Musisz być zalogowany/a
-
WróćX
-
Podzespoły
-
-
Category
-
Półprzewodniki
- Diody
-
Tyrystory
- Tyrystory firmy VISHAY (IR)
- Tyrystory firmy LAMINA
- Tyrystory firmy INFINEON (EUPEC)
- Tyrystory firmy ESTEL
- Tyrystory firmy WESTCODE
- Tyrystory firmy Semikron
- Tyrystory firmy POWEREX
- Tyrystory firmy DYNEX
- Tyrystory do grzejnictwa indukcyjnego
- Tyrystory firmy ABB
- Tyrystory firmy TECHSEM
- Przejdź do podkategorii
-
Moduły elektroizolowane
- Moduły elektroizolowane firmy VISHAY (IR)
- Moduły elektroizolowane firmy INFINEON (EUPEC)
- Moduły elektroizolowane firmy Semikron
- Moduły elektroizolowane firmy POWEREX
- Moduły elektroizolowane firmy IXYS
- Moduły elektroizolowane firmy POSEICO
- Moduły elektroizolowane firmy ABB
- Moduły elektroizolowane firmy TECHSEM
- Przejdź do podkategorii
- Mostki prostownicze
-
Tranzystory
- Tranzystory firmy GeneSiC
- Moduły SiC MOSFET firmy Mitsubishi
- Moduły SiC MOSFET firmy STARPOWER
- Moduły SiC MOSFET firmy ABB
- Moduły IGBT firmy MITSUBISHI
- Moduły tranzystorowe firmy MITSUBISHI
- Moduły MOSFET firmy MITSUBISHI
- Moduły tranzystorowe firmy ABB
- Moduły IGBT firmy POWEREX
- Moduły IGBT - firmy INFINEON (EUPEC)
- Elementy półprzewodnikowe z węglika krzemu
- Przejdź do podkategorii
- Sterowniki
- Bloki mocy
- Przejdź do podkategorii
- Przetworniki prądowe i napięciowe LEM
-
Elementy pasywne (kondensatory, rezystory, bezpieczniki, filtry)
- Rezystory
-
Bezpieczniki
- Bezpieczniki miniaturowe do układów elektronicznych seria ABC i AGC
- Bezpieczniki szybkie rurkowe
- Wkładki zwłoczne o charakterystykach GL/GG oraz AM
- Wkładki topikowe ultraszybkie
- Bezpieczniki szybkie standard brytyjski i amerykański
- Bezpieczniki szybkie standard europejski
- Bezpieczniki trakcyjne
- Wkładki bezpiecznikowe wysokonapięciowe
- Przejdź do podkategorii
-
Kondensatory
- Kondensatory do silników
- Kondensatory elektrolityczne
- Kondensatory foliowe Icel
- Kondensatory mocy
- Kondensatory do obwodów DC
- Kondensatory do kompensacji mocy
- Kondensatory wysokonapięciowe
- Kondensatory do grzejnictwa indukcyjnego
- Kondensatory impulsowe
- Kondensatory DC LINK
- Kondensatory do obwodów AC/DC
- Przejdź do podkategorii
- Filtry przeciwzakłóceniowe
- Superkondensatory
-
Zabezpieczenia przeciwprzepięciowe
- Ograniczniki przepięć dla aplikacji RF
- Ograniczniki przepięć dla systemów wizyjnych
- Ograniczniki przepięć linii zasilających
- Ograniczniki przepięć do LED
- Ograniczniki przepięć do Fotowoltaiki
- Ograniczniki przepięć dla systemów wagowych
- Ograniczniki przepięć dla magistrali Fieldbus
- Przejdź do podkategorii
- Filtry emisji ujawniającej TEMPEST
- Przejdź do podkategorii
-
Przekaźniki i Styczniki
- Teoria przekaźniki i styczniki
- Przekaźniki półprzewodnikowe AC 3-fazowe
