Musisz być zalogowany/a
-
WróćX
-
Alkatrészek
-
-
Kategória
-
Félvezetők
- Diody
-
Tyrystory
- Tyrystory firmy VISHAY (IR)
- Tyrystory firmy LAMINA
- Tyrystory firmy INFINEON (EUPEC)
- Tyrystory firmy ESTEL
- Tyrystory firmy WESTCODE
- Tyrystory firmy Semikron
- Tyrystory firmy POWEREX
- Tyrystory firmy DYNEX
- Tyrystory do grzejnictwa indukcyjnego
- Tyrystory firmy ABB
- Tyrystory firmy TECHSEM
- Przejdź do podkategorii
-
Moduły elektroizolowane
- Moduły elektroizolowane firmy VISHAY (IR)
- Moduły elektroizolowane firmy INFINEON (EUPEC)
- Moduły elektroizolowane firmy Semikron
- Moduły elektroizolowane firmy POWEREX
- Moduły elektroizolowane firmy IXYS
- Moduły elektroizolowane firmy POSEICO
- Moduły elektroizolowane firmy ABB
- Moduły elektroizolowane firmy TECHSEM
- Przejdź do podkategorii
- Mostki prostownicze
-
Tranzystory
- Tranzystory firmy GeneSiC
- Moduły SiC MOSFET firmy Mitsubishi
- Moduły SiC MOSFET firmy STARPOWER
- Moduły SiC MOSFET firmy ABB
- Moduły IGBT firmy MITSUBISHI
- Moduły tranzystorowe firmy MITSUBISHI
- Moduły MOSFET firmy MITSUBISHI
- Moduły tranzystorowe firmy ABB
- Moduły IGBT firmy POWEREX
- Moduły IGBT - firmy INFINEON (EUPEC)
- Elementy półprzewodnikowe z węglika krzemu
- Przejdź do podkategorii
- Sterowniki
- Bloki mocy
- Przejdź do podkategorii
- LEM áram- és feszültségátalakítók
-
Passzív alkatrészek (kondenzátorok, ellenállások, biztosítékok, szűrők)
- Rezystory
-
Bezpieczniki
- Bezpieczniki miniaturowe do układów elektronicznych seria ABC i AGC
- Bezpieczniki szybkie rurkowe
- Wkładki zwłoczne o charakterystykach GL/GG oraz AM
- Wkładki topikowe ultraszybkie
- Bezpieczniki szybkie standard brytyjski i amerykański
- Bezpieczniki szybkie standard europejski
- Bezpieczniki trakcyjne
- Wkładki bezpiecznikowe wysokonapięciowe
- Przejdź do podkategorii
-
Kondensatory
- Kondensatory do silników
- Kondensatory elektrolityczne
- Kondensatory foliowe Icel
- Kondensatory mocy
- Kondensatory do obwodów DC
- Kondensatory do kompensacji mocy
- Kondensatory wysokonapięciowe
- Kondensatory do grzejnictwa indukcyjnego
- Kondensatory impulsowe
- Kondensatory DC LINK
- Kondensatory do obwodów AC/DC
- Przejdź do podkategorii
- Filtry przeciwzakłóceniowe
- Superkondensatory
-
Zabezpieczenia przeciwprzepięciowe
- Ograniczniki przepięć dla aplikacji RF
- Ograniczniki przepięć dla systemów wizyjnych
- Ograniczniki przepięć linii zasilających
- Ograniczniki przepięć do LED
- Ograniczniki przepięć do Fotowoltaiki
- Ograniczniki przepięć dla systemów wagowych
- Ograniczniki przepięć dla magistrali Fieldbus
- Przejdź do podkategorii
- Filtry emisji ujawniającej TEMPEST
- Przejdź do podkategorii
-
Relék és kontaktorok
- Teoria przekaźniki i styczniki
- Przekaźniki półprzewodnikowe AC 3-fazowe
- Przekaźniki półprzewodnikowe DC
- Regulatory, układy sterujące i akcesoria
- Soft starty i styczniki nawrotne
- Przekaźniki elektromechaniczne
- Styczniki
- Przełączniki obrotowe
-
Przekaźniki półprzewodnikowe AC 1-fazowe
- Przekaźniki półprzewodnikowe AC jednofazowe serii 1 | D2425 | D2450
- Przekaźniki półprzewodnikowe AC jednofazowe serii CWA I CWD
- Przekażniki półprzewodnikowe AC jednofazowe serii CMRA I CMRD
- Przekaźniki półprzewodnikowe AC jednofazowe serii PS
- Przekaźniki półprzewodnikowe AC podwójne i poczwórne serii D24 D, TD24 Q, H12D48 D
- 1-fazowe przekaźniki półprzewodnikowe serii gn
- Przekaźniki półprzewodnikowe ac jednofazowe serii ckr
