Jūs turite būti prisijungę
-
sugrįžtiX
-
Komponentai
-
-
Category
-
Puslaidininkiai
- Diodai
- Tiristoriai
-
Elektroizoliuoti moduliai
- Elektrai izoliuoti moduliai | VISHAY (IR)
- Elektrai izoliuoti moduliai | INFINEON (EUPEC)
- Elektrai izoliuoti moduliai | Semikronas
- Elektrai izoliuoti moduliai | POWEREX
- Elektrai izoliuoti moduliai | IXYS
- Elektrai izoliuoti moduliai | POSEICO
- Elektrai izoliuoti moduliai | ABB
- Elektrai izoliuoti moduliai | TECHSEM
- Eikite į subkategoriją
- Lygintuviniai tilteliai
-
Tranzistoriai
- Tranzistoriai | GeneSiC
- SiC MOSFET moduliai | Mitsubishi
- SiC MOSFET moduliai | STARPOWER
- „ABB SiC MOSFET“ moduliai
- IGBT moduliai | MITSUBISHI
- Tranzistorių moduliai | MITSUBISHI
- MOSFET moduliai | MITSUBISHI
- Tranzistorių moduliai | ABB
- IGBT moduliai POWEREX
- IGBT moduliai INFINEON (EUPEC)
- Silicio karbido puslaidininkiniai elementai
- Eikite į subkategoriją
- Valdikliai
- Galios blokai
- Eikite į subkategoriją
- Elektrinių dydžių keitikliai
-
Pasyvūs komponentai (kondensatoriai, rezistoriai, saugikliai, filtrai)
- Rezistoriai
-
Saugikliai
- ABC ir AGC serijos miniatiūriniai saugikliai elektronikai
- Greitaeigiai cilindriniai saugikliai
- Uždelsimo elementai su GL/GG ir AM charakteristikomis
- Ultragreiti intarpai - saugikliai
- Didžiosios Britanijos ir JAV standartų greitaeigiai saugikliai
- Europos standarto greitaeigiai saugikliai
- Saugikliai geležinkeliui
- Aukštos įtampos saugikliai
- Eikite į subkategoriją
-
Kondensatoriai
- Kondensatoriai varikliams
- Elektrolitiniai kondensatoriai
- Snubbers tipo kondensatoriai
- Galios kondensatoriai
- Kondensatoriai DC grandinėms
- Kondensatoriai galios kompensavimui
- Aukštos įtampos kondensatoriai
- Kondensatoriai indukciniam kaitinimui
- Impulsiniai ir energijos kaupimo kondensatoriai
- DC LINK kondensatoriai
- AC / DC grandinių kondensatoriai
- Eikite į subkategoriją
- Slopinimo tinklo filtrai
- Superkondensatoriai
- Apsauga nuo viršįtampių
- TEMPEST spindulių aptikimo filtrai
- Eikite į subkategoriją
-
Relės ir kontaktoriai
- Relių ir kontaktorių teorija
- Trijų fazių puslaidininkinės AC relės
- Puslaidininkinės DC relės
- Reguliatoriai, valdikliai ir jų priedai
- Soft starteriai (minkšto paleidimo įrenginiai) bei reversiniai kontaktoriai
- Elektromechaninės relės
- Kontaktoriai
- Rotaciniai jungikliai
-
Vienos fazės puslaidininkinės AC relės
- AC vienfazės puslaidininkinės relės 1 | D2425 | D2450 serijų
- AC vienfazės puslaidininkinės relės CWA ir CWD serijų
- AC vienfazės puslaidininkinės relės CMRA ir CMRD serijų
- AC vienfazės puslaidininkinės relės PS serijos
- AC puslaidininkinės dvigubos ir keturgubos relės D24 D, TD24 Q, H12D48 D serijų
- Vienfazės puslaidininkinės relės gn serijos
- AC vienfazės puslaidininkinės relės CKR serijos
- AC vienfazės relės DIN bėgiams ERDA ir ERAA serijų
- Vienfazės kintamosios srovės relės, skirtos 150A srovei
- Dvigubos kietojo kūno relės, integruotos su radiatoriumi DIN bėgiui
- Eikite į subkategoriją
- Vienos fazės puslaidininkinės AC relės spausdinimo plokštėms
- Interfejsų relės
- Eikite į subkategoriją
- Indukciniai elementai
- Radiatoriai, varistoriai, termo apsauga
- Ventiliatoriai
- Kondicioneriai, elektros spintų aksesuarai, aušintuvai
-
Baterijos, įkrovikliai, buferiniai maitinimo šaltiniai ir keitikliai
- Baterijos, įkrovikliai - teorinis aprašymas