- Przekaźniki półprzewodnikowe DC
- Regulatory, układy sterujące i akcesoria
- Soft starty i styczniki nawrotne
- Przekaźniki elektromechaniczne
- Styczniki
- Przełączniki obrotowe
-
Przekaźniki półprzewodnikowe AC 1-fazowe
- Przekaźniki półprzewodnikowe AC jednofazowe serii 1 | D2425 | D2450
- Przekaźniki półprzewodnikowe AC jednofazowe serii CWA I CWD
- Przekażniki półprzewodnikowe AC jednofazowe serii CMRA I CMRD
- Przekaźniki półprzewodnikowe AC jednofazowe serii PS
- Przekaźniki półprzewodnikowe AC podwójne i poczwórne serii D24 D, TD24 Q, H12D48 D
- 1-fazowe przekaźniki półprzewodnikowe serii gn
- Przekaźniki półprzewodnikowe ac jednofazowe serii ckr
- Przekaźniki AC jednofazowe na szynę din SERII ERDA I ERAA
- Przekaźniki jednofazowe AC na prąd 150A
- Podwójne przekaźniki półprzewodnikowe zintegrowane z radiatorem na szynę DIN
- Przejdź do podkategorii
- Przekaźniki półprzewodnikowe AC 1-fazowe do druku
- Przekaźniki interfejsowe
- Przejdź do podkategorii
- Rdzenie oraz inne elementy indukcyjne
- Radiatory, Warystory, Zabezpieczenia termiczne
- Wentylatory
- Klimatyzacja, Osprzęt do szaf rozdzielczych, Chłodnice
-
Akumulatory, ładowarki, zasilacze buforowe i przetwornice
- Akumulatory, ładowarki - opis teoretyczny
- Baterie litowo-jonowe. Niestandardowe baterie. System zarządzania baterią (BMS)
- Akumulatory
- Ładowarki akumulatorów i akcesoria
- Zasilacze UPS i zasilacze buforowe
- Przetwornice i osprzęt do fotowoltaiki
- Magazyny energii
- Wodorowe ogniwa paliwowe
- Ogniwa litowo-jonowe
- Przejdź do podkategorii
-
Automatyka
- Części do dronów Futaba
- Wyłączniki krańcowe, Mikrowyłączniki
- Czujniki, Przetworniki
- Pirometry
- Liczniki, Przekaźniki czasowe, Mierniki tablicowe
- Przemysłowe urządzenia ochronne
- Sygnalizacja świetlna i dźwiękowa
- Kamera termowizyjna
- Wyświetlacze LED
- Przyciski i przełączniki
-
Rejestratory
- Rejestrator AL3000
- Rejestrator KR2000
- Rejestrator KR5000
- Miernik z funkcją rejestracji wilgotności i temperatury HN-CH
- Materiały eksploatacyjne do rejestratorów
- Rejestrator 71VR1
- Rejestrator KR 3000
- Rejestratory PC serii R1M
- Rejestratory PC serii R2M
- Rejestrator PC, 12 izolowanych wejść – RZMS-U9
- Rejestrator PC, USB, 12 izolowanych wejść – RZUS
- Przejdź do podkategorii
- Przejdź do podkategorii
-
Przewody, Lica, Peszle, Połączenia elastyczne
- Druty
- Lica
-
Kable do zastosowań specjalnych
- Przewody przedłużające i kompensujące
- Przewody do termopar
- Przewody podłączeniowe do czyjnków PT
- Przewody wielożyłowe temp. -60°C do +1400°C
- SILICOUL przewody średniego napięcia
- Przewody zapłonowe
- Przewody grzejne
- Przewody jednożyłowe temp. -60°C do +450°C
- Przewody kolejowe
- Przewody grzejne w Ex
- Przewody dla przemysłu obronnego
- Przejdź do podkategorii
- Koszulki
-
Plecionki
