Vous devez être connecté
-
revenirX
-
Composants
-
-
Category
-
Semi-conducteurs
- La diode
- Les thyristors
- Modules de puissance isolés
- Ponts redresseurs
-
Transistors
- Transistors | GeneSiC
- Modules MOSFET SiC | Mitsubishi
- Modules MOSFET SiC | STARPOWER
- Modules MOSFET SiC ABB
- Modules IGBT | MITSUBISHI
- Modules de transistors | MITSUBISHI
- Modules MOSFET | MITSUBISHI
- Modules de transistors | ABB
- Modules IGBT | POWEREX
- Modules IGBT | INFINEON (EUPEC)
- Composants semiconducteurs en carbure de silicium
- Aller à la sous-catégorie
- Circuits de commande
- Blocs de puissance
- Aller à la sous-catégorie
- Transducteurs électriques
-
Composants passifs (condensateurs, résistances, fusibles, filtres)
- Résistances
-
Fusibles
- Fusibles miniatures pour c.imp. série ABC et AGC
- Fusible rapides tubulaires
- Cartouches de courbe GL/GG et AM
- Cartouches ultrarapides
- Fusibles à action rapide (norme britannique et américaine)
- Fusibles à action rapide (norme européenne)
- Fusibles de traction
- Cartouche de haute tension
- Aller à la sous-catégorie
-
Condensateurs
- Condensateurs pour moteurs
- Condensateurs électrolitiques
- Condensateurs de type snubbers
- Condensateurs de puissance
- Condensateurs pour circuits continus
- Condensateurs de compensation de puissance
- Condensateurs de haute tension
- Condensateurs pour chauffage par induction
- Condensateurs pour impulsions
- Condensateurs DC LINK
- Condensateurs pour circuits AC/DC
- Aller à la sous-catégorie
- Filtres anti-interférences
- Supercondensateurs
-
Protection contre les surtensions
- Protection contre les surtensions pour les applications coaxiales
- Protection contre les surtensions pour les systèmes de vidéosurveillance
- Parafoudres de ligne électrique
- Protection contre surtensions pour LED
- Parafoudres pour le photovoltaïque
- Protection du système de pesage
- Protection contre les surtensions pour bus de terrain
- Aller à la sous-catégorie
- Filtres de détection des émissions TEMPEST
- Aller à la sous-catégorie
-
Relais et contacteurs
- Théorie relais et contacteurs
- Relais statiques triphasés
- Relais statiques CC
- Régulateurs, circuits de commande et accessoires
- Démarrages progressifs et contacteurs inverseurs
- Relais electromécaniques
- Contacteurs
- Commutateurs rotatifs
-
Relais statiques monophasés
- Relais semi-conducteurs AC monophasés, série 1 | D2425 | D2450
- Relais à semi-conducteurs CA monophasés, séries CWA et CWD
- Relais à semi-conducteurs CA monophasés des séries CMRA et CMRD
- Relais à semi-conducteurs CA monophasés, série PS
- Relais semi-conducteurs AC double et quadruple, série D24 D, TD24 Q, H12D48 D
- Relais statiques monophasés, série GN
- Relais à semi-conducteurs CA monophasés, série CKR
- Relais AC monophasés SÉRIES ERDA ET ERAA pour rail DIN
- Relais CA monophasés pour courant 150A
- Relais à semi-conducteurs doubles intégrés à un dissipateur thermique pour un rail DIN
- Aller à la sous-catégorie
- Relais statiques monophasé pour c.imp.
