Как выбрать средства для фиксации резьбы?
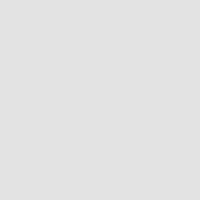
Thread locking is a key element in ensuring the durability and safety of mechanical connections in many applications, from minor home repairs to advanced industrial operations. Products used for this purpose, such as anaerobic adhesives, play a particularly important role due to their unique properties.
Why is thread locking important?
Threaded connections are often exposed to dynamic forces such as vibrations, temperature changes, or high pressures. Without proper locking, screws and nuts can loosen, leading to failures, leaks, or reduced system efficiency. Thread adhesives, such as B222 Eco, B243 Eco, and B270 Eco, have been designed to prevent these problems by creating durable and reliable seals.
How do thread locking products work?
Anaerobic adhesives function through an anaerobic polymerization process: when applied to threads, they harden upon contact with metal and after air access is cut off. This technology ensures strong connections resistant to vibrations, corrosion, and extreme temperatures. Thanks to catalytic curing, these products create both durable threaded connections and effective industrial seals.
Applications of anaerobic adhesives
• Automotive industry: Thread adhesives for automotive screws prevent loosening of components in engines and chassis systems.
• Industrial machines: Adhesives for industrial machinery maintain durability in high mechanical load and vibration conditions.
• Hydraulic and pneumatic systems: Thread sealants protect against leaks in installations operating under high pressure.
Benefits of using industrial adhesives
1. Vibration resistance: Adhesives like B243 Eco effectively prevent loosening of connections in demanding work environments.
2. Temperature resistance: Industrial adhesives withstand extreme temperatures, making them ideal for applications in the aerospace and energy industries.
3. Safety and durability: Connections secured with anaerobic adhesives, such as B270 Eco, have a high breakaway torque, which enhances their reliability.
Types of thread locking products
Thread locking methods vary depending on the type of connection, working conditions, and durability and sealing requirements. There are three main categories: chemical thread locking products, mechanical methods, and tapes and pastes. Each has its unique features and applications.
Anaerobic adhesives – effectiveness in precision applications
Anaerobic adhesives, such as B222 Eco, B243 Eco, and B270 Eco, are advanced chemical products dedicated to permanently locking and sealing threaded connections. Their action involves curing in anaerobic conditions, which ensures strong and vibration-resistant connections.
• Characteristics:
• They create a monolithic seal in threaded spaces.
• They are used in applications requiring resistance to mechanical, chemical, and thermal factors.
• Ideal for one-time connections or those that rarely need to be unscrewed.
Limitations:
• They require proper surface cleanliness and preparation.
• Some applications may require catalytic curing to speed up the chemical reaction.
Spring washers and locking rings – simplicity and convenience
Mechanical methods, such as spring washers or locking rings, provide easy and inexpensive solutions for repeated assemblies. They are more flexible than chemical methods but have lower resistance to extreme conditions.
Applications:
• In environments where disassembly and reassembly are frequent, e.g., in systems with varying loads.
Limitations:
• They do not guarantee complete sealing, making them less suitable for hydraulic or pneumatic connections.
• They require additional components, increasing the number of parts in the system.
Tapes and pastes – flexible sealing solutions
PTFE (Teflon) tapes and sealing pastes are primarily used for sealing connections in hydraulic, gas, and pneumatic systems. They are suitable for applications with lower mechanical strength requirements.
Advantages:
• Easy to use and remove.
• Can be used on metal and plastic threads.
Limitations:
• Limited resistance to high pressures and temperatures compared to industrial adhesives.
• Lower ability to prevent thread loosening.
Each method has its place in different applications. The choice of the appropriate product depends on the specifics of the connection, durability requirements, and the work environment.
Factors determining product selection
Choosing the appropriate thread locking product depends on many variables that must be analyzed individually based on the specifics of the application. One of the key elements is the type of connection. Threaded connections can be made of both metal and plastics, and each of these solutions requires different adhesive or sealant properties. Metal threads, especially in industrial machines, often use anaerobic adhesives with high strength that can withstand extreme loads. For plastic components, less aggressive products are necessary to prevent material deformation.
Operating conditions are also crucial. Extreme temperatures, pressure, and exposure to chemicals affect product selection. In high-temperature environments, products resistant to temperatures above 150°C, which also maintain their properties at very low temperatures, are required. Industrial adhesives that combine mechanical strength with chemical resistance are an example. In environments with high dust or exposure to corrosion, products that additionally form a protective layer are a better choice.
Mechanical load is also important. In applications subject to intense vibrations, such as in the automotive industry, anaerobic adhesives are indispensable because their anaerobic polymerization ability guarantees durability and prevents the loosening of connections. Temporary connections, on the other hand, require products that allow easy disassembly without damaging the threads, which is crucial for machine maintenance and servicing. For this purpose, low breakaway torque adhesives are used.
The frequency of disassembly is the last but equally important aspect. For permanent connections, products with very high strength are selected to ensure maximum safety and stability. Where regular disassembly of components is required, products with lower bonding strength are more suitable, preventing the need for excessive force during disassembly.
