Ви повинні увійти в систему
-
WróćX
-
компоненти
-
-
Category
-
Напівпровідники
- Діоди
- Тиристори
-
Електро-ізольовані модулі
- Електроізольовані модулі | ВІШАЙ (ІЧ)
- Електроізольовані модулі | INFINEON (EUPEC)
- Електроізольовані модулі | Семікрон
- Електроізольовані модулі | POWEREX
- Електроізольовані модулі | IXYS
- Електроізольовані модулі | ПОСЕЙКО
- Електроізольовані модулі | ABB
- Електроізольовані модулі | ТЕХСЕМ
- Przejdź do podkategorii
- Випрямні мости
-
Транзистори
- Транзистори | GeneSiC
- Модулі SiC MOSFET | Mitsubishi
- Модулі SiC MOSFET | STARPOWER
- Модулі ABB SiC MOSFET
- Модулі IGBT | MITSUBISHI
- Транзисторні модулі | MITSUBISHI
- Модулі MOSFET | MITSUBISHI
- Транзисторні модулі | ABB
- Модулі IGBT | POWEREX
- Модулі IGBT | INFINEON (EUPEC)
- Напівпровідникові елементи з карбіду кремнію (SiC)
- Przejdź do podkategorii
- Драйвери
- Блоки потужності
- Przejdź do podkategorii
- Електричні перетворювачі
-
Пасивні компоненти (конденсатори, резистори, запобіжники, фільтри)
- Резистори
-
Запобіжники
- Мініатюрні запобіжники для електронних плат серії ABC і AGC
- Швидкі трубчасті запобіжники
- Повільні запобіжники з характеристиками GL / GG і AM
- Ультрашвидкі плавкі запобіжники
- Швидкі запобіжники: британський та американський стандарт
- Швидкі запобіжники. Європейський стандарт
- Тягові запобіжники
- Високовольтні запобіжні
- Przejdź do podkategorii
-
Конденсатори
- Конденсатори для електродвигунів
- Електролітичні конденсатори
- Снабберні конденсатори
- Конденсатори потужності
- Конденсатори для DC ланцюгів
- Конденсатори для компенсації пасивної потужності
- Високовольтні конденсатори
- Конденсатори великої потужності для індукційного нагріву
- Конденсатори для зберігання імпульсів та енергії
- Конденсатори DC LINK
- Конденсатори для ланцюгів змінного / постійного струму
- Przejdź do podkategorii
- EMI фільтри
- Іоністори (супер-конденсатори)
-
Захист від стрибків напруги
- Захист від перенапруги для коаксіального застосування
- Захист від перенапруг для систем відеоспостереження
- Захист від перенапруги для силових кабелів
- Розрядники перенапруги для світлодіодів
- Розрядники перенапруги для фотоелектрики
- Захист системи зважування
- Захист від перенапруги для Fieldbus
- Przejdź do podkategorii
- Фільтри виявлення випромінювання TEMPEST
- Przejdź do podkategorii
-
Реле та контактори
- Реле та контактори - теорія
- Напівпровідникові реле AC 3-фазні
- Напівпровідникові реле DC
- Контролери, системи управління та аксесуари
- Системи плавного пуску і реверсивні контактори
- Електромеханічні реле
- Контактори
- Оборотні перемикачі
-
Напівпровідникові реле AC 1-фазні
- РЕЛЕ AC 1-ФАЗНЫЕ СЕРИИ 1 D2425 | D2450
- Однофазное реле AC серии CWA и CWD
- Однофазное реле AC серии CMRA и CMRD
- Однофазное реле AC серии PS
- Реле AC двойное и четверное серии D24 D, TD24 Q, H12D48 D
- Однофазні твердотільні реле серії gn
- Однофазні напівпровідникові реле змінного струму, серія ckr
- Однофазні реле змінного струму ERDA та ERAA для DIN-рейки
- Однофазні реле змінного струму для струму 150А
- Подвійні твердотільні реле, інтегровані з радіатором для DIN-рейки
- Przejdź do podkategorii
