Musisz być zalogowany/a
Więcej mocy i wyższa niezawodność dzięki modułowi IGBT 7. generacji z nową technologią SLC
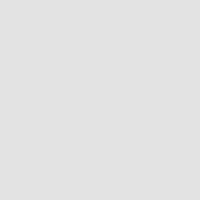
Więcej mocy i wyższa niezawodność dzięki modułowi IGBT 7. generacji z nową technologią SLC
Główne wymagania dotyczące systemów elektroniki mocy to wysoka wydajność, wysoka gęstość mocy i wysoka niezawodność. Aby osiągnąć wysoką wydajność, Mitsubishi Electric opracowało chipset IGBT 7. generacji. Aby dodatkowo spełnić wymagania dotyczące wysokiej niezawodności i wysokiej gęstości mocy, nowo opracowana technologia pakietu SLC jest połączona z czipem 7. generacji w serii modułów IGBT typu NX.
Przez Thomasa Radke, Mitsubishi Electric Europe B.V., Koichi Masuda, Mitsubishi Electric Corp., Japonia
Przemysłowe moduły IGBT są stosowane w różnych dziedzinach zastosowań. Wszystkie te aplikacje wymagają kompaktowych modułów mocy o dużej gęstości mocy, wysokiej niezawodności i wysokiej wydajności przy rozsądnych kosztach. Aby spełnić wszystkie te wymagania, opracowano moduły IGBT NX 7. generacji oparte na technologii SLC. IGBT 7. generacji, oparty na koncepcji CSTBT™, zapewnia wysoką wydajność poprzez redukcję strat dynamicznych i statycznych [2]. Redukcja strat jest pierwszym krokiem w realizacji modułu o dużej gęstości mocy. W drugim kroku należy poprawić oporność termiczną Rth, aby zwiększyć zdolność do przewodzenia mocy przy określonej temperaturze pracy i zmniejszyć wahania temperatury. Poprzez połączenie poprawionej zdolności do cyklicznego obciążenia termicznego i mocy można uzyskać wysoką niezawodność i kompaktowe moduły mocy. Nowo opracowana technologia opakowania SLC zapewnia niską oporność termiczną oraz wysoką zdolność do cyklicznego obciążenia mocy i ciepła.
Technologia SLC
Technologia SLC (SoLid Cover) to nowo opracowana technologia pakietowa umożliwiająca uzyskanie wysokiej niezawodności i wysokiej przewodności cieplnej [3]. Porównanie nowej struktury opakowania z konwencjonalną strukturą przedstawiono na Rysunku 1.
Tradycyjnie stosuje się ceramiczne podłoża metalizowane do zapewnienia izolacji elektrycznej między obwodem elektrycznym z układami półprzewodnikowymi a płytą bazową modułu. Podłoża te są połączone z płytą bazową miedzianą za pomocą warstwy lutu. Wadą tej kombinacji materiałowej jest brak dopasowania współczynnika rozszerzalności termicznej (CTE) między ceramiką, lutem a miedzią. Dopasowanie to powoduje pęknięcia lutu spowodowane wahaniem temperatury i ogranicza czas życia modułów mocy. Zdolność modułu do wytrzymania tego naprężenia jest znana jako zdolność cyklicznego obciążenia termicznego.