- Przekaźniki AC jednofazowe na szynę din SERII ERDA I ERAA
- Przekaźniki jednofazowe AC na prąd 150A
- Podwójne przekaźniki półprzewodnikowe zintegrowane z radiatorem na szynę DIN
- Przejdź do podkategorii
- Przekaźniki półprzewodnikowe AC 1-fazowe do druku
- Przekaźniki interfejsowe
- Przejdź do podkategorii
- Magok és egyéb indukciós elemek
- Hűtőbordák, Varisztorok, Hővédelem
- Ventilátor
- Légkondicionálás, Kapcsolótáblák tartozékai, Hűtők
-
Akkumulátorok, töltők, puffer tápegységek és átalakítók
- Akumulatory, ładowarki - opis teoretyczny
- Baterie litowo-jonowe. Niestandardowe baterie. System zarządzania baterią (BMS)
- Akumulatory
- Ładowarki akumulatorów i akcesoria
- Zasilanie awaryjne UPS i zasilacze buforowe
- Przetwornice i osprzęt do fotowoltaiki
- Magazyny energii
- Ogniwa paliwowe
- Ogniwa litowo-jonowe
- Przejdź do podkategorii
-
Automatizálás
- Futaba Drone Parts
- Wyłączniki krańcowe, Mikrowyłączniki
- Czujniki, Przetworniki
- Pirometry
- Liczniki, Przekaźniki czasowe, Mierniki tablicowe
- Przemysłowe urządzenia ochronne
- Sygnalizacja świetlna i dźwiękowa
- Kamera termowizyjna
- Wyświetlacze LED
- Przyciski i przełączniki
-
Rejestratory
- Rejestrator AL3000
- Rejestrator KR2000
- Rejestrator KR5000
- Miernik z funkcją rejestracji wilgotności i temperatury HN-CH
- Materiały eksploatacyjne do rejestratorów
- Rejestrator 71VR1
- Rejestrator KR 3000
- Rejestratory PC serii R1M
- Rejestratory PC serii R2M
- Rejestrator PC, 12 izolowanych wejść – RZMS-U9
- Rejestrator PC, USB, 12 izolowanych wejść – RZUS
- Przejdź do podkategorii
- Przejdź do podkategorii
-
Kábelek, Litz vezetékek, vezetékek, rugalmas csatlakozások
- Druty
- Lica
-
Kable do zastosowań specjalnych
- Przewody przedłużające i kompensujące
- Przewody do termopar
- Przewody podłączeniowe do czyjnków PT
- Przewody wielożyłowe temp. -60°C do +1400°C
- SILICOUL przewody średniego napięcia
- Przewody zapłonowe
- Przewody grzejne
- Przewody jednożyłowe temp. -60°C do +450°C
- Przewody kolejowe
- Przewody grzejne w Ex
- Przewody dla przemysłu obronnego
- Przejdź do podkategorii
- Koszulki
-
Plecionki
- Plecionki płaskie
- Plecionki okrągłe
- Bardzo giętkie plecionki - płaskie
- Bardzo giętkie plecionki - okrągłe
- Miedziane plecionki cylindryczne
- Miedziane plecionki cylindryczne i osłony
- Paski uziemiające giętkie
- Plecionki cylindryczne z ocynkowanej i nierdzewnej stali
- Miedziane plecionki izolowane PCV - temperatura do 85 stopni C
- Płaskie plecionki aluminiowe
- Zestaw połączeniowy - plecionki i rurki
- Przejdź do podkategorii
- Osprzęt dla trakcji
- Końcówki kablowe
- Szyny elastyczne izolowane
- Wielowarstwowe szyny elastyczne
- Systemy prowadzenia kabli
- Peszle, rury
- Przejdź do podkategorii
- Az összes kategória megtekintése
-
Félvezetők
-
-
- Szállítók
-
Alkalmazások
- Bányászat, kohászat és öntöde
- Berendezések elosztó-, vezérlő- és távközlési szekrényekhez
- Berendezések és alkatrészek veszélyes területekhez [Ex]
- CNC szerszámgépek
- DC és AC hajtások (inverterek)
- Energetika
- Energy bank
- Gépek fa szárítására és feldolgozására
- Hegesztőgépek
- Hőmérséklet mérés és szabályozás
- HVAC automatizálás
- Indukciós Hevítés
- Ipari automatizálás
- Ipari védőeszközök
- Motorok és transzformátorok
- Műanyag hőformázó gépek
- Nyomtatás
- Tápegységek (UPS) és egyenirányító rendszerek
- Villamos és Vasúti Vontatás
- Vizsgálati és laboratóriumi mérések
-