- Ličio jonų baterijos. Individualios baterijos. Baterijų valdymo sistema (BMS)
-
Akumuliatoriai
- Panasonic įmonės akumuliatoriai
- SSB įmonės akumuliatoriai
- Sonnenschein Dryfit įmonės akumuliatoriai
- MK Battery įmonės geliniai akumuliatoriai
- FIAMM įmonės akumuliatoriai
- Victron Energy akumuliatoriai
- „Victron Energy LiFePO4“ akumuliatoriai
- „Dyno“ baterijos
- APC UPS RBC akumuliatorių paketai
- Eikite į subkategoriją
- Akumuliatorių įkrovikliai ir priedai
- UPS atsarginis maitinimo šaltinis ir buferiniai maitinimo šaltiniai
- Fotoelektros keitikliai ir priedai
- Energijos kaupimas
- Kuro elementai
- Ląstelės litio-joninės
- Eikite į subkategoriją
-
Automatikos komponentai
- Futaba Drone Parts
- Galiniai jungikliai, mikrojungikliai
- Jutikliai, keitikliai
- Pirometrai
- Skaitikliai, laiko relės, paneliniai matuokliai
- Pramoniniai apsaugos įrenginiai
- Šviesos ir garso signalizacija
- Terminio vaizdo kamera
- LED švieslentės
- Valdymo aparatūra - mygtukai ir jungikliai
- Eikite į subkategoriją
-
Laidai, pynės, laidų apsauginės žarnos, lankstūs sujungimai
- Laidai
- Daugiagisliai laidai
-
Kabeliai ekstremalioms sąlygoms
- Kompensaciniai ir prailginimo kabeliai
- Laidai termoporoms
- PT jutikliams prijungimo laidai
- Daugiagysliai laidai temp. -60C iki +1400C
- Vidutinės įtampos kabeliai
- Uždegimo laidai
- Šildymo laidai
- Viengysliai laidai temp. -60C iki +450C
- Geležinkelio kabeliai
- Šildymo kabeliai Ex zonoms
- Eikite į subkategoriją
- Apsaugos vamzdeliai
-
Pintinės
- Plokščios pintinės
- Apvalios pintinės
- Plokščios labai elastingos pintinės
- Apvalios labai elastingos pintinės
- Cilindro formos vario pintinės
- Vario cilindrinės pintinės su apsauga
- Elastingos įžeminimo juostos
- Cinkuoto ir nerūdijančio plieno cilindrinės pintinės
- PCV izoliuotos vario pintinės - temperatūra iki 85 C
- Plokščios aliuminio pintinės
- Sujungimo komplektas - pintinės ir vamzdeliai
- Eikite į subkategoriją
- Aksesuarai geležinkeliams
- Kabelių antgaliai
- Lanksčios izoliuotos šynos
- Daugiasluoksnės lanksčios šynos
- Laidų pravedimo sistemos (PESZLE)
- Eikite į subkategoriją
- Žiūrėti visas kategorijas
-
Puslaidininkiai
-
-
- Tiekėjai
-
Pritaikymų sąrašas
- CNC staklės
- Energetika
- Energy bank
- Indukcinis kaitinimas
- Įranga ir komponentai sprogimo pavojaus zonoms (Ex)
- Kasyklos, metalurgijos ir liejimo pramonė
- Laboratoriniai ir moksliniai matavimai
- Maitinimo šaltiniai (UPS) ir lygintuvinės sistemos
- Medienos džiovinimo ir apdirbimo mašinos
- Nuolatinės ir kintamos srovės pavaros (keitikliai)
- Paskirstymo, valdymo ir telekomunikacijos spintų įranga
- Plastmasių liejimo mašinos
- Poligrafija
- Pramoninė apsaugos įranga
- Pramoninė automatika
- Suvirinimo aparatai
- ŠVOK automatika
- Temperatūros matavimas ir nustatymas
- Tramvajų ir traukinių pavaros
- Varikliai ir transformatoriai
-
Montavimas
-
-
Induktoriai
-
-
Indukciniai įtaisai
-
-
Aptarnavimas
-
- Kontaktai
- Zobacz wszystkie kategorie
The use of induction heating in the manufacture of industrial equipment
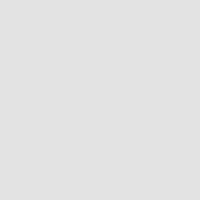
Induction heating is a method of heating conductive materials that is gaining more and more popularity in industrial applications. Compared to conventional heating methods, induction heating provides the highest safety for workers through contact-free operation.
