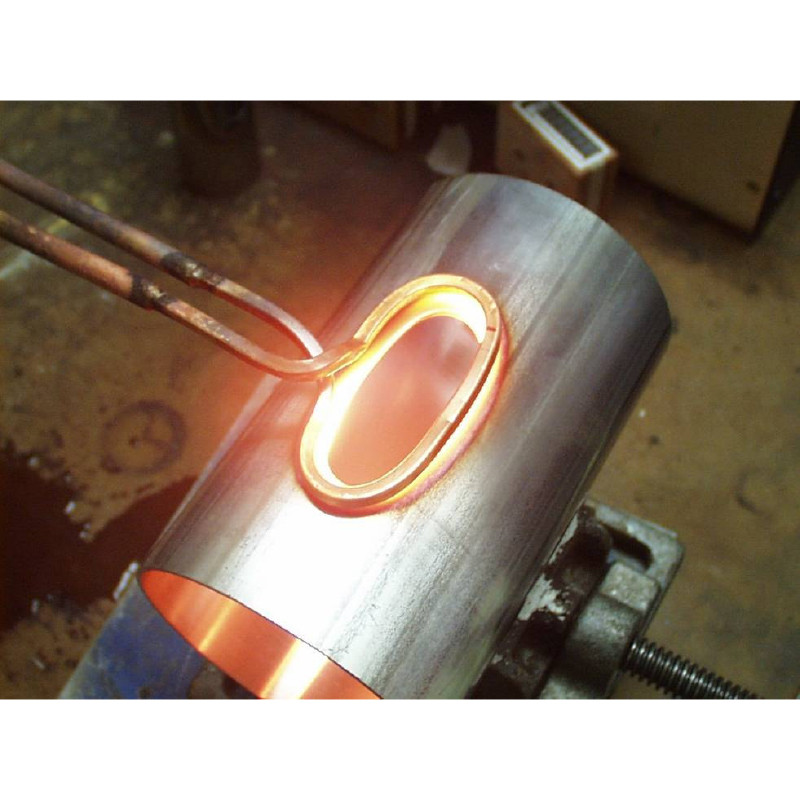
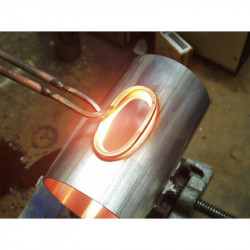
trebuie să fii logat
Category
Fotografiile au doar scop informativ. Vizualizați specificațiile produsului
please use latin characters
Objective: To anneal a ¼” area around an oval cutout on a stainless steel tube prior to extrusion.
Frequency: 300 kHz
Material: .75” (19mm), 1.5” (38.1mm) and 4” (101.6mm) diameter steel tubes
Temperature: 1900 °F (1038 °C)
A single turn helical coil is used on the 4” (101.6mm) diameter tubes and a two turn helical coil is used on the smaller diameters. The coil is placed over the oval cutout and power is supplied for 15 seconds to anneal a 0.25" (6.35mm) diameter around the cutout.
Sunteți interesat de acest produs? Aveți nevoie de informații suplimentare sau de prețuri individuale?
trebuie să fii logat
Objective: To anneal a ¼” area around an oval cutout on a stainless steel tube prior to extrusion.
Frequency: 300 kHz
Material: .75” (19mm), 1.5” (38.1mm) and 4” (101.6mm) diameter steel tubes
Temperature: 1900 °F (1038 °C)
A single turn helical coil is used on the 4” (101.6mm) diameter tubes and a two turn helical coil is used on the smaller diameters. The coil is placed over the oval cutout and power is supplied for 15 seconds to anneal a 0.25" (6.35mm) diameter around the cutout.
Aprecierea ta pentru recenzie nu a putut fi trimisa
Reclama un comentariu
Raport trimis
Reclamatia tau nu a putut fi trimisa
Scrie-ti recenzia
Recenzia a fost trimisa
Recenzia ta nu a putut fi trimisa