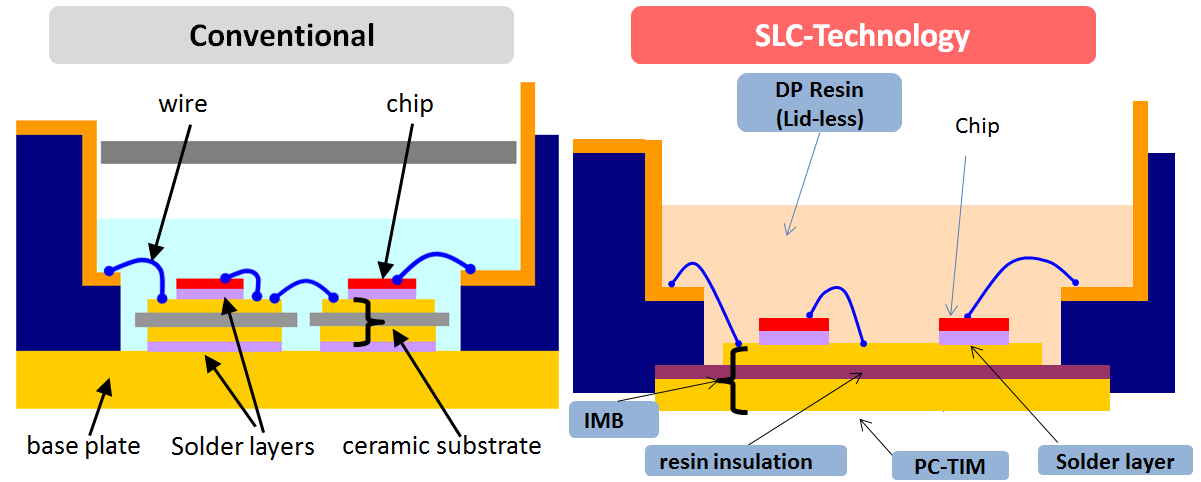
Rysunek 1: Porównanie struktur opakowań SLC i konwencjonalnych
W technologii SLC izolacja jest realizowana przez materiał żywicowy, który ma podobną wartość CTE jak miedź. Płyta bazowa i warstwa lutu są eliminowane, ponieważ górna i dolna warstwa miedzi mogą być bezpośrednio połączone z warstwą izolacyjnej żywicy. Dzięki temu IMB (Insulated Metal Baseplate) zdolność cyklicznego obciążenia termicznego jest znacznie poprawiona. Aktualny stan trwającego testu cyklu temperaturowego pokazano na Rysunku 2. Obecnie osiągnięto 40 tys. cykli przy wahaniach temperatury 80K. Ten wynik jest około 7 razy wyższy niż w przypadku konwencjonalnej zdolności, a test ten trwa nadal bez awarii. Ponadto, jak pokazano po prawej stronie Rysunku 2, po 40 tys. cyklach nie zaobserwowano żadnej delaminacji. Dlatego można się spodziewać jeszcze większej zdolności cyklicznego obciążenia termicznego.
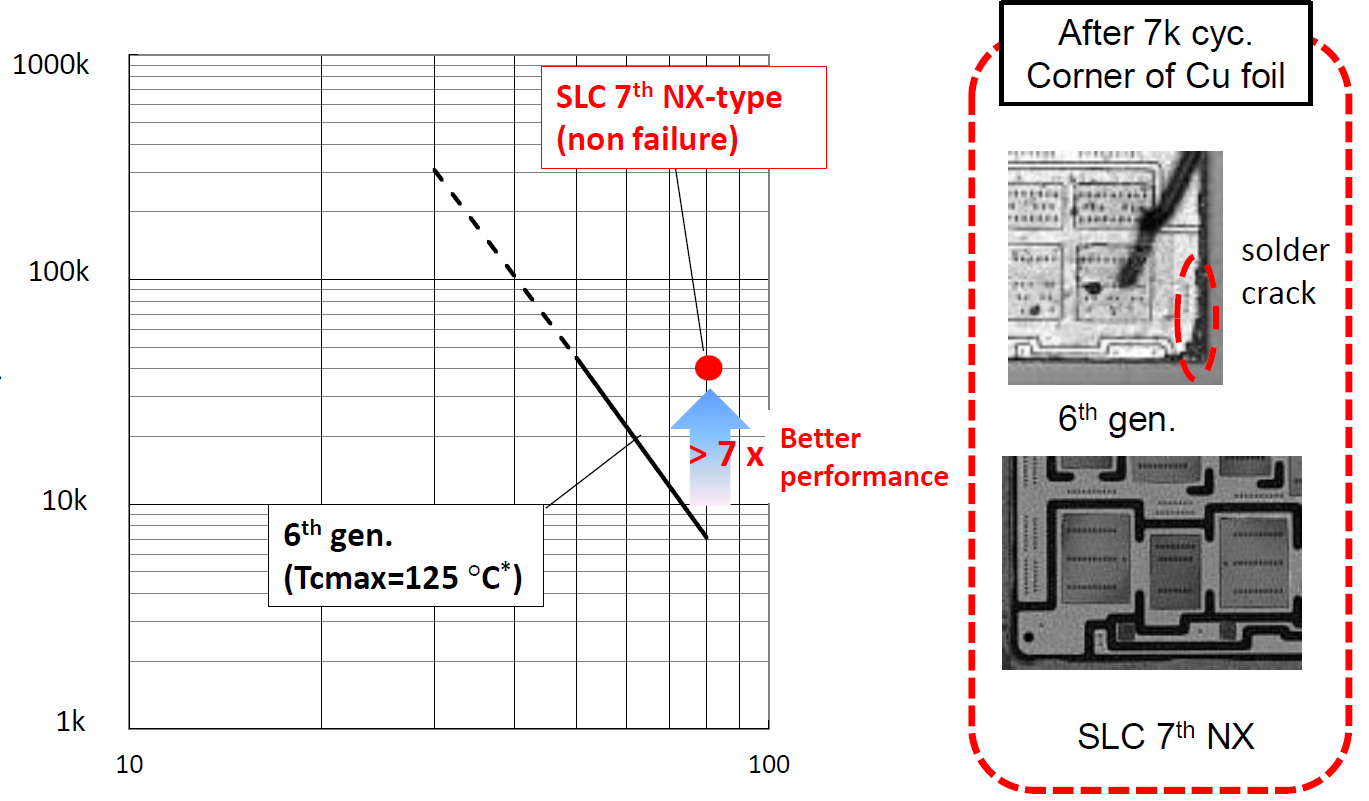
Rysunek 2: Stan testu cyklu termicznego
W konwencjonalnych modułach maksymalny rozmiar ceramicznych podłoży jest ograniczony przez zdolność do cyklicznego obciążania termicznego, ponieważ naprężenia mechaniczne wywołane wahaniem temperatury wzrastają wraz ze wzrostem rozmiaru podłoża. W związku z tym w konwencjonalnych modułach IGBT o rozmiarze podstawy 122 mm x 62 mm zazwyczaj używa się dwóch lub trzech ceramicznych podłoży, jak pokazano na Rysunku 3. Z kolei nowa technologia SLC składa się z jednego wspólnego podłoża IMB dzięki eliminacji warstwy lutu między podłożem a płytą bazową. Dzięki temu podejściu z wykorzystaniem wspólnego podłoża zwiększa się dostępna powierzchnia do montażu układów mocy w module, a połączenia za pomocą wiązek drutów między podłożami są eliminowane, co zmniejsza parazytne indukcyjności wewnętrzne pakietu oraz opór wiodący. Dlatego wspólne podłoże IMB stanowi jedno z kluczowych elementów technologii SLC pozwalających osiągnąć kompaktowe moduły mocy o dużej gęstości mocy.
