Vous devez être connecté
Smart Solution for 1500VDC 3-Level Central PV Inverters
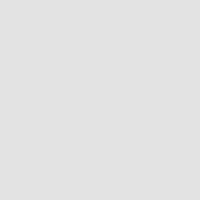
LV100: Smart Solution for 1500VDC 3-Level Central PV Inverters
In central PV inverter applications, 3-level neutral point clamp topologies based on 1200 V IGBTs are a popular approach. However, finding a suitable power module is often challenging considering the requirements of high current ratings, low stray inductance and standardized housing with widespread availability. Therefore a smart solution for the 1500VDC 3-level central PV inverters is needed.
By Thomas Radke, Narender Lakshmanan, Daniel He, Mitsubishi Electric Europe B.V
In general a problem occurs when 3-level NPC topologies are developed using several standard half bridge power modules. A series connection of IGBT modules results in high stray inductances which in combination with high switching di/dt cause high switching overvoltages [2]. IGBT modules with an integrated NPC topology phase-leg containing 4 IGBT and 6 diodes potentially have lower stray inductances but are not available for high current ratings and are more expensive due to the complex internal circuit [3]. The solution is the usage of the active neutral point clamp (A-NPC) topology in combination with a smart modulation scheme which enables the utilization of half bridge IGBT modules such as the new defacto standard (the LV100 modules) without the problem of switching overvoltages caused by high commutation inductances.
Due to a significant system cost reduction, an increased DC-voltage of 1500 VDC has recently become the standard for utility scale photovoltaic power plants Therefore, suitable circuit topologies and semiconductor devices capable of handling the 1500 VDC dc-link for central solar inverters have to be selected in order to fulfill the requirements pertaining to costs, efficiency, reliability and grid harmonics. A 2-level topology is not preferable since 1.7 kV IGBTs do not provide sufficient margin against failure considering the transient overvoltages. Additionally, under such operating conditions, the 1.7 kV IGBTs suffer high failure rates due to cosmic ray. Higher voltage devices such as the 3.3 kV IGBTs offer lower cosmic ray induced failure rates and also provide sufficient margin for transient overvoltage’s. However, the 3.3 kV IGBTs’ switching and conduction losses do not fulfill the system requirements pertaining to efficiency and switching frequency. An optimized intermediate voltage class IGBT blocking capability is commercially not available to support 1500 VDC applications. As a result a 3-level topology based on 1200 V IGBTs is the preferred topology nowadays for inverters with DC-link voltages of up to 1500 VDC [6] in the field of renewable energy applications. A half bridge circuit configuration is the prevalent circuit topology of high power 1200 V IGBT modules. One major reason is that the half bridge modules provide an internal layout which is optimized to reduce the commutation inductance loop and thereby, make it possible to utilize high current 1200 V modules with reasonable transient overvoltages during operation. By using those half bridge modules in a 3-level NPC topology, several modules are involved in the commutation loop and therefore, the benefit of low inductive internal module layout is not present. As a result, half bridge modules cannot be used unless the switching speed, especially the di/dt is significantly slowed down to reduce transient overvoltages. For the latest trench IGBT generation, the di/dt controllability via gate resistances at turn-off is limited, hence a significant slowdown of the switching speed is not possible. In addition the increase of switching energy due to such slowdown would negatively impact the system efficiency, power density and finally the inverter cost.
