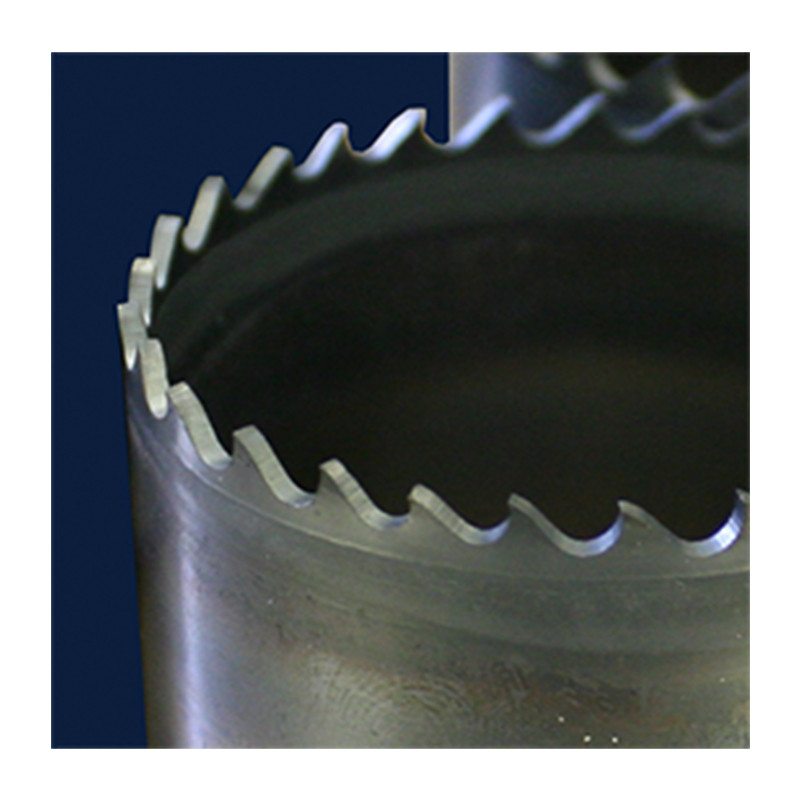
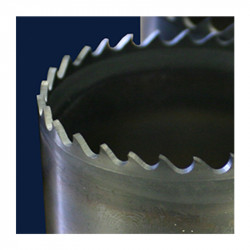
Морате бити пријављени да
Category
Фотографије су само у информативне сврхе. Погледајте спецификацију производа
please use latin characters
Kaljenje je vrsta termičke obrade koja ima za cilj postizanje povećane tvrdoće, čvrstoće, otpornosti na habanje uz smanjenu plastičnost i povećanje krhkosti. U zavisnosti od dubine kaljenja, razlikuju se volumensko i površinsko kaljenje. Volumensko kaljenje podrazumeva zagrevanje materijala kroz celokupni presečak do temperature potrebnih promena, održavanje na toj temperaturi i hlađenje odgovarajućom brzinom. Ovaj proces se koristi za kaljenje čelika srednje ugljeničnih i visokougljeničnih u cilju postizanja umerene čvrstoće i tvrdoće. Površinsko kaljenje podrazumeva brzo zagrevanje tanke površinske sloja materijala do temperature potrebnih promena i brzo hlađenje. Dobija se povećana tvrdoća i čvrstoća samo do određene dubine, dok ostatak materijala ostaje nekalen. Kao sredstva za hlađenje najčešće se koriste: ulje, vazduh, voda, voda sa rastvorljivim polimerima itd.
Moderno indukciono zagrevanje omogućava pouzdano, beškontaktno zagrevanje u minimalnom vremenu bez plamena. Važna osobina je ponovljivost i preciznost procesa – mogućnost podešavanja vremena, temperature, kontrole dubine kaljenja, hlađenja i dela dela za obradu. Poluprovodnički sistemi mogu zagrevati čak i veoma male oblasti u preciznim tolerancijama proizvodnog procesa.
Indukciono kaljenje se vrši na dva načina. Prvi je statčko kaljenje, koje podrazumeva obavljanje procesa zagrevanja bez promene pozicije dela i induktora u odnosu na njih. Ovaj način karakteriše brzina, nepotrebno složena automatizacija i omogućava vrlo precizno određivanje područja za zagrevanje, čak i za komponente složenih oblika. Drugi način je progresivno kaljenje, koje podrazumeva obavljanje procesa zagrevanja uz promenu pozicije dela i induktora u odnosu na njih. To omogućava kaljenje komponenata sa velikim površinama i dimenzijama, kao i zagrevanje nekoliko specifičnih oblasti na jednom delu, bez potrebe za ručnim pomeranjem.
Termička obrada pomoću indukcionih sistema idealna je za primene u industrijama koje zahtevaju automatizovani, precizan i istovremeno brz proces. Indukciono zagrevanje se pokazalo pogodnim za veće preduzetnike koji poseduju mnoge proizvodne linije u kontinuiranoj proizvodnji, zbog povećane efikasnosti. Za manje proizvođače dodatna prednost je gotovo trenutni start mašine. U slučaju prekida proizvodnje, mašina ne mora biti stalno uključena, kao što je to slučaj sa običnim pećima.