Considering the above factors allows for the optimal selection of a product to meet the application's requirements, ensuring both the effectiveness of the locking and ease of use.
Material Compatibility Assessment
Selecting the right thread locking product requires precise adjustment to the material from which the connected components are made. Metals, alloys, and plastics differ in mechanical and chemical properties, as well as susceptibility to damage, which makes the use of a universal product potentially insufficient or even harmful.
For metal components, especially steel and aluminum, anaerobic adhesives are usually the best choice. Their anaerobic polymerization process ensures the durability of threaded connections and vibration resistance, as well as effectively preventing screw loosening. However, for softer metals like copper or brass, caution should be exercised when choosing high-strength products, as they can lead to thread damage during disassembly.
For alloys with different compositions, it is crucial to understand the potential risk of galvanic corrosion. This problem arises when different metals in contact with an electrolyte create galvanic currents that cause degradation of the less noble material. To prevent this, thread locking products with a neutral chemical character should be used, as they do not lead to electrochemical reactions between materials. Thread sealants that also isolate surfaces from moisture and other external factors can be helpful in such situations.
Plastics require an even more specific approach. Adhesives and sealants must be selected in such a way that they do not weaken the material's structure due to chemical reactions, such as dissolution or stress cracking. Anaerobic adhesives with low bonding strength and silicone-based products are often recommended for plastic components, as they provide solid yet flexible connections that do not damage more delicate materials.
Material compatibility assessment is not only about selecting the right product for the material itself but also considering the operating conditions, such as temperature, pressure, or chemical environment, which can affect the durability of the connection. Using the correct thread locking products helps avoid material damage, ensuring long-term efficiency and safety of the construction.
Performance Criteria
When selecting a thread locking product, it is crucial to understand the performance criteria that determine the durability and effectiveness of the connections. The performance of adhesives or sealants can be assessed based on parameters such as shear and tensile strength, vibration resistance, and the ability to function in variable weather conditions.
Shear and tensile strength are the fundamental indicators that determine how effectively the adhesive can hold the connection under mechanical forces. Technical data for such products often present values in force per unit area. In practice, higher shear strength values mean that the product can withstand greater loads without damaging the connection. For industrial applications, such as securing screws in machines or structures exposed to high loads, products with high mechanical strength are recommended. At the same time, in less demanding conditions where easier disassembly is required, products with moderate bonding strength are selected.
Vibration resistance is another key aspect. Anaerobic adhesives are known for their ability to minimize the loosening of threads under vibration. The anaerobic polymerization process allows the formation of a rigid bond that reduces the risk of leakage or loosening of components, even under intense shocks. For applications such as the automotive industry, where threaded connections are exposed to constant vibrations, these products are an essential element of securing the connections.
Long-term exposure to weather conditions, such as moisture, temperature fluctuations, or UV radiation, requires the use of products with appropriate chemical and physical resistance. In such situations, it is important that adhesives and sealants have thermal stability and resistance to corrosion. These products must work effectively over a wide temperature range, from extreme cold to high operating temperatures, while retaining their sealing properties.
When analyzing technical data for thread adhesives, it is important to focus on their specific mechanical properties and resistance to external factors, adjusting the choice to the requirements of the particular application. Choosing the right product will not only ensure the durability and reliability of the connections but also safety in the operation of machines and structures.
Practical Application Tips
Proper application of thread locking products is crucial to achieving durable and reliable connections. The application process requires particular attention, especially at the stage of surface preparation and the actual application of the product. Care in these steps minimizes the risk of technical issues and extends the life of the connection.
Surface Preparation: Cleaning and Degreasing
The first and most important stage of applying adhesive or sealant is thorough surface preparation. Ensure that all elements of the threaded connection are clean, dry, and free from contaminants. Residues of oil, grease, dust, or rust can significantly weaken the adhesive bond, reducing its effectiveness. For this purpose, it is recommended to use appropriate cleaning agents, such as degreasers or isopropanol. The elements should be wiped to achieve a dry, shiny surface, ensuring better adhesive adhesion.
For metal surfaces, particularly those exposed to corrosion or oxidation, it is worth considering the use of an activator or primer to improve the anaerobic polymerization reaction in more challenging conditions.
How to Avoid the Most Common Application Mistakes
When applying thread locking products, several guidelines must be followed to avoid problems with product ineffectiveness. One of the most common mistakes is applying too little or too much adhesive. Insufficient amounts may not cover the entire surface of the thread, weakening the connection's strength. On the other hand, excess product can lead to leakage and complications during further assembly.
Evenly distributing the adhesive along the entire length of the thread is key to success. It is also important to tighten the connection immediately after applying the adhesive, as the polymerization process begins as soon as oxygen is excluded. Delaying too long can result in improper curing of the adhesive.
Another common issue is applying the product on surfaces that are too cold or wet. Application conditions significantly affect the curing process, so it's important to ensure that the surrounding temperature and the temperature of the elements are within the range recommended by the manufacturer.