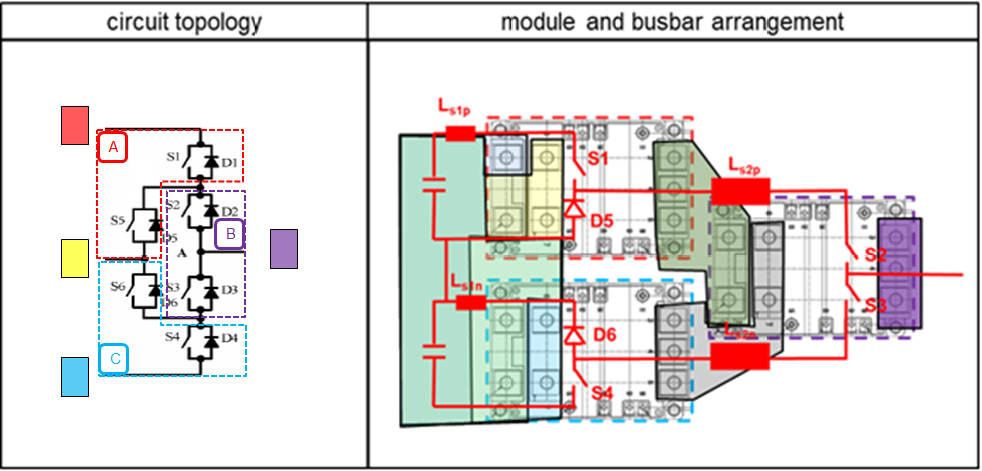
Figure 1: 3-level NPC topology based on three LV100 IGBT modules.
Commutation in 3-level NPC with half bridge / chopper modules Classical 3-level NPC topology
To build a 3-level NPC topology, three modules (one half bridge module and two chopper modules) are required as shown in Figure 1. The modules A and C are the chopper modules and the module B has a half bridge configuration. The parasitic stray inductances of module A and B (Ls1p and Ls1n) to the DC-link is small due to the optimized low inductive IGBT module layout and the consideration of a proper laminated DC-link design. However, the stray inductances (Ls2p and Ls2n) during commutation over several modules is not optimized and therefore, relatively high in comparison.
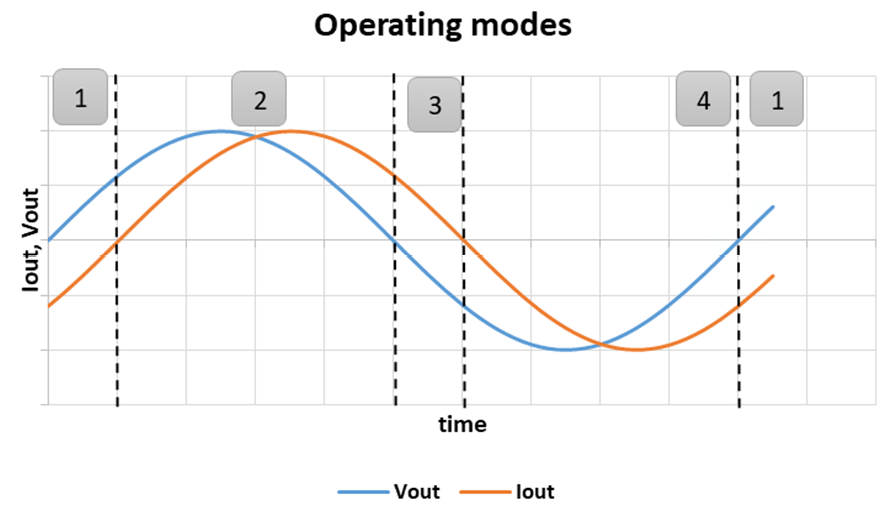
Figure 2: Operating modes of a 3-level inverter
Depending on the operating mode which is related to phase shift of the output voltage and the output current as seen in Figure 2, different commutation inductances need to be considered. The different operating modes for the 3-level NPC topology are shown in Figure 3.
