Морате бити пријављени да
-
moreX
-
Компоненте
-
-
Category
-
Полупроводници
- диоде
- Тиристори
-
Електро изоловани модули
- Електро изоловани модули | ВИСХАИ (ИР)
- Електро изоловани модули | ИНФИНЕОН (ЕУПЕЦ)
- Електро изоловани модули | Семикрон
- Електро изоловани модули | ПОВЕРЕКС
- Електро изоловани модули | ИКСИС
- Електро изоловани модули | ПОСЕИЦО
- Електро изоловани модули | АББ
- Електро изоловани модули | ТЕЦХСЕМ
- Go to the subcategory
- Мостовни исправљачи
-
Транзистори
- Транзистори | GeneSiC
- SiC MOSFET модули | Mitsubishi
- SiC MOSFET модули | STARPOWER
- АББ СиЦ МОСФЕТ модули
- IGBT модули | MITSUBISHI
- Транзисторски модули | MITSUBISHI
- MOSFET модули | MITSUBISHI
- Транзисторски модули | ABB
- ИГБТ модули | POWEREX
- ИГБТ модули | ИНФИНЕОН (ЕУПЕЦ)
- Silicijum-karbidni poluprovodnički elementi
- Go to the subcategory
- Гате Дриверс
- Блокови напајања
- Go to the subcategory
- Električni pretvarači
-
Пасивне компоненте (кондензатори, отпорници, осигурачи, филтери)
- Otpornici
-
Osigurači
- Minijaturni osigurači za elektronske sisteme serije ABC i AGC
- Cilindrični brzi osigurači
- Osigurači sa odloženim delovanjem GL/GG i AM karakteristika
- Ultra-brzi osigurači
- Brzi osigurači sa britanskim i američkim standardom
- Brzi osigurači sa evropskim standardom
- Vučni osigurači
- Visokonaponski osigurači
- Go to the subcategory
-
Kondenzatori
- Motorni kondenzatori
- Elektrolitski kondenzatori
- Kondenzatori - snubberi
- Energetski kondenzatori
- Kondenzatori za DC kola
- kondenzatori za kompenzaciju snage
- Visokonaponski kondenzatori
- Kondenzatori za indukciono grejanje
- Impulsni kondenzatori
- ДЦ ЛИНК кондензатори
- Кондензатори за АЦ/ДЦ кола
- Go to the subcategory
- EMI filtri
- Superkondenzatori
- Заштита од пренапона
- Go to the subcategory
-
Releji i kontaktori
- Теорија релеја и склопника
- Trofazni poluprovodnički releji
- Трофазни полупроводнички релеји наизменичне струје
- Регулатори, команде и додаци
- Sistemi za meki sart i reverziblni kontaktori
- Elektromehanički releji
- Kontaktori
- Rotacioni prekidači
-
Једнофазни полупроводнички релеји наизменичне струје
- Једнофазни релеји наизменичне струје, 1 серија | Д2425 | Д2450
- Jednofazni poluvodički izmjenični releji CWA i CWD serije
- Jednofazni poluvodički izmjenični releji CMRA i CMRD serije
- Jednofazni poluvodički izmjenični releji - serija PS
- Двоструки и четвороструки полупроводнички релеји наизменичне струје, серије Д24 Д, ТД24 К, Х12Д48 Д.