- Plecionki płaskie
- Plecionki okrągłe
- Bardzo giętkie plecionki - płaskie
- Bardzo giętkie plecionki - okrągłe
- Miedziane plecionki cylindryczne
- Miedziane plecionki cylindryczne i osłony
- Paski uziemiające giętkie
- Plecionki cylindryczne z ocynkowanej i nierdzewnej stali
- Miedziane plecionki izolowane PCV - temperatura do 85 stopni C
- Płaskie plecionki aluminiowe
- Zestaw połączeniowy - plecionki i rurki
- Przejdź do podkategorii
- Osprzęt dla trakcji
- Końcówki kablowe
- Szyny elastyczne izolowane
- Wielowarstwowe szyny elastyczne
- Systemy prowadzenia kabli
- Peszle, rury
- Przejdź do podkategorii
- Zobacz wszystkie kategorie
-
Półprzewodniki
-
-
- Dostawcy
-
Aplikacje
- Automatyka HVAC
- Automatyka przemysłowa
- Banki energii
- Energetyka
- Górnictwo, hutnictwo i odlewnictwo
- Maszyny do suszenia i obróbki drewna
- Maszyny do termo-formowania tworzyw sztucznych
- Nagrzewanie indukcyjne
- Napędy prądu stałego i przemiennego (falowniki)
- Obrabiarki CNC
- Podzespoły do stref zagrożonych wybuchem (EX)
- Poligrafia
- Pomiar i regulacja temperatury
- Pomiary badawcze i laboratoryjne
- Przemysłowe urządzenia ochronne
- Silniki i transformatory
- Spawarki i zgrzewarki
- Trakcja tramwajowa i kolejowa
- Wyposażenie do szaf rozdzielczych i sterowniczych
- Zasilacze (UPS) i układy prostownikowe
-
Montaż
-
-
Induktory
-
-
Urządzenia indukcyjne
-
-
Serwis i naprawy
-
- Kontakt
- Zobacz wszystkie kategorie
Zaawansowany projekt układu scalonego Si-IGBT dla maksymalnej wydajności całego systemu
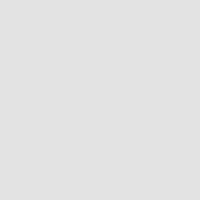
Zaawansowany projekt układu scalonego Si-IGBT dla maksymalnej wydajności całego systemu
Ogólna wydajność systemu jest bez wątpienia w znacznym stopniu uzależniona od wyboru zastosowanej technologii półprzewodnikowej. W przypadku konwencjonalnych modułów IGBT, niedawne postępy w zakresie stosunku VCEsat do Eoff pokazują tendencję do nasycenia, co oznacza, że poprawki wydajności w kolejnych generacjach układów IGBT nie wskazują już na znaczący krok w poprawie efektywności. Dzięki nowej serii układów G1-IPM możliwe jest uzyskanie znacznej poprawy efektywności systemu poprzez zastosowanie zaawansowanego układu Si-IGBT i wprowadzenie adaptacyjnego sterowania bramkowego.
Autorzy: Narender Lakshmanan i Thomas Radke, Mitsubishi Electric Europe B.V.
Wstęp:
Mitsubishi Electric wprowadził na rynek nową serię inteligentnych modułów mocy (IPM) G1 z zaawansowanym układem Si-IGBT, aby rozwiązać kilka kluczowych parametrów wydajnościowych i umożliwić użytkownikowi końcowemu osiągnięcie wysokiej wydajności systemu. Postępy w technologii chipów G1 IPM mają na celu rozwiązanie niektórych wrodzonych wad Si-IGBT, zwłaszcza w przypadku zastosowań sterowania silnikiem. Układ G1 IPM został opracowany poprzez wdrożenie kilku kluczowych innowacji w najnowszej 7. generacji układu IGBT. Można zauważyć (patrz Rysunek 1), że w porównaniu do konwencjonalnego układu Si-IGBT 7. generacji, zaawansowana technologia chipu G1 IPM oferuje znaczne korzyści, chociaż należy do tej samej generacji chipów.