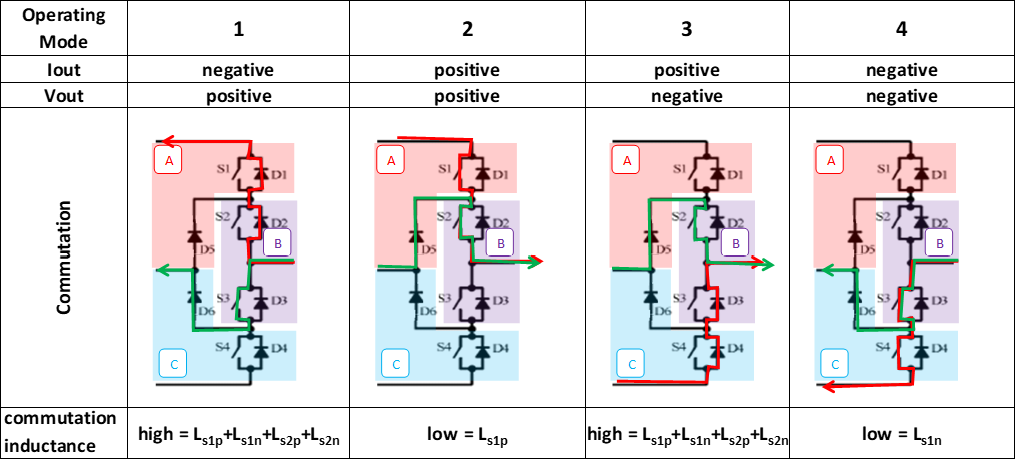
Figure 3: Operating modes for the 3-level NPC topology
In the operating modes 2 and 4, the effective commutation inductance is low since the commutation is within one power module (similar to a conventional 2-level operation). The IGBT module B is conducting the current but is not involved in the commutation loop. In the operating modes 1 and 3 the effective commutation inductance is high because all 3 modules are involved in the commutation event. As a result, overvoltages can occur which may exceed the blocking capability of the semiconductors and leads to the destruction of the IGBT modules.
Low inductive commutation by utilizing A-NPC topology
In the A-NPC 3-level topology, active switches (IGBTs) are added to the neutral point clamp diodes D5 and D6 of the NPC topology. By using these IGBTs, alternative commutation paths for the neutral voltage become available. Different control strategies are available which could lead to a more homogenous distribution [1] [5] of power losses among the different switching elements. Apart from such advantages, the A-NPC topology helps to realize low inductive commutation loops. Figure 4 shows the A-NPC topology being built by using three half bridge modules. For example, when the classical NPC topology is in operating mode 1, no low inductance path would be available since several modules are involved in the commutation event. However, when the A-NPC topology is in the operating mode 1, a new low inductive path over D2 and S5 is available. Additionally, in the operating mode 3, a new low inductive path over S6 and D3 also becomes available. Consequently, in all four operating modes, a low inductive commutation loop utilizing an active switch is present. No high inductive commutation path involving several modules is existing.
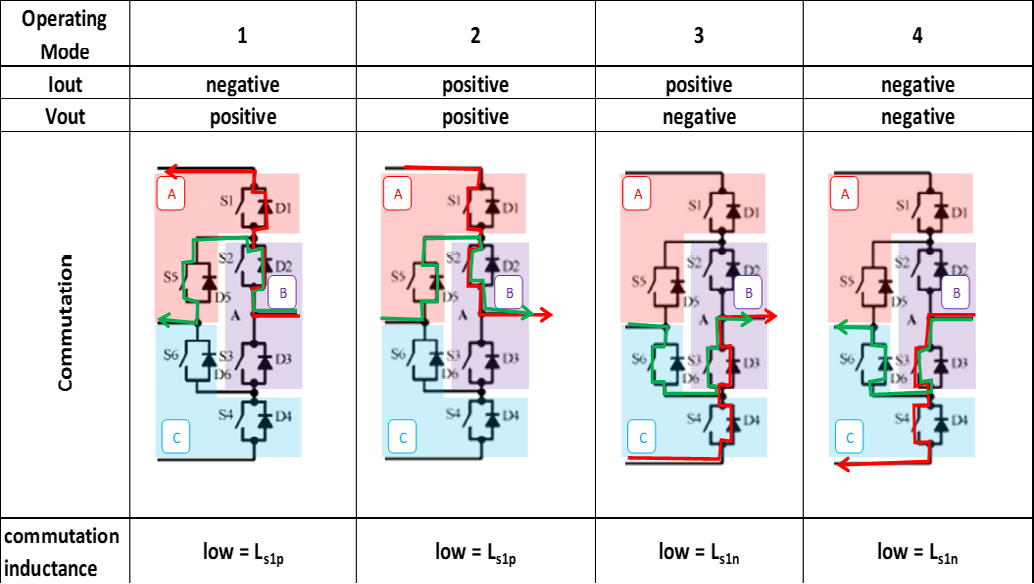
Figure 4: Operating modes for the 3-level A-NPC topology
3-level evaluations with LV100 IGBT modules Test setup
Considering the fact that the LV100 package has been established as a new standard for high power applications such as renewable energy, industrial drives, railway converters and grid applications [7], a test setup with three industrial 1200 A IGBT half bridge modules has been constructed. The setup represents one 3-level A-NPC phase leg as shown in Figure 5. The classical NPC topology commutation has also been evaluated by keeping the IGBTs S5 and S6 turned off. The effective commutation inductances and the maximum current, which can be switched without exceeding 1200 V, has been evaluated. The conditions for this evaluation were Tj=25°C and VCC = 1500 V (2 x 750 V).
