current state of a machine and how it is performing very accurately, it can also detect future failures and allow us to plan maintenance schedules accordingly to keep downtime as short as possible. All of this makes remote condition monitoring a fundamental part of any plant operation.
Planned and preventive diagnostics
The most crucial word in preventive maintenance is scheduling. An effective maintenance, repair and service schedule is the foundation of any well-run production line. Machines and equipment wear out, and the more often they are maintained, the less likely unplanned downtime will occur. The basis for planning future maintenance operations is to analyze historical data and perform analysis. The strategy for machine operation is selected depending on the criticality group to which the machines belong. For example, maintenance and repairs do not have to be planned, and can be planned and decided on dynamically, based on the current technical condition of the machines. The second strategy is the so-called prediction in maintenance, or the optimal use of equipment. Prediction is the planning and setting of concrete inspection and maintenance dates by identifying the condition equipment will be in in the future.
Diagnostic signals
Safety systems such as signaling towers are used to carry diagnostic signals. When there is a risk of system failure, they inform, warn or alert about the event.A tightly coupled system of optical and/or audible towers with sensors located on the production line is the key to reacting promptly, avoiding or quickly repairing a malfunction.
A tightly coupled system of optical and/or audible towers with sensors located on the production line is the key to reacting promptly, avoiding or quickly repairing a malfunction.
Planned and Preventive Diagnostics, diagnostic signals, production line diagnostics, production line, safety systems, industrial machinery, machinery park,
Articles similaires
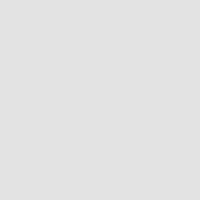
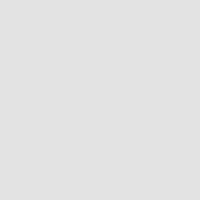
Laissez un commentaire