Telepítés
-
-
Induktorok
-
-
Indukciós eszközök
-
-
https://www.dacpol.eu/pl/naprawy-i-modernizacje
-
-
Szolgáltatás
-
- Kapcsolat
- Zobacz wszystkie kategorie
Legjobb gyakorlatok PCB-alkatrészek árnyékolására EMC szempontjából: Hogyan minimalizáljuk az elektromágneses zavarokat
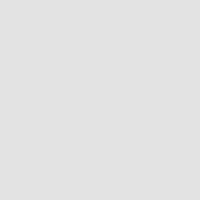
Best Practices for Shielding Components on PCBs for EMC: How to Minimize Electromagnetic Interference
Introduction to the Topic
With the growing demands for electromagnetic compatibility (EMC), designing printed circuit boards (PCBs) is becoming increasingly complex. Shielding is a key technique that protects electronic components from electromagnetic interference (EMI). In this article, we discuss the main challenges and best practices related to designing shielding for PCB components in terms of EMC.
The electronics market is undergoing dynamic changes, and with the increasing number of wireless devices and consumer electronics, electromagnetic compatibility (EMC) has become a critical aspect of design. Electronic devices, from smartphones to advanced medical and automotive systems, must meet strict EMC standards to ensure safe and efficient operation. The rapid development of technologies such as 5G, the Internet of Things (IoT), and wearable electronics contributes to the growing number of devices that operate at higher frequencies. This, in turn, increases susceptibility to electromagnetic interference (EMI).
In 2023, the global electromagnetic shielding market reached a value of $7 billion, highlighting the growing importance of this technology. It is estimated that by 2030, the market value will increase by another 50%, driven by the growing number of applications that require EMC compliance. Companies must invest in advanced shielding techniques to meet these demands. A lack of proper shielding can lead to device compatibility issues and negatively affect their performance and reliability.
History and Origins of the Issue
Problems related to electromagnetic interference date back to the early use of radio technologies in the early 20th century. The first radio communication systems were particularly susceptible to interference caused by other sources of electromagnetic radiation. As electronics and telecommunications developed, engineers began to notice that these interferences could significantly impact signal quality and device reliability. Even then, the first steps were taken to protect systems from EMI, mainly through the use of proper grounding and signal isolation techniques.
In the 1970s, with the rapid growth in the number of electronic devices, the problem of electromagnetic interference became more common and serious. Companies such as Bell Laboratories began conducting intensive research on methods of protection against EMI. The introduction of the first EMC-related regulations, such as the MIL-STD-461 standards for military equipment, forced manufacturers to design devices with shielding in mind.
In the 1980s and 1990s, the development of microprocessor technologies and digital devices further increased the need for EMC compliance. More advanced techniques, such as the Faraday cage, and dedicated shielding materials began to be widely used in the industry. From that moment on, electromagnetic shielding became a standard element of electronic circuit design, especially for devices operating at high frequencies.