- Relais d'interface
- Aller à la sous-catégorie
- Composants inductifs
- Radiateurs, varistances, protections thermiques
- Ventilateurs
- Climatiseurs et accessoires d'armoires électriques
-
Batteries, chargeurs, blocs d'alimentation tampon et onduleurs
- Batteries et Chargeurs - théorie
- Batteries Li-ion et non-standards. Systèmes de gestion des batteries (BMS)
- Batteries
- Chargeurs de batteries et accessoires
- Alimentation de secours UPS et alimentation tampon
- Convertisseurs de tension et accessoires pour photovoltaïque
- Stockage d'Energie
- Réservoirs de carburant
- Batteries lithium-ion
- Aller à la sous-catégorie
-
Automatique industrielle
- Futaba Drone Parts
- Interrupteurs de fin de course, micro-rupteurs
- Capteurs et convertisseurs
- Pyromètres
- Compteurs, Relais temporisés, Indicateurs de tableau
- Appareils industriels de protection
- Signalisation lumineuse et sonore
- Caméra thermique
- Afficheurs à LED
- Boutons et commutateurs
- Aller à la sous-catégorie
-
Câbles et chemins de câbles
- Fils
- Fils de Litz
- Câbles pour les applications spéciales
- Gaines
-
Tresses
- Tresses plates
- Tresses rondes
- Tresses très souples - plates
- Tresses très souples - rondes
- Tresses cuivre cylindriques
- Tresses cuivre cylindriques et protection
- Bandes de mise à la terre souples
- Tresses en acier zingué et inox
- Tresses isolantes en PVC - temp. 85°C
- Tresses plates en aluminium
- Kit de liaison - tresses et gaines
- Aller à la sous-catégorie
- Equipement pour la traction
- Cosses
- Barres flexible isolées
- Barre flexibles multicouches
- Systèmes de traçage des câbles
- Aller à la sous-catégorie
- Voir toutes les catégories
-
Semi-conducteurs
-
-
- Fournisseurs
-
Applications
- Alimentations (UPS) et systèmes de redressement
- Automatisation HVAC
- Automatisation industrielle
- Chauffage par induction
- Composants pour atmosphères potentiellement explosives (EX)
- Dispositifs de protection industriels
- Énergétique
- Energy bank
- Équipements pour armoires de distribution, de contrôle et de télécommunications
- Impression
- Machines à souder et machines à souder
- Machines de séchage et de traitement du bois
- Machines pour le thermoformage des plastiques
- Machines-outils CNC
- Mesure et régulation de la température
- Mesure et régulation de la température
- Mines, métallurgie et fondation
- Moteurs et transformateurs
- Traction de tram et de chemin de fer
- Variateurs CA et CC (onduleurs)
-
Installation
-
-
Inducteurs
-
-
Appareils à induction
-
-
https://www.dacpol.eu/pl/naprawy-i-modernizacje
-
-
Service
-
- Contact
- Zobacz wszystkie kategorie
Risk assessment and explosion risk assessment
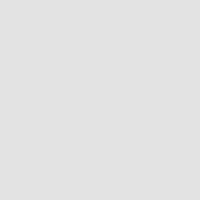
An integral part of every risk and explosion hazard assessment
An integral part of every risk and explosion hazard assessment, which are often elements of the Explosion Protection Document, is a summary containing conclusions regarding recommended changes and procedures in conditions of explosion hazard. Using an example of an explosion hazard assessment prepared for a mill with grain transportation and storage installation, a set of recommendations assigned to the so-called prevention and protection layer can be created. These are sets of factors that limit, on one hand, the possibility of creating an explosive atmosphere, and on the other – in situations where this fails – minimize the risk of the occurrence of an effective ignition source.
Organizational and technical measures for explosion protection
Recommendations and suggestions for the mill installation and grain and flour transportation and storage
The technology used in grain silos and mills encourages the formation of explosive atmospheres and explosions of grain-flour mixtures – especially in cleaning, hulling, and grinding processes of grain. Dust concentrations within explosion limits occur inside all transport devices (bucket elevators, screw and chain conveyors), in many cleaning machines (hullers, brushers, scrubbers), grinding machines (grinders, roller mills, bran cleaners), and in grain and flour chambers during filling.
Hazardous places
Group 1
The first group includes all the above-described internal spaces of machines and devices where dust is generated, transported, or processed. In case of an explosion inside the device, it usually results in more or less rupture of its casing and the ejection of flames and dust to the immediate vicinity of the failure site.
Group 2
The second group includes practically all spaces and surfaces outside production devices where dust can settle, such as floors, window frames, sills, supporting beams, girders, walls, ceilings, machine surfaces, and electrical installations and devices. In the case of dispersed settled dust and its ignition, a catastrophic explosion occurs.
Actions taken should primarily aim at
1. Technological actions
- Grain intake devices should have a functional aspiration system.
- All transport devices (elevators and conveyors) and cleaning machines (triers, brushers, scrubbers) must be dustproof and aspirated at dust-generating points.
- Aspiration should also be applied to such machines as grain and mill winnowers, grinding and sifting machines.
- Aspiration systems should be turned on before starting the machines and devices and turned off only after these machines and devices have been previously turned off.
- Aspiration systems must be constantly functional and subject to inspections.
- Gravity transport pipes should be sealed, and all inspection holes and viewports should be closed during the process.