Oprócz zdolności do cyklicznego obciążania termicznego, należy również uwzględnić zdolność do cyklicznego obciążania prądem w celu opracowania modułu mocy o wysokiej niezawodności. Główną przyczyną awarii związanej z cyklicznym obciążaniem prądem jest degradacja połączenia drutów wiązanego. Ciągły przepływ prądu i związane z tym wahania temperatury złączy przewodów powodują naprężenia w połączeniach drutowych. W nowej technologii SLC druty połączeniowe są pokryte twardą żywicą do bezpośredniego otoczenia, a nie miękkim żelem silikonowym. Dzięki twardej żywicy DP, naprężenia mechaniczne połączenia drutowego są równomiernie rozłożone na całej powierzchni drutu, jak pokazano na Rysunku 4. W konwencjonalnym module mocy naprężenie mechaniczne drutu nie jest tak bardzo absorbowane przez miękki żel silikonowy, a to naprężenie skupia się w podstawie drutu wiązanego. Moduły IGBT 6. generacji zastosowały już zoptymalizowaną i ulepszoną technologię wiązania drutów, aby osiągnąć wysoką żywotność cyklu mocy przy użyciu drutów aluminiowych i powłoki miękkiego żelu silikonowego. Ponadto, poprzez połączenie tej technologii wiązania drutów i technologii SLC, zdolność do cyklicznego obciążania prądem jest istotnie zwiększona, zachowując sprawdzone i kosztowo korzystne połączenia drutów aluminiowych w porównaniu do drogich technologii, takich jak wiązanie drutem miedzianym. Porównanie między docelową zdolnością do cyklicznego obciążania prądem technologii SLC a modułami 6. generacji jest pokazane na Rysunku 5.