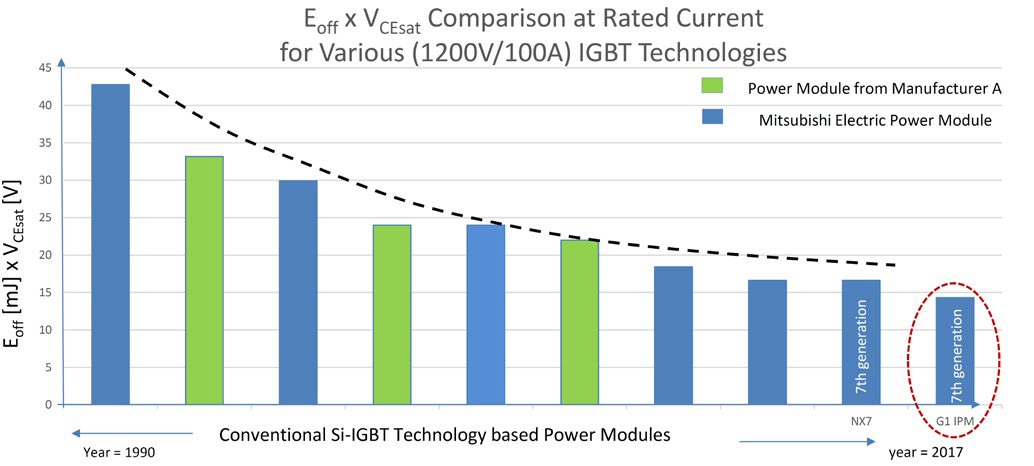
Rysunek 1: Porównanie wskaźnika VCEsat x EOFF dla różnych technologii Si-IGBT
Zdolność do zwarcia i wydajność elektryczna:
Ochrona przed zwarciem dla konwencjonalnego układu Si-IGBT została zaimplementowana za pomocą systemu opartego na „wykrywaniu desaturacji”, w którym obserwuje się napięcie VCE na IGBT w celu potwierdzenia wystąpienia zwarcia. Aby umożliwić skuteczne wykrycie, konwencjonalne układy Si-IGBT są projektowane w taki sposób, że wiele komórek bramkowych w chipie pozostaje niepodłączonych [6][2]. Chociaż zapewnia to, że IGBT wchodzi w tryb desaturacji powyżej określonej wartości IC, oznacza to również, że kilka parametrów elektrycznych jest pewnym stopniu kompromisowych [6][2][3]. Układ G1 IPM posiada chip Si-IGBT z monolitycznie zintegrowanym emiterem prądu (patrz Rysunek 2). Cechą emitera prądu jest umożliwienie oceny prądu kolektora IGBT poprzez bezpośrednie pomiar. Na podstawie informacji z emitera prądu można przypisać poziomy przerwy i rozpocząć wyłączanie SC przed desaturacją chipu. To podejście do bezpośredniego określania chwilowego IC czyni system oparty na wykrywaniu desaturacji na podstawie VCE przestarzałym. Nie jest już konieczne zapewnienie, że IGBT przechodzi w tryb desaturacji. Bezpośrednim skutkiem tego jest to, że wszystkie dostępne komórki bramkowe w chipie Si-IGBT mogą być połączone, co przekształca chip w „pełny IGBT” i pozwala na wykorzystanie korzyści elektrycznych wynikających z większego wykorzystania chipa Si-IGBT [1]. Ponadto, chip IGBT jest wyposażony w diodę czujnika temperatury na chipie, umieszczoną centralnie na chipie, w celu skutecznego określenia temperatury złącza IGBT (patrz Rysunek 2).
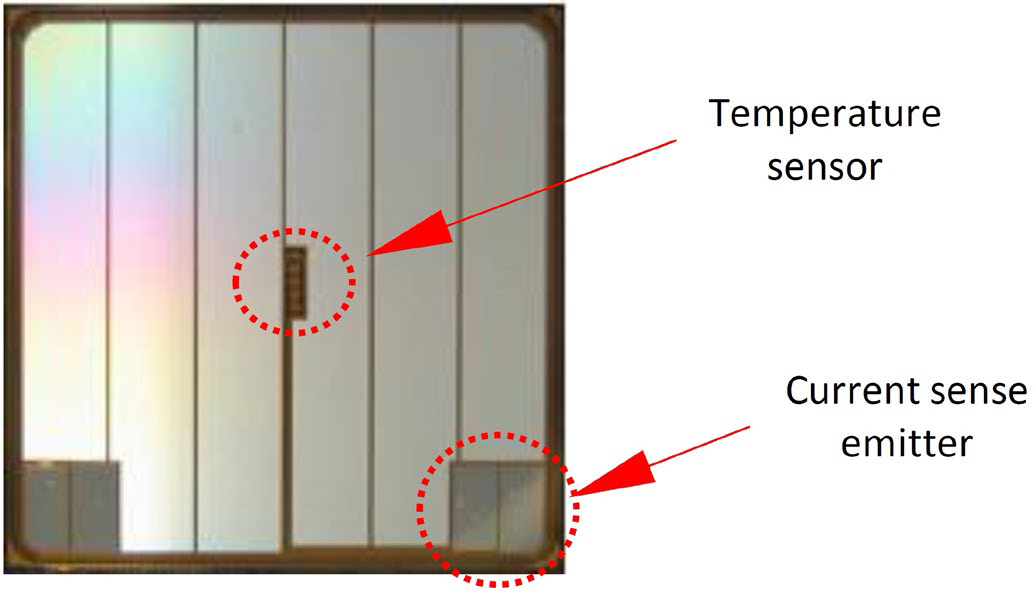
Rysunek 2: Czujnik temperatury i komponent emitera prądu na chipie IGBT w G1-IPM
Szybkość zmiany napięcia (dv/dt) jako czynnik ograniczający wydajność:
Jednym z czynników negatywnie wpływających na żywotność warstw izolacyjnych w systemie (izolacja uzwojenia silnika lub izolacja kabla) jest ekspozycja na wysokie prędkości przejściowe napięć (dv/dt). Zdarzenie przełączania IGBT jest zdolne do generowania wysokiego dv/dt na zaciskach modułu mocy (szczególnie podczas zdarzenia włączania). Konwencjonalnym rozwiązaniem tego problemu jest ograniczenie prędkości przełączania IGBT poprzez zastosowanie impedancji bramkowej tak, aby dv/dt przełączania było utrzymywane poniżej określonego poziomu. Charakterystyka dv/dt vs IC jest taka, że