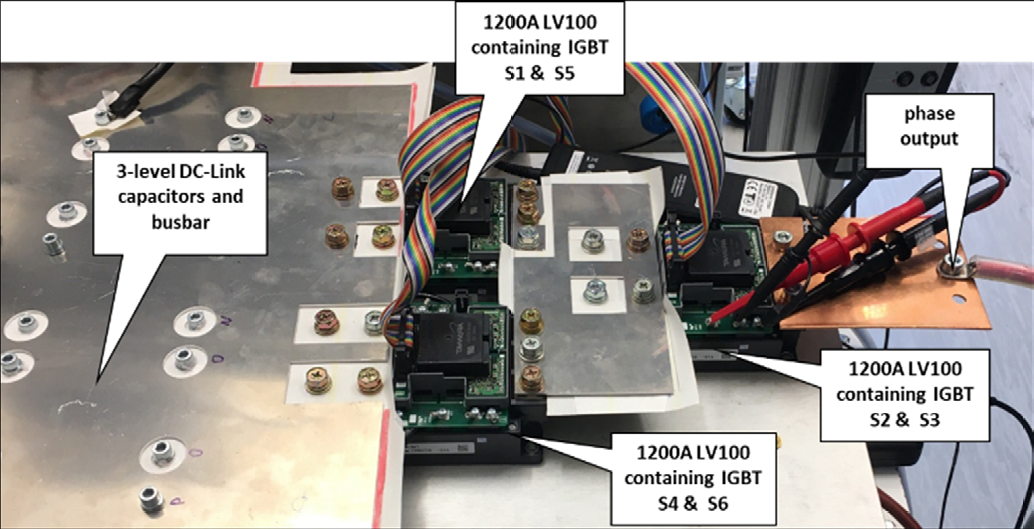
Figure 5: 3-level test setup based on three 1200 A LV100 IGBT half bridge modules
Evaluation results
The evaluation results shown in Figure 6 indicate that by utilizing the A-NPC topology, the stray inductance in all operating modes is less than 19 nH. In all operating modes the maximum current of 2400A (twice rated current) was not limited by transient overvoltages. The 2400A limitation indicated here pertains to the RBSOA limit as per datasheet for the 1200A IGBT module [8]. As shown in Figure 7, the maximum collector-emitter voltage (VCE) while switching off a collector current IC of 2400 A is less than 1100 V. However, by using the classical NPC topology, VCE reaches 1200 V while turning off a 637 A collector current. The high overvoltage is caused by the high stray inductance of 118.2 nH.