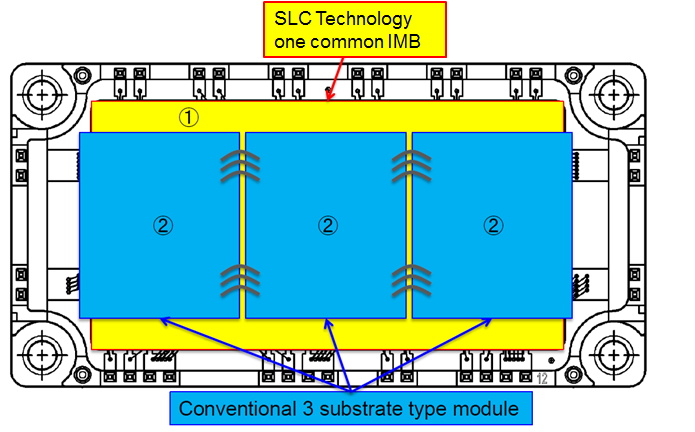
Rysunek 3: Pakiet typu NX z: 1 IMB i 2. Konwencjonalne podłoże ceramiczne
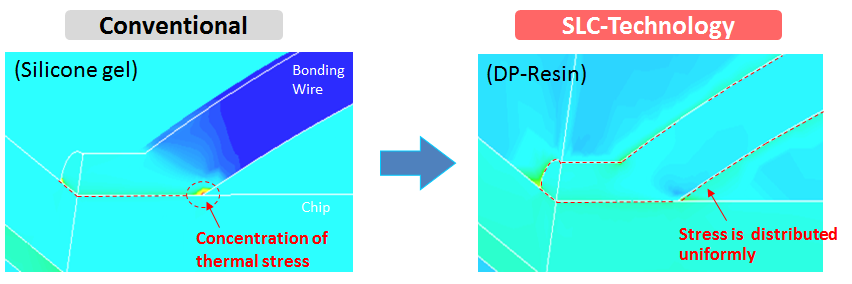
Rysunek 4: Skupienie naprężenia na wiązce drutów w technologii konwencjonalnej i SLC
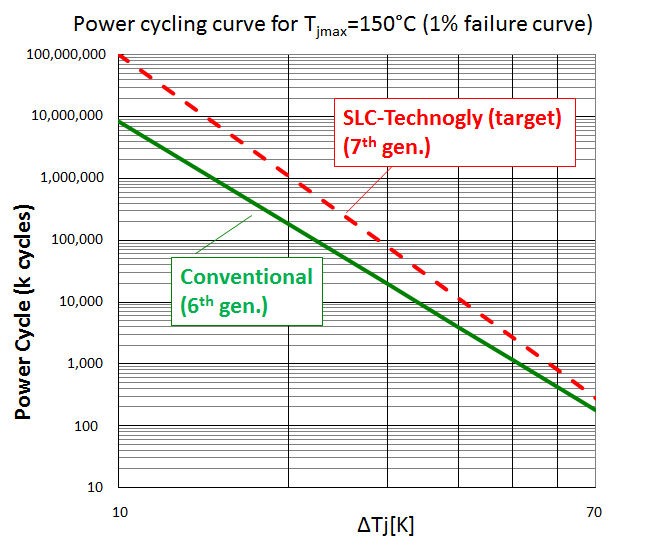
Rysunek 5: Zdolność do cyklicznego obciążania prądem w technologii konwencjonalnej i SLC
Aby dalszo poprawić żywotność cyklu mocy, należy zredukować wahania temperatury przyłącza. Można to osiągnąć poprzez poprawę oporu termicznego modułu mocy. Aplikacje o stałym obciążeniu są zazwyczaj ograniczone termicznie przez maksymalną temperaturę złącza.
Aby spełnić również te wymagania, technologia SLC poprawiła opory termiczne. Technologia SLC stosuje IMB, dlatego eliminowana jest warstwa lutu o niskiej przewodności cieplnej między podłożem a płytą bazową. Materiał izolacyjny i grubość warstwy izolacyjnej IMB są dobrane w celu osiągnięcia najlepszego kompromisu pomiędzy zdolnością izolacji, niezawodnością i niskim oporem termicznym. Dzięki tej optymalizacji możliwe jest osiągnięcie redukcji oporu termicznego od złącza do obudowy Rth(j-c) o około 30% w porównaniu do konwencjonalnych modułów, w których tlenek glinu (Al2O3) jest powszechnie stosowany jako materiał ceramiczny.