- Напівпровідникові реле AC 1-фазні для друкованих плат
- Інтерфейсні реле
- Przejdź do podkategorii
- Індукційні компоненти
- Радіатори, варистори, термічний захист
- Вентилятори
- Кондиціонери, обладнання для шаф електричних, охолоджувачі
-
Батареї, зарядні пристрої, буферні блоки живлення та інвертори
- Батареї, зарядні пристрої - теоретичний опис
- Літій-іонні батареї. Спеціальні батареї. Система управління акумулятором (BMS)
- Батареї
- Зарядні пристрої та аксесуари
- Резервне джерело живлення ДБЖ та буферні джерела живлення
- Перетворювачі та аксесуари для фотоелектрики
- Зберігання енергії
- Паливні елементи
- Літій-іонні акумулятори
- Przejdź do podkategorii
- Автоматика
-
Провід, літцендрат, гофровані рукави, гнучкі з'єднання
- Дроти
- Багатожильні дроти Lica
-
Кабелі і дроти для спеціальних застосувань
- Подовжувальні та компенсаційні дроти
- Дроти для термопар
- Приєднувальні дроти для датчиків PT
- Багатожильні дроти темп. -60C до +1400C
- Дроти середньої напруги
- Дроти запалювання
- Нагрівальні дроти
- Одножильні дроти темп. -60C до +450C
- Залізничні дроти
- Нагрівальні дроти для вибухонебезпечних зон
- Przejdź do podkategorii
- Оболонки
-
Плетені кабелі
- Плоскі плетені кабелі
- Круглі плетені кабелі
- Дуже гнучкі плетені кабелі - плоскі
- Дуже гнучкі плетені кабелі - круглі
- Мідні циліндричні плетені кабелі
- Мідні циліндричні плетені кабелі і кожуха
- Гнучкі заземлювальні стрічки
- Циліндричні плетені дроти з лудженої і нержавіючої сталі
- Мідні ізольовані плетені дроти PCV - температура до 85 градусів C
- Плоскі алюмінієві плетені дроти
- З'єднувальний набір - плетені дроти і трубки
- Przejdź do podkategorii
- Аксесуари для тяги
- Кабельні наконечники
- Ізольовані еластичні шини
- Багатошарові гнучкі шини
- Системи прокладки кабелю (PESZLE)
- Przejdź do podkategorii
- Zobacz wszystkie kategorie
-
Напівпровідники
-
-
- Постачальники
-
додатки
- Energy bank
- ІНДУКЦІЙНИЙ НАГРІВ
- Автоматизація HVAC
- Верстати з ЧПУ
- ВИМІРЮВАННЯ ТА РЕГУЛЮВАННЯ ТЕМПЕРАТУРИ
- Вимірювання та регулювання температури
- ГІРНИЧОДОБУВНА ПРОМИСЛОВІСТЬ, СТАЛЕЛИВАРНІ КОМБІНАТИ, ГЗК
- ДВИГУНИ І ТРАНСФОРМАТОРИ
- ЕНЕРГЕТИКА
- ЗВАРЮВАЛЬНІ АПАРАТИ
- КОМПЛЕКТУЮЧІ ДЛЯ РОЗПОДІЛЬНИХ, ТЕЛЕКОМУНІКАЦІЙНИХ ШАФ І ШАФ УПРАВЛІННЯ
- МАШИНИ ДЛЯ ДЕРЕВООБРОБКИ ТА СУШІННЯ ДЕРЕВИНИ
- ПОЛІГРАФІЯ
- ПРИВІД ПОСТІЙНОГО І ЗМІННОГО СТРУМУ
- ПРИЛАДИ ТА ОБЛАДНАННЯ ДЛЯ ВИБУХОНЕБЕЗПЕЧНИХ ЗОН (EX)
- ПРИСТРОЇ БЕЗПЕРЕБІЙНОГО ЖИВЛЕННЯ (UPS) І ВИПРЯМЛЯЧІ
- ПРОМИСЛОВІ ЗАСОБИ ЗАХИСТУ
- ПРОМИСЛОВА АВТОМАТИКА
- ТЕРМОФОРМОВОЧНІ МАШИНИ
- ТЯГОВИЙ ПРИВІД
-
монтаж
-
-
Індуктори
-
-
Індукційні прилади
-
-
https://www.dacpol.eu/pl/naprawy-i-modernizacje
-
-
Сервіс
-
- Контакт
- Zobacz wszystkie kategorie
1200V SiC Hybrid IGBT Modules for High Frequency Applications
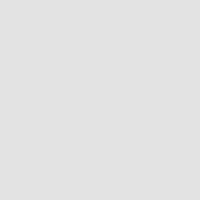
1200V SiC Hybrid IGBT Modules for High Frequency Applications
Dedicated IGBT-modules for high switching frequency operation have been successfully introduced to the market over the past years. Typical applications are X-ray generators, CT-scanners, induction heating, welding, plasma cutters or inverters for isolated or contactless electrical power conversion.
