Study of Parameters for the Explosiveness of Combustible Dusts
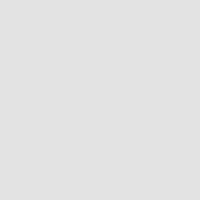
Study of Parameters for the Explosiveness of Combustible Dusts
Introduction
The text aims to provide practical guidance for individuals who are faced with the need to assess safety requirements in industrial plants where large quantities of combustible solid particles (dusts) are processed. From a process safety perspective, it is essential that the dust be examined to determine the type of risk involved. Which dusts should be tested? What tests are required? When can values obtained from published sources be used? These are some of the issues that will be addressed in the following text. The goal is to offer advice that enables the reader to make informed decisions to improve safety while minimizing costs. The first step in establishing a sound safety foundation is understanding the nature of the materials being processed.
Testing Substances vs. Using Existing Data
In the case of well-known raw materials, published data may be acceptable in many instances. Usually, such data can be considered relatively safe provided they come from a credible source, such as NFPA documents. However, it would be a mistake to accept published data without reservation, and, therefore, the most sensible approach is to compare available data describing parameters with those of the actual material currently being analyzed.
Granular Material | Pmax (bar) | Kst (bar*m/s) |
---|---|---|
Aluminum | 12.4 | 415 |
Coal | 9.2 | 129 |
Corn Starch | 7.9 | 186 |
Dextrin | 8.8 | 106 |
Epoxy Resin | 7.9 | 129 |
Iron Carbonyl | 6.1 | 111 |
Lactose | 7.7 | 81 |
Polypropylene | 8.4 | 101 |
Rice | 7.7 | 118 |
Sugar - Granulated | 6.2 | 66 |
Sugar - Powdered | 7.0 | 122 |
Sulfur | 6.8 | 151 |
Wheat Flour | 8.3 | 87 |
Wheat Grain | 9.3 | 112 |
Wood Flour | 10.5 | 205 |
TABLE 1 - PUBLISHED DUST VALUES - NFPA 652 2019
For instance, a significant parameter in assessing the explosive hazard of dust is the weight percentage of moisture content. If they are not similar - meaning the moisture level in the sources compared to the actual situation - it indicates that the data is not suitable for the analyzed scenario. Test protocols typically specify whether the tested materials have a moisture content below 5% by weight. Another useful characteristic for comparing materials is the particle size distribution. Maintaining the same oxidation conditions, larger particles oxidize more slowly than smaller particles. Comparing the particle size distribution is useful when using the provided data. In cases where published data pertains to a material significantly different from the one being processed, complications may arise. Even if both materials are similar in other aspects, this can lead to problems. A short case study illustrates the difficulty that can arise.
For example, a significant parameter in assessing the explosive hazard of dust is the weight percentage of moisture content. If they are not similar - meaning the moisture level in the sources compared to the actual situation - it indicates that the data is not suitable for the analyzed scenario. Test protocols typically specify whether the tested materials have a moisture content below 5% by weight. Another useful characteristic for comparing materials is the particle size distribution. Maintaining the same oxidation conditions, larger particles oxidize more slowly than smaller particles. Comparing the particle size distribution is useful when using the provided data. In cases where published data pertains to a material significantly different from the one being processed, complications may arise. Even if both materials are similar in other aspects, this can lead to problems. A short case study illustrates the difficulty that can arise.
The published data pertains to granulated sugar. However, at the end of the production line, sugar was collected in the form of dust through one of the filters. The dust turned out to consist of significantly smaller particles than the granulated sugar that was tested.
This difference is significant because sugar in the form of dust ignites much more easily and oxidizes faster (i.e., it has a low Minimum Ignition Energy (MIE) and a high Kst). In short, an explosion occurred due to the underestimation of the protective system. Another less obvious drawback of using published data is their conservatism. This means that the published values may be higher, and in many cases, significantly higher than the actual values for the given materials. In other words, studying the actual dust often leads to substantial savings in the design and construction of tanks/facilities requiring explosion protection. This will be discussed in detail later in the article.
Combustible Dust Explosion Classification | Kst |
St1 | 0-200 |
St2 | 200-300 |
St3 | >300 |
Dust Testing
There are many tests that can be conducted to assess the risk and behavior associated with combustible dusts. However, experts do not always agree on when and why specific tests should be performed for a given dust scenario. A comprehensive discussion on this topic goes beyond the scope of this publication. Instead, a brief overview of the most commonly performed tests and the reasons for conducting them will be presented. It is essential to note that not every test is necessary or required every time for every type of dust or situation. Therefore, it is advisable to seek the help of an expert or a specialized company who can determine the appropriate tests to be performed and guide accordingly.
What Tests are Available?
- The combustibility test of dust is also known as "the OSHA Salt Lake City test" or "the Go/No-Go test." Currently, it is part of ASTM E1226 (see below). This is a simple screening test conducted to determine whether the dust can behave explosively. This method cannot be used for sizing, but it can minimize testing costs if the result is "NO-GO." It is essential to note that this test should be conducted first when the explosibility conductivity of the dust is in accordance with ASTM E-1226.