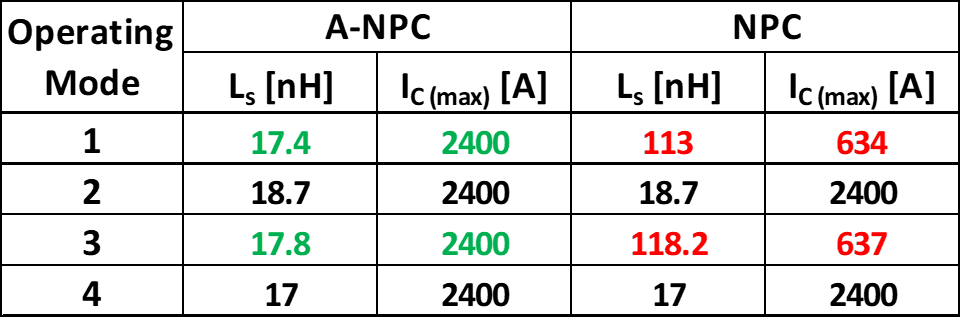
Figure 6: Evaluation results of operating modes: Commutation inductance and maximum collector current at 1200V for A-NPC and NPC topology
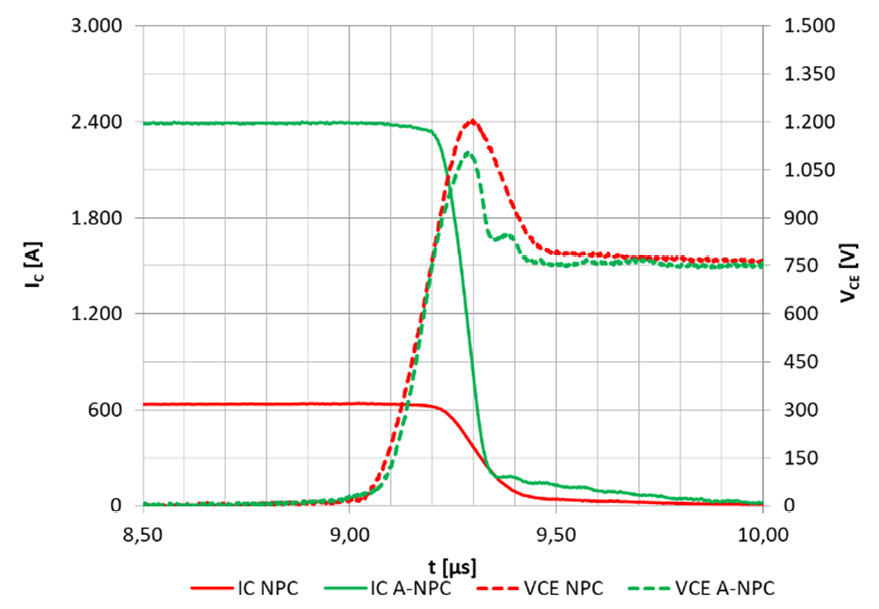
Figure 7: IGBT turn off waveform comparison: A-NPC vs. NPC in operating mode 3 at VCC=2x750 V, Tj=25°C.
Zero voltage crossing commutation in A-NPC topology
3-level voltage source PV-Inverters modulate sinusoidal voltages with a fundamental frequency of 50 Hz or 60 Hz. During the sinusoidal half waves (positive or negative) the A-NPC topology provide low inductive commutation paths. However, while changing the output voltage’s polarity, for example changing from operation mode 2 to 3 or from 4 to 1, a high inductive commutation over several modules cannot be avoided. In case of a power factor for purely active power [3] [4] (cos(φ)=1/-1) the output current is zero and the higher commutation inductance cause no overvoltages. But in case the inverter has to provide reactive power, the current needs to commutate over the high inductance path. Since a maximum collector current limitation such as the evaluated 637 A would not be acceptable, a dedicated novel switching pattern is required to reduce the overvoltage. The example in Figure 8 shows the commutation during an output voltage polarity change from the negative to the positive half wave at negative output current condition. This represents the change from operating mode 4 to 1. During the negative half wave, the IGBTs S4 and S6 are switched alternatively. The current commutates between path 1 and 2. By changing to the positive voltage half wave, the current has to commutate from the half bridge IGBT module C to A, via the high inductance path of 118.2 nH. During the polarity change, the commutation path 2 and 3 can be switched on in parallel by turning on the IGBTs S2, S3, S5 and S6. As shown in the waveform in Figure 8, the current will naturally commutate partially via path 2 to 3. In th evaluations with the 1200 A LV100 IGBT modules, it can be observed that after 80μs about 40% of the current of path 2 (IC S3) has commutated over to path 3 (IC S2) without any overvoltage. After this partia commutation, path 2 can be switched off by turn off of IGBT S6 and S3. At this turn off the di/dt is reduced since the current is already reduced by 40% before turning off. As shown in Figure 9, when IGBT S3 is switched off, an overvoltage will occur caused by the turn-off di/dt and the corresponding commutation inductance. The resulting overvoltage measured at the IGBT is devoid of the magnitude of the DC-link voltage, since the path 3 (D2 and S5) are already conducting.