W konwencjonalnych modułach z płytą bazową miedzianą i podłożem ceramicznym należy również uwzględnić wykrzywienie płyty bazowej podczas cykli temperaturowych spowodowane niezgodnymi współczynnikami rozszerzalności cieplnej i wynikającym z tego "efektem bimetalicznym". To wykrzywienie ogranicza możliwość poprawy oporu termicznego kontaktu między płytą bazową a radiator ciepła Rth(c-s). Dzięki nowej technologii SLC, która ma dopasowane współczynniki rozszerzalności cieplnej, to wykrzywienie można praktycznie wyeliminować, a interfejs termiczny między płytą bazową a radiator ciepła można dalszo poprawić, stosując zoptymalizowany materiał termoprzewodzący zmieniający fazę (PC-TIM) o wcześniej zastosowanym zastosowaniu. Całkowity opór termiczny od złącza do radiatora ciepła konwencjonalnej technologii modułów jest o około 43% wyższy niż w technologii SLC przy tych samych rozmiarach układu scalonego. Ta wyjątkowa wydajność termiczna jest również jedną z istotnych cech, które spełniają wymagania rynkowe dotyczące wysokiej gęstości mocy i wysokiej niezawodności.
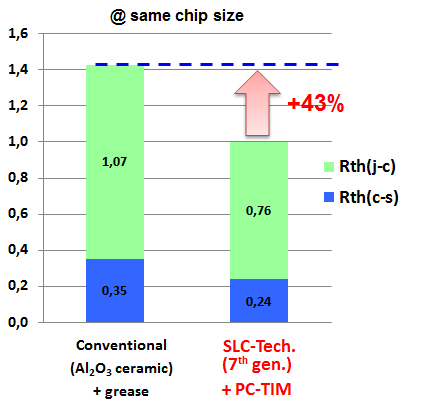
Rysunek 6: Porównanie oporów termicznych przy tych samych rozmiarach układu scalonego
Moduły IGBT 7. generacji typu NX
Nowa technologia SLC wraz z układem scalonym IGBT 7. generacji została wprowadzona w serii modułów typu NX firmy Mitsubishi Electric.
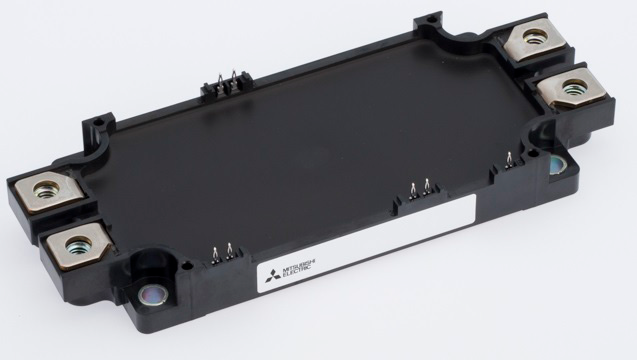
Rysunek 7: Moduł IGBT 7. generacji typu NX 2in1
Układ scalony IGBT 7. generacji ma ulepszony kompromis napięcia nasycenia kolektor-emiter i strat przełączania wyłączania. Projekt komórki jest zoptymalizowany w celu uzyskania lepszej kontrolowalności dv/dt przez rezystor bramkowy. Poprzez zastosowanie struktury RFC (Relaksujące pole katody) dla diody swobodnej jest również możliwe poprawienie kompromisu między stratami rekuperacji a spadkiem napięcia w przód przez zachowanie łagodnego zachowania rekuperacji [2].
Cechy nowego zestawu układów były oceniane i wykorzystywane do symulacji strat przy użyciu oprogramowania do symulacji MELCOSIM firmy Mitsubishi [1]. Wynik jest taki, że układ IGBT 7. generacji o klasie 1200 V może oszczędzić około 15% całkowitych strat w porównaniu do układu IGBT 6. generacji w typowych warunkach zastosowania falownika do sterowania silnikiem. W celu wsparcia procesu montażu falownika po stronie klienta, wszystkie moduły NX typu 7. generacji będą dostępne z zoptymalizowanymi terminalami PC-TIM i PressFit Pin. Rysunek 8 pokazuje, że ta linia modułów IGBT 7. generacji typu NX z technologią SLC jest w trakcie rozwoju, oferując kompleksowy zestaw produktów wspierających szeroki zakres zastosowań z wykorzystaniem tych nowych technologii.
