Ви повинні увійти в систему
-
WróćX
-
компоненти
-
-
Category
-
Напівпровідники
- Діоди
- Тиристори
-
Електро-ізольовані модулі
- Електроізольовані модулі | ВІШАЙ (ІЧ)
- Електроізольовані модулі | INFINEON (EUPEC)
- Електроізольовані модулі | Семікрон
- Електроізольовані модулі | POWEREX
- Електроізольовані модулі | IXYS
- Електроізольовані модулі | ПОСЕЙКО
- Електроізольовані модулі | ABB
- Електроізольовані модулі | ТЕХСЕМ
- Przejdź do podkategorii
- Випрямні мости
-
Транзистори
- Транзистори | GeneSiC
- Модулі SiC MOSFET | Mitsubishi
- Модулі SiC MOSFET | STARPOWER
- Модулі ABB SiC MOSFET
- Модулі IGBT | MITSUBISHI
- Транзисторні модулі | MITSUBISHI
- Модулі MOSFET | MITSUBISHI
- Транзисторні модулі | ABB
- Модулі IGBT | POWEREX
- Модулі IGBT | INFINEON (EUPEC)
- Напівпровідникові елементи з карбіду кремнію (SiC)
- Przejdź do podkategorii
- Драйвери
- Блоки потужності
- Przejdź do podkategorii
- Електричні перетворювачі
-
Пасивні компоненти (конденсатори, резистори, запобіжники, фільтри)
- Резистори
-
Запобіжники
- Мініатюрні запобіжники для електронних плат серії ABC і AGC
- Швидкі трубчасті запобіжники
- Повільні запобіжники з характеристиками GL / GG і AM
- Ультрашвидкі плавкі запобіжники
- Швидкі запобіжники: британський та американський стандарт
- Швидкі запобіжники. Європейський стандарт
- Тягові запобіжники
- Високовольтні запобіжні
- Przejdź do podkategorii
-
Конденсатори
- Конденсатори для електродвигунів
- Електролітичні конденсатори
- Снабберні конденсатори
- Конденсатори потужності
- Конденсатори для DC ланцюгів
- Конденсатори для компенсації пасивної потужності
- Високовольтні конденсатори
- Конденсатори великої потужності для індукційного нагріву
- Конденсатори для зберігання імпульсів та енергії
- Конденсатори DC LINK
- Конденсатори для ланцюгів змінного / постійного струму
- Przejdź do podkategorii
- EMI фільтри
- Іоністори (супер-конденсатори)
-
Захист від стрибків напруги
- Захист від перенапруги для коаксіального застосування
- Захист від перенапруг для систем відеоспостереження
- Захист від перенапруги для силових кабелів
- Розрядники перенапруги для світлодіодів
- Розрядники перенапруги для фотоелектрики
- Захист системи зважування
- Захист від перенапруги для Fieldbus
- Przejdź do podkategorii
- Przejdź do podkategorii
-
Реле та контактори
- Реле та контактори - теорія
- Напівпровідникові реле AC 3-фазні
- Напівпровідникові реле DC
- Контролери, системи управління та аксесуари
- Системи плавного пуску і реверсивні контактори
- Електромеханічні реле
- Контактори
- Оборотні перемикачі
-
Напівпровідникові реле AC 1-фазні
- РЕЛЕ AC 1-ФАЗНЫЕ СЕРИИ 1 D2425 | D2450
- Однофазное реле AC серии CWA и CWD
- Однофазное реле AC серии CMRA и CMRD
- Однофазное реле AC серии PS
- Реле AC двойное и четверное серии D24 D, TD24 Q, H12D48 D
- Однофазні твердотільні реле серії gn
- Однофазні напівпровідникові реле змінного струму, серія ckr
- Однофазні реле змінного струму ERDA та ERAA для DIN-рейки
- Однофазні реле змінного струму для струму 150А
- Подвійні твердотільні реле, інтегровані з радіатором для DIN-рейки
- Przejdź do podkategorii
- Напівпровідникові реле AC 1-фазні для друкованих плат
- Інтерфейсні реле
- Przejdź do podkategorii
- Індукційні компоненти
- Радіатори, варистори, термічний захист
- Вентилятори
- Кондиціонери, обладнання для шаф електричних, охолоджувачі
-
Батареї, зарядні пристрої, буферні блоки живлення та інвертори
- Батареї, зарядні пристрої - теоретичний опис
- Літій-іонні батареї. Спеціальні батареї. Система управління акумулятором (BMS)
- Батареї
- Зарядні пристрої та аксесуари