By Eckhard Thal, Mitsubishi Electric Europe B.V., Ratingen, Germany
The switching frequency in those applications is usually higher than 20kHz, thus exceeding the range for which standard industrial IGBTmodules are optimized for. Since several years Mitsubishi Electric is offering a dedicated IGBT-series for those high frequency applications, called NFH-series. For reducing the switching loss it is using IGBT-chips with an optimized trade-off between Vce(sat) and Eoff. As next innovation step Mitsubishi Electric now is introducing it’s Silicon Carbide Chip technology to this proven NFH-series design.
Hybrid SiC-IGBT module approach
A series of 1200V dual modules with current ratings between 100A and 600A was developed [1] by using SiC Schottky Barrier Diodes (SBD). This approach is called “Hybrid SiC” module. For better understanding the used terminology, please refer to Figure 1. A hybrid SiC module is containing Silicon-based IGBT in combination with SiCbased Schottky Barrier diodes. The IGBT-chips are kept the same in both the conventional NFH-series and new hybrid SiC NFH-series.
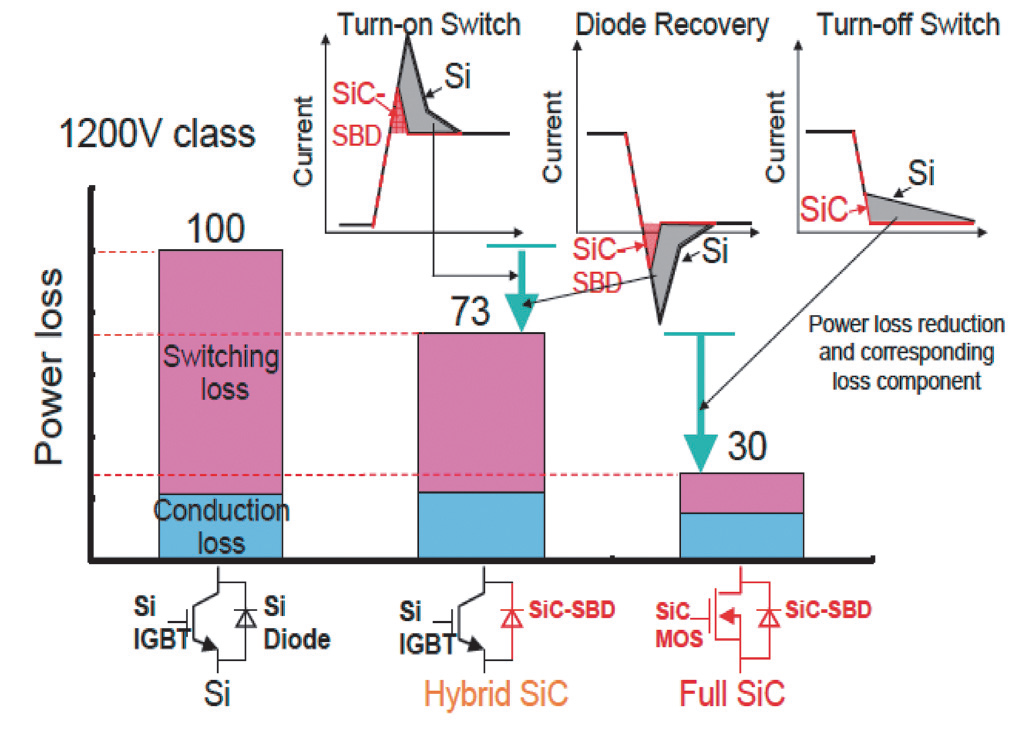
Figure 1: Evolution of SiC technology in power modules
Type | Voltage | Current | Connection | Baseplate size |
CMH100DY-24NFH | 1200V | 100A | 2in1 | 48x94mm |
CMH150DY-24NFH | 150A | |||
CMH200DU-24NFH | 200A | 62x108mm | ||
CMH300DU-24NFH | 300A | |||
CMH400DU-24NFH | 400A | 80x110mm | ||
CMH600DU-24NFH | 600A |
Table 1: Line-up
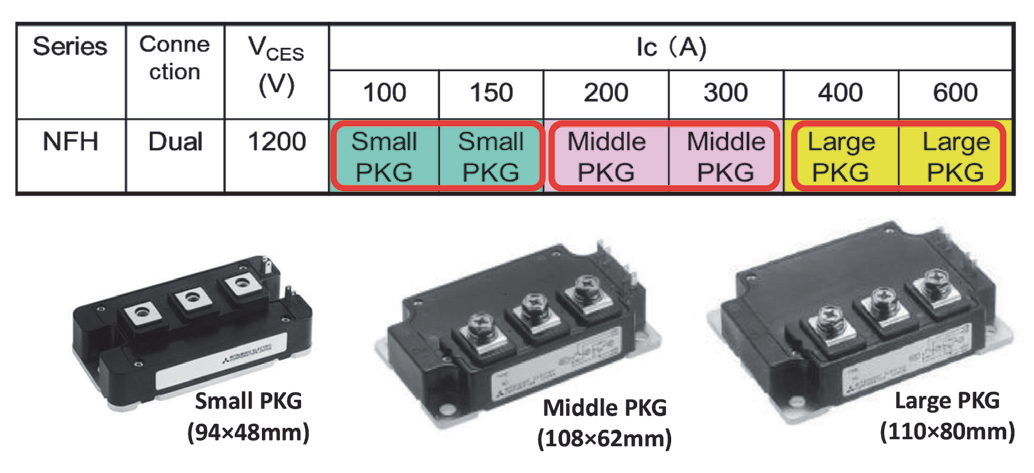
Figure 2: Line-up and Package outlines