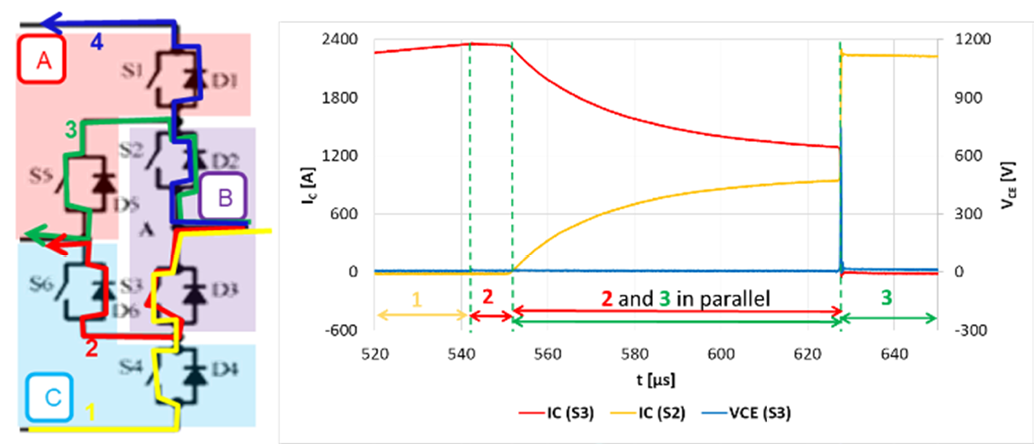
Figure 8: Novel commutation from operating mode 4 to 1 with reduced overvoltage

Figure 9: Waveform of IGBT S3’s turn off during the novel commutation with reduced overvoltage
The evaluation shows that at turn off of 2300 A, the resulting overvoltage is 750 V and thereby, well below the 1200 V limitation. The voltage polarity change to the positive sinusoidal half wave can herewith successfully be executed and the low inductive path 3 and 4 can be switched alternatively.
LV100 optimized for renewable and industrial applications
It has been demonstrated that half bridge IGBT modules can be used without the typical drawbacks related to the commutation inductances for the 3-level inverters. Additionally, considering the fact that central PV inverters require reliable, scalable and standardized power modules, the LV100 for industrial and renewable applications provide an optimized solution [7]. The LV100 housing is the new defacto standard for high power IGBT modules and therefore it has compatible outline to power modules from different suppliers. The line-up of the LV100 for indutrail applications covers the 1200V and 1700V blocking voltage ratings as shown in Figure 10.
The LV100 for indutrail applications is based on the SLC packaging technology which has been proven to be a thermal cycle failure free packaging technology [9]. The thermal cycling failure mode is absent since the SLC packaging technology utilizes interconnecting materials with matched thermal expansion coefficients and does not require a solder layer to connect the substrate to the baseplate. The 7th generation IGBT and diode chips’ technology helps in achieving the highest possible inverter efficiency. A combination of these technologies with the advanced symmetrical low inductive internal layout delivers the highest possible power density [7] and a reliable operation.