- Резервне джерело живлення ДБЖ та буферні джерела живлення
- Перетворювачі та аксесуари для фотоелектрики
- Зберігання енергії
- Паливні елементи
- Літій-іонні акумулятори
- Przejdź do podkategorii
-
Автоматика
- Futaba Drone Parts
- Кінцеві вимикачі, Мікровимикачі
- Датчики Перетворювачі
- Пірометри
- Лічильники, Реле часу, Панельні вимірювальні прилади
- Промислові захисні пристрої
- Світлові і звукові сигнальні установки
- Термокамери, Тепловізори
- LED-екрани
- Керуюча апаратура
-
Реєстратори
- Реєстратори температури з записом на стрічку і з цифровим індикатором - AL3000
- Мікропроцесорні реєстратори з екраном LCD серія KR2000
- Реєстратор KR5000
- Вимірювач з функцією реєстрації вологості і температури HN-CH
- Експлуатаційні матеріали для реєстраторів
- Компактний графічний реєстратор 71VR1
- Реєстратор KR 3000
- Реєстратор PC серії R1M
- Реєстратор PC серії R2M
- Реєстратор PC, USB, 12 ізольованих входів – RZMS
- Реєстратор PC, USB, 12 ізольованих входів – RZUS
- Przejdź do podkategorii
- Przejdź do podkategorii
-
Провід, літцендрат, гофровані рукави, гнучкі з'єднання
- Дроти
- Багатожильні дроти Lica
-
Кабелі і дроти для спеціальних застосувань
- Подовжувальні та компенсаційні дроти
- Дроти для термопар
- Приєднувальні дроти для датчиків PT
- Багатожильні дроти темп. -60C до +1400C
- Дроти середньої напруги
- Дроти запалювання
- Нагрівальні дроти
- Одножильні дроти темп. -60C до +450C
- Залізничні дроти
- Нагрівальні дроти для вибухонебезпечних зон
- Przejdź do podkategorii
- Оболонки
-
Плетені кабелі
- Плоскі плетені кабелі
- Круглі плетені кабелі
- Дуже гнучкі плетені кабелі - плоскі
- Дуже гнучкі плетені кабелі - круглі
- Мідні циліндричні плетені кабелі
- Мідні циліндричні плетені кабелі і кожуха
- Гнучкі заземлювальні стрічки
- Циліндричні плетені дроти з лудженої і нержавіючої сталі
- Мідні ізольовані плетені дроти PCV - температура до 85 градусів C
- Плоскі алюмінієві плетені дроти
- З'єднувальний набір - плетені дроти і трубки
- Przejdź do podkategorii
- Аксесуари для тяги
- Кабельні наконечники
- Ізольовані еластичні шини
- Багатошарові гнучкі шини
- Системи прокладки кабелю (PESZLE)
- Шланги
- Przejdź do podkategorii
- Zobacz wszystkie kategorie
-
Напівпровідники
-
-
- Постачальники
-
додатки
- Energy bank
- ІНДУКЦІЙНИЙ НАГРІВ
- Автоматизація HVAC
- Верстати з ЧПУ
- ВИМІРЮВАННЯ ТА РЕГУЛЮВАННЯ ТЕМПЕРАТУРИ
- Вимірювання та регулювання температури
- ГІРНИЧОДОБУВНА ПРОМИСЛОВІСТЬ, СТАЛЕЛИВАРНІ КОМБІНАТИ, ГЗК
- ДВИГУНИ І ТРАНСФОРМАТОРИ
- ЕНЕРГЕТИКА
- ЗВАРЮВАЛЬНІ АПАРАТИ
- КОМПЛЕКТУЮЧІ ДЛЯ РОЗПОДІЛЬНИХ, ТЕЛЕКОМУНІКАЦІЙНИХ ШАФ І ШАФ УПРАВЛІННЯ
- МАШИНИ ДЛЯ ДЕРЕВООБРОБКИ ТА СУШІННЯ ДЕРЕВИНИ
- ПОЛІГРАФІЯ
- ПРИВІД ПОСТІЙНОГО І ЗМІННОГО СТРУМУ
- ПРИЛАДИ ТА ОБЛАДНАННЯ ДЛЯ ВИБУХОНЕБЕЗПЕЧНИХ ЗОН (EX)
- ПРИСТРОЇ БЕЗПЕРЕБІЙНОГО ЖИВЛЕННЯ (UPS) І ВИПРЯМЛЯЧІ
- ПРОМИСЛОВІ ЗАСОБИ ЗАХИСТУ
- ПРОМИСЛОВА АВТОМАТИКА
- ТЕРМОФОРМОВОЧНІ МАШИНИ
- ТЯГОВИЙ ПРИВІД
-
монтаж
-
-
Індуктори
-
-
Індукційні прилади
-
-
https://www.dacpol.eu/pl/naprawy-i-modernizacje
-
-
Сервіс
-
- Контакт
- Zobacz wszystkie kategorie
Enhancing Plastic Production with ENDA ERC Industrial IoT Gateway: Data Integration, Monitoring, and Remote Management
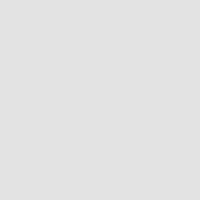
In the era of the Fourth Industrial Revolution, IoT (Internet of Things) technology plays a key role in optimizing production processes. In plastic manufacturing, precise monitoring and control of processes are essential for ensuring high product quality. One of the devices that enables such control is the ENDA ERC gateway. This advanced tool allows for the collection and transmission of data from various devices and systems to the cloud, enabling remote monitoring and analysis of production processes. ENDA ERC leads to modernization of production, as every sensor or controller with Modbus communication, thanks to ERC, is accessible from the cloud. In this article, we will take a closer look at the applications of ENDA ERC in plastic manufacturing.