- In the technological process, permanent magnets or electromagnets should be installed to capture ferromagnetic contaminants before the following machines:
- Hullers, scrubbers.
- Grinders, first-grind roller mills.
- The condition of installed magnetic barriers should be regularly checked.
- Observe the fire safety instructions when operating grain dryers, especially:
- Direct only dried grain to the dryer.
- Do not exceed permissible grain drying temperatures.
- Maintain the efficient operation of ejectors.
- Prevent the accumulation of dust inside dryers.
- Maintain constant supervision of the operating dryer.
- Observe the occupational health and safety instructions for operating machines and devices posted at workplaces.
2. Technical and maintenance actions
- Electrical devices in the plant must be uniformly grounded.
- In accordance with the requirements of applicable energy device operation regulations, required periodic inspections, maintenance, repairs, and measurements must be performed:
- Power networks.
- Electrical drive devices.
- Electrical devices in explosion hazard areas.
- Work on maintenance, repairs, and overhauls of power devices should be performed after disconnecting these devices from the power supply by persons with the required qualifications.
- Electric motors and electrical equipment, depending on the hazard location, should be used in the required degree of protection IP. The hazard locations and the equipment used are specified for each facility by the "classification of facility rooms to the appropriate category of fire hazard and explosion hazard category and determination of fire zones".
- For pneumatic transport devices:
- Maintain pipeline tightness continuously.
- Maintain a functional equipotential bonding system.
- Perform required periodic grounding and equipotential bonding resistance measurements at least once a year.
- All internal transport devices (elevators and conveyors) are subject to constant daily inspections of technical condition and proper operation.
- Aspiration (dust removal) devices are subject to daily functional inspections, particularly:
- Bag filters – functional inspection of shaking devices.
- Filter cyclones – functional inspection of cleaning devices.
- Cyclones – adjustment of cleaning irregularities.
- Aspiration pipes – tightness and patency.
- Regularly inspect and lubricate the bearings of machines and devices as required.
- Maintain constant dust-tightness of lighting fixtures, socket outlets, junction boxes, and other devices and elements of the electrical installation in production and storage rooms.
3. Technical and organizational actions and recommendations
- Fire-hazardous work (welding, heating, cutting, soldering, etc.) in the vicinity of silos and mill rooms should only be performed with permission; storing wet grain in chambers (silos) is particularly hazardous.
- During long-term storage, ensure grain moisture does not exceed 14%.
- Grain storage in heaps should be based on the degree of moisture and the strength of ceilings.
- Periodically conduct organoleptic quality control and state of stored grain; if necessary, perform conservation treatments by ventilation – turning over to remove excess moisture and reduce grain temperature.
- Secure existing technological openings, e.g., cover metal lids over silos after work, cover grain, flour, and bran chamber covers.
- For lighting grain, flour, and bran chambers, use:
- Fixed lamps placed outside the chambers in hermetically sealed enclosures.
- Portable lamps placed outside the chamber designed to prevent dust atmosphere penetration inside.
These lamps should be powered by current not exceeding 24 V, dust-tight, and protected against mechanical damage.
- Electric flashlights up to 6 V.
- Maintain order and cleanliness in all production and storage rooms. Do not allow dust accumulation on mechanical and electrical devices and structural parts of buildings (ceilings, walls, columns, girders, etc.).
- Cleaning (dusting) around power devices in mills and silos is performed by:
- Electricians – inside closed switchboards and distribution boxes – direct operational maintenance (users).
- Outside switchboards, switches, socket outlets, lighting fixtures, and electric motors – under constant electrician supervision.
Cleaning work should be performed systematically.
- Keep portable fire-fighting equipment technically functional and in quantities compliant with the allocation for individual rooms.
- Maintain constant access to fire-fighting equipment and main power switches.
- Follow the fire safety regulations in the mill facility and the provisions of the Fire Safety Instructions of the plant.
Summary
The above list concerns a specific industry, in this case, the food industry, but provides an overview of the factors that must be considered when making recommendations summarizing methods for maintaining explosion hazards at an appropriately low level.
Articles similaires
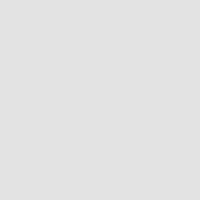
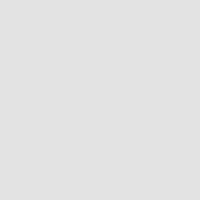
Laissez un commentaire