- Jednofazni poluvodički releji - gn serije
- Jednofazni kružni releji Ckr serije
- Jednofazni AC poluvodički releji za DIN sabirnice - ERDA I ERAA serija
- 150A AC jednofazni releji
- Čvrsti releji s ugrađenim hladnjakom na šini - ENDA, ERDA1 / ERAA1 series
- Go to the subcategory
- Monofazni poluprovodnički releji za štampane ploče
- Интерфејс релеји
- Go to the subcategory
- Indukcione komponenete
- Radijatori, Varistori, Termička zaštita
- Ventilatori
- Klimatizacija, Pribor za industrijska kućišta, Kuleri
-
Батерије, пуњачи, бафер напајања и претварачи
- Батерије, пуњачи - теоријски опис
- Litijum-jonske baterije. Nestandardne baterije. Sistem za upravljanje baterijom (BMS)
- Baterije
- Punjači i dodaci za baterije
- UPS i puferski izvori napajanja
- Pretvarači i dodaci- fotonaponski
- Складиште енергије
- Гориве ћелије
- Литијум-јонске батерије
- Go to the subcategory
-
Automatika
- Futaba Drone Parts
- Крајњи прекидачи, микро прекидачи
- Сензори, претварачи
- Пирометрија
- Бројачи, тајмери, панел мерачи
- Индустријски заштитни уређаји
- Светлосна и звучна сигнализација
- Термовизијска камера
- ЛЕД дисплеји
- Тастери и прекидачи
-
Снимачи
- Снимач АЛ3000
- КР2000 снимач
- Снимач КР5000
- ХН-ЦХ мерач са функцијом регистрације влажности и температуре
- Потрошни материјал за снимаче
- 71ВР1 снимач
- Снимач КР 3000
- ПЦ снимачи серије Р1М
- ПЦ снимачи серије Р2М
- ПЦ снимач, 12 изолованих улаза - РЗМС-У9
- ПЦ снимач, УСБ, 12 изолованих улаза - РЗУС
- Go to the subcategory
- Go to the subcategory
-
Kablovi, Licnaste žice, Kablovski kanali, Fleksibilne veze
- жице
- лицнастим жице
- Каблови за специјалне намене
- схиртс
-
плетенице
- браидс флат
- плетенице коло
- Врло флексибилан плетеница - стан
- Врло флексибилан плетеница - коло
- Бакар плетена цилиндрични
- Бакра плетеница штит и цилиндрични
- Флексибилни уземљење траке
- Плетенице ЦИЛИНДРИЦАЛ поцинковани и нерђајућег челика
- ПВЦ изолацијом бакарне плетенице - Температура 85 ° Ц
- Стан плетени алуминијум
- Цоннецтион Кит - плетенице и цеви
- Go to the subcategory
- Прибор за вучу
- папучица
- Флексибилни исолатед сабирнице
- Вишеслојна флексибилан шина
- системи за управљање кабл
- Водове, цеви
- Go to the subcategory
- View all categories
-
Полупроводници
-
-
- Suppliers
-
Applications
- Automatika industrijska
- CNC alatni strojevi
- DC i izmjenični pogoni (pretvarači)
- Energy bank
- Indukciono grejanje
- Industrijski zaštitni uređaji
- Istraživanje i laboratorijska merenja
- Mašine za sušenje i obradu drveta
- Mašine za termoformiranje
- Merenje i regulacija temperature
- Motori i transformatori
- Oprema i dijelovi za opasna područja (EX)
- Oprema za centrale, kontrolne ormare i telekomunikacije
- Poligrafija
- Rudarstvo, metalurgija i livnica
- Tramvajska i železnička vuča
- UPS i ispravljački sistemi
- Апарати за заваривање и апарати за заваривање
- Индустријска аутоматизација
- ХВАЦ аутоматизација
-
Инсталација
-
-
Индуктори
-
-
Индукциони уређаји
-
-
https://www.dacpol.eu/pl/naprawy-i-modernizacje
-
-
Услуга
-
- Kontakt
- Zobacz wszystkie kategorie
Types of temperature sensors
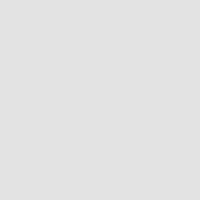
We use temperature sensors every day to regulate, for example, the temperature in buildings, to regulate water temperature. Temperature sensors are also needed in many other applications such as consumer, medical and industrial electronics.
Each application may have different needs for temperature sensors. They differ in what is being measured (air, mass, or liquid), where it is being measured (indoors or outdoors), and the range of temperature measured, among other things.
Today we will focus on 7 types of temperature sensors and devices used indoors and outdoors - how they work, what sets them apart, and the pros and cons of these solutions.
Thermocouples
Thermocouples are the most commonly used type of temperature sensor. They are used in industrial, automotive and consumer applications. Thermocouples are self-powered, require no excitation, can operate over a wide temperature range and have a fast response time.
Thermocouples are made by joining two different metal wires together. This results in the Seebeck effect. The Seebeck effect is a phenomenon in which a temperature difference between two different conductors causes a voltage difference between the two substances. It is this voltage difference that can be measured and used to calculate the temperature.
There are several types of thermocouples that are made of different materials, allowing for different temperature ranges and different sensitivities. The different types are distinguished by letter designations. Types include: E, J, K, N, T, R/S, B.
Some disadvantages of thermocouples include the fact that temperature measurement can be difficult due to their low output voltage that requires precise amplification, susceptibility to external noise on long wires and cold junction. The cold junction is where the thermocouple wires meet the copper signal circuit paths. This creates another Seebeck effect that must be compensated for, called cold junction compensation.
Resistance Temperature Sensors – RTS
As the temperature changes, the resistance of each metal also changes. This difference in resistance is what resistive temperature sensors are based on. An RTS is a resistor with well-defined resistance characteristics as a function of temperature. Platinum is the most common and most accurate material used to make this type of sensor.
Platinum RTS are most common because they offer a nearly linear response to temperature changes, are stable and accurate, provide repeatable response, and have a wide temperature range. Resistive temperature sensors are often used in precision applications because of their accuracy and repeatability.