Odpuštanje je vrsta termičke obrade koja se sastoji u smanjenju krhkosti, lomljivosti, tvrdoće na željeni nivo i uklanjanju naprezanja kaljenja u prethodno kaljenoj čeliku. Ovaj proces se obavlja na relativno niskim temperaturama, nižim od temperature kaljenja. Komponenta se zagreva, održava na povišenoj temperaturi određeno vreme, a zatim se polako hladi.
Indukciono odpuštanje obavljeno pomoću indukcionih sistema donosi mnoge prednosti koje su opisane uz kaljenje, kao što su kraće vreme procesa (čak u sekundama!), ušteda energije, mogućnost precizne kontrole i ponovljivost. Integracija ovih sistema u proizvodne linije omogućava pojednostavljenje upravljanja procesom, ubrzanje proizvodnje i povećanje profita.
Да ли вас занима овај производ? Да ли су вам потребне додатне информације или појединачне цене?
морате бити пријављени
Kaljenje je vrsta termičke obrade koja ima za cilj postizanje povećane tvrdoće, čvrstoće, otpornosti na habanje uz smanjenu plastičnost i povećanje krhkosti. U zavisnosti od dubine kaljenja, razlikuju se volumensko i površinsko kaljenje. Volumensko kaljenje podrazumeva zagrevanje materijala kroz celokupni presečak do temperature potrebnih promena, održavanje na toj temperaturi i hlađenje odgovarajućom brzinom. Ovaj proces se koristi za kaljenje čelika srednje ugljeničnih i visokougljeničnih u cilju postizanja umerene čvrstoće i tvrdoće. Površinsko kaljenje podrazumeva brzo zagrevanje tanke površinske sloja materijala do temperature potrebnih promena i brzo hlađenje. Dobija se povećana tvrdoća i čvrstoća samo do određene dubine, dok ostatak materijala ostaje nekalen. Kao sredstva za hlađenje najčešće se koriste: ulje, vazduh, voda, voda sa rastvorljivim polimerima itd.
Moderno indukciono zagrevanje omogućava pouzdano, beškontaktno zagrevanje u minimalnom vremenu bez plamena. Važna osobina je ponovljivost i preciznost procesa – mogućnost podešavanja vremena, temperature, kontrole dubine kaljenja, hlađenja i dela dela za obradu. Poluprovodnički sistemi mogu zagrevati čak i veoma male oblasti u preciznim tolerancijama proizvodnog procesa.
Indukciono kaljenje se vrši na dva načina. Prvi je statčko kaljenje, koje podrazumeva obavljanje procesa zagrevanja bez promene pozicije dela i induktora u odnosu na njih. Ovaj način karakteriše brzina, nepotrebno složena automatizacija i omogućava vrlo precizno određivanje područja za zagrevanje, čak i za komponente složenih oblika. Drugi način je progresivno kaljenje, koje podrazumeva obavljanje procesa zagrevanja uz promenu pozicije dela i induktora u odnosu na njih. To omogućava kaljenje komponenata sa velikim površinama i dimenzijama, kao i zagrevanje nekoliko specifičnih oblasti na jednom delu, bez potrebe za ručnim pomeranjem.
Termička obrada pomoću indukcionih sistema idealna je za primene u industrijama koje zahtevaju automatizovani, precizan i istovremeno brz proces. Indukciono zagrevanje se pokazalo pogodnim za veće preduzetnike koji poseduju mnoge proizvodne linije u kontinuiranoj proizvodnji, zbog povećane efikasnosti. Za manje proizvođače dodatna prednost je gotovo trenutni start mašine. U slučaju prekida proizvodnje, mašina ne mora biti stalno uključena, kao što je to slučaj sa običnim pećima.
Odpuštanje je vrsta termičke obrade koja se sastoji u smanjenju krhkosti, lomljivosti, tvrdoće na željeni nivo i uklanjanju naprezanja kaljenja u prethodno kaljenoj čeliku. Ovaj proces se obavlja na relativno niskim temperaturama, nižim od temperature kaljenja. Komponenta se zagreva, održava na povišenoj temperaturi određeno vreme, a zatim se polako hladi.
Indukciono odpuštanje obavljeno pomoću indukcionih sistema donosi mnoge prednosti koje su opisane uz kaljenje, kao što su kraće vreme procesa (čak u sekundama!), ušteda energije, mogućnost precizne kontrole i ponovljivost. Integracija ovih sistema u proizvodne linije omogućava pojednostavljenje upravljanja procesom, ubrzanje proizvodnje i povećanje profita.
Vaša zahvalnost na komentar ne može biti registrovana
Prijavite nepristojan komentar
Prija nepristojnog komentara registrovana
Vaša prijava nepristojnog komentara ne može biti registrovana
Napišite vaš komentar
Komentar poslat
Vaš komentar ne može biti registrovan