The technology is developing rapidly and there are more and more solutions and devices using it on the market. The vast majority of companies decide to switch to such a solution, due to the savings of time and money associated with heating processes.
What is induction heating?
Induction heating is a method of heating conductive materials used in the production and machining of mechanical parts or industrial machine components. The process involves placing the workpiece near an induction coil through which an alternating current is passed. As the current flows through the coil, an alternating magnetic field is generated in its field, which initiates eddy currents within the workpiece material. Unlike common heating methods, in induction the heat is not supplied from outside, but is generated in the workpiece itself. This gives many advantages for production processes, energy consumption and working conditions.
The benefits of induction heating:
- Saves energy and reduces CO₂ emissions, thanks to short heating times;
- All induction processes are easily repeatable;
- Precision heating significantly reduces scrap and rework;
- Ability to automate and integrate with other manufacturing processes;
- Even the largest induction systems take up relatively little space;
- Induction processes are easy to use;
- Each solution can be easily selected and adapted to each application.
Induction heating systems
Each induction heating system consists of an induction generator, a workstation and an induction coil. Additionally, depending on the application, peripheral devices supporting the system operation can be added, such as chillers for the coil cooling water, pyrometers for measuring the heating temperature, industrial regulators for controlling the generator operation.
Induction generators are responsible for converting input current into alternating current at a specific frequency. By selecting the appropriate power and frequency range of the generator, we can adjust the heating time and heat penetration depth of the heat-treated material, depending on the size and weight of the work insert.
Workstations are components of a heating system in which induction coils are placed. Depending on the solution, the workstation may be built into the generator or may exist as an independent part of the unit to facilitate equipment operation. In most cases, cooling water also flows through the workstation and is then directed to the heating coil.
The coil itself is the element through which heat is generated in the workpiece. By selecting the size, shape and design of the coil, we can achieve different types of heating - from spot heating to area heating. The coils are usually made of copper, because copper conducts electricity very well, and by using a cooling system, we can reduce excessive heating of the coil.
Induction heating applications
- Induction heating is used in many heating processes. The most important of these are:
- Soldering and brazing;
- Heating, bonding;
- Shrink fitting;
- Annealing, hardening, tempering and curing;
- Melting and hot forming;
- Forging;
- Stacking;
- Sealing;
- Glaze removal;
- Material testing.
Except for the aforementioned applications, induction heating is used in high-tech applications where specific standards and high hygiene are required, e.g. medical applications (nanoparticle technology), chemical industry, etc.
Related products
Related posts
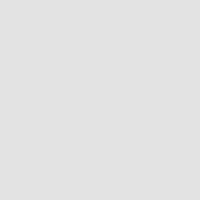
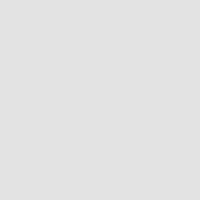
Leave a comment