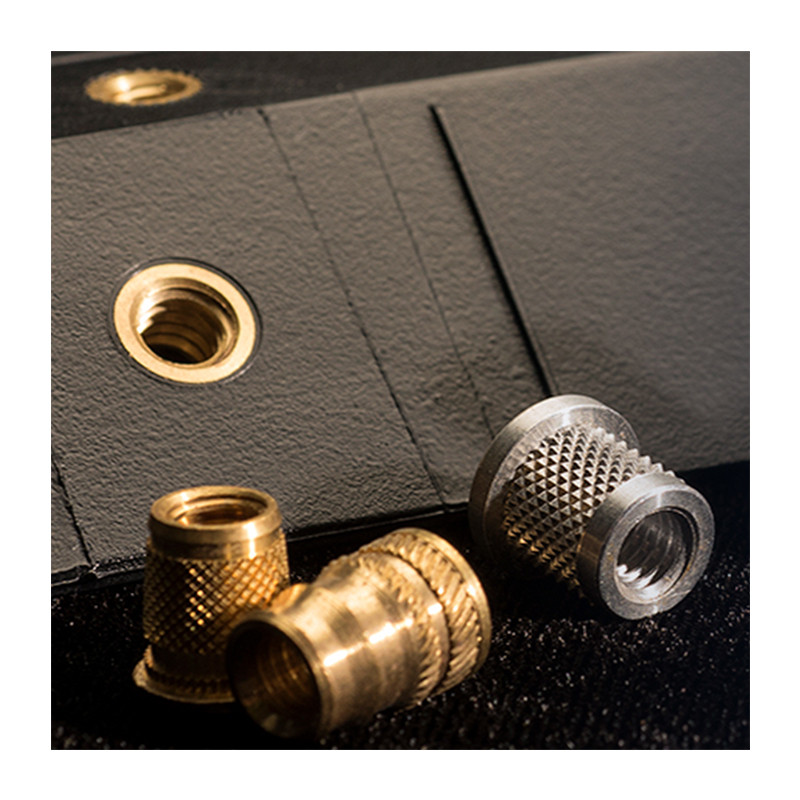
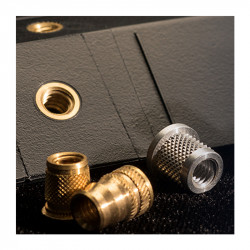
trebuie să fii logat
Category
Fotografiile au doar scop informativ. Vizualizați specificațiile produsului
please use latin characters
When a structural component is produced from a thermoplastic material, it is possible to heat a threaded metal insert to a temperature above the plastic reflow point and press it into the plastic part. There are many types of metal inserts, specially designed for retention strength, produced for this purpose. With the increasing need for lighter, stronger structural components, metal inserts are now frequently used when strong threaded connections are required. Metal to plastic bonding is one of several plastic reflow appli-cations for induction heating. Other processes involving heating plastic to a liquidous state include metal reclaiming and thermoplastic composite manufacturing.
The metal to plastic bonding process requires fast, accurate and repeatable heating to avoid such quality defects as flashing (molten plastic overflow) and burning. Modern induction heating systems quickly heat the inserts from the outside surface, limiting the heat energy to the outer edges where heat is needed to reflow the plastic. Longer heating cycles may result in the softening of the internal threads, especially at the low temperatures needed for heating brass inserts. Heating with induction is reliable, repeatable, non-contact and energy-efficient. Solid state systems, when used in conjunction with temperature sensing and control equipment, are capable of heating very small areas within precise production tolerances.
Typical RF power supplies for metal to plastic bonding range from 1 to 20kW, depending on the parts and application requirements.
Sunteți interesat de acest produs? Aveți nevoie de informații suplimentare sau de prețuri individuale?
trebuie să fii logat
When a structural component is produced from a thermoplastic material, it is possible to heat a threaded metal insert to a temperature above the plastic reflow point and press it into the plastic part. There are many types of metal inserts, specially designed for retention strength, produced for this purpose. With the increasing need for lighter, stronger structural components, metal inserts are now frequently used when strong threaded connections are required. Metal to plastic bonding is one of several plastic reflow appli-cations for induction heating. Other processes involving heating plastic to a liquidous state include metal reclaiming and thermoplastic composite manufacturing.
The metal to plastic bonding process requires fast, accurate and repeatable heating to avoid such quality defects as flashing (molten plastic overflow) and burning. Modern induction heating systems quickly heat the inserts from the outside surface, limiting the heat energy to the outer edges where heat is needed to reflow the plastic. Longer heating cycles may result in the softening of the internal threads, especially at the low temperatures needed for heating brass inserts. Heating with induction is reliable, repeatable, non-contact and energy-efficient. Solid state systems, when used in conjunction with temperature sensing and control equipment, are capable of heating very small areas within precise production tolerances.
Typical RF power supplies for metal to plastic bonding range from 1 to 20kW, depending on the parts and application requirements.
Aprecierea ta pentru recenzie nu a putut fi trimisa
Reclama un comentariu
Raport trimis
Reclamatia tau nu a putut fi trimisa
Scrie-ti recenzia
Recenzia a fost trimisa
Recenzia ta nu a putut fi trimisa