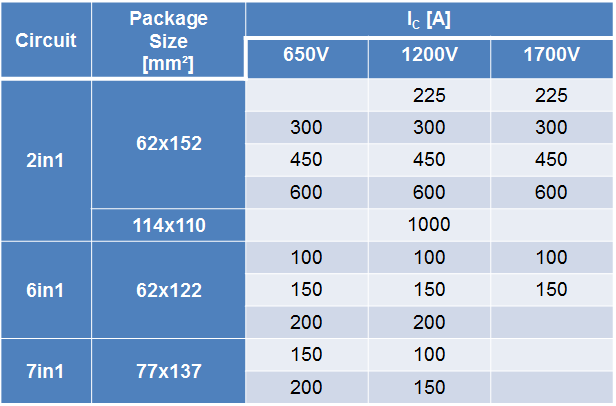
Rysunek 8: Plan linii modułów 7. generacji NX-Type z opcjami PC-TIM i PressFit
Wydajność systemu zestawu układów 7. generacji i technologii SLC
Omówiono cechy zestawu układów 7. generacji z punktu widzenia modułu IGBT. Jednak aby zrozumieć wpływ na system falownika, te cechy muszą zostać ocenione na podstawie profilu misji, który jest reprezentatywny dla typowego trybu pracy falownika. Dla wielu zastosowań muszą być uwzględniane cykle obciążenia w profilu misji. Na podstawie symulacji strat przy użyciu charakterystyk układu scalonego IGBT i diody, ten profil obciążenia można przekształcić w profil strat. Na podstawie tego profilu strat i impedancji termicznej można obliczyć profil temperatury. Ostatecznie można przewidzieć żywotność na podstawie profilu temperatury w połączeniu z krzywymi zdolności cyklicznej modułów [4].
Na Rysunku 9 przedstawiono przykład znormalizowany. Na podstawie symulacji strat za pomocą oprogramowania MELCOSIM zauważono, że całkowite straty zestawu 7. generacji można zmniejszyć o 15% w porównaniu do poprzedniej generacji. Oznacza to, że profil strat zostaje zmniejszony o 15% do 85%. Biorąc pod uwagę tę 15% redukcję strat i około 30% poprawy oporu termicznego, wahania temperatury złącza Tj mogą zostać zmniejszone do 60% w porównaniu do konwencjonalnego modułu z podłożem ceramicznym z tlenku glinu i płytą bazową miedzianą. W przypadku stosowania tych samych strat, wahania temperatury złącza dla konwencjonalnego modułu wynoszą 50 K, a wahania temperatury złącza dla technologii SLC z układem IGBT 7. generacji wynoszą 30 K. Dlatego wynik krzywych zdolności do cyklicznego obciążania przy zmniejszonych wahaniach temperatury złącza jest taki, że można osiągnąć żywotność ponad 10 razy większą w porównaniu do konwencjonalnego modułu, stosując technologię SLC z układem IGBT 7. generacji. Lub w przypadku tej samej żywotności wahania temperatury złącza przy zastosowaniu technologii SLC mogą być zwiększone do około 57 K, co odpowiada zwiększonej mocy wyjściowej o ponad 50%.
Podsumowanie
Została opracowana nowa seria modułów IGBT firmy Mitsubishi o napięciu znamionowym 600 V i 1200 V, obejmująca szeroki zakres prądowy, oparta na dobrze znanych rozwiązaniach w stylu opakowania NX. Nowa seria modułów IGBT łączy najnowszy układ scalony IGBT 7. generacji i FWDi z innowacyjną technologią pakowania o nazwie technologia SLC. Nowa seria modułów IGBT umożliwia projektowanie falowników o wyższych prądach wyjściowych, wyższej gęstości mocy i poprawionej niezawodności (większa żywotność cyklu mocy i większa żywotność cyklu temperatury). Jest doskonałą odpowiedzią na złożone potrzeby nowoczesnych projektów falowników.