najwyższe dv/dt (najgorszy przypadek dv/dt) występuje podczas włączania przy niskim IC, a dv/dt włączania zmniejsza się wraz ze wzrostem IC. Chociaż najgorszy przypadek dv/dt generowany jest tylko podczas włączania przy niskim IC, konwencjonalny sterownik bramkowy z ustalonymi rezystorami włączania bramki wymusi ograniczenie prędkości przełączania dla wszystkich wartości IC. Takie podejście generuje znaczne straty włączania przy pracy przy wysokim IC, nawet jeśli dv/dt przełączania nie jest najgorszym przypadkiem podczas pracy przy wysokim IC. Jasne jest więc, że dla konwencjonalnej technologii Si-IGBT istnieje kompromis między kontrolą najgorszego przypadku dv/dt a wydajnością.
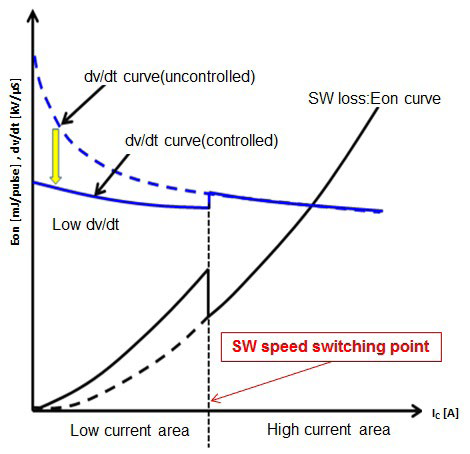
Rysunek 3: Wykorzystanie emitera prądu do implementacji kontroli prędkości przełączania w G1 IPM
Wykorzystanie emitera prądu do kontroli dv/dt bez uszczerbku dla wydajności:
Dostęp do emitera prądu w zaawansowanym układzie Si-IGBT otwiera możliwość określenia IC. Na podstawie zależności dv/dt vs IC wynika, że w celu skierowania najgorszego przypadku dv/dt, odpowiednie jest wprowadzenie ograniczenia prędkości przełączania tylko podczas przełączania przy niskim IC. Zgodnie z tym kluczowym punktem, w układach G1 IPM Si-IGBT zastosowano technikę przełączania, w której prędkość przełączania włączania jest regulowana na podstawie IC. Jeśli IC (na podstawie danych z emitera prądu) zostanie ustalone jako niższe niż określony próg, jednostka napędu bramki zostanie poinformowana o zastosowaniu ograniczenia prędkości przełączania, aby uniknąć najgorszego przypadku dv/dt. Gdy prąd IC przekroczy predefiniowaną wartość progową, jednostka napędu bramki zostanie poinformowana o włączeniu IGBT z wyższą prędkością przełączania, tak aby można było zoptymalizować straty włączania. Dzięki temu podejściu unika się najgorszego przypadku dv/dt podczas przełączania, jednocześnie zapewniając, że efektywność systemu nie jest kompromitowana (patrz Rysunek 3).
Pełny IGBT z emiterem prądu - Analiza ogólnej wydajności:
Moduł G1 IPM wykorzystuje pełny IGBT 7. generacji wyposażony w monolitycznie zintegrowany emiter prądu. To podejście ma na celu połączenie korzyści płynących z pełnego IGBT wraz z zaletami komponentu emitera prądu. Celem jest zapewnienie maksymalnej wydajności, wysokiej niezawodności (ochrona SC oparta na chwilowym prądzie IC) i akceptowalnego profilu EMI (kontrola dv/dt). Rysunek 4 przedstawia porównanie całkowitej straty mocy całkowitej układu dla pełnego bramkowego układu 7. generacji z konwencjonalnym układem Si-IGBT (przy tej samej wartości dv/dt podczas włączania). Jak wynika z Ryciny 4, układ pełnego IGBT generuje około 18% mniejsze straty ogólne niż układ konwencjonalny podczas wymienionych warunków pracy.
