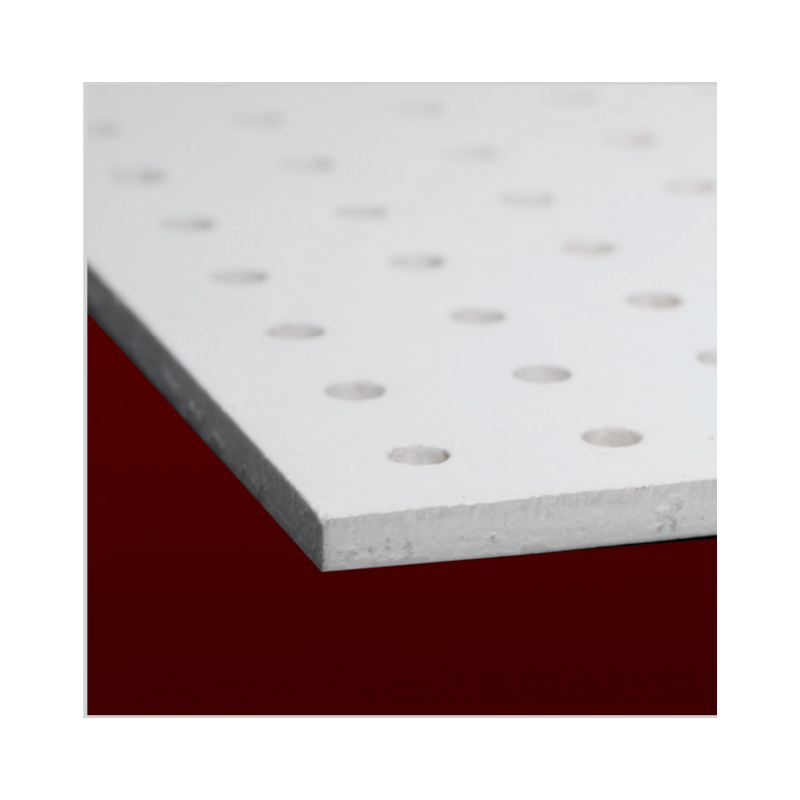
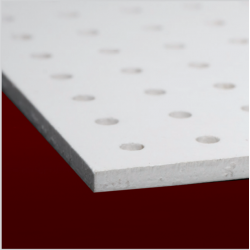
trebuie să fii logat
Category
Fotografiile au doar scop informativ. Vizualizați specificațiile produsului
please use latin characters
Alumina 99.5% porous
Due to the low thermal capacity, the energy demand of the kiln is lower compared to conventional sintered plates. The time and energy required to heat up and cool down the kiln equipment is significantly reduced by using KERAFOL® sintered plates.
Our customers use these sinters to sinter low temperature co-fired ceramics (LTCC), solid oxide fuel cells, dental ceramics, and to debind and sinter metal injection molding (MIM) stainless steel components. The high flatness of Keralpor 99 leads to accurate sintering results. Due to the high porosity of the alumina matrix, gases can easily diffuse through the sinter during the debinding and sintering process.
Parts do not adhere to the sinter during the debinding process. Keralpor 99 works best as a sintered board on furniture made of silicon carbide, mullite, corundum, molybdenum or graphite.
All sizes are available in thicknesses
1,0 / 1,5 / 2,0 mm!
Ask for dimensions tailored to your needs and we will quickly create your Keralpor 99.
Typical features | Unit | Value |
---|---|---|
Color | - | white |
Gross density | g/cm3 | 2,56 |
Surface roughness Ra | µm | 0,7 |
Bending strength | MPa | >50 |
Bend | % | < 0,3 |
Porosity | Vol.% | 36 - 38 |
Average pore size | µm | 1 |
Dimensions | mm | 10 x 10 do 310 x 310 |
Standard thicknesses | mm | 1,0 / 1,5 / 2,0 |
Main ingredients | % | 99,5 Al2O3 |
Maximum operating temperature | Tmax | 1500°C |
Benefits
Usage
Sunteți interesat de acest produs? Aveți nevoie de informații suplimentare sau de prețuri individuale?
trebuie să fii logat
Alumina 99.5% porous
Due to the low thermal capacity, the energy demand of the kiln is lower compared to conventional sintered plates. The time and energy required to heat up and cool down the kiln equipment is significantly reduced by using KERAFOL® sintered plates.
Our customers use these sinters to sinter low temperature co-fired ceramics (LTCC), solid oxide fuel cells, dental ceramics, and to debind and sinter metal injection molding (MIM) stainless steel components. The high flatness of Keralpor 99 leads to accurate sintering results. Due to the high porosity of the alumina matrix, gases can easily diffuse through the sinter during the debinding and sintering process.
Parts do not adhere to the sinter during the debinding process. Keralpor 99 works best as a sintered board on furniture made of silicon carbide, mullite, corundum, molybdenum or graphite.
All sizes are available in thicknesses
1,0 / 1,5 / 2,0 mm!
Ask for dimensions tailored to your needs and we will quickly create your Keralpor 99.
Typical features | Unit | Value |
---|---|---|
Color | - | white |
Gross density | g/cm3 | 2,56 |
Surface roughness Ra | µm | 0,7 |
Bending strength | MPa | >50 |
Bend | % | < 0,3 |
Porosity | Vol.% | 36 - 38 |
Average pore size | µm | 1 |
Dimensions | mm | 10 x 10 do 310 x 310 |
Standard thicknesses | mm | 1,0 / 1,5 / 2,0 |
Main ingredients | % | 99,5 Al2O3 |
Maximum operating temperature | Tmax | 1500°C |
Benefits
Usage
Aprecierea ta pentru recenzie nu a putut fi trimisa
Reclama un comentariu
Raport trimis
Reclamatia tau nu a putut fi trimisa
Scrie-ti recenzia
Recenzia a fost trimisa
Recenzia ta nu a putut fi trimisa