Data Collection and System Integration
Plastic manufacturing involves many stages, such as mixing raw materials, injection molding, forming, cooling, and packaging. Each of these stages requires precise monitoring of parameters like temperature, pressure, machine speed, and cycle time. The ENDA ERC gateway allows for data collection from various sensors and devices, integrating them into a unified management system. This enables operators to monitor production processes in real-time, leading to faster responses to potential issues and minimization of downtime.
ENDA ERC does not directly automate processes but provides necessary data that operators can use to make informed decisions. By integrating with devices communicating via Modbus, ERC allows access to data from sensors and controllers from the cloud, which significantly modernizes production processes.
Data Monitoring and Analysis
One of the key aspects of industrial IoT is the ability to collect and analyze vast amounts of data. The ENDA ERC gateway allows for data collection from various sensors and devices in real-time and their transmission to the cloud. This data can then be analyzed to identify patterns, predict failures, and optimize processes.
In plastic manufacturing, monitoring parameters such as mold temperature, injection pressure, and cycle time is crucial for ensuring high product quality. With ENDA ERC, these data points can be monitored continuously, and any deviations from the norm can be immediately identified by operators, who can then take corrective actions. This helps maintain consistent production quality and minimize waste.
Remote Management and Maintenance
One of the most important aspects of modern IoT systems is the ability to remotely manage and monitor devices. The ENDA ERC gateway allows for remote monitoring of production device parameters from anywhere in the world. This means that operators can quickly respond to issues even if they are not physically present in the factory.
Remote management also enables predictive maintenance. By analyzing data from devices, the system can predict when a particular machine will require servicing, allowing maintenance to be scheduled in a way that minimizes production downtime. This, in turn, leads to increased efficiency and reduced operating costs.
Conclusion
The ENDA ERC gateway is a versatile tool that offers numerous benefits for the plastic manufacturing industry. Data collection and transmission, monitoring and analysis, as well as remote management and maintenance are just some of the capabilities that this device offers. By applying IoT technology, plastic manufacturers can enhance operational efficiency, improve product quality, and reduce production costs. Additionally, with the ability to integrate devices communicating via Modbus and access them from the cloud, ENDA ERC leads to significant modernization of production processes. Implementing ENDA ERC into the production process is a step towards a modern, automated, and intelligent factory of the future.
Related product
Related posts
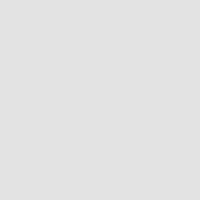
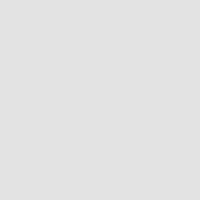
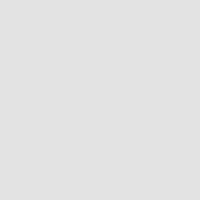
Leave a comment