It is also essential to follow the curing time specified in the product's technical specifications. Prematurely loading the connection may weaken it. For anaerobic adhesives, full curing can take from a few hours to 24 hours, depending on the type of adhesive and surrounding conditions.
In summary, surface preparation and careful application of the adhesive are crucial elements that determine the effectiveness of thread locking. Proper adherence to the manufacturer's recommendations and avoiding typical mistakes will ensure that connections are durable, reliable, and resistant to extreme operating conditions.
Cost and Profitability Analysis
Choosing the right thread-locking products is a decision that has significant financial consequences, both in the short and long term. Analyzing the costs and benefits of these products requires considering not only their purchase price but also the benefits of preventing potential failures and minimizing maintenance costs for machines or infrastructure.
Thread-locking products, such as anaerobic adhesives, may initially seem relatively expensive compared to traditional methods like washers or sealing tapes. However, their high efficiency and ability to create durable and resistant connections allow for significant cost reductions in terms of downtime and the need for frequent maintenance.
High-quality industrial adhesives, although more expensive to purchase, help reduce the risk of machinery failures, which in turn translates into savings in the long run. For example, using adhesives with high shear strength eliminates the need for regularly tightening screws in machines exposed to vibrations, reducing costs related to service work and spare parts.
Incorrect thread-locking, such as using the wrong product or applying it insufficiently, can lead to serious failures. The costs of such incidents are multidimensional. In the automotive industry, loosening threaded connections can result in damage to key vehicle components, leading to costly repairs. In the energy industry, leaks in threaded connections can lead to repairs that not only generate costs but also cause production downtime.
An example from the aerospace industry shows that inadequate securing of screws in an engine can lead to failures with enormous financial and reputational consequences. The costs of such situations include not only repairs but also compensation or loss of customer trust.
Using high-quality thread sealants and adhesives for automotive screws or industrial machines can prevent such situations, which practically means savings that outweigh the initial investment in thread-locking products. Moreover, durable connections reduce the need for frequent disassembly, which also lowers labor and consumable material costs.
Investing in high-quality thread-locking products, such as anaerobic adhesives or thread sealants, is an expense that quickly pays off due to the savings generated from their use. Eliminating failures, increasing connection durability, and reducing the need for maintenance are key factors that make these products a cost-effective choice, both for small workshops and large industrial facilities.
Summary
The choice of the best thread-locking product depends on several key factors that directly affect performance, durability, and costs in a given industrial application. To make an optimal choice, it is necessary to consider the type of threaded connection, working conditions, mechanical loads, and the material from which the elements are made. Here are several essential points to consider when selecting the appropriate products:
Type of connection and material - The first step is to fully understand what type of connection is required. For fine-threaded connections and those made from high-strength metals like stainless steel or titanium alloys, anaerobic adhesives are an excellent solution. For more delicate materials, such as plastics or composites, more specialized products may be needed that not only provide the necessary strength but are also gentle on the surface.
Working conditions - Adhesives and thread-locking products vary in their resistance to temperature, pressure, and exposure to chemicals. In applications exposed to high temperatures (e.g., automotive and energy industries), products with temperature resistance tailored to these conditions should be chosen. For applications requiring resistance to vibrations, such as in industrial machinery, adhesives with high resistance to dynamic loads are recommended.
Frequency of disassembly - The decision to choose a thread-locking product may also depend on the need for potential disassembly of connections. If the connections need to be temporarily secured, such as in the case of repairs or adjustments, it is worth selecting products that allow easy disassembly, such as low-strength thread adhesives. For permanent connections that will not require disassembly, products with high strength, which provide long-term stability, are ideal.
Costs and cost-effectiveness - The choice of thread-locking product should not be based solely on the purchase price. It is important to also consider long-term savings, such as reducing the risk of failures, repairs, or the need for frequent screw tightening. Proper selection of the product can therefore lead to significant savings related to reducing machine downtime and repair costs.
Where to find technical support and training materials?
DACPOL, as a leader in providing professional solutions, offers a wide range of technical support and educational resources to help in making the best choice of thread-locking products. DACPOL provides comprehensive assistance in selecting the right products, offering access to technical documentation, safety data sheets, application instructions, and detailed product information.
Additionally, the company organizes specialized courses and training sessions, which are an excellent opportunity to expand knowledge about the properties of anaerobic adhesives and other DACPOL products. During these training sessions, participants can learn how to correctly apply thread-locking products, how to match them to different materials, and how to avoid common mistakes during application. The company also regularly organizes webinars and industry seminars, providing an opportunity for direct exchange of experiences with experts and other users.
DACPOL also offers free samples of its products, allowing customers to conduct tests in real-world conditions, which enables them to assess the effectiveness of the products before making a purchase. Furthermore, the company provides full application support, helping clients find optimal solutions that contribute to improving the quality of threaded connections and increasing operational efficiency in industrial plants.
Through collaboration with DACPOL's experienced team, customers can count on the highest quality products and support at every stage of the selection and application of thread-locking products.
Оставить комментарий