The principle switching waveforms are given in Figure 1. Due to the fact that Schottky diodes as unipolar semiconductors don’t have any reverse recovery charge, there is no reverse recovery loss. The absence of diode reverse recovery current on the other hand leads to a substantial reduction of IGBT turn-on energy.
A further reduction of total power loss can be achieved if both the active switch and the free-wheeling diode are made of SiC. This approach is called “Full SiC” module.
Line-up & Package outlines
The line-up of new hybrid SiC NFH-series is shown in table 1; the package outlines are given in Figure 2. For the middle and large size packages the main terminals are located at the side of the housing. This arrangement allows using a laminated main terminal structure inside the module for reducing the internal package inductance Lint. For all current ratings of both middle and large size package this internal package inductance is in the range of 18…22nH (defi ned between Pand N - main terminals).
Switching behavior
The turn-on waveforms under inductive load condition of conventional NFH-module CM600DU-24NFH and new hybrid SiC module CMH600DU-24NFH are shown in Figure 3. Taking into account that both module types are using exactly the same IGBT-chips the difference in switching waveform is entirely the result of difference in free-wheel diode behavior. The key difference between both current waveforms can be explained by the lack of reverse recovery charge (and consequently the diode’s reverse recovery current) in the hybrid SiC module CMH600DU-24NFH as the Schottky Barrier Diode is a unipolar semiconductor. Consequently both the turn-off loss of freewheeling diode and the turn-on loss of IGBT under inductive load switching are drastically reduced, as it can be seen in the switching energy diagrams given in Figure 4 and 5.