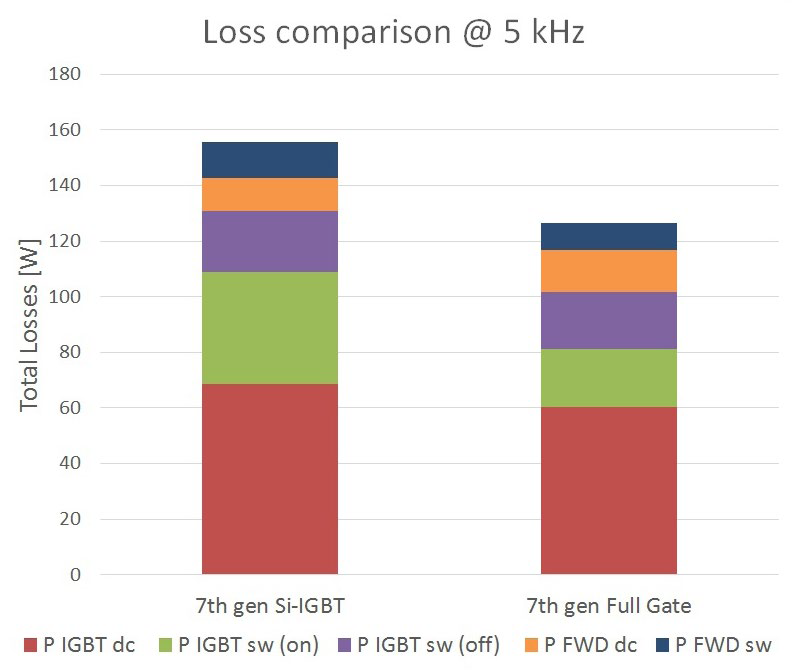
Rysunek 4: Porównanie całkowitej straty mocy generowanej przez pojedyncze połączenie IGBT + dioda w układzie pełnej bramki 7. generacji (100A/1200V) i 7. generacji Si-IGBT (100A/1200V) dla warunków: VCC = 600V, Iout = 100 A rms, fC = 5 kHz, m = 1, cos(φ) = 0,8, TS = 80°C, fo = 50 Hz
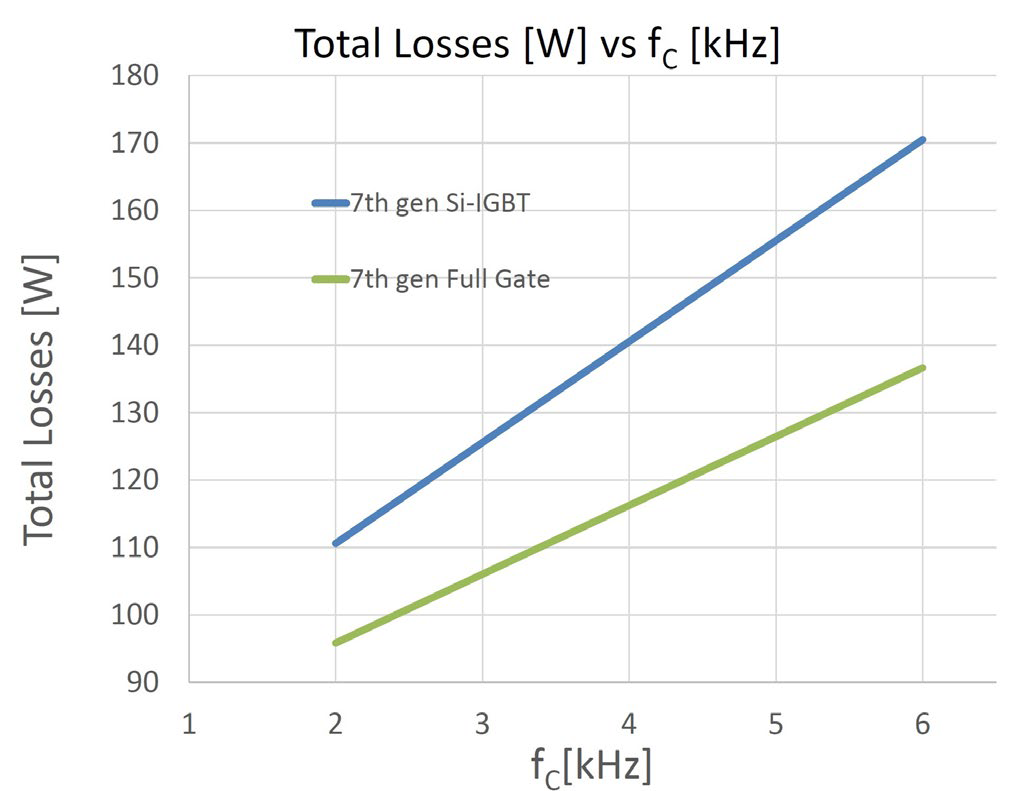
Rysunek 5: Porównanie całkowitych strat generowanych w pojedynczym połączeniu IGBT + dioda w układzie pełnej bramki 7. generacji (100A/1200V) i 7. generacji Si-IGBT (100A/1200V) dla kilku częstotliwości przełączania. Warunki: VCC = 600V, Iout = 100 Arms, m = 1, cos (φ) = 0,8, Ts = 80°C, fo = 50 Hz
W warunkach wymienionych na Rysunku 4, technika kontroli prędkości przełączania pozwala na redukcję strat włączania o 48%. Pełne IGBT (z emiterem prądu) wyraźnie generuje znacznie mniejsze straty przełączania w porównaniu do swojego konwencjonalnego odpowiednika. Rysunek 5 przedstawia całkowitą stratę mocy w zależności od fC (częstotliwość przełączania) dla pełnego IGBT (z emiterem prądu) i układu konwencjonalnego Si-IGBT. Różnica w wydajności między pełnym IGBT (z emiterem prądu) a konwencjonalnym Si-IGBT wzrasta wraz ze wzrostem fC.
Dla aplikacji, które wymagają pracy przy niskim poziomie hałasu słyszalnego (wymagane są wysokie częstotliwości przełączania), 7. generacja pełnego IGBT (z emiterem prądu) obiecuje ogromne korzyści na poziomie systemu. Istnieją pewne punkty przeciążenia dla aplikacji sterowania silnikiem. Podczas bezruchu (silnik zablokowany) - prąd