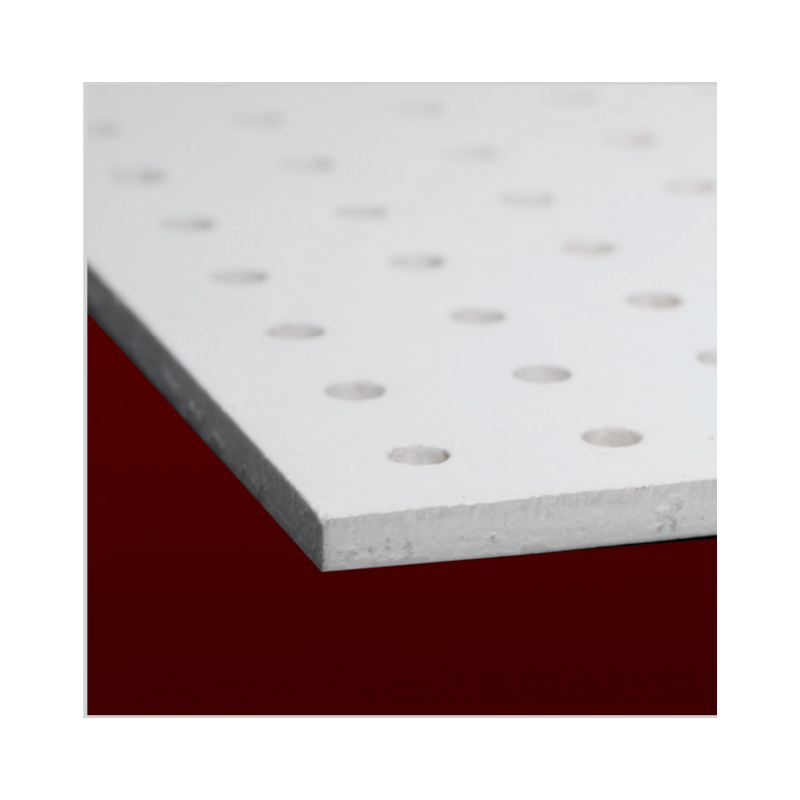
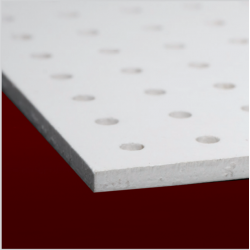
Jūs turite būti prisijungę
Category
Nuotraukos yra skirtos tik informaciniams tikslams. Peržiūrėkite produkto specifikaciją
please use latin characters
Alumina 99.5% porous
Due to the low thermal capacity, the energy demand of the kiln is lower compared to conventional sintered plates. The time and energy required to heat up and cool down the kiln equipment is significantly reduced by using KERAFOL® sintered plates.
Our customers use these sinters to sinter low temperature co-fired ceramics (LTCC), solid oxide fuel cells, dental ceramics, and to debind and sinter metal injection molding (MIM) stainless steel components. The high flatness of Keralpor 99 leads to accurate sintering results. Due to the high porosity of the alumina matrix, gases can easily diffuse through the sinter during the debinding and sintering process.
Parts do not adhere to the sinter during the debinding process. Keralpor 99 works best as a sintered board on furniture made of silicon carbide, mullite, corundum, molybdenum or graphite.
All sizes are available in thicknesses
1,0 / 1,5 / 2,0 mm!
Ask for dimensions tailored to your needs and we will quickly create your Keralpor 99.
Typical features | Unit | Value |
---|---|---|
Color | - | white |
Gross density | g/cm3 | 2,56 |
Surface roughness Ra | µm | 0,7 |
Bending strength | MPa | >50 |
Bend | % | < 0,3 |
Porosity | Vol.% | 36 - 38 |
Average pore size | µm | 1 |
Dimensions | mm | 10 x 10 do 310 x 310 |
Standard thicknesses | mm | 1,0 / 1,5 / 2,0 |
Main ingredients | % | 99,5 Al2O3 |
Maximum operating temperature | Tmax | 1500°C |
Benefits
Usage
Ar Jūs domina šis produktas? Ar Jums reikia papildomos informacijos ar individualaus pasiūlymo?
tu turi būti prisijungęs
Alumina 99.5% porous
Due to the low thermal capacity, the energy demand of the kiln is lower compared to conventional sintered plates. The time and energy required to heat up and cool down the kiln equipment is significantly reduced by using KERAFOL® sintered plates.
Our customers use these sinters to sinter low temperature co-fired ceramics (LTCC), solid oxide fuel cells, dental ceramics, and to debind and sinter metal injection molding (MIM) stainless steel components. The high flatness of Keralpor 99 leads to accurate sintering results. Due to the high porosity of the alumina matrix, gases can easily diffuse through the sinter during the debinding and sintering process.
Parts do not adhere to the sinter during the debinding process. Keralpor 99 works best as a sintered board on furniture made of silicon carbide, mullite, corundum, molybdenum or graphite.
All sizes are available in thicknesses
1,0 / 1,5 / 2,0 mm!
Ask for dimensions tailored to your needs and we will quickly create your Keralpor 99.
Typical features | Unit | Value |
---|---|---|
Color | - | white |
Gross density | g/cm3 | 2,56 |
Surface roughness Ra | µm | 0,7 |
Bending strength | MPa | >50 |
Bend | % | < 0,3 |
Porosity | Vol.% | 36 - 38 |
Average pore size | µm | 1 |
Dimensions | mm | 10 x 10 do 310 x 310 |
Standard thicknesses | mm | 1,0 / 1,5 / 2,0 |
Main ingredients | % | 99,5 Al2O3 |
Maximum operating temperature | Tmax | 1500°C |
Benefits
Usage
Jūsų atsiliepimo įvertinimas negali būti išsiųstas
Pranešti apie komentarą
Pranešimas apie atsiliepimą išsiųstas
Jūsų pranešimas apie atsiliepimą neišsiųstas
Parašyti savo atsiliepimą
Atsiliepimas išsiųstas
Jūsų atsiliepimas neišsiųstas