Loss performance comparison
A power loss simulation under inverter operation conditions (hard switching) with sine-wave PWM reveals the big impact of using SiC Schottky diodes instead of conventional Si-diodes for the NFH-series modules: at fc=30kHz the hybrid SiC module has just half of the total losses of its Si-counterpart, see Figure 6.
The dependency of total module power loss on PWM switching frequency fc is given in Figure 7. From this diagram it can be derived that the total power loss of new hybrid SiC type CMH600DU-24NFH at fc=50kHz is at the same level as its full Si-counterpart at fc=17kHz. Considering that both modules CMH600DU-24NFH and CM600DU24NFH have the same power loss handling capability (same baseplate size and hence the same Rth(c-f); same Rth(j-c) for IGBT) it seems to be possible for such applications to triple the switching frequency fc while keeping the module power loss at the same level.
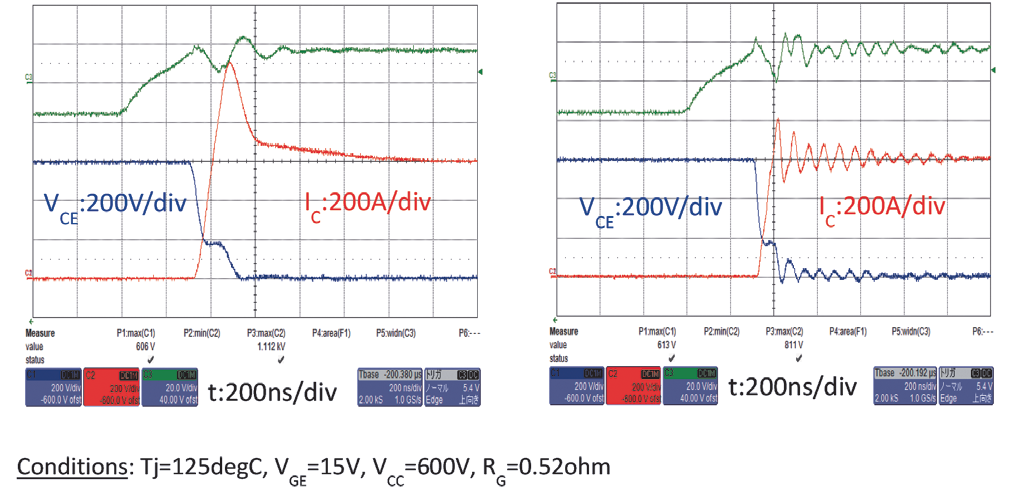
Figure 3: Ic-waveforms at turn-on
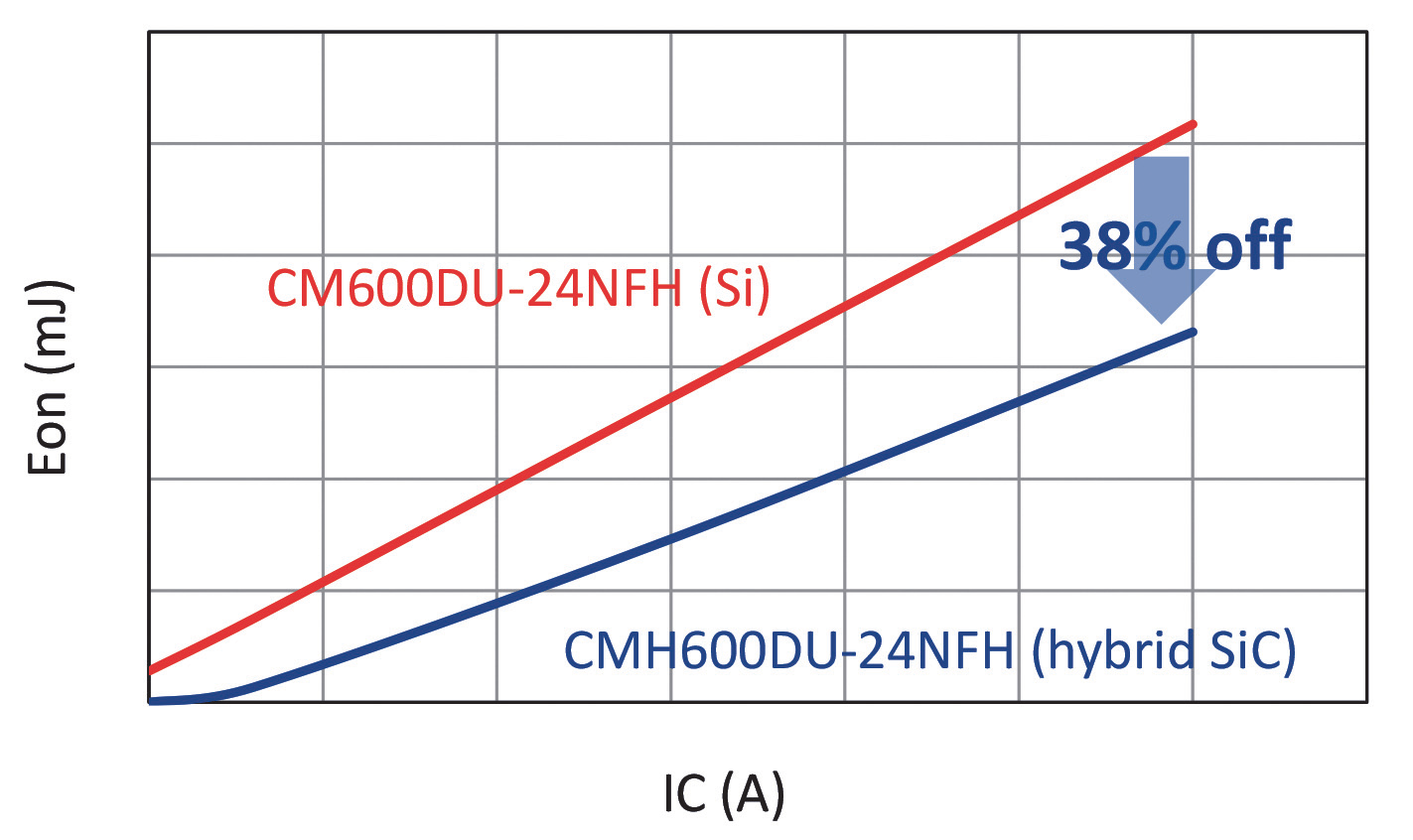
Figure 4: IGBT turn-on energy E(on) vs. current
Application benefits
The described improvements in switching loss performance under hard switching conditions are offering system benefi ts basically in two directions when using the new hybrid SiC NFH-series: The most obvious one is the possibility of increasing the switching frequency fc. The size of inductive components in a power electronic system is often determined by the switching frequency. Consequently an increase of fc can help to reduce size (and cost) of those inductive components. Also the dynamic response of a power electronic system can be improved by increasing fc. Another direction is improving the energy effi ciency of a power electronic system. This is an interesting option especially in application where low system effi ciency is penalized. In general reducing the power loss dissipated in the IGBT modules will help to reduce heat sink size. This is interesting for such applications where heat sink is the limiting factor for system size reduction. Another potential benefi t of using the new hybrid SiC series can be expected in soft switching applications. Here the principle absence of reverse recovery charge at diode turn-off can contribute to a further power loss reduction.