obciążenia nie jest równomiernie rozłożony między IGBT w falowniku, a podczas bardzo niskich częstotliwości wyjściowych - IGBT w falowniku mogą doświadczyć wysokiej pulsacji prądu. W takich warunkach przeciążenia istotne jest określenie temperatur złączy IGBT każdego chipa, aby uniknąć awarii związanej z przegrzaniem. Temperaturę złącza IGBT można skutecznie monitorować za pomocą wbudowanego czujnika temperatury na każdym chipie.
Można zatem stwierdzić, że pełny IGBT wyposażony w emiter prądu i czujnik temperatury rozwiązuje kilka kluczowych problemów związanych z konwencjonalnym podejściem Si-IGBT, co pozwala deweloperowi falownika osiągnąć znacznie wyższą wydajność systemu.
Źródła:
[1] An Advanced Si-IGBT Chip for Delivering Maximum Overall System Performance, Narender Lakshmanan i Thomas Radke, Proc. PCIM 2017
[2] USING F-SERIES IGBT MODULES, MITSUBISHI ELECTRIC. Nota aplikacyjna. Luty 2000
[3] New chip design technology for next generation power module. Katsumi Satoh i inni, Proc. PCIM 2008
[4] A 6-in-1 IGBT module performance evaluation platform determining the trade-off between dV/dt and turn-on loss of different IGBT/FwDi chip setups, Marco Honsberg i inni, Proc. EPE 2011
[5] Karta danych - CM100TX-24T
[6] A Novel Series of Intelligent Power Modules “V1” with Internally Paralleled FULL GATE CSTBTTM and mirror Emitter technology for short circuit sensing, Nishida Nobuya i inni, Proc. PCIM 2010
Powiązane posty
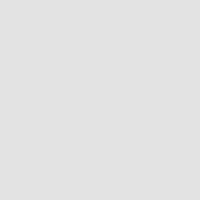
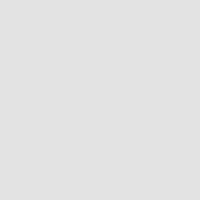
Dodaj komentarz