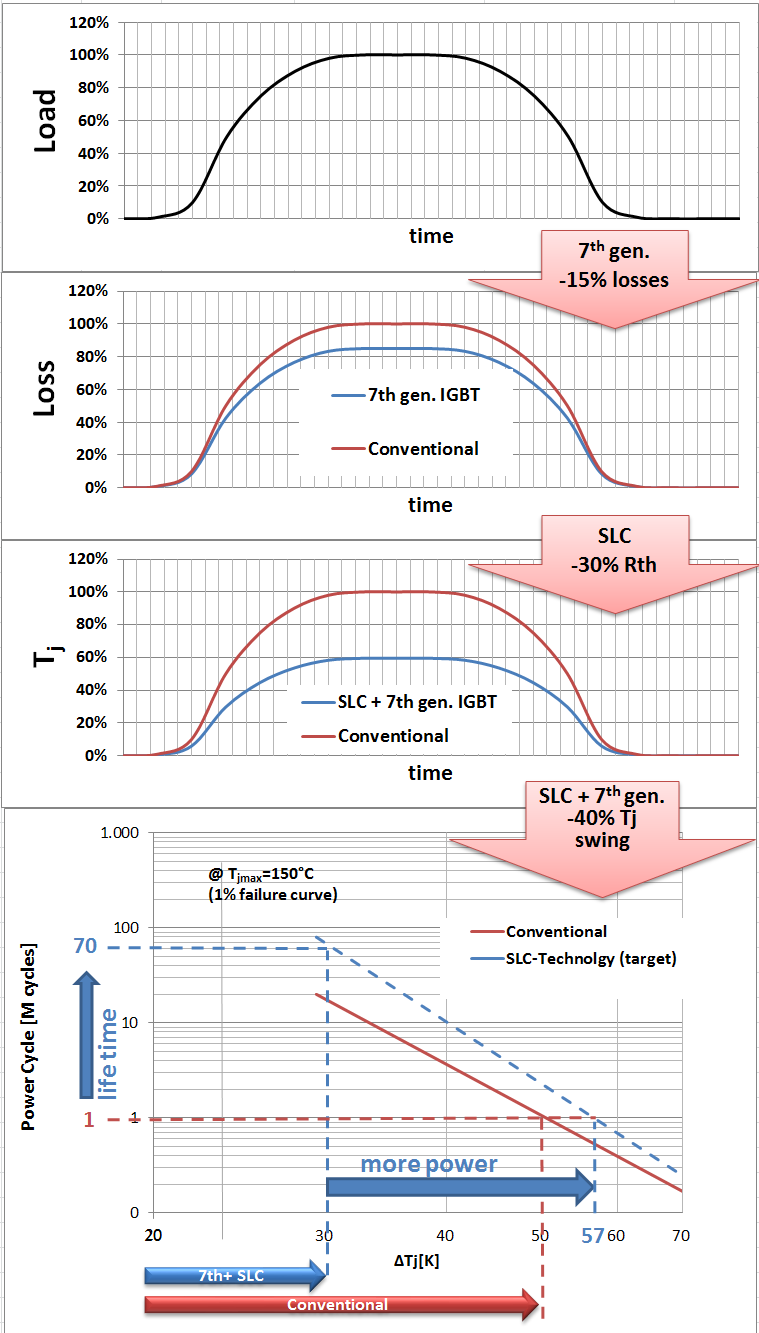
Rysunek 9: Przykład cyklu obciążenia znormalizowanego z porównaniem technologii SLC z 7. generacją IGBT i modułem konwencjonalnym
Odwołania
[1] MELCOSIM: oprogramowanie do symulacji termicznej i strat IGBT, dostępne na stronie www.mitsubishielectric.com/semiconductors/simulator/
[2] T. Radke; K. Masuda: "Zestaw układów IGBT i diodowych 7. generacji umożliwiający moduły o najwyższej wydajności", Bodo's Power Systems, czerwiec 2015, strony 42-35
[3] Kota Ohara i inni: "Nowy moduł IGBT z izolowaną płytą metalową (IMB) i układami 7. generacji", PCIM Europe 2015, strony 1145-1148, ISBN 978-3-8007-3924-0
[4] Notatka aplikacyjna 6.1. generacji serii S1 NX-Type, dostępna na stronie www.mitsubishielectric.com/semiconductors/files/manuals/igbt_ nx_note_e.pdf
Leave a comment