Today, shielding techniques and electromagnetic interference management are integral parts of the electronics industry, especially in the context of emerging 5G technologies, IoT, and the automotive industry, where autonomous and electric systems are becoming increasingly common.
Key Challenges and Problems
Miniaturization and Design Complexity
With the ongoing miniaturization of electronic devices, designers face the challenge of efficiently placing components in limited space. The smaller the size of the PCB, the harder it is to maintain proper distance between interference-emitting elements and sensitive components. When designing analog, digital, and power systems, it is especially important to avoid mutual interference. Improper component placement can lead to interference, which affects device stability.
Managing the Ground Plane
A uniform, unbroken ground plane is the foundation for designing PCBs that are resistant to electromagnetic interference. The ground plane plays a key role in absorbing conducted interference. However, designing multi-layer PCBs, especially for complex devices like cell phones or medical equipment, can lead to discontinuities in the ground plane. Vias can further introduce problems with conducted interference if they are not properly placed and grounded.
Ground Loops and Conducted Interference
Ground loops are a common problem in multi-layer devices. They occur when different sections of the board have different ground potentials, leading to conducted interference. Signals that flow through these loops can cause interference between components. To prevent this phenomenon, designers must carefully plan grounding and signal paths to minimize the risk of such loops.
Shielding Material
Choosing the right shielding materials plays a key role in ensuring effective protection against EMI. Materials such as copper, aluminum, and stainless steel have different conductivity and interference attenuation properties. Copper, due to its excellent conductivity, is most commonly used, especially in high-performance designs. Stainless steel, though cheaper, offers poorer interference attenuation and is used in less demanding applications. The high frequencies at which today's devices operate require the use of more advanced materials and techniques, such as multi-layer shielding coatings.
Radiated Interference
Radiated interference can penetrate key components such as microprocessors, oscillators, or radio modules. Especially in IoT devices, which often operate in high-EMI environments, it is important for designers to use proper shielding and signal isolation techniques. The high operating frequencies of such devices, reaching even tens of GHz, mean that standard shielding techniques may not be sufficient. In such cases, the use of special shielding materials and precise circuit design becomes essential.
Best Practices and Design Techniques
Isolation of Analog and Digital Signals
One of the most important aspects of designing EMC-compliant PCBs is the proper separation of analog and digital signals. High-frequency digital signals can introduce interference into analog signal paths, affecting measurement accuracy and device stability. Therefore, it is recommended that, where possible, analog and digital sections be placed on different layers or physically separated on the board.
Proper Placement of Vias
Vias are often used in multi-layer designs, but improper placement can lead to conducted interference. To avoid this, vias should not be placed near sensitive components and should be introduced symmetrically to minimize potential differences on the ground plane.
Using EMI-Absorbing Materials
EMI-absorbing materials, such as ferrite beads and films, can significantly reduce the electromagnetic radiation generated by components. Especially in high-density devices, where space is limited, these materials can be used in places where standard shielding techniques are difficult to implement.
Designing Low-Impedance Connectors
Low-impedance connectors, such as coaxial connectors, provide effective protection against interference. They are especially important in high-frequency connections, where even small impedance differences can lead to signal reflections and interference. Choosing the right type of connector, along with its precise placement, can significantly improve the EMC compliance of the entire system.
Conclusion
Designing EMC-compliant PCBs requires a comprehensive approach that considers both the selection of appropriate materials and design techniques. Miniaturization, high operating frequencies, and the complexity of modern electronic devices make EMC compliance an increasingly challenging task. Using best practices, such as shielding, proper placement of vias, and signal isolation, minimizes the risk of interference and ensures the reliability and safety of device operation.
Related posts
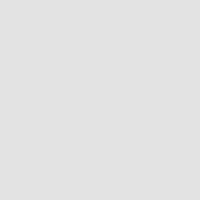
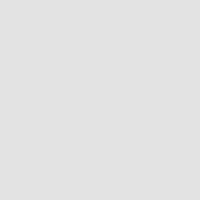
Leave a comment