RTS elements tend to have higher thermal mass and therefore respond more slowly to temperature changes than thermocouples. Signal conditioning is important for RTS. They also require an excitation current to flow through the sensors. If this current is known, the resistance can be calculated.
Thermistors
Thermistors are similar to resistive sensors in that changes in temperature cause measurable changes in resistance. Thermistors are usually made of polymer or ceramic material. In most cases, thermistors are less expensive, but they are also less accurate than RTS. Most thermistors are available in two-wire configurations.
The Negative Temperature Coefficient (NTC) thermistor is the most commonly used thermistor for measuring temperature. The resistance of an NTC thermistor decreases as the temperature increases. Thermistors have a non-linear dependence of resistance on temperature. This requires significant correction for correct data interpretation. A popular approach to using a thermistor is to have the thermistor and a fixed value resistor form a voltage divider with an output that is converted to a digital value by an ADC.
Semiconductor based ICs
Semiconductor temperature sensors come in two different types: the local temperature sensor and the remote digital temperature sensor. Local temperature sensors are integrated circuits that measure the temperature of their own die using the physical properties of the transistor. Remote digital temperature sensors measure the temperature of an external transistor.
Local temperature sensors can use analogue or digital outputs. Analog outputs can be voltage or current while digital outputs can be seen in several formats such as I²C, SMBus, 1-Wire® and Serial Peripheral Interface (SPI). Local temperature sensors sense the temperature on circuit boards or the surrounding air.
Remote digital temperature sensors work similarly to local temperature sensors, using the physical properties of a transistor. The difference is that the transistor is placed away from the sensor chip. Some microprocessors and FPGAs include a bipolar sensor transistor to measure the die temperature of the target IC.
Infrared Sensors
Infrared sensors are non-contact sensors. For example, if you apply a typical infrared sensor to the front of a desk without contact, the sensor will tell you the temperature of the desk based on its radiation - probably room temperature.
With a non-contact ice water measurement, the measurement will be slightly below 0 °C due to evaporation, which may slightly lower the expected temperature reading.
Phase-change temperature sensors
Phase-change sensors measure the change in state of a material caused by a change in temperature, as when ice changes to water and then to steam. Commercially available devices of this type come in the form of labels, lozenges, crayons, or varnishes.
For example, labels can be used on steam traps. When a steam trap needs adjustment, it becomes hot; then a white dot on the label indicates the increase in temperature by turning black. The dot will remain black even if the temperature returns to normal levels.
Temperature labels are useful when confirmation is needed that the temperature has not exceeded a certain level, for example for technical or legal reasons during transportation. Because variable phase devices are non-electrical, like a bimetallic strip, they have an advantage in some applications. Some forms of this family of sensors (paint, crayons) do not change color; the marks made by them simply disappear. The lozenge version visually deforms or dissolves completely.
The limitation is the relatively slow response time. Therefore, if there is a temperature spike going up and then down very quickly, there may be no visible response. Accuracy is also not as high as most other devices commonly used in industry. However, they are very practical for applications where you need an irreversible indication that does not require electrical power.
Other labels that are reversible operate on a completely different principle, using a liquid crystal display. The display changes color from black to brown, blue or green, depending on the temperature reached.
Silicon diode
A silicon diode sensor is a device that has been developed specifically for the cryogenic temperature range. They are essentially linear devices in which the conductivity of the diode increases linearly in the low cryogenic ranges.
Regardless of the sensor you choose, it will likely not work on its own. Since most sensors overlap in temperature range and accuracy, the choice of sensor will depend on how it is integrated into the system.
Temperature sensors - Summary
Thermocouples, resistance sensors, thermistors and semiconductor integrated circuits are the main types of temperature sensors used today. Thermocouples are inexpensive, durable and can measure a wide range of temperatures. RTS's offer a wide range of temperature measurements (although they are smaller than thermocouples) and provide accurate and repeatable measurements. However, they are slower, require excitation current and require signal conditioning. Thermistors are durable and small, but are less accurate than resistive sensors and require more data correction for temperature interpretation. Semiconductor ICs are flexible to implantation and can come in very small form factors, but have a limited temperature range.
The rest of the solutions that have been presented are custom and mostly used in specific applications.
Related products
Related posts
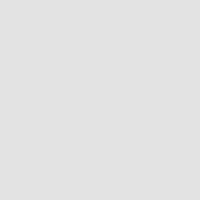
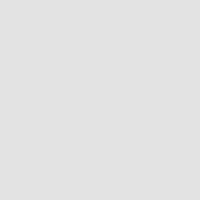
Leave a comment