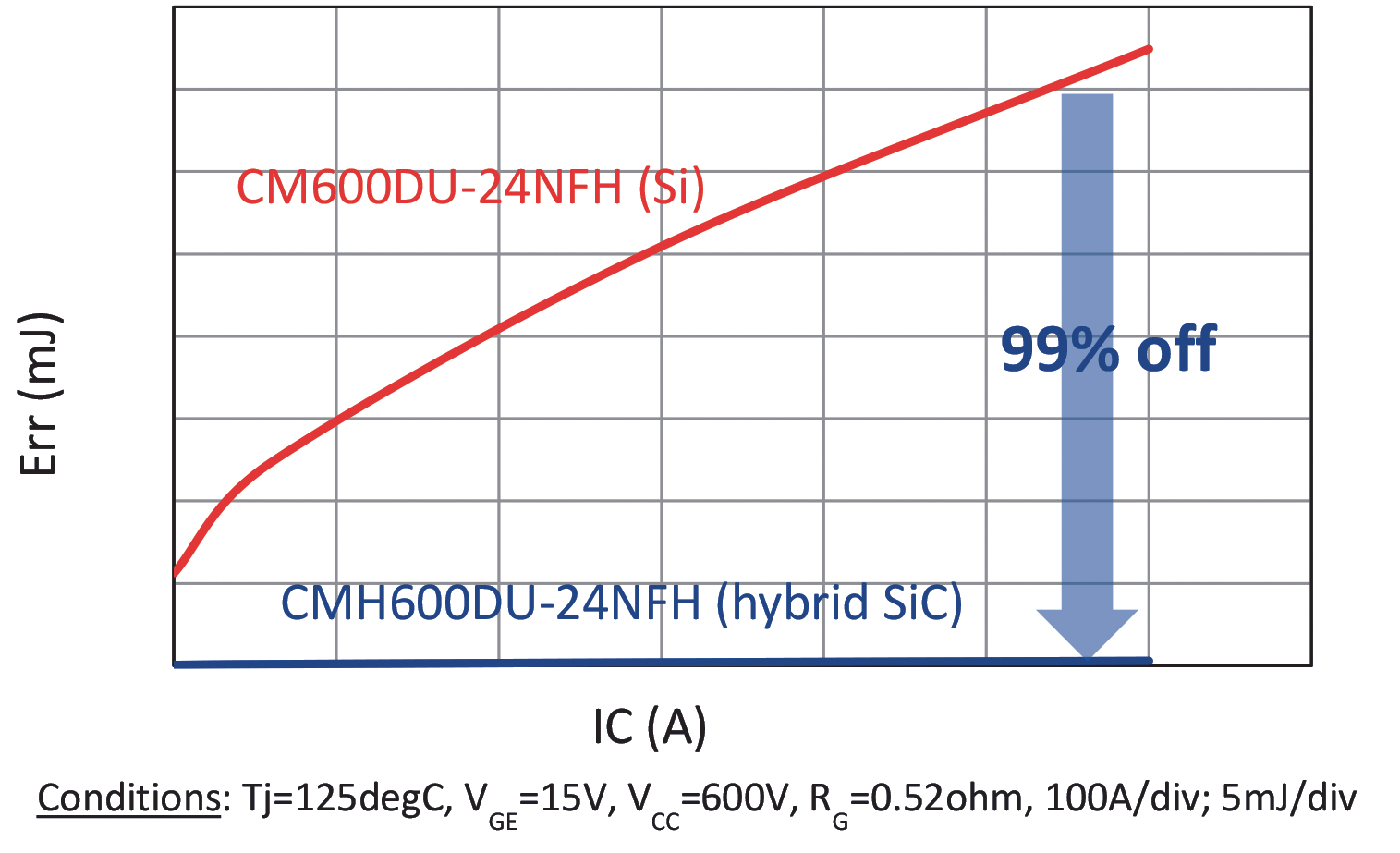
Figure 5: Freewheeling diode turn-off energy vs. current

Figure 6: Power loss simulation (inverter operation with sinus PWM)
Summary and outlook
By using Mitsubishi’s new hybrid SiC IGBT modules for high frequency applications a drastical reduction of switching loss is possible. The use of SiC Schottky Barrier diodes instead of conventional Silicon diodes as freewheeling diodes in the modules of NFH-series is eliminating the reverse recovery charge at freewheeling diode turnoff. Under hard switching inverter operation conditions this allows to increase the switching frequency by a factor of 2…3 compared with conventional Si-based IGBT modules.
