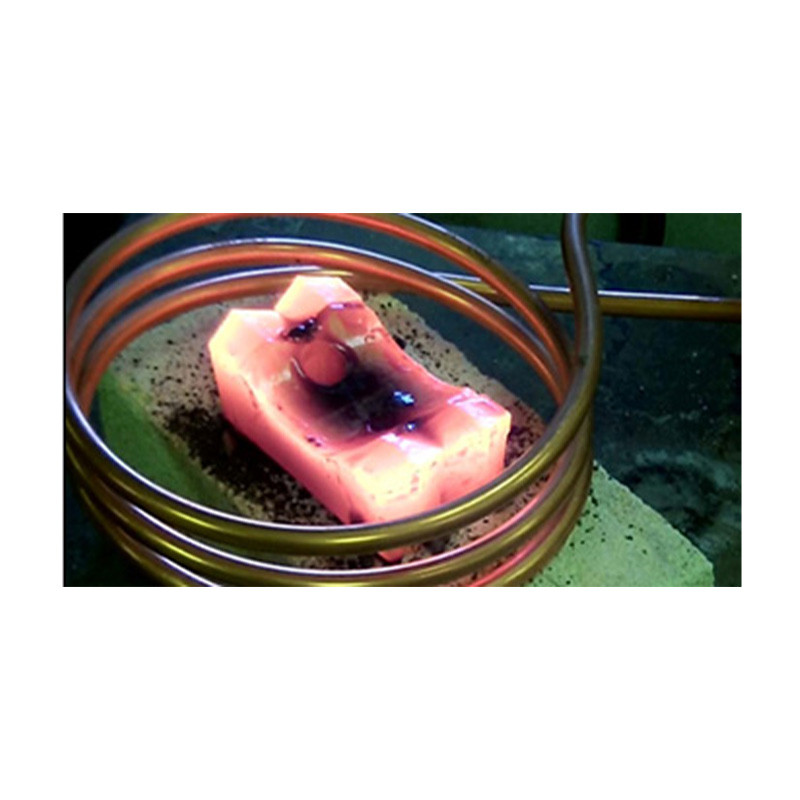
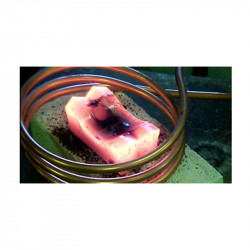
Vous devez être connecté
Category
Les photos sont à titre informatif uniquement. Voir les spécifications du produit
please use latin characters
Objective |
To heat a magnetic steel cutting tool for a brazing application; the end product is a cutter for the logging industry |
---|---|
Material |
|
Temperature | 871°C |
Frequency | 55kHz |
Equipment |
|
Process |
The multiple-position coil was used to test the brazing application on a large rectangular cutting head. With an EKOHEAT 45 kW power supply, the part can be heated to temperature within 150 seconds. Despite testing occurring on a 45kW /100 kHz power supply, Ambrell actually recommends an EKOHEAT 50 kW/30 kHz |
Results |
|
Êtes-vous intéressé par ce produit? Avez-vous besoin d'informations supplémentaires ou d'une tarification individuelle?
Ajouter à la liste de souhaits
Vous devez être connecté
Objective |
To heat a magnetic steel cutting tool for a brazing application; the end product is a cutter for the logging industry |
---|---|
Material |
|
Temperature | 871°C |
Frequency | 55kHz |
Equipment |
|
Process |
The multiple-position coil was used to test the brazing application on a large rectangular cutting head. With an EKOHEAT 45 kW power supply, the part can be heated to temperature within 150 seconds. Despite testing occurring on a 45kW /100 kHz power supply, Ambrell actually recommends an EKOHEAT 50 kW/30 kHz |
Results |
|
Votre avis ne peut pas être envoyé
Signaler le commentaire
Signalement envoyé
Votre signalement ne peut pas être envoyé
Donnez votre avis
Avis envoyé
Votre avis ne peut être envoyé