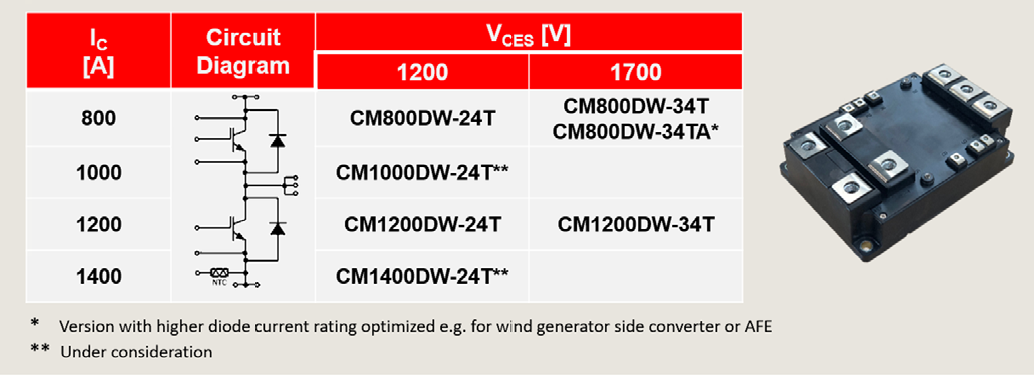
Figure 10: Line-up of LV100 for industrial and renewable applications
Summary
High power 3-level central PV inverters with low inductive commutation can be realized by using half bridge IGBT modules. It has been shown that by using LV100 IGBT modules in combination with the active neutral clamp (A-NPC) topology, a low inductive commutation path is available for all operating modes. During an output voltage polarity change, the novel commutation pattern described here can be applied to effectively reduce the switching overvoltage.
Conclusion: An excellent solution for high power 3-level inverters can be achieved by combining the high reliability offered by the SLC packaging technology, the power loss optimization offered by the 7th generation chip technology, the supply chain security available for the LV100 housing and the opportunity to establish low inductance switching schemes.
References:
[1] D. Floricau, E. Floricau and G. Gateau, "Three-level active NPC converter: PWM strategies and loss distribution," 2008 34th Annual Conference of IEEE Industrial Electronics, Orlando, FL, 2008, pp. 3333-3338
[2] M. Honsberg and T. Radke: “4in1 400A/1200V Module with T-type Topology for 3-Level Applications” Bodos Power Feb’2015, pages 26-28.
[3] M.Honsberg, T. Radke : “3-level IGBT modules with Trench Gate IGBT and their thermal analysis in UPS, PFC and PV operation modes” - EPE 2009 – Barcelona - ISBN: 9789075815009 pages 1-7
[4] T. Radke and M. Honsberg: “A family of 3-level IGBT modules from 10A to 600A equipped with Trench Gate IGBT and their thermal performance under typical conditions for UPS and PV inverter operation” PCIM2009 ISBN: 978-3-8007-3158-9 pages 136-139
[5] L. Caballero, S. Ratés, O. Caubet, S. Busquets-Monge: “Advantages of ac-ac power converters based on ANPC topology for wind applications” E EWEA 2015
[6] N. Lakshmanan and T. Radke: “Power Modules for Combining Innovation, Flexibility and Power Capability in the Various 3-Level Topologies” Bodo’s Power Systems April 2016, pages 26-29
[7] T. Radke and N. Lakshmanan: “The Next Generation of High Power IGBT Modules LV100 for Wind Converter, Photovoltaic Inverter and Motor Drives” Bodo’s Power Systems May 2019, pages 42-45
[8] Datasheets 1200A LV100 IGBT Module CM1200DW-34T and CM1200DW-24T
[9] T. Radke and N. Lakshmanan: “New Horizons in Thermal Cycling Capability Realized with the 7th gen. IGBT Module Based on SLC-Technology” Bodo’s Power Systems May 2017, pages 48-51
Laissez un commentaire