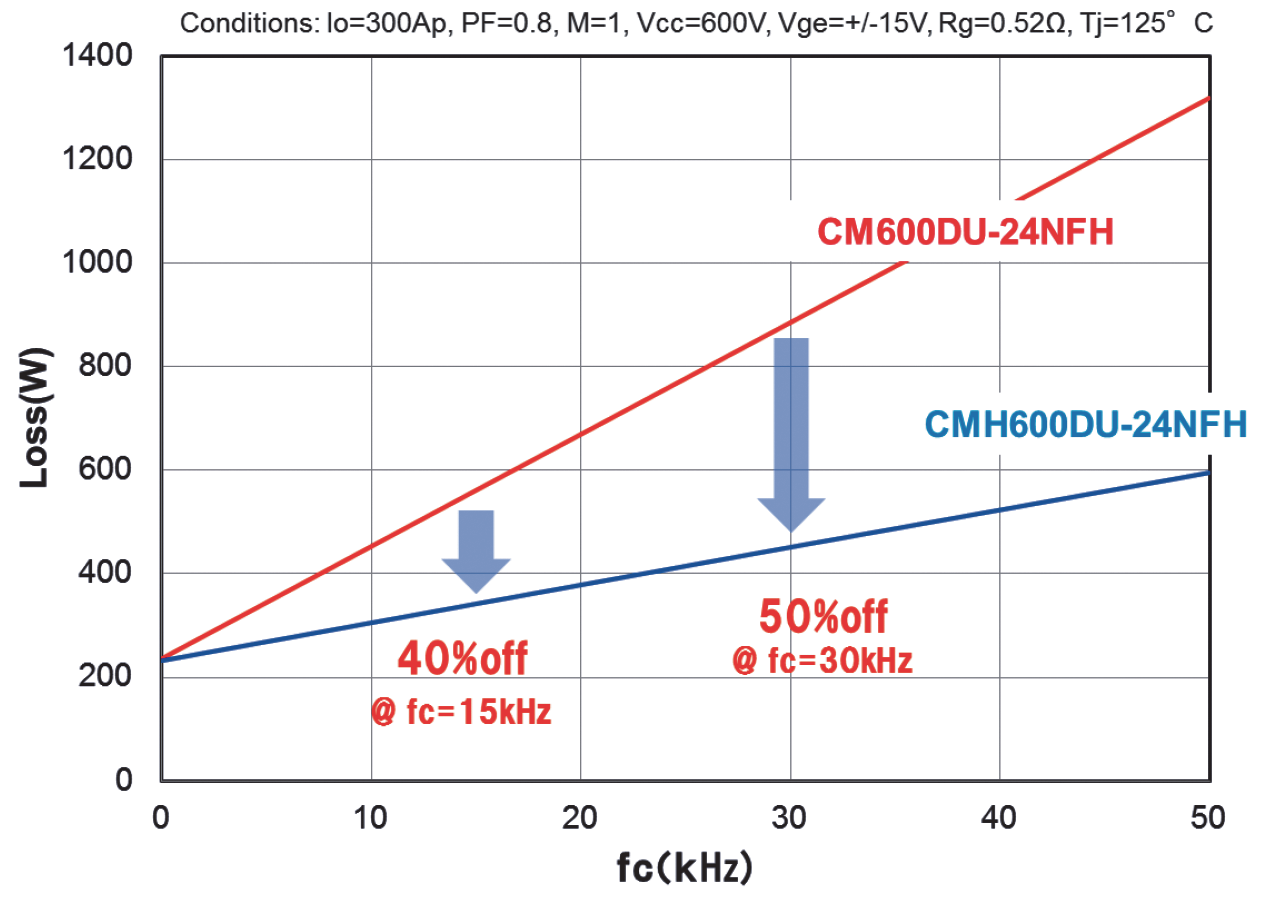
Figure 7: Power loss versus PWM switching frequency fc
Application benefi ts can be also expected when using the new hybrid SiC modules in soft switching applications due to the absence of reverse recovery charge at diode turn-off. Here further investigations are needed.
Literature
[1] “Mitsubishi Electric to Ship Sample Hybrid SiC Power Semiconductor Modules for High-frequency Switching Applications”; Press Release of Mitsubishi Electric Corporation; Tokyo, May 15, 2014
Related posts
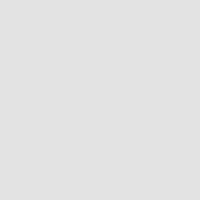
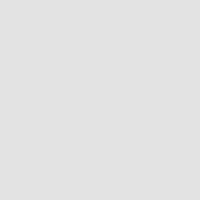
Leave a comment