- The combustibility test of dust in North America is defined by ASTM E-1226, but a similar protocol exists for Europe (results from tests conducted in notified laboratories in the EU can be safely used). This test is most commonly performed using a 20-liter sphere, but it can also be conducted using a 1 m3 test vessel (more on this later in the article) and provides Kst and Pmax values. These values are essential for the selection of explosion protection devices such as venting panels or active suppression systems. This test belongs to the basic category and should be conducted for all combustible dusts.
- Minimum Explosible Concentration (MEC). In North America, it is defined by ASTM 1515, but a similar standard exists in Europe. For dust to behave explosively, it must be lifted into a dust cloud (known as a cloud) with a sufficient concentration for the flame to propagate through the mass of unburned material in a chain reaction. This test is useful in situations where dust concentration may be low and controlled. Examples may include certain types of dryers or conveyors.
- Minimum Ignition Energy (MIE). In North America, it is defined by the ASTM E-2019 standard, but a similar test method also exists in Europe. Some dusts ignite more easily than others. This test determines how much electrostatic discharge energy is required to ignite a dust cloud (cloud). Combustible dusts differ in their ease of ignition. Both extreme cases are essential for understanding the processed materials. There are situations where safe handling requires personnel working with the materials to be grounded to prevent self-ignition due to electrostatic discharges from their own bodies. On the other hand, there are materials that are so difficult to ignite that they can be safely processed without the concern of electrostatic discharges.
This raises a certain question: Should the dust be tested in its received state, or should it be dried and reduced/classified to test only fine particles? Again, accepted standards encourage efforts to consider the worst-case scenario. In cases where variables such as particle size and moisture content are carefully monitored and controlled, testing materials in their received state may be the best option. Otherwise, it is advisable to adopt a more cautious approach and follow standards that represent the current engineering knowledge.
Another important factor is whether the processed dust consists of a single material or is a mixture of several. Mixtures present several challenges. Firstly, they often contain multiple components. For example, many vitamins are commonly made up of a bill of materials with at least 25 different components. Testing everything is not practical. Generally, the components that make up the majority of the total mixture by weight or volume will be representative of the overall combustibility characteristics of the mixture. Thus, in the case of a multi-component vitamin, the five or six major components that make up the highest percentage of the mixture should be tested as a minimum.
Dusts that can change their properties or undergo degradation pose particular challenges in both sampling and packaging or shipping. Metal dusts provide an excellent example. They readily undergo oxidation and must be packed in airtight vacuum containers and shipped as quickly as possible. However, it should be noted that not all dust samples can be transported by air.
Controversies regarding the validity of tests
A recent commission was carried out where certain materials were tested with positive results. However, these results are being questioned, and despite articles and heated discussions, the final results remain controversial. A scientific publication was prepared, and further discussions were organized, but the controversy remains unresolved. To describe the dispute, it is necessary to present the background of the entire history. As mentioned, the test set consists of a 20-liter sphere and another vessel with a volume of 1 cubic meter. The 20-liter sphere was specifically developed as a practical laboratory set that could provide results close enough (i.e., +/- 10%) to those obtained in the 1-cubic-meter sphere, which serves as the benchmark testing sphere. The 1-cubic-meter sphere is the sphere of reference testing. There are various settings and equipment configurations enabling an acceptable level of accuracy, and it is a common practice to regulate this type of setup. A versatile methodology ensuring the mentioned accuracy has also been developed. In the case of materials that might be very difficult to ignite, the 20-liter sphere showed positive results, but retesting in the 1-cubic-meter sphere did not confirm the findings. Why? What does this mean? Can the results obtained using the 20-liter sphere be considered reliable?
The reasons for this situation seem to stem from the fact that depending on the testing setup, the 20-liter sphere may be overly stimulated by excessive ignition energy. As a result, some customers pay for costly additional tests in the larger 1-cubic-meter sphere and receive negative results. What does this imply? We know that in one set of conditions, the test material showed positive results, while in another set, it yielded negative results. Regulatory organizations typically take the stance that a positive result is a positive result, and the fact that different results are obtained using a different test set is considered insignificant. According to OSHA, Kst = 1 bar*m/s indicates a combustible dust. Furthermore, the 20-liter sphere has been commonly used in North America for decades, making it challenging to question its data. However, recent studies suggest that data from the 20-liter sphere may also not be accurate for metal dusts. Comparative tests between the 20-liter sphere and the 1-cubic-meter sphere showed that the same metal dusts actually increased the Kst value during testing in the larger apparatus. Further research is being conducted to explain this phenomenon, as metal dusts exhibit different behavior during testing compared to organic materials.
The first step in developing a solid foundation for the safety of combustible dusts is to gain scientific and comprehensive understanding of the materials being worked with. Each dust is unique, and each explosion related to them is also exceptional. The more we know, the greater the chances of avoiding unacceptable losses. For well-known materials, such as most agricultural dusts, data published by reputable sources should be sufficiently accurate. It is also essential to ensure that the published data used are representative of materials similar to those being worked with. When in doubt, testing the material is necessary. There are many tests available to determine the characteristics of the dust, and not every test is required in every situation. A thorough understanding of the process is necessary to determine which tests are needed. While some testing methods have been questioned, it is a fact that those who utilized the data and acted accordingly improved their safety and, as far as is known, did not incur any losses.
Оставить комментарий